Einführung in den Vakuum-Drucksinterofen
Der Vakuum-Drucksinterofen ist eine revolutionäre Technologie, die die Fertigungsindustrie verändert hat und zahlreiche Vorteile und Anwendungen bietet. Dieser Artikel befasst sich mit dem Grundprinzip und den Komponenten des Ofens und beleuchtet, wie das Vakuumsintern die Umstrukturierung von Materialien auf mikroskopischer Ebene fördert, was zu dichten Strukturen und überlegener Leistung führt und gleichzeitig Oxidations- und Verschmutzungseffekte verhindert. Wenn wir die Vorteile, das Funktionsprinzip und die Anwendungen des Vakuumdrucksinterns erforschen, wird deutlich, dass diese Technologie für verschiedene Industriezweige einen Wendepunkt darstellt, da sie saubere, glänzende Teile, unglaubliche Designflexibilität und maximale Produktivität bietet. Begeben wir uns auf eine Reise, um das unglaubliche Potenzial des Vakuum-Drucksinterofens zu entdecken.
Vorteile des Vakuum-Drucksinterofens
Entdecken Sie die Vorteile des Vakuumsinterns: saubere, glänzende Teile, unglaubliche Designflexibilität, schnelle Durchlaufzeiten, hervorragende Qualität, weniger Fehler, einfache Wartung und maximale Produktivität. Erfahren Sie, wie Sie auf effiziente Weise empfindliche und komplizierte Teile mit minimalem Abfall fügen können.
Was ist ein Vakuum-Sinterofen?
Unter Sintern versteht man das Erzeugen einer festen Materialmasse mit Hilfe von Hitze und Druck - ohne dass das Material verflüssigt wird. Vakuumsintern ist eine Wärmebehandlung, die dazu dient, Teile mit möglichst wenig Abfall zu verbinden, um konsistente Komponenten ohne Nähte, Füllstoffe oder Verbindungen herzustellen. Die in einem Vakuumsinterofen behandelten Bauteile sind oft kompliziert, empfindlich und schwierig herzustellen.
Zu den Vorteilen des Vakuumsinterns gehören:
-
Temperatur- und Druckgrenzen können während der Konstruktionsphase gewählt und während der Verarbeitung manuell oder automatisch gesteuert werden.
-
Vakuumöfen können so gebaut werden, dass sie sowohl das Entbindern als auch das Sintern durchführen können, was Zeit und Geld spart, da kein Teiletransfer, keine sekundären Maschinen und keine Ressourcen für einen sich wiederholenden Prozess erforderlich sind.
-
Vakuumöfen eignen sich perfekt für Sinteranwendungen bei höheren Temperaturen und bieten hochgradig anpassbare Steuerungen für manuelle oder automatische Temperaturänderungen je nach Projektanforderungen, wodurch eine einheitliche Temperatur und eine gleichbleibende Teilequalität gewährleistet werden.
Vorteile des Vakuum-Sinterofens
Beim Vakuumsintern wird die Verunreinigung durch schädliche Stoffe (wie Wasser, Sauerstoff, Stickstoff und andere Verunreinigungen) in der Atmosphäre reduziert, wodurch nachteilige Reaktionen wie Entkohlung, Aufkohlung, Reduktion, Oxidation und Nitrierung vermieden werden. Die Vakuumumgebung übertrifft andere Sintermethoden, wobei die Restgasreinheit 99,99987% Argon entspricht, wenn der Vakuumdruck 1,3*10^-1 Pascal erreicht.
Vakuum-Sinterofen
Kleine oder komplexe Teile lassen sich nur schwer durch Gießen oder maschinelle Bearbeitung herstellen. Komponenten, die gesintert werden müssen, sind oft empfindlich, kompliziert und fehleranfällig. Vakuumsintern fügt Teile effizient und mit minimalem Abfall zusammen und produziert gleichmäßige, blanke Teile ohne Nähte, Fugen oder Füllstoffe. Technologien wie Metallpulver, Metallspritzguss und 3D-Druck profitieren in hohem Maße von der überlegenen Qualität und Flexibilität des Vakuumsinterns.
Vorteile eines Vakuum-Sinterofens
- Saubere, glänzende Teile
- Unglaubliche Designflexibilität
- Schnelle Durchlaufzeit
- Hervorragende Qualität
- Weniger Defekte
- Einfache Wartung
- Höchste Produktivität
Arbeitsprinzip des Vakuumdrucksinterns
Der Prozess des Vakuumdrucksinterns spielt eine entscheidende Rolle bei der Bindung von Materialien durch Atomwanderung. Diese innovative Technologie nutzt das Induktionssintern zum Erhitzen von Materialien, wodurch das Vorhandensein von schädlichen Substanzen wie Wasserdampf, Sauerstoff, Stickstoff und anderen Verunreinigungen in der Atmosphäre wirksam reduziert wird. Durch die Minimierung dieser Verunreinigungen wird eine Reihe von Reaktionen wie Entkohlung, Nitrierung, Aufkohlung, Reduktion und Oxidation vermieden, was zu einer engeren Verbindung zwischen den Werkstoffen führt und die Verschleißfestigkeit und Festigkeit erhöht. Die Reduzierung von Gas in den Poren und die Entfernung von Oxidschichten auf den Materialoberflächen tragen zur Verbesserung der Qualität und Leistung der gesinterten Produkte bei. Darüber hinaus ist das Vakuuminduktionssintern für seine Fähigkeit bekannt, die Produktkosten zu senken, was es zu einem wirtschaftlich vorteilhaften Verfahren macht.
In einer Vakuumumgebung verringert der relativ niedrige Gasgehalt die Auswirkungen von Konvektion und Wärmeleitung, wobei die Wärme vom Heizmodul hauptsächlich durch Strahlung auf die Materialoberfläche übertragen wird. Die Auswahl eines geeigneten Heizmoduls auf der Grundlage der spezifischen Sintertemperatur und der physikalischen und chemischen Eigenschaften des Materials ist entscheidend. Im Vergleich zur Vakuum-Widerstandserwärmung hilft das Induktionssintern mit Mittelfrequenz-Stromversorgungserwärmung dabei, die Probleme mit der Hochtemperaturisolierung zu mildern, die bei Vakuumöfen mit interner Widerstandserwärmung auftreten.
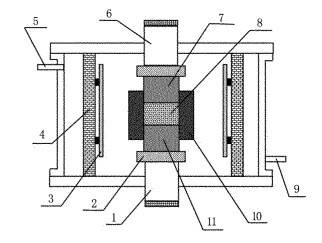
Temperatur- und Druckgrenzen spielen in der Entwicklungsphase eine entscheidende Rolle und können während der Verarbeitungsphase manuell oder automatisch gesteuert werden. Vakuumöfen sind so konstruiert, dass sie sowohl das Entbindern als auch das Sintern durchführen können, was durch die Kombination dieser Prozesse in einem einzigen Ofen Zeit und Ressourcen spart. Durch diese Integration entfällt der Bedarf an Teiletransport, Sekundärmaschinen oder die Verschwendung von Ressourcen für sich wiederholende Prozesse.
Der Einsatz von Vakuumöfen ist besonders vorteilhaft für Sinteranwendungen bei höheren Temperaturen. Diese Öfen bieten hochgradig anpassbare Steuerungen, die manuelle oder automatische Temperatureinstellungen je nach den spezifischen Projektanforderungen ermöglichen. Die gleichmäßige Temperaturverteilung im Vakuumofen gewährleistet eine gleichbleibende Qualität der Teile und trägt so zur allgemeinen Zuverlässigkeit und Leistung der Sinterprodukte bei.
Der Entbinderungsprozess im Vakuumofen spielt eine entscheidende Rolle bei der Entfernung von Bindemitteln, die den Ofen und das Endprodukt verunreinigen können. Während Bindemittel für die Verdichtung einzelner Teile unerlässlich sind, werden sie während des Sinterprozesses unnötig und schädlich. Durch die Beseitigung dieser Bindemittel wird der Sinterprozess optimiert, was zur Herstellung von sauberen, hochwertigen Teilen führt.
Das Vakuumsintern erfordert eine Hochvakuumumgebung, um die Herstellung sauberer und hochwertiger Teile zu gewährleisten. Die Temperatur muss sorgfältig kontrolliert werden, um eine reibungslose Verbindung der Metalle zu ermöglichen, ohne dass ein Verflüssigungspunkt erreicht wird. Die Abkühlgeschwindigkeit nach dem Sintern hängt von den spezifischen Materialeigenschaften und -anforderungen ab.
Der Vakuumsinterofen, ein Hochtemperatur-, Hochdruck- und Niederdruck-Sintergerät, wird vor allem für die Herstellung von Hochleistungskeramik, Metallen und Verbundwerkstoffen eingesetzt. Dieser Ofen besteht in der Regel aus einem Ofenkörper, einer Heizvorrichtung, einem Vakuumsystem und einem Kontrollsystem. Das Grundprinzip besteht darin, Pulver oder Stückgut bei hoher Temperatur, im Vakuum oder unter Inertgas zu sintern, wodurch die Umstrukturierung des Materials auf mikroskopischer Ebene und die Rekristallisation gefördert werden. Dieser Prozess führt zur Bildung einer dichten Struktur mit ausgezeichneten Leistungsmerkmalen, während unerwünschte Effekte wie Oxidation und Verschmutzung des Materials verringert werden.
Durch das Verständnis des Funktionsprinzips des Vakuumdrucksinterns und der Feinheiten von Vakuumöfen können Hersteller und Forscher diese fortschrittlichen Technologien nutzen, um den Sinterprozess zu optimieren, die Produktqualität zu verbessern und Kosteneinsparungen bei der Materialvorbereitung und Produktion zu erzielen.
Anwendungen und Funktionen von Vakuum-Heißpressöfen
Vakuum-Heißpressöfen spielen in verschiedenen wissenschaftlichen und industriellen Anwendungen eine entscheidende Rolle, da sie eine präzise Kontrolle über Temperatur, Druck und Atmosphäre ermöglichen. Diese Öfen sind unverzichtbar für Heißpress-Sinterexperimente im Vakuum oder unter Schutzatmosphäre und erleichtern die Entwicklung und Herstellung fortschrittlicher Materialien. Im Folgenden werden die Anwendungen und Funktionen von Vakuum-Heißpressöfen im Detail erläutert:
Anwendungen
1. Pulvermetallurgie und Funktionskeramik: Vakuum-Warmpressöfen werden in großem Umfang für die Hochtemperatur-Warmumformung von neuen Werkstoffen wie Pulvermetallurgie und Funktionskeramik eingesetzt. Diese Öfen ermöglichen das Vakuumsintern von transparenten Keramiken, Industriekeramiken und Metallen, einschließlich Legierungen aus hochschmelzenden Metallen.
2. Sintern von keramischen Werkstoffen: Materialien wie Siliziumkarbid und Siliziumnitrid werden in Vakuum-Heißpressöfen bei hohen Temperaturen gesintert. Dieses Verfahren verbessert ihre mechanischen Eigenschaften und ermöglicht die Herstellung fortschrittlicher keramischer Komponenten mit präziser Maßkontrolle.
3. Wärmebehandlung von Pulvern und Presslingen: Vakuum-Warmpressöfen ermöglichen die Wärmebehandlung von Pulvern und Presslingen unterhalb ihres Schmelzpunktes. Dieser metallurgische Prozess verbessert die Festigkeit der Werkstoffe durch Partikelbindung und erhöht damit ihre Eignung für verschiedene Anwendungen.
4. Forschung und Entwicklung: Diese Öfen sind unverzichtbare Werkzeuge für Forschung und Entwicklung, da sie eine kontrollierte Umgebung für die Untersuchung des Materialverhaltens bei hohen Temperaturen und Drücken bieten. Sie ermöglichen Wissenschaftlern und Ingenieuren die Erforschung neuartiger Werkstoffe und Fertigungstechniken mit unvergleichlicher Präzision.
Funktionen
1. Höchste Arbeitstemperatur: Vakuum-Warmpressöfen weisen eine bemerkenswerte maximale Arbeitstemperatur von bis zu 2200 Grad Celsius auf. Diese hohe Temperatur ermöglicht die Verarbeitung eines breiten Spektrums von Materialien, einschließlich solcher, die extreme Hitzebedingungen zum Sintern und Verdichten erfordern.
2. Präzisions-Steuerungssystem: Ausgestattet mit einem hochpräzisen Regelsystem ermöglichen diese Öfen eine genaue Regelung von Temperatur, Druck und Verdrängungsrate während des Heißpress-Sinterprozesses. Dieses Maß an Kontrolle gewährleistet die Reproduzierbarkeit und Konsistenz der Materialeigenschaften, die für die Forschung und die industrielle Produktion unerlässlich sind.
3. Einstellbarer Arbeitsdruck: Die Öfen sind mit auf- und abwärtsgerichteten Suppressionsölen ausgestattet, die eine Anpassung des Arbeitsdrucks an die jeweiligen technischen Anforderungen ermöglichen. Diese Flexibilität ermöglicht maßgeschneiderte Verarbeitungsbedingungen, die den Anforderungen unterschiedlicher Materialien und Anwendungen gerecht werden und optimale Leistung und Qualität gewährleisten.
4. Temperaturstabilität: Mit einstellbaren Temperatureinstellungen können Vakuum-Heißpressöfen eine konstante Temperatur über längere Zeiträume aufrechterhalten, was eine gleichmäßige Erwärmung und eine präzise Steuerung des Sinterprozesses gewährleistet. Diese Temperaturstabilität ist entscheidend für das Erreichen der gewünschten Materialeigenschaften und die Vermeidung von Mängeln in den Endprodukten.
Zusammenfassend lässt sich sagen, dass Vakuum-Heißpressöfen vielseitige und unentbehrliche Werkzeuge für eine breite Palette von Anwendungen in der Materialwissenschaft, Fertigung und Forschung sind. Mit ihren fortschrittlichen Funktionen und präzisen Kontrollsystemen ermöglichen diese Öfen die Entwicklung und Herstellung innovativer Werkstoffe mit maßgeschneiderten Eigenschaften, die den Fortschritt in verschiedenen Branchen vorantreiben.
Vorteile des Sinterns unter Vakuum und Druck
Das Sintern unter Vakuum bietet zahlreiche Vorteile bei der Herstellung von Teilen und Komponenten. Ein Hauptvorteil ist die Herstellung glänzender Teile nach dem Sintern, was auf das Fehlen von Oxidation und Verunreinigung der Atmosphäre in der Vakuumumgebung zurückzuführen ist. Diese kontrollierte Einstellung ermöglicht eine genaue Überwachung und Anpassung der Prozessparameter, wodurch sichergestellt wird, dass die gewünschten Ergebnisse konstant erzielt werden.
In bestimmten Fällen erfordern Werkstoffe, insbesondere hochreaktive Werkstoffe wie Titan, das Sintern unter bestimmten Druckbedingungen. So sind für das Sintern extrem reaktiver Werkstoffe häufig Druckwerte zwischen 10-2 Millibar und 10-4 Millibar erforderlich, um unerwünschte Reaktionen zu vermeiden und optimale Sinterergebnisse zu erzielen.
Darüber hinaus können Materialien wie nichtrostende Stähle während des Sinterprozesses Atmosphären erfordern, die mit Inertgasen angereichert sind. Die Verwendung von Inertgasen, wie z. B. Mischungen auf Argonbasis, trägt dazu bei, Probleme wie die Ausscheidung von Chromnitrid während der Abkühlung zu vermeiden, insbesondere wenn keine hohen Abkühlungsraten erreicht werden können. Gemische auf Stickstoffbasis eignen sich dagegen für verschiedene andere Materialtypen.
Ein wesentlicher Vorteil des Sinterns unter Vakuum und Druck ist die Möglichkeit, die Sinteratmosphäre auf die spezifischen Materialanforderungen abzustimmen und so den Sinterprozess für die gewünschten Eigenschaften zu optimieren. Durch die Wahl der geeigneten Sinteratmosphäre können die Hersteller ein Gleichgewicht zwischen günstigen Ergebnissen und Betriebskosten erreichen.
Darüber hinaus bietet die kontrollierte Umgebung vonVakuum-Sinteröfen zu einer Verbesserung der Materialeigenschaften und des Aussehens der Teile bei. Durch die Reduzierung schädlicher Verunreinigungen wie Wasser, Sauerstoff und Stickstoff minimiert das Vakuumsintern das Risiko nachteiliger Reaktionen wie Entkohlung, Aufkohlung, Oxidation und Nitrierung. Diese Reinheit der Vakuumumgebung mit Restgasreinheiten, die außergewöhnliche Werte wie 99,99987 % Argon erreichen, unterscheidet das Vakuumsintern von anderen Sinterverfahren.
Zusammenfassend lässt sich sagen, dass die Vorteile des Sinterns unter Vakuum und Druck sehr vielfältig sind. Die Fähigkeit, blanke, saubere Teile mit verbesserten Eigenschaften, vereinfachten Prozessen und reproduzierbaren Ergebnissen herzustellen, unterstreicht den Wert des Einsatzes von Vakuumsintertechniken in verschiedenen Fertigungsanwendungen. Indem sie die Vorteile des Vakuumsinterns nutzen, können Hersteller bessere Ergebnisse erzielen, die Bearbeitungszeit verkürzen und die Gesamtproduktivität bei der Herstellung hochwertiger Komponenten steigern.
Kontaktieren Sie uns für eine kostenlose Beratung
Die Produkte und Dienstleistungen von KINTEK LAB SOLUTION werden von Kunden auf der ganzen Welt anerkannt. Unsere Mitarbeiter helfen Ihnen gerne bei allen Fragen weiter. Kontaktieren Sie uns für eine kostenlose Beratung und sprechen Sie mit einem Produktspezialisten, um die am besten geeignete Lösung für Ihre Anwendungsanforderungen zu finden!