Das Sputtern ist aufgrund grundlegender Unterschiede in den Mechanismen und Betriebsbedingungen langsamer als das Aufdampfen.Beim Sputtern werden die Atome mit Hilfe von energiereichen Ionen aus dem Zielmaterial herausgeschleudert, was im Vergleich zur thermischen Verdampfung bei der Verdampfung ein weniger effizienter Prozess ist.Beim Verdampfen wird das Ausgangsmaterial auf hohe Temperaturen erhitzt, wodurch ein robuster Dampfstrom entsteht, der schneller auf dem Substrat kondensiert.Außerdem findet das Sputtern bei höherem Gasdruck statt, so dass Kollisionen mit den Gasteilchen den Abscheidungsprozess verlangsamen, während die Verdampfung im Hochvakuum erfolgt, was eine direkte Flugbahn und eine schnellere Abscheidung ermöglicht.Diese Faktoren tragen gemeinsam dazu bei, dass beim Sputtern im Vergleich zum Verdampfen langsamere Abscheidungsraten zu beobachten sind.
Die wichtigsten Punkte werden erklärt:
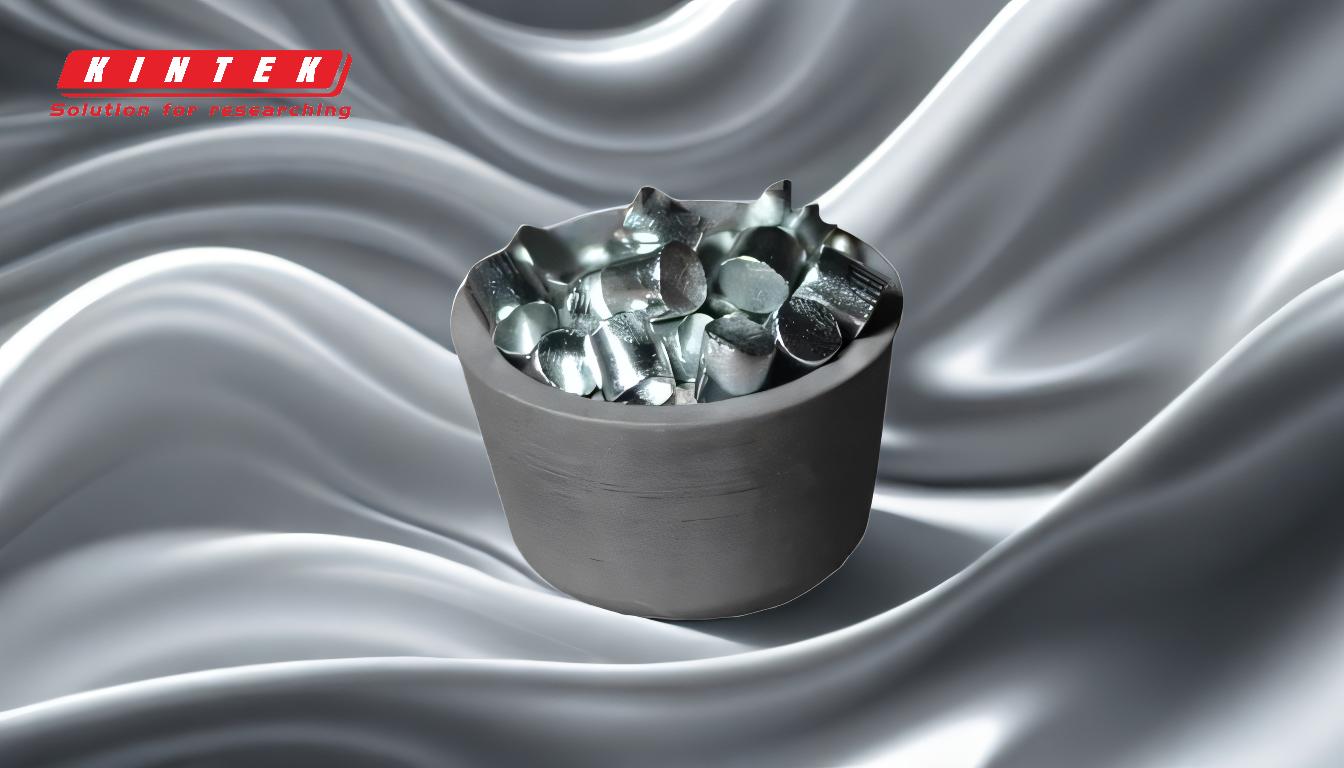
-
Mechanismus der Materialverdampfung:
- Sputtern:Bei diesem Verfahren stoßen energiereiche Ionen mit einem Zielmaterial zusammen und schleudern die Atome einzeln oder in kleinen Clustern heraus.Dieser Prozess ist von Natur aus langsamer, da er auf physikalischem Bombardement und nicht auf thermischer Energie beruht.
- Verdampfung:Nutzt thermische Energie, um das Ausgangsmaterial über seine Verdampfungstemperatur hinaus zu erhitzen, wodurch ein kontinuierlicher und robuster Dampfstrom entsteht.Diese Methode ist effizienter und führt zu höheren Abscheideraten.
-
Betriebsbedingungen:
- Sputtern:Bei höheren Gasdrücken (5-15 mTorr) werden die gesputterten Partikel mehrfach mit Gasmolekülen zusammengestoßen, bevor sie das Substrat erreichen.Durch diese Zusammenstöße werden die Partikel verlangsamt, wodurch sich die Gesamtabscheidungsrate verringert.
- Verdampfung:Wird in der Regel in einer Hochvakuumumgebung durchgeführt, was eine direkte Flugbahn der verdampften Partikel zum Substrat ermöglicht.Dies minimiert Kollisionen und führt zu einer schnelleren Abscheidung.
-
Energie und Effizienz:
- Sputtern:Erfordert komplexe und leistungsstärkere Stromquellen, um die für den Sputterprozess benötigten energiereichen Ionen zu erzeugen.Die Energieübertragung ist im Vergleich zur thermischen Verdampfung weniger effizient.
- Verdampfung:Effiziente Nutzung der Wärmeenergie zur Verdampfung des Ausgangsmaterials, was zu einem schnelleren und kontinuierlichen Abscheidungsprozess führt.
-
Abscheidungsrate:
- Sputtern:Im Allgemeinen ist die Abscheiderate geringer, insbesondere bei nichtmetallischen Werkstoffen.Der Prozess ist langsamer, da die Atome schrittweise ausgestoßen werden und die Partikel sich langsamer durch das Gas bewegen.
- Verdampfung:Bietet eine höhere Abscheidungsrate, da der Dampfstrom intensiver und direkter ist, was eine schnellere Schichtbildung auf dem Substrat ermöglicht.
-
Schichtqualität und Gleichmäßigkeit:
- Sputtern:Erzeugt Filme mit besserer Stufenabdeckung und Gleichmäßigkeit, insbesondere auf unebenen Oberflächen.Dies hat jedoch den Nachteil, dass die Abscheidungsrate geringer ist.
- Verdampfung:Es ist zwar schneller, kann aber aufgrund des stärker gerichteten Dampfstroms zu weniger gleichmäßigen Schichten führen, insbesondere auf komplexen oder unebenen Substraten.
-
Skalierbarkeit und Automatisierung:
- Sputtern:Obwohl das Sputtern langsamer ist, ist es hochgradig skalierbar und kann für die Produktion in großem Maßstab automatisiert werden, so dass es sich für Anwendungen eignet, bei denen Gleichmäßigkeit und Qualität entscheidend sind.
- Verdampfung:Schnellere Abscheidungsraten machen es ideal für Anwendungen, die schnelle Durchlaufzeiten erfordern, aber es ist möglicherweise weniger geeignet für groß angelegte oder automatisierte Prozesse aufgrund möglicher Gleichmäßigkeitsprobleme.
Zusammenfassend lässt sich sagen, dass die langsamere Abscheidungsrate beim Sputtern im Vergleich zur Verdampfung in erster Linie auf den weniger effizienten Mechanismus des Materialauswurfs, höhere Betriebsgasdrücke und die Notwendigkeit komplexer Energiequellen zurückzuführen ist.Obwohl das Sputtern Vorteile bei der Schichtqualität und der Skalierbarkeit bietet, bleibt die Verdampfung die bevorzugte Methode für Anwendungen, die hohe Abscheideraten erfordern.
Zusammenfassende Tabelle:
Blickwinkel | Sputtering-Beschichtung | Verdampfungsabscheidung |
---|---|---|
Mechanismus | Ausschleudern von Atomen durch energiereichen Ionenbeschuss | Thermische Verdampfung des Ausgangsmaterials |
Betriebsdruck | Höhere Gasdrücke (5-15 mTorr), die Teilchenkollisionen verursachen | Hochvakuum, das eine direkte Abscheidung in Sichtweite ermöglicht |
Energie-Effizienz | Weniger effizient aufgrund des komplexen Energiebedarfs | Effizienter, da die thermische Energie für eine schnelle Verdampfung genutzt wird |
Abscheiderate | Langsamer, insbesondere bei nichtmetallischen Werkstoffen | Schneller, mit intensivem und direktem Dampffluss |
Qualität des Films | Bessere Gleichmäßigkeit und Stufenabdeckung, ideal für unebene Oberflächen | Weniger gleichmäßig, insbesondere auf komplexen oder unebenen Substraten |
Skalierbarkeit | Hochgradig skalierbar und geeignet für die Produktion in großem Maßstab | Schneller, aber weniger geeignet für groß angelegte oder automatisierte Prozesse |
Benötigen Sie Hilfe bei der Auswahl der richtigen Abscheidungsmethode für Ihre Anwendung? Kontaktieren Sie noch heute unsere Experten für eine persönliche Beratung!