Die Abscheidung ist ein entscheidender Prozess in der Materialwissenschaft und der Dünnschichttechnologie, bei dem ein Material auf einem Substrat abgeschieden wird, um einen dünnen Film zu bilden. Die Temperatur, bei der die Abscheidung erfolgt, kann abhängig von der spezifischen Abscheidungstechnik, dem abzuscheidenden Material und den gewünschten Eigenschaften des resultierenden Films stark variieren. In dieser Antwort werden die Faktoren untersucht, die die Abscheidungstemperatur beeinflussen, und wie sie sich auf die Eigenschaften des Films auswirkt.
Wichtige Punkte erklärt:
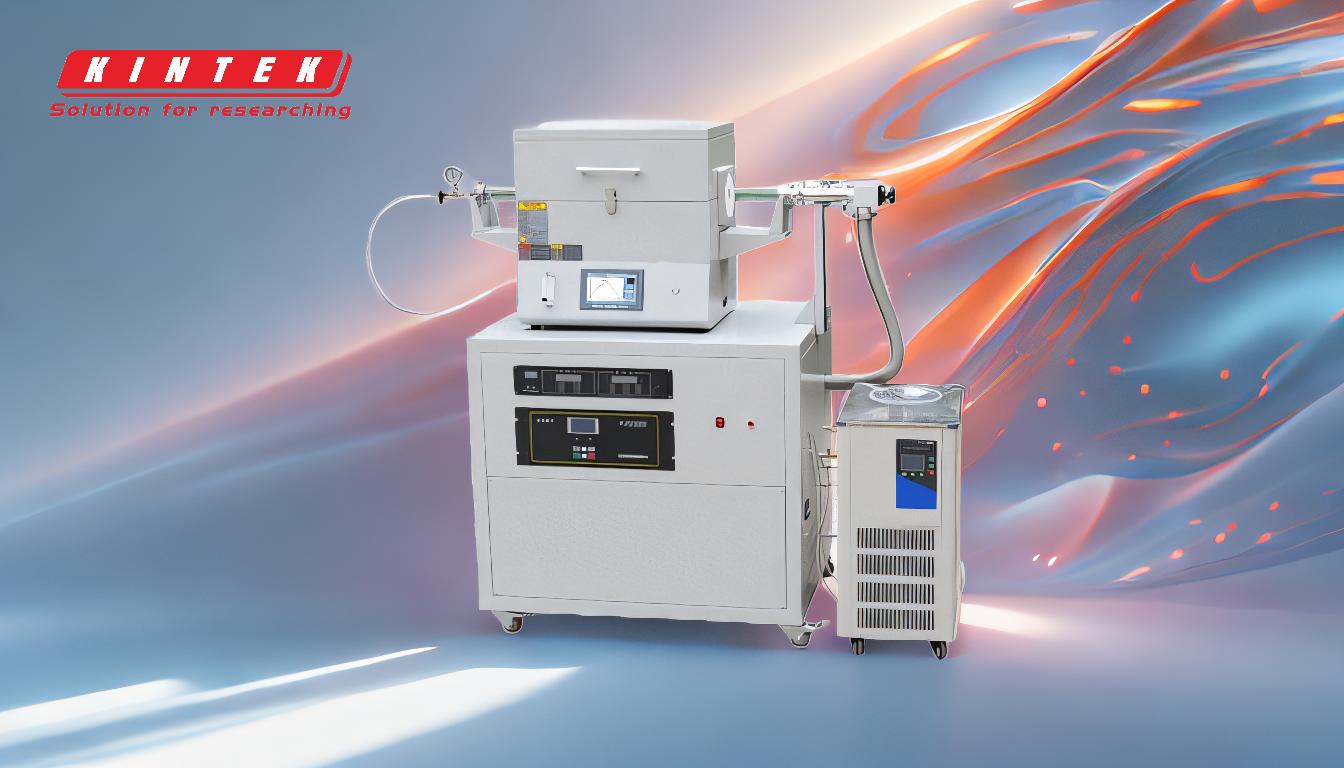
-
Abscheidungstechniken und Temperaturbereiche:
- Physikalische Gasphasenabscheidung (PVD): Techniken wie Sputtern und Verdampfen finden typischerweise bei Temperaturen zwischen Raumtemperatur und mehreren hundert Grad Celsius statt. Beispielsweise erfolgt das Sputtern von Metallen wie Aluminium oder Titan häufig bei Temperaturen zwischen 50 °C und 300 °C.
- Chemische Gasphasenabscheidung (CVD): CVD-Prozesse wie thermisches CVD oder plasmaunterstütztes CVD erfordern im Allgemeinen höhere Temperaturen, häufig zwischen 500 °C und 1200 °C, abhängig vom Material und den gewünschten Filmeigenschaften. Beispielsweise kann die Abscheidung von Siliziumdioxid mittels CVD bei Temperaturen um 700 °C bis 900 °C erfolgen.
- Atomlagenabscheidung (ALD): ALD ist ein Niedertemperaturprozess, der typischerweise zwischen 100 °C und 400 °C betrieben wird und sich daher für temperaturempfindliche Substrate eignet.
-
Einfluss der Temperatur auf Filmeigenschaften:
- Kristallinität: Höhere Abscheidungstemperaturen führen oft zu einer besseren Kristallinität im abgeschiedenen Film. Beispielsweise können bei PVD erhöhte Temperaturen die Beweglichkeit von Adatomen erhöhen, was zu geordneteren Kristallstrukturen führt.
- Stress und Adhäsion: Die Temperatur kann die Beanspruchung und Haftung der Folie beeinflussen. Höhere Temperaturen können die intrinsische Spannung verringern, könnten aber aufgrund der unterschiedlichen Wärmeausdehnungskoeffizienten zwischen Film und Substrat auch die thermische Spannung erhöhen.
- Dichte und Gleichmäßigkeit: Erhöhte Temperaturen können die Filmdichte und Gleichmäßigkeit verbessern, indem sie eine bessere Oberflächendiffusion der abgeschiedenen Atome fördern. Zu hohe Temperaturen können jedoch aufgrund erhöhter Desorptions- oder Wiederverdampfungsraten zu Ungleichmäßigkeiten führen.
-
Kompromisse bei den Abscheidungsbedingungen:
- Abscheidungsrate vs. Temperatur: Wie in der Referenz erwähnt, erfordern schnellere Abscheidungsraten oft höhere Temperaturen oder Leistung, was sich auf die Filmeigenschaften auswirken kann. Beispielsweise kann eine Erhöhung der Temperatur beim CVD die Reaktionskinetik beschleunigen, was zu höheren Abscheidungsraten führt, aber möglicherweise die Filmqualität beeinträchtigt.
- Materialspezifische Überlegungen: Unterschiedliche Materialien haben unterschiedliche Temperaturabhängigkeiten. Beispielsweise kann die Abscheidung organischer Materialien mittels PVD niedrigere Temperaturen erfordern, um eine Zersetzung zu verhindern, wohingegen die Abscheidung hochschmelzender Metalle wie Wolfram mittels CVD häufig hohe Temperaturen erfordert, um die gewünschten Filmeigenschaften zu erreichen.
-
Überlegungen zum Substrat:
- Thermische Stabilität: Die thermische Stabilität des Substrats ist ein entscheidender Faktor bei der Bestimmung der Abscheidungstemperatur. Beispielsweise können sich Polymersubstrate bei hohen Temperaturen zersetzen, wodurch der Abscheidungsprozess auf niedrigere Temperaturen beschränkt wird.
- Nichtübereinstimmung der Wärmeausdehnung: Nicht übereinstimmende Wärmeausdehnungskoeffizienten zwischen Film und Substrat können zu Spannungen und Delaminierung führen, insbesondere bei hohen Abscheidungstemperaturen.
-
Prozessoptimierung:
- Balanceakt: Das Erreichen der gewünschten Filmeigenschaften erfordert häufig einen Kompromiss zwischen Abscheidungstemperatur, -rate und anderen Prozessparametern. Beispielsweise könnten bei der ALD niedrigere Temperaturen verwendet werden, um eine konforme Abdeckung komplexer Geometrien sicherzustellen, auch wenn dies einen Verlust an Filmdichte bedeutet.
- Fortgeschrittene Techniken: Techniken wie plasmaunterstützte CVD oder gepulste Laserabscheidung können niedrigere Abscheidungstemperaturen ermöglichen und dennoch qualitativ hochwertige Filme erzeugen, was eine Möglichkeit bietet, einige der mit der Temperatur verbundenen Kompromisse abzumildern.
Zusammenfassend ist die Temperatur, bei der die Abscheidung erfolgt, ein kritischer Parameter, der die Eigenschaften des abgeschiedenen Films maßgeblich beeinflusst. Sie schwankt stark je nach Abscheidungstechnik, Material und Substrat und erfordert oft das Abwägen mehrerer Faktoren, um die gewünschten Filmeigenschaften zu erreichen. Das Verständnis dieser Zusammenhänge ist für die Optimierung von Abscheidungsprozessen in verschiedenen Anwendungen von entscheidender Bedeutung.
Übersichtstabelle:
Ablagerungstechnik | Temperaturbereich | Hauptmerkmale |
---|---|---|
Physikalische Gasphasenabscheidung (PVD) | 50°C bis 300°C | Geeignet für Metalle wie Aluminium und Titan |
Chemische Gasphasenabscheidung (CVD) | 500°C bis 1200°C | Ideal für hochwertige Filme wie Siliziumdioxid |
Atomlagenabscheidung (ALD) | 100°C bis 400°C | Perfekt für temperaturempfindliche Untergründe |
Einfluss der Temperatur | Auswirkung auf Filmeigenschaften | |
Höhere Temperaturen | Verbesserte Kristallinität, reduzierte Eigenspannung, bessere Dichte | |
Niedrigere Temperaturen | Verhindert die Zersetzung des Substrats, geeignet für organische Materialien | |
Überlegungen zum Substrat | Schlüsselfaktoren | |
Thermische Stabilität | Begrenzt die Abscheidungstemperatur für empfindliche Substrate | |
Nichtübereinstimmung der Wärmeausdehnung | Kann bei hohen Temperaturen zu Spannungen oder Delamination führen |
Benötigen Sie Hilfe bei der Optimierung Ihres Abscheidungsprozesses? Kontaktieren Sie noch heute unsere Experten für maßgeschneiderte Lösungen!