Der Dampfabscheidungsprozess, insbesondere die chemische Gasphasenabscheidung (CVD), ist eine hochentwickelte Herstellungstechnik, mit der dünne Materialfilme auf einem Substrat abgeschieden werden. Dieser Prozess umfasst mehrere Schlüsselschritte, darunter den Transport gasförmiger Reaktanten zur Substratoberfläche, die Adsorption dieser Reaktanten, chemische Reaktionen, die zur Filmbildung führen, und die Entfernung von Nebenprodukten. CVD unterscheidet sich von der physikalischen Gasphasenabscheidung (PVD) dadurch, dass es eher auf chemischen Reaktionen als auf physikalischen Prozessen beruht. Es wird in verschiedenen Branchen häufig zur Herstellung hochwertiger, langlebiger Beschichtungen und Filme für Anwendungen von der Elektronik bis hin zu Schutzbeschichtungen eingesetzt.
Wichtige Punkte erklärt:
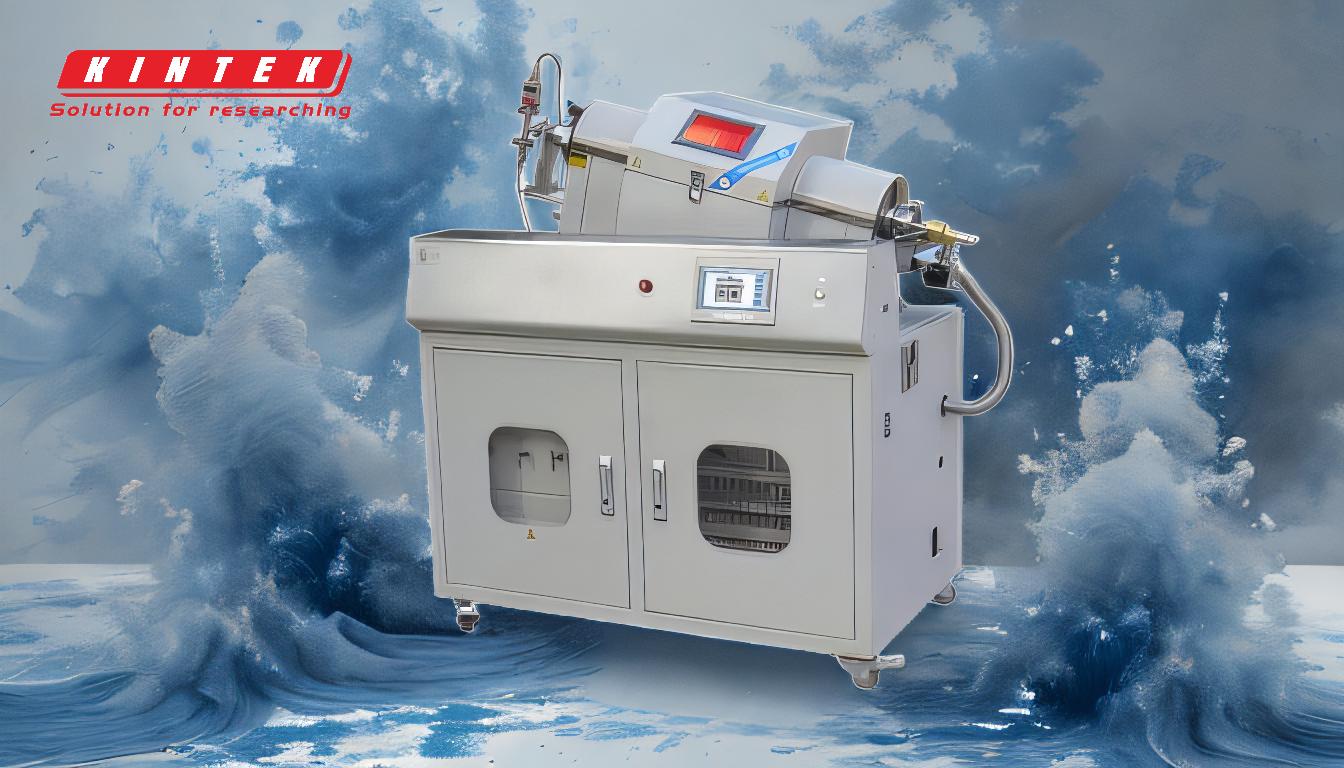
-
Definition der chemischen Gasphasenabscheidung (CVD):
- CVD ist ein Dünnschichtabscheidungsverfahren, bei dem durch chemische Reaktionen in der Dampfphase ein fester Film auf einem erhitzten Substrat gebildet wird. Bei diesem Prozess reagieren typischerweise Atome, Moleküle oder eine Kombination aus beiden auf der Substratoberfläche und bilden einen dünnen, festen Film. Im Gegensatz zur physikalischen Gasphasenabscheidung (PVD), die auf physikalischen Prozessen wie Verdampfen oder Sputtern beruht, zeichnet sich CVD durch oberflächenvermittelte chemische Reaktionen aus.
-
Schritte bei CVD:
- Transport reagierender gasförmiger Spezies: Der Prozess beginnt mit dem Transport gasförmiger Reaktanten zur Substratoberfläche. Bei diesen Reaktanten handelt es sich typischerweise um flüchtige Verbindungen, die leicht verdampfen können.
- Adsorption an der Oberfläche: Sobald die gasförmigen Spezies das Substrat erreichen, adsorbieren sie an dessen Oberfläche. Dieser Schritt ist von entscheidender Bedeutung, da er die Reaktanten auf die nachfolgenden chemischen Reaktionen vorbereitet.
- Oberflächenkatalysierte Reaktionen: Die adsorbierten Spezies unterliegen chemischen Reaktionen auf der Substratoberfläche, die häufig durch die Oberfläche selbst katalysiert werden. Diese Reaktionen führen zur Bildung des gewünschten festen Films.
- Oberflächendiffusion zu Wachstumsstellen: Die reagierten Spezies diffundieren dann über die Oberfläche zu bestimmten Wachstumsstellen, wo der Film Keime bildet und wächst.
- Keimbildung und Wachstum des Films: An den Wachstumsstellen beginnt der Film zu keimen und zu wachsen und bildet eine kontinuierliche Schicht über dem Substrat.
- Desorption von Nebenprodukten: Schließlich desorbieren alle während der Reaktion gebildeten gasförmigen Nebenprodukte von der Oberfläche und werden abtransportiert, wobei der abgeschiedene Film zurückbleibt.
-
Anwendungen von CVD:
- CVD wird in der Halbleiterindustrie häufig zur Abscheidung dünner Schichten aus Materialien wie Siliziumdioxid, Siliziumnitrid und verschiedenen Metallen eingesetzt. Es wird auch bei der Herstellung von Schutzschichten, optischen Beschichtungen und sogar bei der Herstellung komplexer Nanostrukturen eingesetzt.
-
Vorteile von CVD:
- Hochwertige Filme: CVD kann Filme mit ausgezeichneter Gleichmäßigkeit, Reinheit und Haftung auf dem Substrat erzeugen.
- Vielseitigkeit: Es kann eine breite Palette von Materialien abscheiden, darunter Metalle, Keramik und Polymere.
- Komplexe Geometrien: CVD kann komplexe Formen und komplizierte Geometrien beschichten und eignet sich daher für eine Vielzahl von Anwendungen.
-
Vergleich mit Physical Vapour Deposition (PVD):
- Obwohl sowohl CVD als auch PVD zur Abscheidung dünner Schichten verwendet werden, unterscheiden sie sich grundlegend in ihren Mechanismen. PVD beruht auf physikalischen Prozessen wie Verdampfen oder Sputtern, während CVD chemische Reaktionen beinhaltet. Aufgrund dieser Unterscheidung eignet sich CVD besonders für Anwendungen, die eine präzise Kontrolle der Filmzusammensetzung und -eigenschaften erfordern.
-
Polymerisation mittels CVD:
- CVD kann auch verwendet werden, um Materialien direkt auf einem Substrat zu polymerisieren. Beispielsweise kann Poly(paraxylol) mittels CVD in einer Vakuumkammer abgeschieden werden, wo der Monomerdampf bei Kontakt mit dem Substrat polymerisiert und einen dünnen Polymerfilm bildet.
-
Umwelt- und Sicherheitsaspekte:
- Bei CVD-Prozessen kommen häufig gefährliche Chemikalien und hohe Temperaturen zum Einsatz, was strenge Sicherheitsprotokolle erforderlich macht. Eine ordnungsgemäße Belüftung, Abfallentsorgung und persönliche Schutzausrüstung sind für einen sicheren Betrieb unerlässlich.
Zusammenfassend ist das chemische Gasphasenabscheidungsverfahren eine vielseitige und leistungsstarke Technik zur Abscheidung dünner Filme mit hoher Präzision und Qualität. Seine Nutzung chemischer Reaktionen ermöglicht die Herstellung von Filmen mit maßgeschneiderten Eigenschaften, was es in der modernen Fertigung und Technologie unverzichtbar macht. Ausführlichere Informationen zum Thema finden Sie im chemische Gasphasenabscheidung Verfahren.
Übersichtstabelle:
Aspekt | Einzelheiten |
---|---|
Definition | CVD scheidet dünne Filme durch chemische Reaktionen in der Dampfphase ab. |
Wichtige Schritte | 1. Transport von Gasen 2. Adsorption 3. Oberflächenreaktionen 4. Filmwachstum |
Anwendungen | Halbleiter, Schutzbeschichtungen, optische Filme, Nanostrukturen. |
Vorteile | Hochwertige Folien, Vielseitigkeit, Fähigkeit zur Beschichtung komplexer Geometrien. |
Vergleich mit PVD | CVD nutzt chemische Reaktionen; PVD beruht auf physikalischen Prozessen. |
Sicherheitsüberlegungen | Erfordert den Umgang mit gefährlichen Chemikalien und hohen Temperaturen. |
Entdecken Sie, wie CVD Ihre Fertigungsprozesse verbessern kann – Kontaktieren Sie uns noch heute für fachkundige Beratung!