PVD-Beschichtungen (Physical Vapor Deposition) werden durch ein hochgradig kontrolliertes Verfahren aufgebracht, bei dem ein festes Material in einer Vakuumumgebung verdampft und auf ein Substrat aufgebracht wird, um eine dünne, dauerhafte Schicht zu bilden.Das Verfahren wird häufig in Branchen wie der Luft- und Raumfahrt, der Automobilindustrie und der Werkzeugherstellung eingesetzt, um Oberflächeneigenschaften wie Härte, Verschleißfestigkeit und Korrosionsbeständigkeit zu verbessern.Zu den wichtigsten Schritten gehören die Vorbereitung des Substrats, das Erzeugen eines Vakuums, das Verdampfen des Zielmaterials und das Aufbringen des verdampften Materials auf das Substrat.Um die Eigenschaften der Beschichtung zu verändern, können reaktive Gase zugeführt werden, und das Verfahren wird in einer Vakuumkammer durchgeführt, um Sauberkeit und Präzision zu gewährleisten.
Die wichtigsten Punkte werden erklärt:
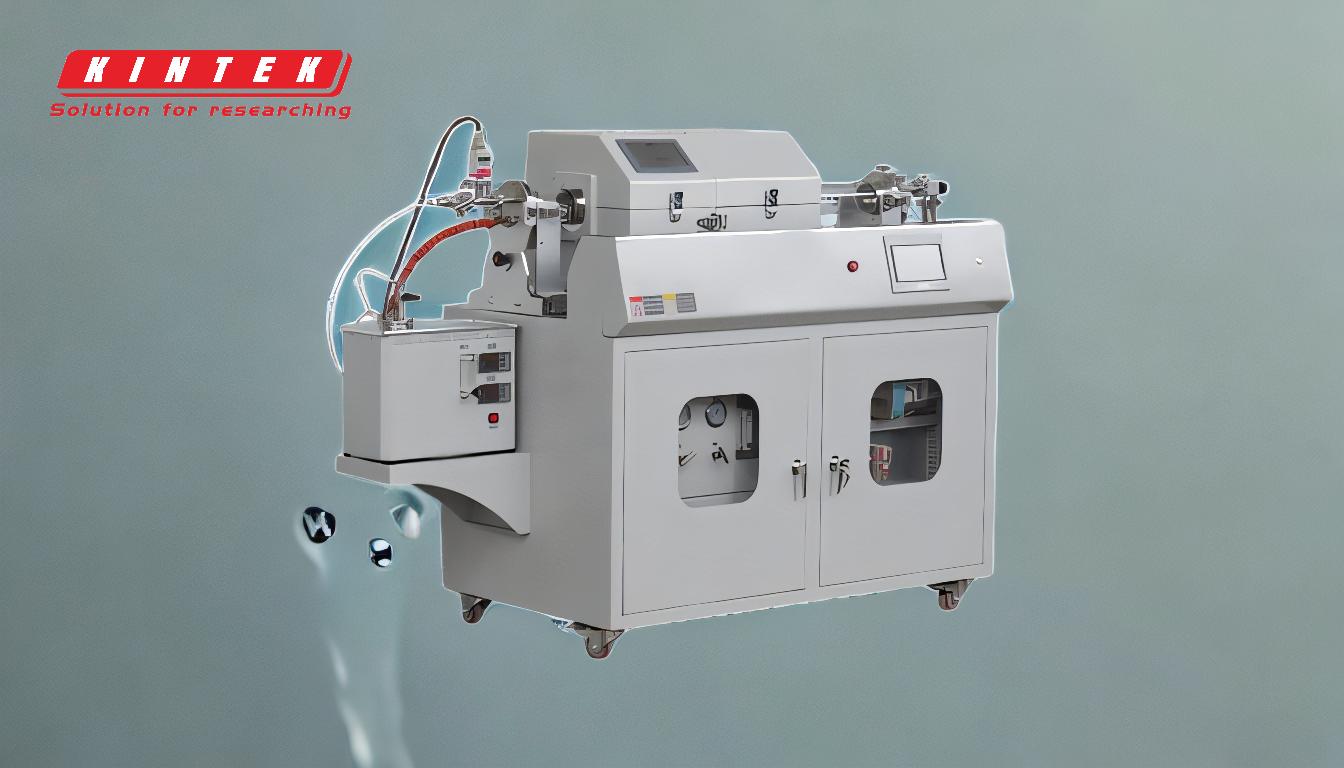
-
Vorbereitung des Substrats:
- Reinigung:Das Substrat wird gründlich gereinigt, um Verunreinigungen wie Öle, Staub oder Oxide zu entfernen.Dieser Schritt ist entscheidend, um eine starke Haftung der Beschichtung zu gewährleisten.
- Vorbehandlung:Das Substrat kann zusätzlich behandelt werden, z. B. durch Ätzen oder Ionenbeschuss, um die Oberflächenrauheit zu verbessern und die Haftung der Beschichtung zu erhöhen.
-
Schaffung einer Vakuumumgebung:
- Das Substrat und das Zielmaterial werden in eine Vakuumkammer gebracht, die dann evakuiert wird, um eine Hochvakuumumgebung zu schaffen (in der Regel 10-³ bis 10-⁹ Torr).Dieser Schritt stellt sicher, dass das verdampfte Material nicht verunreinigt wird und genau kontrolliert werden kann.
-
Verdampfung des Zielmaterials:
-
Techniken zur Verdampfung:Zur Verdampfung des Zielmaterials werden verschiedene Verfahren eingesetzt, darunter:
- Elektronenstrahlverdampfung:Ein hochenergetischer Elektronenstrahl erhitzt das Zielmaterial, bis es verdampft.
- Sputtern:Durch Ionenbeschuss werden Atome aus dem Zielmaterial herausgelöst.
- Kathodische Lichtbogenverdampfung:Ein Hochstromlichtbogen verdampft das Zielmaterial.
- Thermische Verdampfung:Das Zielmaterial wird in einem Schmelztiegel erhitzt, bis es verdampft.
- Reaktive Gase:Reaktive Gase wie Stickstoff oder Sauerstoff können eingeführt werden, um die Zusammensetzung des verdampften Materials zu verändern und Verbindungen wie Metallnitride oder -oxide zu bilden.
-
Techniken zur Verdampfung:Zur Verdampfung des Zielmaterials werden verschiedene Verfahren eingesetzt, darunter:
-
Transport von verdampftem Material:
- Die verdampften Atome oder Moleküle werden durch die Vakuumkammer zum Substrat transportiert.Dieser Schritt wird durch den Vakuumdruck und den Abstand zwischen dem Target und dem Substrat beeinflusst.
-
Abscheidung auf dem Substrat:
-
Das verdampfte Material kondensiert auf dem Substrat und bildet einen dünnen, gleichmäßigen Film.Der Abscheidungsprozess kann verbessert werden durch:
- Ionen-Beschuss:Ionen werden eingesetzt, um die Dichte und Haftung der Beschichtung zu verbessern.
- Plasma Unterstützung:Eine Plasmaumgebung kann die Reaktivität und Gleichmäßigkeit der Beschichtung verbessern.
-
Das verdampfte Material kondensiert auf dem Substrat und bildet einen dünnen, gleichmäßigen Film.Der Abscheidungsprozess kann verbessert werden durch:
-
Post-Deposition-Prozesse:
- Qualitätskontrolle:Die Beschichtung wird geprüft, um sicherzustellen, dass sie den Spezifikationen für Dicke, Haftung und Leistung entspricht.
- Endbearbeitung:Zusätzliche Behandlungen wie Polieren oder Oberflächenmodifikation können angewendet werden, um das Aussehen oder die Funktionalität der Beschichtung zu verbessern.
-
Vorteile von PVD-Beschichtungen:
- Dauerhaftigkeit:PVD-Beschichtungen sind äußerst verschleiß-, korrosions- und oxidationsbeständig.
- Präzision:Das Verfahren ermöglicht eine genaue Kontrolle der Schichtdicke und der Zusammensetzung.
- Vielseitigkeit:Eine breite Palette von Werkstoffen kann als Targets verwendet werden, und die Eigenschaften der Beschichtung können durch Anpassung der Prozessparameter maßgeschneidert werden.
Wenn diese Schritte befolgt werden, bieten PVD-Beschichtungen eine leistungsstarke, dauerhafte Oberfläche, die den hohen Anforderungen moderner industrieller Anwendungen gerecht wird.
Zusammenfassende Tabelle:
Schritt | Wichtige Details |
---|---|
Vorbereitung des Substrats | Reinigung und Vorbehandlung (Ätzen, Ionenbeschuss) für starke Haftung. |
Vakuum-Umgebung | Die Hochvakuumkammer (10-³ bis 10-⁹ Torr) gewährleistet eine kontaminationsfreie Verdampfung. |
Verdampfungstechniken | Elektronenstrahl-, Sputtering-, kathodische Bogen- oder thermische Verdampfungsmethoden. |
Reaktive Gase | Stickstoff oder Sauerstoff verändern die Beschichtungseigenschaften (z. B. Metallnitride/-oxide). |
Transport und Abscheidung | Das verdampfte Material kondensiert auf dem Substrat und bildet einen gleichmäßigen, dünnen Film. |
Post-Deposition-Prozesse | Qualitätskontrolle und Endbearbeitung (Polieren, Oberflächenmodifikation) für mehr Leistung. |
Entdecken Sie, wie PVD-Beschichtungen Ihre industriellen Anwendungen verbessern können. Kontaktieren Sie unsere Experten noch heute !