Einführung in die Dünnschichtabscheidung
Bei der Dünnschichtabscheidung wird eine dünne Materialschicht auf einem Substrat abgeschieden. Es wird häufig bei der Herstellung elektronischer und optischer Geräte wie integrierter Schaltkreise, Solarzellen und Flachbildschirme verwendet. Die beiden am häufigsten verwendeten Techniken zur Dünnschichtabscheidung sind Aufdampfen und Sputtern. Beim Verdampfen wird das Material erhitzt, bis es verdampft und auf dem Substrat kondensiert. Beim Sputtern wird das Material aus einem Target herausgeschleudert, indem es mit hochenergetischen Ionen beschossen wird. Beide Techniken haben ihre Vor- und Nachteile und die Wahl der Technik hängt von der konkreten Anwendung ab.
Inhaltsverzeichnis
- Einführung in die Dünnschichtabscheidung
- Überblick über Verdampfungs- und Sputtertechniken
- Verdampfungsmethoden: Widerstandsthermisch und Elektronenstrahl
- Sputterprozess: Gasionisierung und Zielbeschuss
- Vergleich von Verdampfung und Sputtern
- Vor- und Nachteile jeder Technik
- Anwendungen und Verwendungen von Verdampfung und Sputtern
- Fazit: Welche Technik eignet sich am besten für die Dünnschichtabscheidung?
Überblick über Verdampfungs- und Sputtertechniken
Die Dünnschichtabscheidung ist eine Vakuumtechnik, mit der Beschichtungen aus reinen Materialien auf die Oberfläche verschiedener Objekte wie Halbleiterwafer, optische Komponenten, Solarzellen und viele andere Möglichkeiten aufgetragen werden. Es stehen verschiedene Formen der Dünnschichtabscheidung zur Verfügung, darunter physikalische Gasphasenabscheidung (PVD) und Sputtern.
Verdampfungstechnik
Verdampfung ist eine PVD-Technik, bei der ein festes Material in einer Vakuumkammer erhitzt wird, bis es verdampft und auf einem Substrat kondensiert. Die Technik fällt unter den PVD-Bereich und besteht aus thermischer Verdampfung, Elektronenstrahlverdampfung und induktiver Erwärmung. Durch thermische Verdampfung werden Metalle für Dünnschichttransistoren, Solarzellen und OLEDs abgeschieden. Die Elektronenstrahlverdampfung wird bei der Herstellung optischer Dünnschichten wie Gläsern und Solarpaneelen eingesetzt. Aufgrund mangelnder Effizienz wird induktive Erwärmung in der Nano-/Mikrofertigungsindustrie selten eingesetzt.
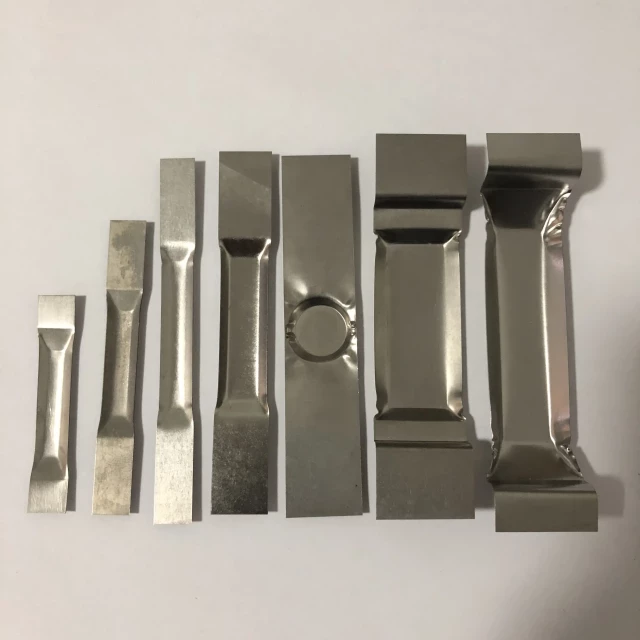
Die Verdampfung ist eine einfachere und kostengünstigere Technik und ermöglicht die Herstellung von Filmen mit hoher Reinheit und Gleichmäßigkeit. Es wird häufig bei der Herstellung von OLEDs, Solarzellen und integrierten Schaltkreisen verwendet. Allerdings leidet es unter einer schlechten Gleichmäßigkeit, dem höchsten Verunreinigungsgrad aller PVD-Methoden und einer mäßigen Filmspannung.
Sputtertechnik
Sputtern ist eine PVD-Technik, bei der ein Material mit Ionen oder hochenergetischen Partikeln bombardiert wird, um Atome oder Moleküle auszustoßen, die dann auf einem Substrat kondensieren. Die Technik wird häufig zur Abscheidung von Metallen und Dielektrika eingesetzt. Es gibt zwei Arten des Sputterns: Magnetronsputtern und Ionenstrahlsputtern.
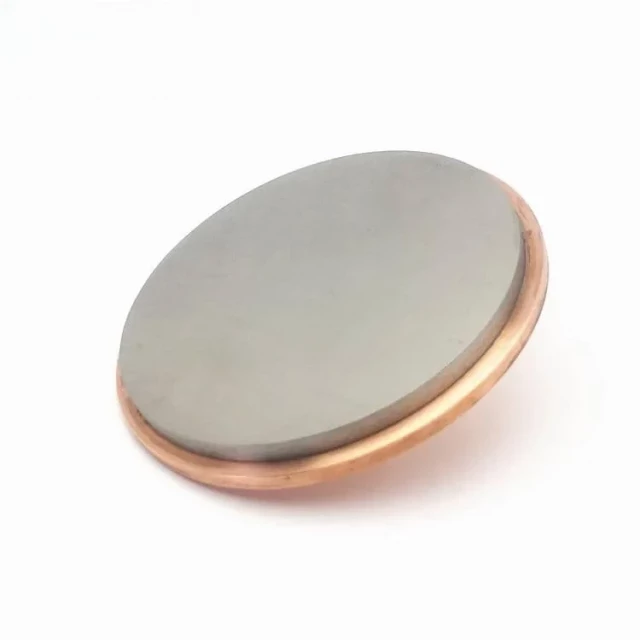
Beim Magnetronsputtern wird ein kontrolliertes Gas, typischerweise chemisch inertes Argon, in eine Vakuumkammer eingeführt und anschließend eine Kathode elektrisch mit Strom versorgt, um ein sich selbst erhaltendes Plasma zu erzeugen. Die freiliegende Oberfläche der Kathode, das sogenannte Target, ist ein Stück des Materials, das auf die Substrate aufgetragen wird. Die Gasatome werden durch den Verlust von Elektronen im Plasma zu positiv geladenen Ionen und werden dann mit ausreichender kinetischer Energie beschleunigt, um das Ziel zu treffen und Atome oder Moleküle aus dem Zielmaterial zu lösen. Dieses gesputterte Material besteht nun aus einem Dampfstrom, der durch die Kammer strömt und als Film oder Beschichtung auf das Substrat trifft und daran haftet.
Das Ionenstrahlsputtern ähnelt dem Magnetronsputtern, verwendet jedoch einen Ionenstrahl anstelle eines Plasmas. Es entstehen Filme mit höherer Dichte und besserer Haftung auf dem Untergrund. Es kann auch zum Abscheiden einer breiteren Palette von Materialien verwendet werden, darunter Metalle, Keramik und Polymere.
Sputtern wird häufig bei der Herstellung von Festplattenlaufwerken, optischen Beschichtungen und Dünnschichtsolarzellen eingesetzt. Es können Filme mit bemerkenswerter Präzision und qualitativ hochwertige Filme mit weniger Streuung als bei der herkömmlichen Verdampfung erzeugt werden. Allerdings erfordert das Sputtern einen komplexeren Aufbau und ist teurer als das Verdampfen.
Insgesamt haben sowohl das Verdampfen als auch das Sputtern ihre eigenen Stärken und Schwächen. Die Wahl der Technik hängt von der konkreten Anwendung und den gewünschten Eigenschaften des Dünnfilms ab.
Verdampfungsmethoden: Widerstandsthermisch und Elektronenstrahl
Die Dünnschichtabscheidung ist ein wichtiger Prozess bei der Herstellung verschiedener High-Tech-Geräte, darunter elektronische Geräte, Solarmodule und optische Komponenten. Zwei beliebte Techniken zur Dünnschichtabscheidung sind Aufdampfen und Sputtern. In diesem Abschnitt besprechen wir zwei Arten von Verdampfungsmethoden, die üblicherweise bei der Dünnschichtabscheidung verwendet werden: Widerstandsthermische Verdampfung und Elektronenstrahlverdampfung.
Widerstandsthermische Verdampfung
Widerstandsthermische Verdampfung ist ein Prozess, bei dem ein Widerstandsheizelement zum Verdampfen des Materials verwendet wird. Bei dieser Methode wird das Ausgangsmaterial in einen Tiegel aus passivem Material wie Bornitrid (BN) und eine externe Heizung gegeben. Mit der Heizung wird dann das Widerstandsmaterial auf seinen Schmelzpunkt erhitzt, wodurch es verdampft und auf einem Substrat kondensiert, um einen dünnen Film zu bilden. Dieser Prozess wird typischerweise in einer Vakuumumgebung mit einem Druck von weniger als 10^-5 Torr durchgeführt.
Widerstandsthermische Verdampfung ist eine relativ einfache und kostengünstige Methode zur Dünnschichtabscheidung. Es handelt sich außerdem um eine sanfte Technik, die verdampfte Teilchenenergien von etwa 0,12 eV oder 1500 K erzeugt. Allerdings weist diese Methode einige Einschränkungen auf, wie z. B. eine schlechte Kontrolle über den Abscheidungsprozess.
Elektronenstrahlverdampfung
Die Elektronenstrahlverdampfung ist eine weitere Technik, die bei der Dünnschichtabscheidung eingesetzt wird. Bei dieser Methode wird das Material in einem wassergekühlten Kupferherd oder -tiegel mit einem hochenergetischen Elektronenstrahl erhitzt. Dieser Prozess erzeugt eine sehr hohe Temperatur, die es ermöglicht, Metalle und Dielektrika mit hohen Schmelztemperaturen, wie etwa Gold und Siliziumdioxid, zu verdampfen und auf einem Substrat abzuscheiden, um einen dünnen Film zu bilden.
Im Vergleich zur thermischen Widerstandsverdampfung weist die Elektronenstrahlverdampfung eine bessere Abscheidungsrate auf und kann hochwertige Dünnfilme mit einem hohen Maß an Kontrolle erzeugen. Allerdings ist diese Methode komplexer und erfordert ein Kühlsystem, was die Produktionsraten verringern und die Energiekosten erhöhen kann.
Vergleich der thermischen Widerstands- und Elektronenstrahlverdampfung
Sowohl die Widerstandsthermo- als auch die Elektronenstrahlverdampfung haben ihre jeweiligen Vor- und Nachteile. Die widerstandsbehaftete thermische Verdampfung ist eine einfache und kostengünstige Methode zur Dünnschichtabscheidung, lässt sich jedoch schlecht über den Abscheidungsprozess steuern. Die Elektronenstrahlverdampfung hingegen bietet eine bessere Kontrolle über den Abscheidungsprozess und kann hochwertige Dünnfilme erzeugen, es handelt sich jedoch um eine komplexere Methode, die ein Kühlsystem erfordert.
Letztendlich hängt die Wahl zwischen diesen beiden Techniken von den spezifischen Anforderungen der Dünnschichtanwendung und den verfügbaren Ressourcen ab. Eine vergleichende Untersuchung der Verdampfungs- und Sputtertechniken kann Forschern und Herstellern dabei helfen, die Vorteile und Grenzen der einzelnen Methoden besser zu verstehen und fundierte Entscheidungen im Dünnschichtabscheidungsprozess zu treffen.
Sputterprozess: Gasionisierung und Zielbeschuss
Sputtern ist ein physikalischer Prozess, bei dem Atome aus einem festen Targetmaterial in die Gasphase geschleudert werden. Bei der Herstellung elektronischer Geräte wird es häufig verwendet, um einen dünnen Film auf ein Substrat aufzutragen. Dieser Prozess wird in einer Vakuumkammer durchgeführt, in der das Zielmaterial mit energiereichen Ionen bombardiert wird, wodurch Atome aus der Zieloberfläche herausgeschleudert werden.
Gasionisation
Beim Sputterprozess wird Gasionisation eingesetzt, um ein Plasma zu erzeugen. Das dabei verwendete Gas ist typischerweise Argon, das durch Anlegen einer Hochspannung ionisiert wird. Dadurch entsteht ein Plasma aus positiv geladenen Ionen und Elektronen, die dann in Richtung des Zielmaterials beschleunigt werden.
Zielbeschuss
Sobald das Plasma erzeugt ist, werden die positiv geladenen Ionen in Richtung des Zielmaterials beschleunigt. Wenn die Ionen mit der Zieloberfläche kollidieren, übertragen sie ihre Energie auf die Atome im Zielmaterial, wodurch diese aus der Oberfläche herausgeschleudert werden. Diese ausgestoßenen Atome wandern dann durch die Vakuumkammer und lagern sich auf dem Substrat ab, wodurch ein dünner Film entsteht.
Sputterausbeute
Die Effizienz des Sputterprozesses wird anhand der Sputterausbeute gemessen, bei der es sich um die Anzahl der Atome handelt, die pro einfallendem Ion von der Oberfläche ausgeschleudert werden. Die Sputterausbeute hängt von mehreren Faktoren ab, darunter der Energie der einfallenden Ionen, der Masse der Ionen und Zielatome sowie der Bindungsenergie der Atome im Festkörper.
Kontrolle über die Dicke und Zusammensetzung dünner Filme
Einer der Vorteile des Sputterverfahrens ist die Möglichkeit, die Dicke und Zusammensetzung des Dünnfilms besser steuern zu können. Der Prozess ermöglicht die Abscheidung mehrerer Schichten und ermöglicht so die Schaffung komplexer Dünnschichtstrukturen. Dieses Maß an Kontrolle ist mit anderen Abscheidungstechniken, wie etwa der Verdampfung, nicht möglich.
Große Auswahl an Materialien
Durch Sputtern kann im Vergleich zur Verdampfung auch ein breiteres Spektrum an Materialien abgeschieden werden. Dazu gehören Metalle, Keramik und Halbleiter. Dies macht das Sputtern zu einer vielseitigeren Technik für die Dünnschichtabscheidung in der Elektronikindustrie.
Zusammenfassend lässt sich sagen, dass der Sputterprozess die Verwendung von Gasionisation und Targetbeschuss umfasst, um einen dünnen Film auf einem Substrat abzuscheiden. Dieses Verfahren ermöglicht eine bessere Kontrolle über die Dicke und Zusammensetzung des Films sowie die Möglichkeit, ein breiteres Spektrum an Materialien aufzubringen. Diese Vorteile machen Sputtern zu einer effizienteren und präziseren Methode im Vergleich zur Verdampfung zur Dünnschichtabscheidung in der Elektronikindustrie.
Vergleich von Verdampfung und Sputtern
Techniken zur Dünnschichtabscheidung sind für verschiedene wissenschaftliche und industrielle Anwendungen von entscheidender Bedeutung. Zwei häufig verwendete Techniken zur Dünnschichtabscheidung sind Aufdampfen und Sputtern. In diesem Abschnitt vergleichen wir diese beiden Techniken anhand verschiedener Faktoren wie Materialeigenschaften, Filmdicke und Anwendungsanforderungen.
Materialeigenschaften
Die Verdunstung wird durch die Art der verdampfbaren Materialien begrenzt. Andererseits ermöglicht das Sputtern die Abscheidung einer größeren Bandbreite an Materialien, was es zu einer vielseitigeren Technik macht.
Schichtdicke
Die Verdampfung ist eine relativ einfache und kostengünstige Methode, bei der ein Ausgangsmaterial erhitzt wird, bis es verdampft und auf einem Substrat kondensiert, um einen dünnen Film zu bilden. Sie ist jedoch durch die Dicke und Gleichmäßigkeit der resultierenden Filme begrenzt. Sputtern hingegen ermöglicht eine bessere Kontrolle über die Filmdicke und -zusammensetzung. Die Dicke kann durch einfaches Anpassen der Abscheidungszeit gesteuert werden.
Filmqualität
Beim Sputtern entstehen im Allgemeinen Filme mit höherer Dichte und glatteren Oberflächen als beim Aufdampfen. Dies liegt daran, dass das Sputtern eine energiereichere und gerichtetere Abscheidung von Atomen ermöglicht, was zu weniger Defekten und Verunreinigungen in den Filmen führt. Bei bestimmten Anwendungen, bei denen eine porösere oder rauere Oberfläche gewünscht wird, kann die Verdampfung jedoch von Vorteil sein.
Kosten und Komplexität
Im Vergleich zum Sputtern ist die Verdampfung eine relativ einfache und kostengünstige Methode. Beim Sputtern kann jedoch ein breiteres Spektrum an Materialien abgeschieden werden, wobei die Filmdicke und -zusammensetzung besser kontrolliert werden kann. Die Einrichtung und Wartung kann jedoch komplexer und teurer sein als beim Verdampfen.
Anwendungen
Die Wahl zwischen Verdampfen und Sputtern hängt von verschiedenen Faktoren wie den Materialeigenschaften, der Schichtdicke und den Anwendungsanforderungen ab. Wenn beispielsweise eine porösere oder rauere Oberfläche gewünscht wird, kann die Verdunstung von Vorteil sein. Wenn andererseits hochwertige Filme mit besserer Kontrolle über Dicke und Zusammensetzung benötigt werden, ist Sputtern die bessere Wahl.
Zusammenfassend lässt sich sagen, dass sowohl das Verdampfen als auch das Sputtern ihre eigenen Vor- und Nachteile haben. Eine vergleichende Untersuchung der beiden Techniken kann Forschern dabei helfen, die für ihre spezifischen Anwendungen am besten geeignete Methode auszuwählen.
Vor- und Nachteile jeder Technik
Verdunstung
- Einfache und kostengünstige Technik.
- Kann zum Auftragen verschiedenster Materialien verwendet werden.
- Bietet hohe Abscheidungsraten.
- Gute Haftung auf dem Untergrund.
- Kann zur Abscheidung dicker Schichten verwendet werden.
- Begrenzt durch niedrige Ablagerungsraten.
- Schlechte Haftung auf dem Untergrund.
- Schwieriger ist es, die Filmkomposition zu kontrollieren.
- Keine Möglichkeit zur Vor-Ort-Reinigung von Substratoberflächen.
- Die Stufenabdeckung ist schwieriger zu verbessern.
Sputtern
- Bietet höhere Ablagerungsraten.
- Bessere Haftung auf dem Untergrund.
- Größere Kontrolle über Filmdicke und -zusammensetzung.
- Arbeitet im kleineren Vakuumbereich.
- Kann zum Auftragen verschiedenster Materialien verwendet werden.
- Komplexerer und teurerer Prozess.
- Erfordert den Einsatz spezieller Ausrüstung.
- Es sind hohe Kapitalaufwendungen erforderlich.
- Die Ablagerungsraten einiger Materialien sind relativ gering.
- Beim Sputtern besteht eine größere Tendenz, Verunreinigungen in das Substrat einzubringen.
- Einige Materialien wie organische Feststoffe werden durch Ionenbeschuss leicht abgebaut.
- Es kann zu Röntgenschäden durch Elektronenstrahlverdampfung kommen.
Auswahl der geeigneten Technik
Die Wahl der Technik hängt von den spezifischen Anforderungen der Anwendung ab, wie z. B. der gewünschten Filmdicke, Zusammensetzung und Eigenschaften. Beide Techniken haben ihre Vor- und Nachteile, und das Verständnis der Unterschiede zwischen diesen Techniken ist entscheidend für die Auswahl der am besten geeigneten Methode für jede Anwendung. Beispielsweise kann Verdampfung zur Abscheidung dicker Filme und einer besseren Stufenabdeckung genutzt werden, während Sputtern für eine bessere Haftung auf dem Substrat und eine bessere Kontrolle über Filmdicke und -zusammensetzung eingesetzt werden kann. Darüber hinaus wird Sputtern bevorzugt, wenn eine Kontamination ein Problem darstellt und höhere Abscheidungsraten erforderlich sind.
Anwendungen und Verwendungen von Verdampfung und Sputtern
Die Dünnschichtabscheidung mithilfe von Verdampfungs- und Sputtertechniken wird in verschiedenen industriellen Anwendungen häufig eingesetzt. Beide Methoden haben einzigartige Vor- und Nachteile, die sie für bestimmte Anwendungen geeignet machen.
Anwendungen der Verdunstung
Verdampfung wird häufig bei der Herstellung organischer elektronischer Geräte wie OLEDs und Solarzellen eingesetzt. Es wird auch in der Elektronikindustrie zur Herstellung dünner Filmbeschichtungen für leitende, isolierende und schützende Schichten auf Halbleiterbauelementen verwendet. Die Optikindustrie nutzt die Aufdampfung auch zur Herstellung dünner Filmbeschichtungen für Linsen und andere optische Komponenten, um deren Leistung zu verbessern. Darüber hinaus wird die Verdunstungsabscheidung in der Luft- und Raumfahrtindustrie zur Herstellung dünner Filmbeschichtungen für Triebwerksteile eingesetzt, um deren Verschleißfestigkeit und Haltbarkeit zu verbessern.
Anwendungen des Sputterns
Sputtern wird häufig bei der Herstellung von Hartbeschichtungen für Schneidwerkzeuge und verschleißfesten Beschichtungen für Maschinenteile eingesetzt. Es wird auch bevorzugt für die Abscheidung von Materialien mit hohem Schmelzpunkt verwendet und eignet sich daher für Anwendungen, die eine höhere morphologische Qualität der Oberflächen erfordern, bei denen Rauheit, Korngröße, Stöchiometrie und andere Anforderungen wichtiger sind als die Abscheidungsrate. Sputtern wird auch bei der Herstellung dünner Filmbeschichtungen für magnetische Speichergeräte, optische Beschichtungen und Halbleiterbauelemente eingesetzt.
Vorteile des Verdampfens und Sputterns
Sowohl die Verdampfungs- als auch die Sputtertechnik haben ihre einzigartigen Vorteile, die sie für verschiedene Anwendungen geeignet machen. Durch die Verdampfung lässt sich beispielsweise die Dicke und Zusammensetzung des abgeschiedenen Films präzise steuern. Es eignet sich auch zum Auftragen von Materialien mit niedrigem Schmelzpunkt. Andererseits ermöglicht das Sputtern die Abscheidung von Materialien mit hohem Schmelzpunkt und wird für Anwendungen bevorzugt, die eine höhere morphologische Qualität der Oberflächen erfordern. Es handelt sich außerdem um eine vielseitigere Methode zur Dünnschichtabscheidung, da sie zur Abscheidung einer breiten Palette von Materialien verwendet werden kann und an viele verschiedene Anwendungen angepasst werden kann.
Zusammenfassend lässt sich sagen, dass sowohl Verdampfungs- als auch Sputtertechniken in verschiedenen industriellen Anwendungen weit verbreitet sind. Das Verständnis der Unterschiede zwischen diesen Techniken ist für die Entwicklung neuer und fortschrittlicher elektronischer Geräte von entscheidender Bedeutung. Die Wahl zwischen Verdampfen und Sputtern hängt von der konkreten Anwendung und dem abzuscheidenden Material ab. Eine ordnungsgemäße Steuerung des Abscheidungsprozesses ist für die Herstellung hochwertiger Dünnfilme mit den gewünschten Eigenschaften und Leistungen von entscheidender Bedeutung.
Fazit: Welche Technik eignet sich am besten für die Dünnschichtabscheidung?
Zusammenfassend lässt sich sagen, dass sowohl die Verdampfungs- als auch die Sputtertechnik bei der Dünnschichtabscheidung ihre Vor- und Nachteile haben. Die Verdampfung ist eine einfachere und kostengünstigere Methode, sie ist jedoch nur begrenzt in der Lage, bestimmte Materialien abzuscheiden, und kann zu einer geringeren Filmqualität führen. Sputtern hingegen ist eine vielseitigere und präzisere Technik, aber auch komplexer und teurer. Die Wahl zwischen den beiden Methoden hängt letztlich von den spezifischen Anforderungen der Anwendung ab. Wenn eine höhere Filmqualität erforderlich ist, ist Sputtern im Allgemeinen die bevorzugte Methode. Wenn jedoch Kosten und Einfachheit im Vordergrund stehen, ist die Verdampfung die bessere Option.
Kontaktieren Sie uns für eine kostenlose Beratung
Die Produkte und Dienstleistungen von KINTEK LAB SOLUTION werden von Kunden auf der ganzen Welt anerkannt. Unsere Mitarbeiter helfen Ihnen gerne bei allen Fragen weiter. Kontaktieren Sie uns für eine kostenlose Beratung und sprechen Sie mit einem Produktspezialisten, um die am besten geeignete Lösung für Ihre Anwendungsanforderungen zu finden!