Beim Hartlöten handelt es sich um einen Metallverbindungsprozess, bei dem ein Füllmetall über seinen Schmelzpunkt erhitzt und durch Kapillarwirkung zwischen zwei oder mehr eng anliegenden Teilen verteilt wird. Die zum Löten erforderliche Temperatur liegt typischerweise zwischen 450 °C (842 °F) und 900 °C (1652 °F), abhängig von den zu verbindenden Materialien und der Art des verwendeten Zusatzmetalls. Der Prozess erfordert eine sorgfältige Temperaturkontrolle, um einen ordnungsgemäßen Fluss des Zusatzmetalls sicherzustellen, ohne die Grundmaterialien zu beschädigen. Im Folgenden untersuchen wir die Schlüsselfaktoren, die die Löttemperatur beeinflussen, und wie man den geeigneten Bereich für bestimmte Anwendungen bestimmt.
Wichtige Punkte erklärt:
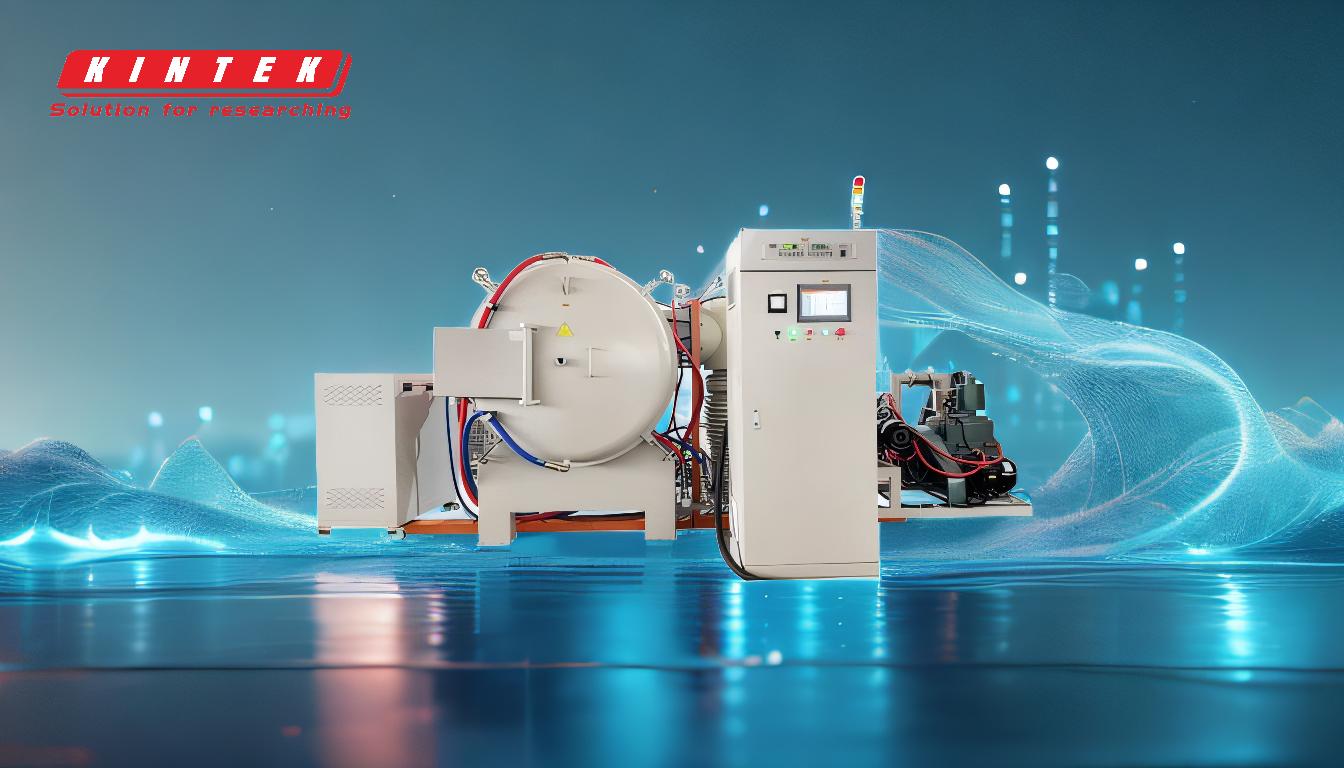
-
Definition der Löttemperatur
- Die Löttemperatur bezieht sich auf den Bereich, in dem das Zusatzmetall schmilzt und in die Verbindung zwischen den Grundmetallen fließt.
- Die Temperatur muss hoch genug sein, um das Zusatzmetall zu schmelzen, aber niedrig genug, um ein Schmelzen der Grundmaterialien zu vermeiden.
-
Typischer Temperaturbereich
- Der allgemeine Bereich zum Hartlöten beträgt 450 °C bis 900 °C (842 °F bis 1652 °F) .
- Beispielsweise schmelzen Füllmetalle auf Silberbasis typischerweise zwischen 600 °C und 800 °C (1112 °F bis 1472 °F), während Füllmetalle auf Kupferbasis höhere Temperaturen erfordern, oft etwa 800 °C bis 900 °C (1472 °F). bis 1652°F).
-
Faktoren, die die Löttemperatur beeinflussen
- Grundmaterialeigenschaften: Verschiedene Metalle und Legierungen haben unterschiedliche Schmelzpunkte und Wärmeleitfähigkeiten, die sich auf die erforderliche Löttemperatur auswirken.
- Zusammensetzung des Zusatzmetalls: Der Schmelzpunkt des Zusatzmetalls bestimmt die Mindestlöttemperatur. Zu den gängigen Zusatzmetallen gehören Silber-, Kupfer-, Aluminium- und Nickellegierungen.
- Gelenkdesign: Der Spalt zwischen den zu verbindenden Teilen beeinflusst die Kapillarwirkung und die Wärmeverteilung und beeinflusst so die optimale Temperatur.
- Atmosphäre: Das Vorhandensein einer kontrollierten Atmosphäre (z. B. Inertgas oder Vakuum) kann den Lötprozess und die Temperaturanforderungen beeinflussen.
-
Bedeutung der Temperaturkontrolle
- Vermeidung von Schäden durch unedle Metalle: Übermäßige Hitze kann die Grundmaterialien verformen oder schmelzen und so die Integrität der Verbindung beeinträchtigen.
- Gewährleistung eines ordnungsgemäßen Flusses des Zusatzwerkstoffs: Unzureichende Hitze kann dazu führen, dass das Füllmetall nicht ausreichend fließt, was zu schwachen Verbindungen führt.
- Oxidationsprävention: Die Aufrechterhaltung der richtigen Temperatur trägt dazu bei, Oxidation zu minimieren, die die Bindung schwächen kann.
-
Bestimmen der richtigen Temperatur für Ihre Anwendung
- Konsultieren Sie die Spezifikationen des Zusatzwerkstoffherstellers für den empfohlenen Schmelzbereich.
- Bedenken Sie das Schmelzpunkte der Grundmaterialien und thermische Eigenschaften.
- Testen Sie den Prozess an Probeverbindungen, um die Temperatur für optimale Ergebnisse zu optimieren.
-
Häufige Anwendungen und ihre Temperaturanforderungen
- Kupferrohr: Typischerweise bei etwa 800 °C (1472 °F) unter Verwendung von Kupfer-Phosphor-Füllmetallen gelötet.
- Edelstahl: Oft bei 700 °C bis 900 °C (1292 °F bis 1652 °F) mit silberbasierten oder nickelbasierten Füllstoffen gelötet.
- Aluminiumkomponenten: Erfordern niedrigere Temperaturen, etwa 450 °C bis 600 °C (842 °F bis 1112 °F), bei Verwendung von Aluminium-Silizium-Füllmetallen.
-
Geräte und Werkzeuge für das Temperaturmanagement
- Öfen: Wird für eine gleichmäßige Erwärmung in kontrollierten Umgebungen verwendet.
- Fackeln: Stellen Sie lokale Wärme für kleinere oder kompliziertere Gelenke bereit.
- Temperatursensoren: Gewährleisten Sie eine präzise Überwachung und Steuerung des Lötprozesses.
Wenn Sie diese Schlüsselpunkte verstehen, können Sie die geeignete Löttemperatur für Ihre spezifische Anwendung auswählen und so starke, dauerhafte und zuverlässige Verbindungen gewährleisten.
Übersichtstabelle:
Aspekt | Einzelheiten |
---|---|
Typischer Temperaturbereich | 450 °C bis 900 °C (842 °F bis 1652 °F) |
Beispiele für Zusatzwerkstoffe | Silberbasis: 600°C–800°C, Kupferbasis: 800°C–900°C, Aluminium: 450°C–600°C |
Wichtige Einflussfaktoren | Grundmaterial, Zusatzwerkstoff, Verbindungsdesign und Atmosphäre |
Anwendungen | Kupferrohre: ~800 °C, Edelstahl: 700 °C–900 °C, Aluminium: 450 °C–600 °C |
Benötigen Sie Hilfe bei der Bestimmung der richtigen Löttemperatur für Ihr Projekt? Kontaktieren Sie noch heute unsere Experten !