Wasserstoff wird aufgrund seiner einzigartigen Eigenschaften und Vorteile häufig im Sinterprozess eingesetzt.Er wirkt als hochwirksames Reduktionsmittel und ist in der Lage, Oberflächenoxide und Verunreinigungen wie Siliziumdioxid aus Legierungen zu entfernen, insbesondere bei Teilen aus rostfreiem Stahl.Das Ergebnis sind hochreine Sinterprodukte mit hervorragenden mechanischen Eigenschaften und einer Dichte, die mit der von Knetteilen vergleichbar ist.Darüber hinaus sorgt Wasserstoff für eine hochwertige Sinteratmosphäre, die die Leistung des Ofens verbessert und niedrigere Taupunkte ermöglicht, was die Reduktionsbedingungen verbessert.Seine Fähigkeit, Teileigenschaften wie Dichte und Korrosionsbeständigkeit zu maximieren, macht ihn bei Hochtemperatursinterprozessen unverzichtbar.
Die wichtigsten Punkte erklärt:
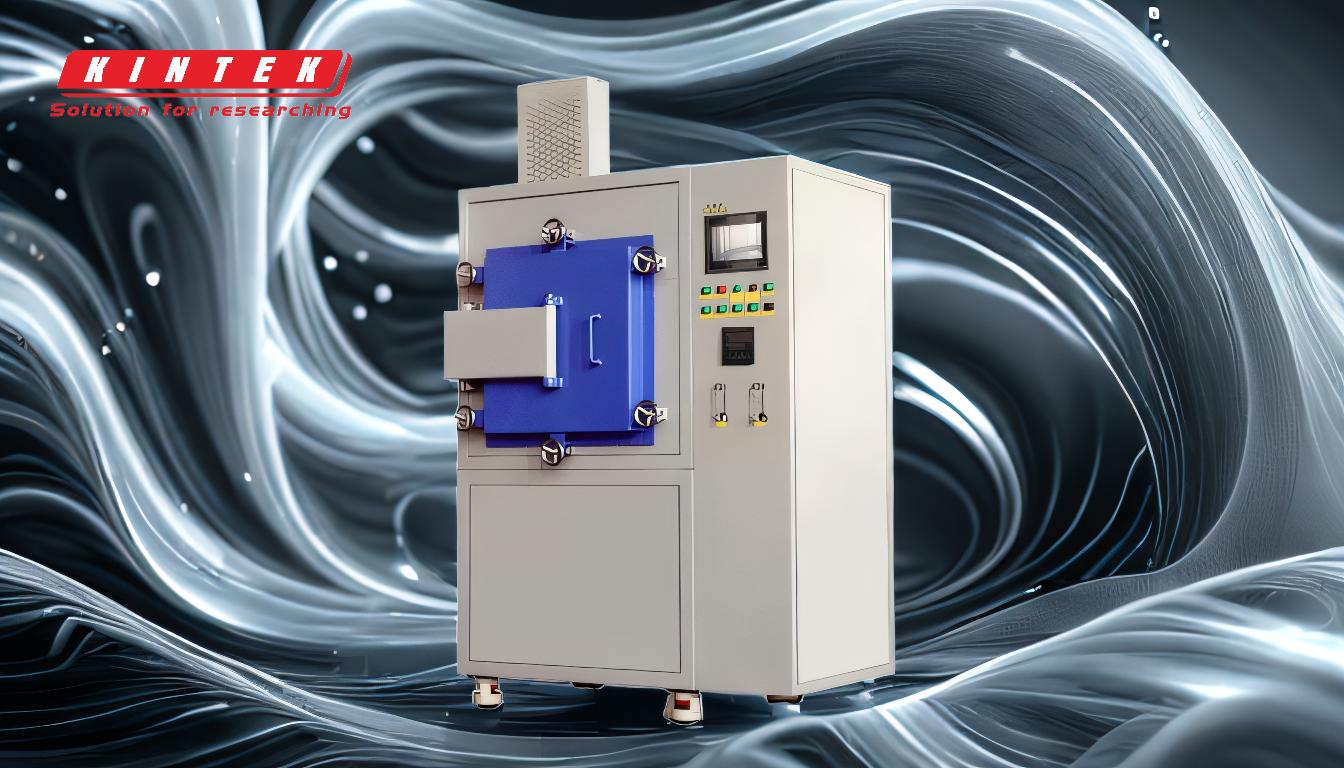
-
Hohe Reinheit und Reduktionsvermögen
- Wasserstoffgas mit einem Reinheitsgrad von >99,9995% ist ideal für Sinterprozesse.
- Es reduziert effektiv Oberflächenoxide und entfernt Verunreinigungen wie Siliziumdioxid (SiO2) aus Legierungen und sorgt so für sauberere und einheitlichere Materialeigenschaften.
- Dieser Reduktionsprozess ist besonders wichtig für Teile aus rostfreiem Stahl, wo Oberflächenoxide die Qualität des Endprodukts beeinträchtigen können.
-
Verbesserte Sinteratmosphäre
- Wasserstoff schafft eine hochwertige Atmosphäre im Sinterofen und verbessert so die Gesamtleistung.
- Er senkt den Taupunkt, was die Reduktionsbedingungen verbessert und das Risiko der Oxidation während des Sinterprozesses minimiert.
- Diese kontrollierte Umgebung ist für die Erzielung gleichmäßiger und hochwertiger Sinterprodukte unerlässlich.
-
Verbesserte mechanische Eigenschaften
- Durch die Entfernung von Verunreinigungen und die Reduzierung von Oxiden trägt das Wasserstoffsintern zu einer hohen Dichte des Endprodukts bei, die mit der von Knetteilen vergleichbar ist.
- Dies führt zu besseren mechanischen Eigenschaften, wie z. B. einer höheren Festigkeit, Haltbarkeit und Korrosionsbeständigkeit.
- Diese Verbesserungen sind entscheidend für Anwendungen, die Hochleistungsmaterialien erfordern.
-
Vielseitigkeit bei Sinteranwendungen
- Wasserstoff kann in verschiedenen Formen verwendet werden, z. B. als reiner Wasserstoff, als Wasserstoff/Stickstoff-Gasgemisch oder als dissoziiertes Ammoniak, wodurch er sich an verschiedene Sinterverfahren anpassen lässt.
- Seine Kompatibilität mit einer Vielzahl von Materialien, einschließlich Metallen und Keramiken, macht ihn zu einer vielseitigen Wahl für das industrielle Sintern.
-
Wirtschaftliche und betriebliche Vorteile
- Der Einsatz von Wasserstoff kann zu einer besseren Ofenleistung führen, die Betriebskosten senken und die Effizienz steigern.
- Seine Fähigkeit, die Reduktionsbedingungen zu verbessern und die Taupunkte zu senken, minimiert den Bedarf an zusätzlichen Nachbearbeitungsschritten und spart so Zeit und Ressourcen.
-
Entscheidende Rolle bei der Herstellung von Teilen hoher Qualität
- Das Wasserstoffsintern ist für die Herstellung von Teilen mit hoher Dichte, Korrosionsbeständigkeit und mechanischer Integrität unerlässlich.
- Es stellt sicher, dass das Endprodukt strengen Qualitätsstandards entspricht und eignet sich daher für anspruchsvolle Anwendungen in Branchen wie der Luft- und Raumfahrt, der Automobilindustrie und der Medizintechnik.
Zusammenfassend lässt sich sagen, dass die einzigartigen Eigenschaften von Wasserstoff ihn zu einem unverzichtbaren Bestandteil des Sinterprozesses machen, da er Vorteile wie hohe Reinheit, effektive Reduzierung von Verunreinigungen und verbesserte mechanische Eigenschaften bietet.Seine Fähigkeit, eine kontrollierte und effiziente Sinterumgebung zu schaffen, gewährleistet die Herstellung von qualitativ hochwertigen Teilen und macht ihn zu einer bevorzugten Wahl für industrielle Anwendungen.
Zusammenfassende Tabelle:
Hauptnutzen | Beschreibung |
---|---|
Hohe Reinheit | Wasserstoff (>99,9995%) reduziert Oxide und entfernt Verunreinigungen wie Kieselsäure. |
Verbesserte Atmosphäre | Senkt den Taupunkt, verbessert die Reduktionsbedingungen und minimiert das Oxidationsrisiko. |
Verbesserte mechanische Eigenschaften | Erzielt eine hohe Dichte, Festigkeit und Korrosionsbeständigkeit. |
Vielseitigkeit | Kompatibel mit Metallen, Keramiken und verschiedenen Gasgemischen. |
Wirtschaftliche Vorteile | Reduziert die Betriebskosten und den Nachbearbeitungsbedarf. |
Hochwertige Teile | Stellt sicher, dass die Teile die strengen Normen für die Luft- und Raumfahrt, die Automobilindustrie und die Medizintechnik erfüllen. |
Verbessern Sie Ihren Sinterprozess mit Wasserstoff. Kontaktieren Sie noch heute unsere Experten um mehr zu erfahren!