Kalzinieren und Schmelzen sind Hochtemperaturverfahren, die spezielle Öfen erfordern, um die gewünschten chemischen und physikalischen Umwandlungen zu erreichen.Bei der Kalzinierung werden Materialien unter Abwesenheit oder begrenzter Zufuhr von Luft auf hohe Temperaturen erhitzt, um eine thermische Zersetzung zu bewirken, während beim Schmelzen Erze geschmolzen werden, um Metalle zu gewinnen.Zu den Öfen, die für diese Prozesse verwendet werden, gehören Muffelöfen, Flammöfen, Schachtöfen und Drehrohröfen.Diese Öfen sind so konzipiert, dass sie eine gleichmäßige Erwärmung, eine präzise Temperaturregelung und die Möglichkeit zur Verarbeitung großer Mengen an Materialien bieten.Für industrielle Anwendungen werden je nach Kosten- und Umweltaspekten häufig befeuerte oder elektrische Prozessöfen verwendet.Im Folgenden werden die wichtigsten Arten von Öfen für die Kalzinierung und Verhüttung, ihre Konfigurationen und ihre Anwendungen erläutert.
Die wichtigsten Punkte erklärt:
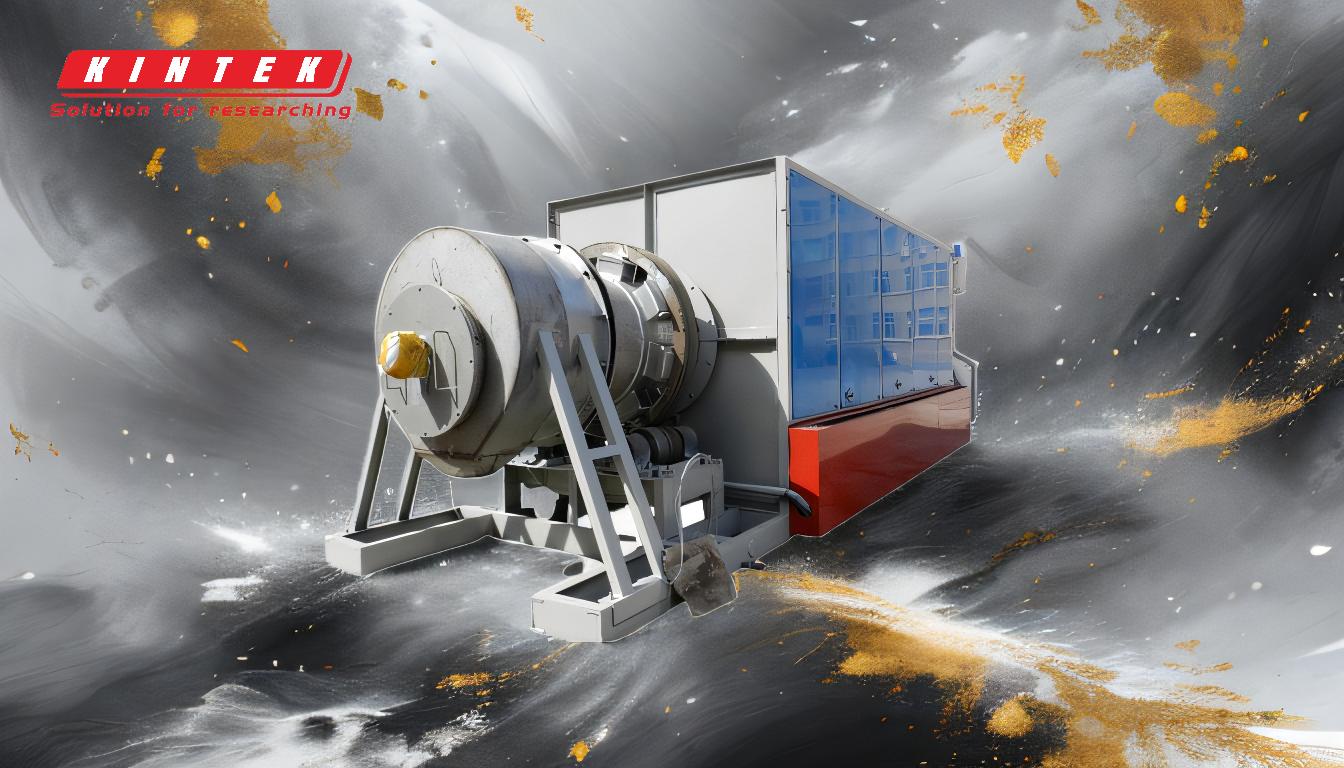
-
Muffelöfen:
- Muffelöfen werden häufig zum Kalzinieren verwendet, da sie eine gleichmäßige Beheizung gewährleisten und das Material von den Verbrennungsgasen isolieren.Sie sind mit Heizelementen ausgestattet, die eine Kammer umgeben und eine präzise Temperaturregelung gewährleisten.
- Anwendungen:Kalzinierung von Materialien wie Kalkstein (zur Herstellung von Kalk), Keramik und Katalysatoren.
- Vorteile:Hohe Temperaturgleichmäßigkeit, Isolierung von Verunreinigungen und Eignung für kleine Labor- oder Industrieanwendungen.
-
Hallraumöfen:
- Die großen, industriell genutzten Öfen werden zum Schmelzen und Kalzinieren verwendet.Sie verfügen über eine flache Herdplatte und ein Dach, das die Wärme auf das Material reflektiert und so eine effiziente Wärmeübertragung gewährleistet.
- Anwendungen:Verhüttung von Metallen wie Kupfer und Blei sowie Kalzinierung von Erzen.
- Vorteile:Hohe Kapazität, Fähigkeit, große Mengen zu verarbeiten, und Eignung für den Dauerbetrieb.
-
Schachtöfen:
- Schachtöfen sind vertikale Öfen, die zum Kalzinieren und Schmelzen verwendet werden.Bei ihrem Betrieb werden die Materialien von oben aufgegeben und durch eine beheizte Kammer nach unten befördert, wo sie einer Wärmebehandlung unterzogen werden.
- Anwendungen:Kalzinierung von Kalkstein und Dolomit sowie Verhüttung von Eisenerzen in Hochöfen.
- Vorteile:Effiziente Wärmenutzung, kontinuierlicher Betrieb und hoher Durchsatz.
-
Drehrohröfen:
- Drehrohröfen sind zylindrische Öfen, die sich drehen, um eine gleichmäßige Erwärmung des Materials zu gewährleisten.Sie werden in der Regel sowohl für Kalzinierungs- als auch für Schmelzprozesse verwendet.
- Anwendungen:Kalzinierung von Zementklinker, Tonerde und anderen Industriemineralien sowie Verhüttung von Erzen.
- Vorteile:Hoher Wärmewirkungsgrad, Fähigkeit zur Verarbeitung einer breiten Palette von Materialien und kontinuierliche Verarbeitung.
-
Elektrische vs. befeuerte Prozessöfen:
- Elektrische Prozessöfen werden zum Kalzinieren und Schmelzen in Bereichen eingesetzt, in denen der Umweltschutz von entscheidender Bedeutung ist.Sie sind teurer, bieten aber eine präzise Temperaturregelung und erzeugen keine Emissionen.
- Befeuerte Prozessöfen verwenden verbrennende Brennstoffe (z. B. Gas oder Öl) zur Wärmeerzeugung und werden aufgrund ihrer geringeren Betriebskosten häufig in der Industrie eingesetzt.
- Anwendungen:Elektroöfen werden bevorzugt für hochreine Materialien eingesetzt, während befeuerte Öfen in Raffinerien, petrochemischen Anlagen und bei der Metallverhüttung verwendet werden.
-
Spezialisierte Öfen für industrielle Anwendungen:
- Drehtrommelöfen, Rollenherdöfen, Stoßplattenöfen und Hubbodenöfen sind Spezialöfen, die zum Sintern und Schmelzen von Industrieprodukten eingesetzt werden.
- Anwendungen:Sintern von Keramiken, Metallen und anderen Materialien sowie Schmelzen von Erzen.
- Vorteile:Hoher Durchsatz, präzise Temperaturregelung und Eignung für großtechnische Verfahren.
Wenn man die spezifischen Anforderungen von Kalzinierungs- und Schmelzprozessen, wie Temperaturbereich, Materialvolumen und Umweltaspekte, kennt, kann der geeignete Ofentyp ausgewählt werden, um optimale Leistung und Effizienz zu gewährleisten.
Zusammenfassende Tabelle:
Ofentyp | Anwendungen | Vorteile |
---|---|---|
Muffelöfen | Kalzinierung von Kalkstein, Keramik, Katalysatoren | Hohe Temperaturgleichmäßigkeit, Isolierung von Verunreinigungen, Einsatz in kleinem Maßstab |
Flammöfen | Verhüttung von Kupfer, Blei; Kalzinierung von Erzen | Hohe Kapazität, Verarbeitung großer Mengen, kontinuierlicher Betrieb |
Schachtöfen | Kalzinierung von Kalkstein, Dolomit; Verhüttung von Eisenerzen | Effiziente Wärmenutzung, kontinuierlicher Betrieb, hoher Durchsatz |
Drehrohröfen | Brennen von Zementklinker, Tonerde; Schmelzen von Erzen | Hoher thermischer Wirkungsgrad, breites Materialspektrum, kontinuierliche Verarbeitung |
Elektrische Prozessöfen | Hochreine Materialien, schadstoffempfindliche Anwendungen | Präzise Temperaturregelung, keine Emissionen |
Befeuerte Prozessöfen | Raffinerien, petrochemische Anlagen, Metallverhüttung | Geringere Betriebskosten, weit verbreitet in industriellen Umgebungen |
Spezialisierte Öfen | Sintern von Keramiken, Metallen; Schmelzen von Erzen | Hoher Durchsatz, präzise Temperaturregelung, großindustrieller Betrieb |
Benötigen Sie Hilfe bei der Auswahl des richtigen Ofens für Ihren Kalzinierungs- oder Schmelzprozess? Kontaktieren Sie noch heute unsere Experten !