Das Vakuumsintern ist ein spezielles Verfahren, das in der industriellen Metallurgie und der Werkstoffkunde zur Herstellung von hochdichten und leistungsstarken Werkstoffen eingesetzt wird.Dabei werden Materialien in einer Vakuumumgebung auf Temperaturen nahe dem Schmelzpunkt erhitzt, so dass eine atomare Diffusion ohne Oxidation oder Verunreinigung stattfinden kann.Dieses Verfahren eignet sich besonders für Materialien mit hohem Schmelzpunkt, wie Keramik, Metalle und Legierungen.Die Vakuumumgebung sorgt dafür, dass die Materialien frei von Verunreinigungen bleiben, was zu hervorragenden mechanischen und thermischen Eigenschaften führt.Das Vakuumsintern ist in Branchen wie der Luft- und Raumfahrt, der Elektronik und der Fertigung weit verbreitet, um Bauteile mit präzisen Spezifikationen und verbesserter Haltbarkeit herzustellen.
Die wichtigsten Punkte erklärt:
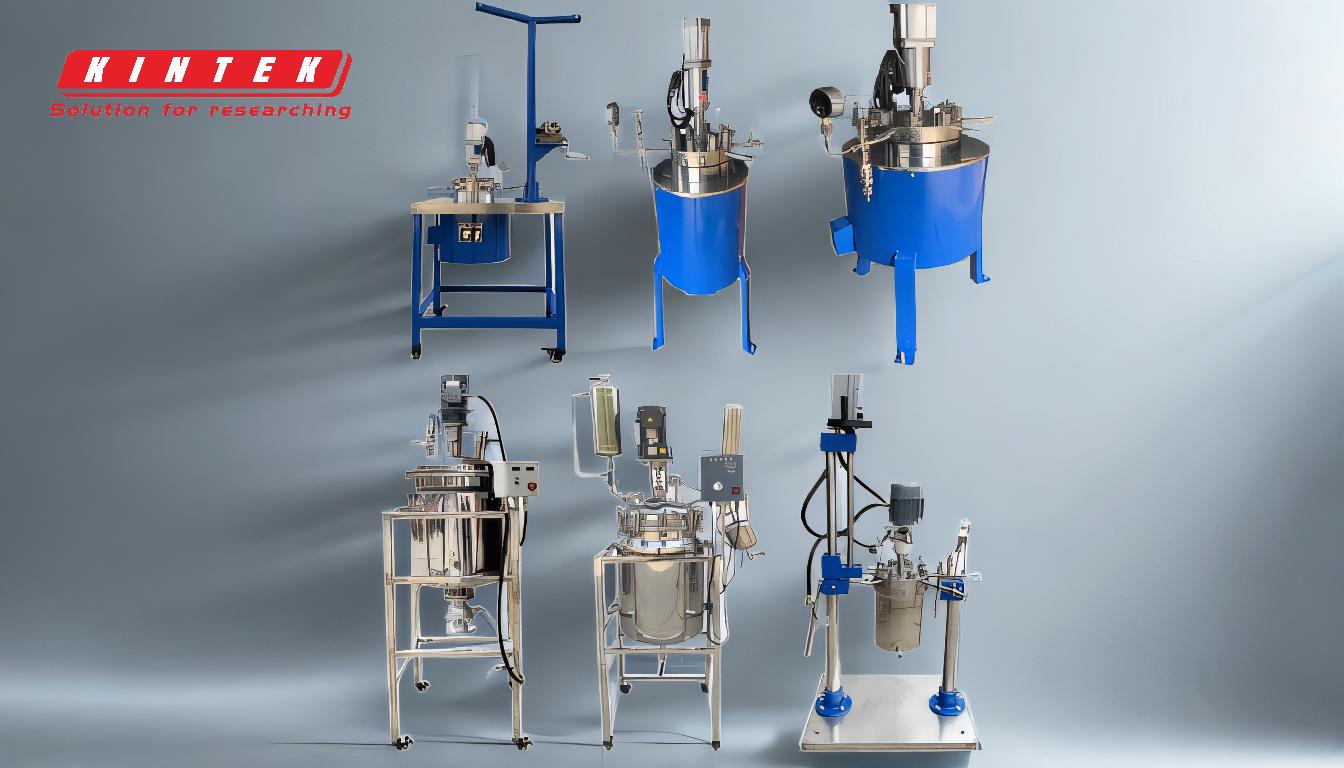
-
Definition des Vakuumsinterns:
- Beim Vakuumsintern werden Materialien in einer Vakuumumgebung auf Temperaturen nahe dem Schmelzpunkt erhitzt.Dies ermöglicht die Diffusion von Atomen und verdichtet das Material zu einer dichten, festen Form, ohne es vollständig zu schmelzen.Durch die Abwesenheit von Luft werden Oxidation und Verunreinigung verhindert, was qualitativ hochwertige Ergebnisse gewährleistet.
-
Arbeitsprinzip eines Vakuum-Sinterofens:
- In einem Vakuumsinterofen wird in der Kammer ein Vakuum erzeugt, wodurch alle atmosphärischen Gase entfernt werden.Das Material wird dann auf hohe Temperaturen erhitzt, was die atomare Diffusion und die Bewegung der Korngrenzen ermöglicht.Das Ergebnis ist ein dichtes, festes Produkt mit verbesserten mechanischen Eigenschaften.
-
Die Schritte des Vakuumsinterprozesses:
- Aufladen:Das Material wird in den Ofen gelegt.
- Vakuum-Erzeugung:Die Luft wird evakuiert, um eine Vakuumumgebung zu schaffen.
- Heizung:Die Temperatur wird schrittweise bis zum Sinterpunkt erhöht.
- Isolierung:Das Material wird für eine bestimmte Dauer auf der Sintertemperatur gehalten.
- Abkühlung:Das Material wird unter kontrollierten Bedingungen abgekühlt, um eine Oxidation zu verhindern.
-
Vorteile des Vakuumsinterns:
- Oxidationsschutz:Die Vakuumumgebung schließt das Risiko der Oxidation aus und gewährleistet Reinheit.
- Verbesserte Materialeigenschaften:Das Verfahren verbessert die Dichte, Festigkeit und thermische Stabilität.
- Vielseitigkeit:Geeignet für eine breite Palette von Werkstoffen, einschließlich Keramik, Metalle und Legierungen.
-
Anwendungen des Vakuumsinterns:
- Keramiken und Hartlegierungen:Für die Herstellung von Hochleistungskeramiken und Hartlegierungen.
- Optische und elektrische Komponenten:Ideal für die Herstellung optischer und elektrischer Formmassen.
- Graphit-Reinigung:Zur Reinigung und Sinterung von Graphitmaterialien.
-
Vergleich mit anderen Sinterverfahren:
- Im Gegensatz zum Atmosphärensintern, das auf einer kontrollierten Gasumgebung beruht, werden beim Vakuumsintern alle Gase eliminiert, was zu einer höheren Reinheit und besseren Materialeigenschaften führt.Es ist auch effektiver als herkömmliche Sinterverfahren für Materialien mit hohem Schmelzpunkt.
-
Industrielle Bedeutung:
- Das Vakuumsintern ist von entscheidender Bedeutung für Branchen, die hochpräzise Komponenten benötigen, wie z. B. die Luft- und Raumfahrt, die Elektronik und die moderne Fertigung.Das Verfahren stellt sicher, dass die Materialien strenge Qualitätsstandards erfüllen und auch unter extremen Bedingungen zuverlässig funktionieren.
Wenn ein Käufer von Vakuumsinteranlagen diese Schlüsselpunkte versteht, kann er fundierte Entscheidungen über die Eignung dieses Verfahrens für seine spezifischen Anwendungen und Materialanforderungen treffen.
Zusammenfassende Tabelle:
Aspekt | Einzelheiten |
---|---|
Definition | Erhitzen von Materialien im Vakuum auf Temperaturen nahe dem Schmelzpunkt, um die Diffusion von Atomen zu ermöglichen. |
Arbeitsprinzip | In einem Vakuumsinterofen werden die Gase entfernt, was die atomare Diffusion ermöglicht. |
Schritte | Aufladung, Vakuumerzeugung, Erwärmung, Isolierung und kontrollierte Abkühlung. |
Vorteile | Verhindert Oxidation, verbessert die Materialeigenschaften und bietet Vielseitigkeit. |
Anwendungen | Keramik, Hartlegierungen, optische/elektrische Komponenten und Reinigung von Graphit. |
Industrielle Bedeutung | Entscheidend für die Luft- und Raumfahrt, die Elektronik und die Fertigungsindustrie. |
Sind Sie bereit, Ihre Materialleistung zu verbessern? Kontaktieren Sie uns noch heute für eine fachkundige Beratung zu Lösungen für das Vakuumsintern!