Eine Vakuumbeschichtungsanlage ist eine Spezialmaschine zum Aufbringen dünner Schutzschichten auf Substrate, in der Regel Metalle oder Keramiken, durch ein Verfahren, das als physikalische Gasphasenabscheidung (PVD) bezeichnet wird. Das Verfahren findet in einer Vakuumkammer statt, in der das Beschichtungsmaterial mit Hilfe von Wärmeenergie oder Plasma verdampft oder ionisiert und dann in einer kontrollierten Umgebung auf das Substrat aufgebracht wird. So entstehen nanoskalige Schichten, die Eigenschaften wie Härte, Verschleißfestigkeit und Korrosionsbeständigkeit verbessern. Die Vakuumbeschichtungsanlage besteht aus mehreren wichtigen Komponenten, darunter die Vakuumkammer, das Vakuumsystem, die Stromversorgung, das Gaszufuhrsystem und das Kühlsystem, die alle zusammenarbeiten, um eine präzise und effiziente Beschichtung zu gewährleisten.
Die wichtigsten Punkte erklärt:
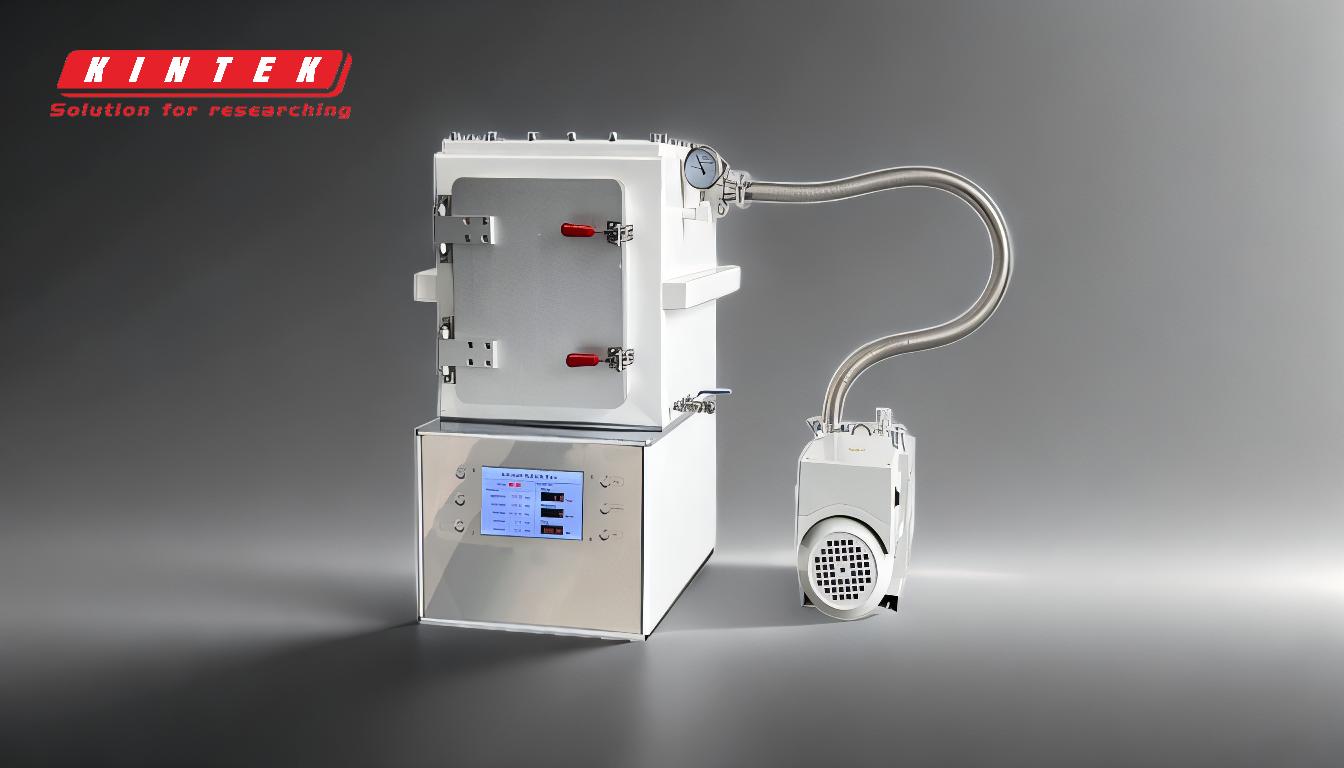
-
Vakuumkammer und Beschichtungsumgebung
- Die Vakuumkammer ist das Herzstück des Vakuumbeschichtungsgeräts. Sie bietet eine kontrollierte, unteratmosphärische Umgebung für den Beschichtungsprozess.
- Ein Vakuum ist unerlässlich, um Verunreinigungen zu beseitigen und die Reinheit der Beschichtung zu gewährleisten. Außerdem ermöglicht es die präzise Steuerung der verdampften Partikel, die sich auf dem Substrat ablagern.
- Die Kammer ist für hohe Temperaturen und Drücke ausgelegt und gewährleistet Stabilität während des Beschichtungsprozesses.
-
Verdampfung des Beschichtungsmaterials
- Der Beschichtungswerkstoff, in der Regel ein Metall oder eine Keramik, wird in der Vakuumkammer verdampft oder ionisiert.
- Dies geschieht durch thermische Energie (z. B. Widerstandsheizung) oder durch ein Plasma, das das Material in atomare oder molekulare Partikel zerlegt.
- Das verdampfte Material wird dann durch die Vakuumumgebung zum Substrat transportiert.
-
Abscheidungsprozess
- Das verdampfte Beschichtungsmaterial kondensiert auf dem Substrat und bildet eine dünne, gleichmäßige Schicht.
- Dieser Prozess wird in hohem Maße kontrolliert, um die gewünschte Dicke und die Eigenschaften der Beschichtung, oft im Nanobereich, zu gewährleisten.
- Die Abscheidung kann je nach Anwendung durch verschiedene PVD-Techniken erfolgen, z. B. durch Sputtern oder Aufdampfen.
-
Vorbereitung des Substrats
- Vor der Beschichtung wird das Substrat gründlich gereinigt, um Verunreinigungen zu entfernen und eine gute Haftung der Beschichtung zu gewährleisten.
- Dies kann durch abrasive Reinigung, chemische Behandlung oder Plasmareinigung in der Vakuumkammer erfolgen.
- Eine ordnungsgemäße Oberflächenvorbereitung ist entscheidend für eine hochwertige, dauerhafte Beschichtung.
-
Hauptkomponenten einer Vakuumbeschichtungsanlage
- Vakuumkammer und Beschichtungsanlage: Sie beherbergen das Substrat und das Beschichtungsmaterial und bieten eine kontrollierte Umgebung.
- Vakuum-Erzeugungssystem: Erzeugt und hält das Vakuum mit Hilfe von Pumpen und Dichtungen aufrecht.
- Vakuum-Messsystem: Überwacht das Druckniveau innerhalb der Kammer.
- Stromversorgung: Liefert Energie für die Verdampfung, Ionisierung und Plasmaerzeugung.
- Prozessgas-Eingangssystem: Führt reaktive oder inerte Gase ein, um den Beschichtungsprozess zu verbessern.
- Mechanisches Übertragungssystem: Bewegt das Substrat oder Beschichtungsmaterial je nach Bedarf.
- Heizung und Temperaturkontrolle: Reguliert die Temperatur für optimale Beschichtungsbedingungen.
- Ionenverdampfung und Sputtering-Quelle: Erzeugt das verdampfte Beschichtungsmaterial.
- Wasser-Kühlsystem: Verhindert die Überhitzung der Maschinenkomponenten.
-
Anwendungen und Vorteile
- Die Vakuumbeschichtung ist in Branchen wie der Luft- und Raumfahrt, der Automobilindustrie, der Elektronik und der Medizintechnik weit verbreitet.
- Die Beschichtungen bieten verbesserte Eigenschaften, wie z. B. höhere Härte, Verschleißfestigkeit, Korrosionsbeständigkeit und thermische Stabilität.
- Das Verfahren ist umweltfreundlich, da es die Abfallmenge minimiert und schädliche Chemikalien vermeidet.
-
Prozesskontrolle und Präzision
- Die Vakuumbeschichtungsanlage ermöglicht eine präzise Kontrolle der Schichtdicke, Zusammensetzung und Gleichmäßigkeit.
- Fortschrittliche Überwachungssysteme gewährleisten eine gleichbleibende Qualität und Leistung der Beschichtungen.
- Durch die Möglichkeit, Schichten im Nanobereich abzuscheiden, ist die Vakuumbeschichtung ideal für hochpräzise Anwendungen.
Durch die Kombination dieser Elemente erzeugt eine Vakuumbeschichtungsanlage Hochleistungsbeschichtungen, die den hohen Anforderungen der modernen Industrie gerecht werden. Das Verfahren ist ein Beweis für die Integration von fortschrittlicher Technik und Materialwissenschaft und liefert Lösungen, die die Haltbarkeit und Funktionalität wichtiger Komponenten verbessern.
Zusammenfassende Tabelle:
Schlüsselkomponente | Funktion |
---|---|
Vakuumkammer | Bietet eine kontrollierte, unteratmosphärische Umgebung für den Beschichtungsauftrag. |
System zur Erzeugung des Vakuums | Erzeugt und hält das Vakuum mit Hilfe von Pumpen und Dichtungen aufrecht. |
Stromversorgung | Liefert Energie für die Verdampfung, Ionisierung und Plasmaerzeugung. |
Prozessgas-Eingabesystem | Führt reaktive oder inerte Gase ein, um den Beschichtungsprozess zu verbessern. |
Wasser-Kühlsystem | Verhindert die Überhitzung von Maschinenkomponenten. |
Ionenverdampfung/Sputtering-Quelle | Erzeugt verdampftes Beschichtungsmaterial für die Abscheidung. |
Sind Sie bereit, Ihre Materialien mit Präzisionsbeschichtungen zu veredeln? Kontaktieren Sie uns noch heute um mehr über Vakuumbeschichtungsanlagen zu erfahren!