Die Erhöhung der Temperatur während des Schmiedens ist ein entscheidender Aspekt des Metallbearbeitungsprozesses, da sie sich direkt auf die Eigenschaften des Materials und die Leichtigkeit der Formgebung auswirkt.Beim Schmieden wird Metall durch Druckkräfte in die gewünschte Form gebracht, und die Temperatur spielt eine entscheidende Rolle für den Erfolg dieses Prozesses.Das Erhitzen des Metalls auf hohe Temperaturen macht es formbarer, verringert die für die Verformung erforderliche Kraft und minimiert das Risiko von Rissen oder Brüchen.Außerdem ermöglichen höhere Temperaturen eine bessere Verfeinerung der Kornstruktur, was die mechanischen Eigenschaften des Endprodukts verbessert.Wenn man die Gründe für die Erhöhung der Temperatur beim Schmieden versteht, kann man den Prozess sowohl hinsichtlich der Effizienz als auch der Qualität optimieren.
Die wichtigsten Punkte werden erklärt:
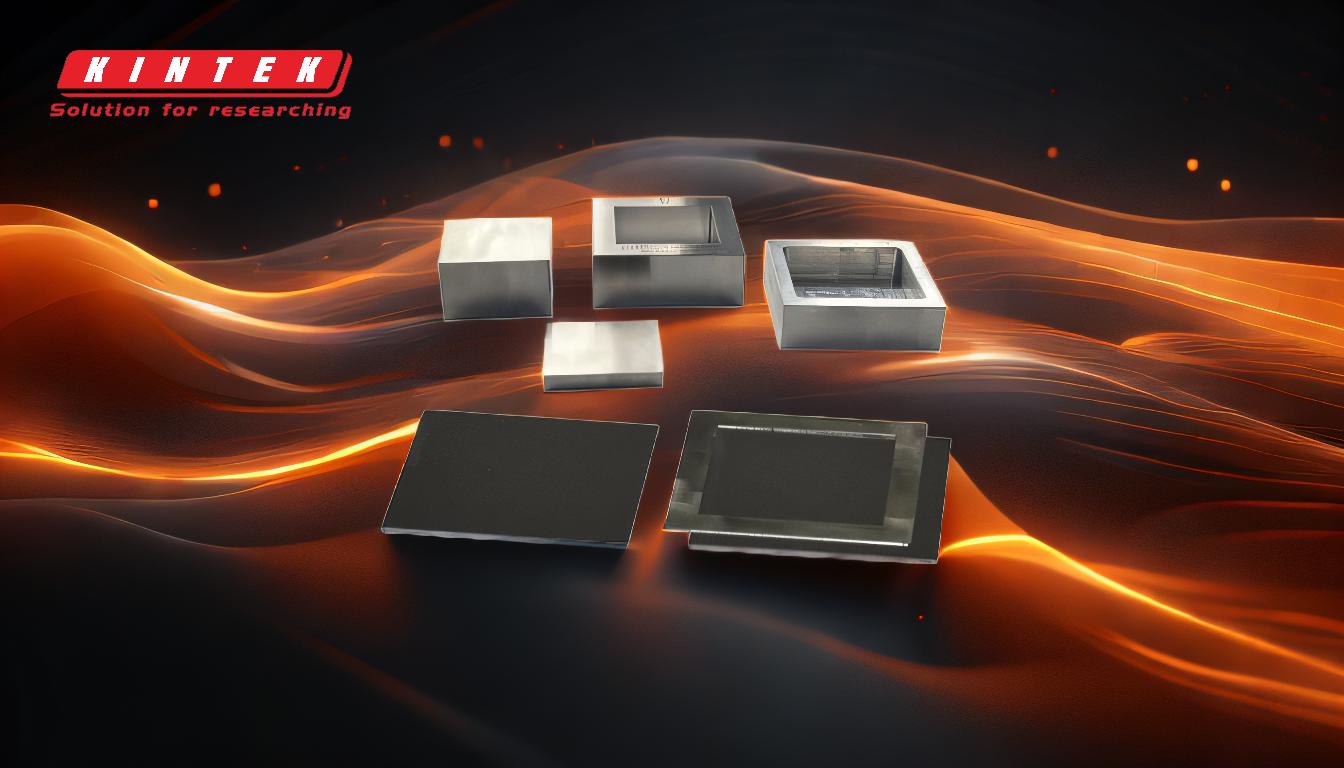
-
Verbesserte Verformbarkeit und reduzierter Kraftaufwand:
- Metalle werden durch Erhitzung dehnbarer und leichter formbar.Das liegt daran, dass die Wärmeenergie die atomaren Bindungen aufbricht, so dass sich das Metall unter Druck leichter verformen lässt.
- Bei höheren Temperaturen sinkt die Streckgrenze des Metalls, so dass weniger Kraft erforderlich ist, um die gewünschte Verformung zu erreichen.Dies verringert den Verschleiß der Schmiedeanlagen und senkt den Energieverbrauch.
-
Vorbeugung von Rissbildung und Versagen:
- Kaltschmieden (Schmieden bei oder nahe der Raumtemperatur) kann zu Sprödigkeit und Rissbildung führen, insbesondere bei härteren Metallen.Die Erwärmung des Metalls reduziert die inneren Spannungen und verhindert Brüche während der Verformung.
- Höhere Temperaturen sorgen für eine gleichmäßigere Verteilung der Spannungen im gesamten Material und minimieren so das Risiko örtlich begrenzter Ausfälle.
-
Verfeinerung der Kornstruktur:
- Durch Erhitzen des Metalls auf seine Rekristallisationstemperatur können sich die Körner im Material zu einer feineren, gleichmäßigeren Struktur umformen.Dadurch verbessern sich die mechanischen Eigenschaften des Schmiedeteils, wie Festigkeit, Zähigkeit und Ermüdungsbeständigkeit.
- Die richtige Temperaturkontrolle während des Schmiedens stellt sicher, dass der Kornfluss den Konturen der endgültigen Form folgt, was die Haltbarkeit des Teils erhöht.
-
Verbesserte Verarbeitbarkeit komplexer Formen:
- Bei höheren Temperaturen kann das Metall leichter in komplizierte Formen oder Gesenke fließen, so dass komplexe Geometrien mit Präzision geschmiedet werden können.
- Dies ist besonders wichtig für Branchen wie die Luft- und Raumfahrt und die Automobilindustrie, wo Bauteile oft komplizierte Konstruktionen und enge Toleranzen erfordern.
-
Energieeffizienz und Prozessoptimierung:
- Das Erhitzen erfordert zwar Energie, aber der Prozess wird insgesamt effizienter, weil weniger mechanische Kraft für die Formgebung des Metalls erforderlich ist.Dadurch halten sich Energiezufuhr und -abgabe die Waage, was den Prozess nachhaltiger macht.
- Ein angemessenes Temperaturmanagement verringert auch die Anzahl der erforderlichen Schmiedeschritte und spart so Zeit und Ressourcen.
-
Werkstoffspezifische Überlegungen:
- Die verschiedenen Metalle haben unterschiedliche Schmiedetemperaturbereiche.So wird Stahl in der Regel bei Temperaturen zwischen 950°C und 1250°C geschmiedet, während Aluminiumlegierungen bei niedrigeren Temperaturen (etwa 350°C bis 500°C) geschmiedet werden.
- Die Kenntnis der spezifischen Temperaturanforderungen für jedes Material gewährleistet optimale Ergebnisse und verhindert Überhitzung, die die Eigenschaften des Metalls beeinträchtigen kann.
-
Auswirkungen auf die Qualität des Endprodukts:
- Die Temperatur beim Schmieden wirkt sich direkt auf das Gefüge und die mechanischen Eigenschaften des Endprodukts aus.Eine ordnungsgemäße Erwärmung gewährleistet eine hochwertige Oberfläche mit minimalen Fehlern.
- Eine gleichmäßige Temperaturkontrolle während des gesamten Prozesses ist wichtig, um gleichmäßige Eigenschaften des Schmiedeteils zu erreichen.
Zusammenfassend lässt sich sagen, dass die Erhöhung der Temperatur während des Schmiedevorgangs von entscheidender Bedeutung ist, um die Verarbeitbarkeit des Metalls zu verbessern, Fehler zu vermeiden und die mechanischen Eigenschaften des Endprodukts zu verbessern.Durch eine sorgfältige Temperaturkontrolle können Hersteller effiziente, qualitativ hochwertige Schmiedeprozesse erzielen, die auf die spezifischen Anforderungen des Materials und das gewünschte Ergebnis zugeschnitten sind.
Zusammenfassende Tabelle:
Hauptnutzen | Erläuterung |
---|---|
Erhöhte Verformbarkeit | Durch die Erwärmung von Metallen werden diese dehnbarer, so dass weniger Kraft für die Verformung erforderlich ist. |
Verhindert Rissbildung und Versagen | Erhöhte Temperaturen reduzieren innere Spannungen und verhindern Brüche. |
Verfeinerung der Kornstruktur | Verbessert die Festigkeit, Zähigkeit und Ermüdungsbeständigkeit. |
Verbesserte Bearbeitbarkeit komplexer Formen | Ermöglicht präzises Schmieden komplizierter Formen. |
Energie-Effizienz | Reduziert den Bedarf an mechanischer Kraft und sorgt für ein Gleichgewicht zwischen Energiezufuhr und -abgabe. |
Materialspezifische Überlegungen | Verschiedene Metalle haben optimale Schmiedetemperaturbereiche für beste Ergebnisse. |
Einfluss auf die Qualität des Endprodukts | Gewährleistet eine hochwertige Oberfläche mit minimalen Fehlern und gleichmäßigen Eigenschaften. |
Sind Sie bereit, Ihren Schmiedeprozess zu optimieren? Kontaktieren Sie noch heute unsere Experten für maßgeschneiderte Lösungen!