Das Sputtern ist aufgrund grundlegender Unterschiede in den Mechanismen und Betriebsparametern langsamer als das Aufdampfen.Beim Sputtern werden einzelne Atome oder Cluster durch Ionenbeschuss aus einem Zielmaterial herausgeschleudert, was im Vergleich zum robusten Dampfstrom, der bei der thermischen Verdampfung erzeugt wird, ein weniger effizienter Prozess ist.Darüber hinaus wird beim Sputtern mit höheren Gasdrücken gearbeitet, was dazu führt, dass die gesputterten Teilchen mit der Gasphase kollidieren, was die Abscheidung weiter verlangsamt.Im Gegensatz dazu wird beim Aufdampfen das Ausgangsmaterial erhitzt, um einen Dampfstrom mit hoher Dichte zu erzeugen, was schnellere Abscheidungsraten ermöglicht.Diese Faktoren in Verbindung mit den Unterschieden bei der Energieübertragung, den Partikeltrajektorien und der Skalierbarkeit tragen zu den beim Sputtern beobachteten langsameren Abscheideraten bei.
Die wichtigsten Punkte werden erklärt:
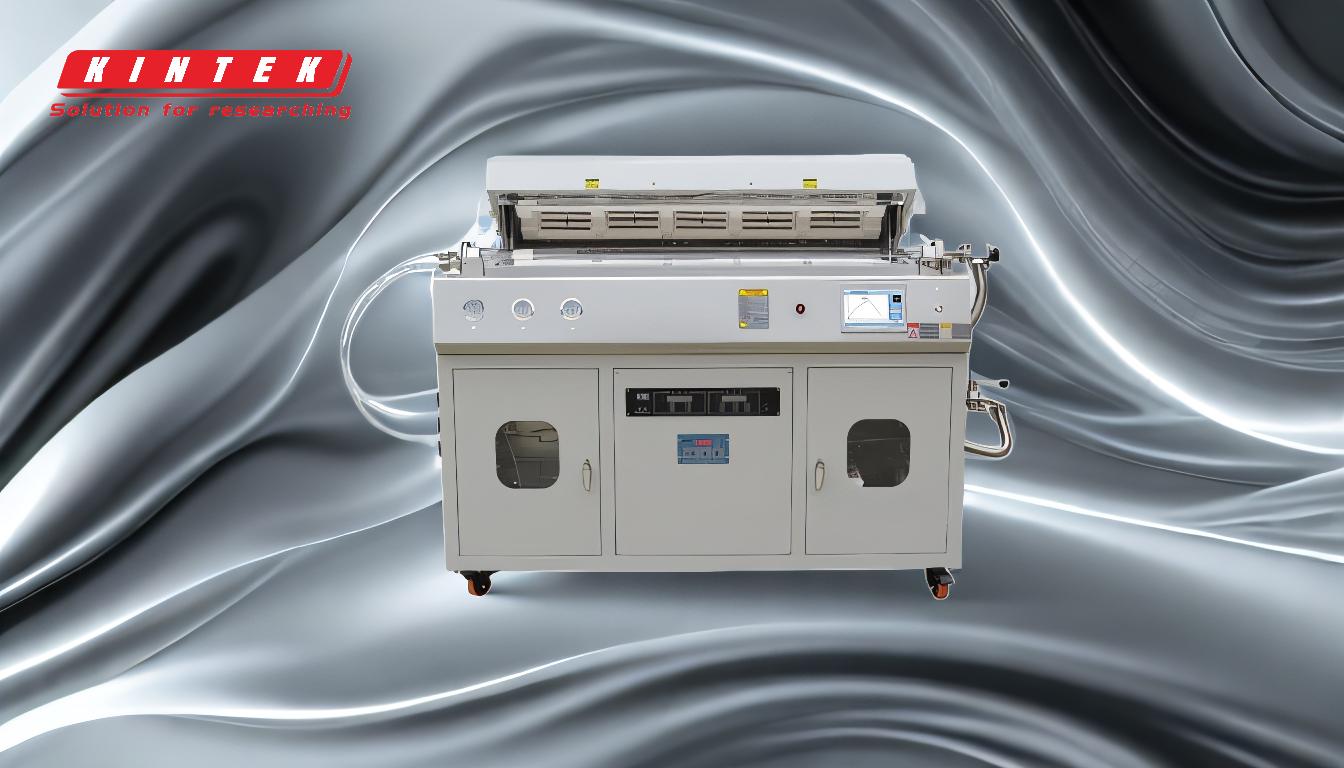
-
Mechanismus des Materialauswurfs:
- Sputtern:Bei diesem Verfahren stoßen energiereiche Ionen mit einem Zielmaterial zusammen und schleudern einzelne Atome oder kleine Cluster heraus.Dieses Verfahren ist weniger effizient, da es einen präzisen Ionenbeschuss und Energietransfer erfordert, um die Atome zu lösen.
- Verdampfung:Bei diesem Verfahren wird das Ausgangsmaterial über seine Verdampfungstemperatur hinaus erhitzt, wodurch ein dichter Dampfstrom entsteht.Dieser thermische Prozess ist effizienter und erzeugt einen höheren Materialfluss, was zu schnelleren Abscheideraten führt.
-
Energieübertragung und Verhalten der Partikel:
- Sputtern:Die ausgestoßenen Atome oder Cluster haben aufgrund des Ionenbeschusses eine höhere kinetische Energie.Allerdings wird beim Sputtern mit höheren Gasdrücken gearbeitet (5-15 mTorr), so dass die gesputterten Teilchen mit den Gasmolekülen zusammenstoßen und Energie verlieren, was ihre Abscheidung auf dem Substrat verlangsamt.
- Verdampfung:Die Partikel im Dampfstrom haben eine geringere kinetische Energie und folgen einer direkten Flugbahn zum Substrat.Dies minimiert den Energieverlust und ermöglicht eine schnellere Abscheidung.
-
Skalierbarkeit und Automatisierung:
- Sputtern:Das Sputtern ist zwar langsamer, bietet aber eine bessere Skalierbarkeit und kann für verschiedene Anwendungen automatisiert werden.Es ist besonders nützlich für die Abscheidung gleichmäßiger dünner Schichten auf unebenen Oberflächen, da es eine bessere Stufenabdeckung ermöglicht.
- Verdampfung:Obwohl die Verdampfung schneller ist, ist sie weniger skalierbar und in der Regel auf einfachere Geometrien beschränkt, da die Abscheidung in Sichtlinie erfolgt.
-
Abscheiderate und Effizienz:
- Sputtern:Die Abscheiderate ist von Natur aus niedriger, da der Prozess vom Ausstoß einzelner Atome oder kleiner Cluster abhängt.Darüber hinaus wird die Geschwindigkeit durch den Bedarf an Energiequellen mit höherer Leistung und komplexen Anlagen weiter eingeschränkt.
- Verdampfung:Das thermische Verfahren erzeugt einen robusten Dampfstrom, der höhere Abscheideraten und kürzere Laufzeiten ermöglicht.Dadurch eignet sich die Verdampfung besser für Anwendungen, die eine schnelle Beschichtung erfordern.
-
Filmqualität und Auswirkungen auf das Substrat:
- Sputtern:Erzeugt Schichten mit höherer Haftung, besserer Homogenität und kleinerer Korngröße.Allerdings können die Hochgeschwindigkeitsatome möglicherweise empfindliche Substrate beschädigen.
- Verdampfung:Das Aufdampfen ist zwar schneller, kann aber zu Schichten mit geringerer Haftung und größerer Korngröße führen.Aufgrund der geringeren Energie der abgeschiedenen Partikel ist es weniger wahrscheinlich, dass Substrate beschädigt werden.
-
Betriebsparameter:
- Sputtern:Der Betrieb erfolgt bei höherem Gasdruck, wodurch die Partikel thermisch erhitzt werden und ihre Abscheidung verlangsamt wird.Dies steht im Gegensatz zu der Niederdruckumgebung der Verdampfung, die eine schnellere und direktere Abscheidung ermöglicht.
- Verdampfung:Erfordert ein Hochvakuum, das Teilchenkollisionen minimiert und einen direkten Dampfstrom zum Substrat gewährleistet, was die Abscheidegeschwindigkeit erhöht.
Zusammenfassend lässt sich sagen, dass die Sputterbeschichtung langsamer ist als die Verdampfungsbeschichtung, da sie auf Ionenbeschuss, höhere Gasdrücke und die Notwendigkeit einer präzisen Energieübertragung angewiesen ist.Während das Sputtern Vorteile bei der Schichtqualität und der Skalierbarkeit bietet, ermöglichen der thermische Prozess und der direkte Dampfstrom der Verdampfung deutlich schnellere Abscheidungsraten.
Zusammenfassende Tabelle:
Blickwinkel | Sputter-Beschichtung | Verdampfungsabscheidung |
---|---|---|
Mechanismus | Der Ionenbeschuss schleudert einzelne Atome oder kleine Cluster aus. | Durch Erhitzen des Ausgangsmaterials wird ein Dampfstrom mit hoher Dichte erzeugt. |
Energieübertragung | Höhere kinetische Energie, aber verlangsamt durch Zusammenstöße in der Gasphase. | Niedrigere kinetische Energie bei direkter Ablagerung in Sichtweite. |
Ablagerungsrate | Langsamer aufgrund eines weniger effizienten Ausstoßes und höherer Gasdrücke. | Schneller aufgrund des robusten Dampfstroms und minimaler Partikelkollisionen. |
Qualität des Films | Höhere Adhäsion, bessere Homogenität, kleinere Korngrößen. | Geringere Adhäsion, größere Korngrößen, aber weniger Substratschäden. |
Skalierbarkeit | Besser für unebene Oberflächen und Automatisierung. | Aufgrund der Sichtverbindung auf einfachere Geometrien beschränkt. |
Betriebsdruck | Höhere Gasdrücke (5-15 mTorr). | Hochvakuum für minimale Teilchenkollisionen. |
Benötigen Sie Hilfe bei der Auswahl der richtigen Abscheidungsmethode für Ihre Anwendung? Kontaktieren Sie noch heute unsere Experten für eine persönliche Beratung!