Die ideale Schichtdicke hängt von der Art der Beschichtung, der Anwendung und der gewünschten Leistung ab.Für Pulverbeschichtungen empfehlen die Hersteller in der Regel eine Schichtdicke von 2 bis 8 mils (50 bis 200 Mikrometer), um eine optimale Haltbarkeit, Korrosionsbeständigkeit und ein ästhetisches Finish zu gewährleisten.Bei anderen Arten von Beschichtungen, wie z. B. Dünnfilmbeschichtungen, kann die Schichtdicke jedoch wesentlich geringer sein und zwischen 0,25 und 5 Mikron liegen.Die erforderliche Schichtdicke hängt von Faktoren wie dem Substratmaterial, den Umgebungsbedingungen und den funktionalen Anforderungen des beschichteten Gegenstands ab.
Die wichtigsten Punkte erklärt:
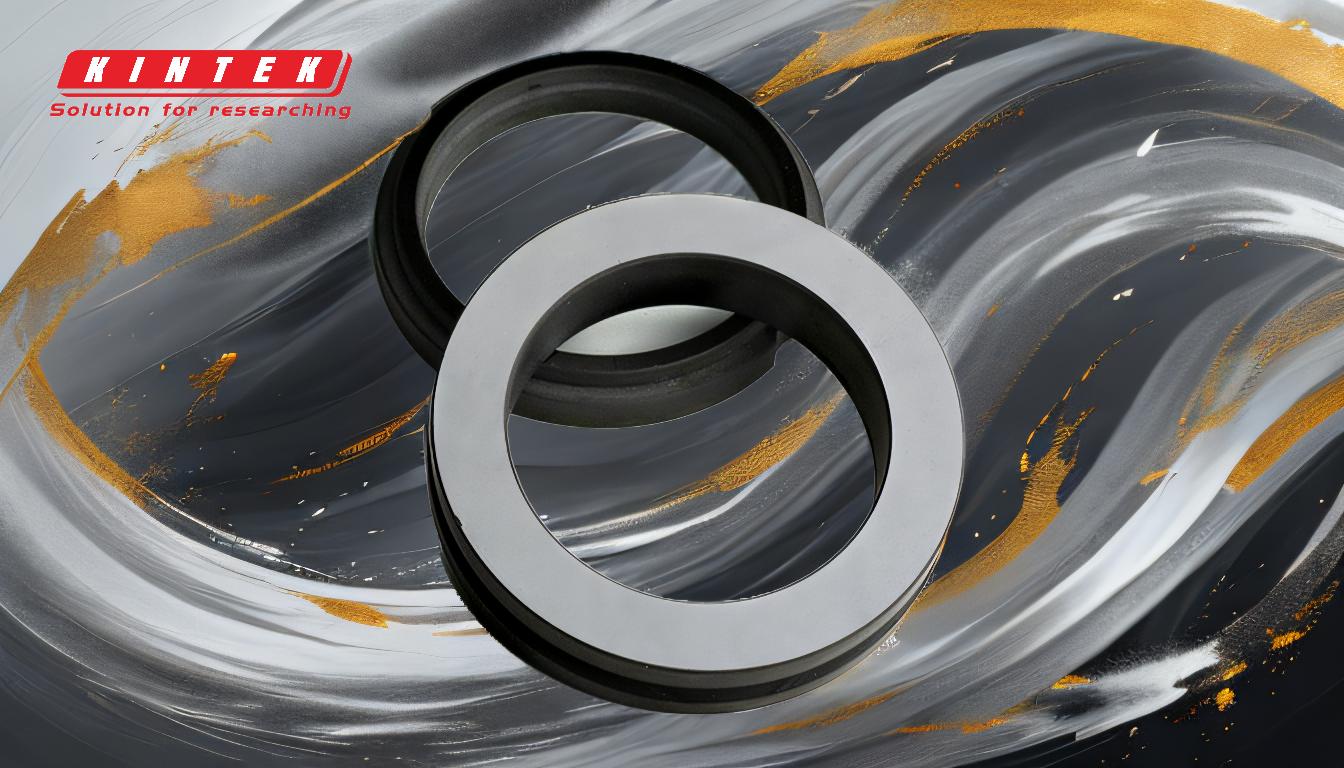
-
Empfehlungen zur Pulverbeschichtungsdicke:
- Die Hersteller von Pulverbeschichtungen empfehlen im Allgemeinen eine Schichtdicke von 2 bis 8 mils (50 bis 200 Mikrometer) für optimale Leistung.
-
Dieser Bereich gewährleistet:
- Langlebigkeit:Eine angemessene Dicke verhindert Absplitterungen, Risse und Abnutzung im Laufe der Zeit.
- Korrosionsbeständigkeit:Dickere Beschichtungen bieten einen besseren Schutz gegen Rost und Umweltschäden.
- Ästhetisches Finish:Die richtige Dicke gewährleistet eine gleichmäßige, glatte Oberfläche ohne Defekte wie Orangenhaut oder Nadelstiche.
-
Dünnfilm-Beschichtungsdicke:
- Bei Dünnfilmbeschichtungen, wie sie in der Elektronik oder bei optischen Anwendungen verwendet werden, ist die Dicke viel geringer und liegt normalerweise zwischen 0,25 bis 5 Mikrometer .
-
Diese Beschichtungen sind für spezifische Funktionen wie:
- Elektrische Isolierung:Dünne Beschichtungen können isolierend wirken, ohne die Masse zu erhöhen.
- Optische Klarheit:Ultradünne Beschichtungen sorgen für Transparenz und Lichtdurchlässigkeit.
- Abnutzungswiderstand:Selbst bei geringen Schichtdicken können diese Beschichtungen die Oberflächenhärte erhöhen und die Reibung verringern.
-
Faktoren, die die Beschichtungsdicke beeinflussen:
- Material des Substrats:Unterschiedliche Materialien (z. B. Metall, Kunststoff, Holz) erfordern unterschiedliche Beschichtungsstärken, um gut zu haften und zu funktionieren.
- Umweltbedingungen:In rauen Umgebungen (z. B. hohe Luftfeuchtigkeit, UV-Belastung) können dickere Beschichtungen für zusätzlichen Schutz erforderlich sein.
- Funktionelle Anforderungen:Der Verwendungszweck des beschichteten Gegenstands (z. B. dekorativ, strukturell oder funktionell) bestimmt die erforderliche Dicke.
- Anwendungsmethode:Techniken wie Sprühbeschichtung, Tauchbeschichtung oder elektrostatische Abscheidung können die erreichbare Dicke beeinflussen.
-
Wichtigkeit der Einhaltung der empfohlenen Schichtdicke:
- Zu dünn:Beschichtungen, die unterhalb des empfohlenen Bereichs liegen, können keinen ausreichenden Schutz bieten, was zu vorzeitigem Versagen, schlechter Haftung oder unzureichender Abdeckung führt.
- Zu dick:Eine zu dicke Schicht kann zu Problemen wie Rissbildung, Abblättern oder ungleichmäßiger Aushärtung führen, insbesondere bei Pulverbeschichtungen.Außerdem können sich dadurch die Materialkosten unnötig erhöhen.
-
Messung der Beschichtungsdicke:
- Werkzeuge wie Schichtdickenmessgeräte (z. B. magnetisch, Wirbelstrom oder Ultraschall) werden eingesetzt, um sicherzustellen, dass die Beschichtung die vorgegebenen Anforderungen erfüllt.
- Regelmäßige Qualitätskontrollen während und nach dem Beschichtungsprozess tragen dazu bei, Konsistenz und Leistung zu erhalten.
Durch die Kenntnis dieser wichtigen Punkte können Einkäufer und Verarbeiter fundierte Entscheidungen über die Beschichtungsdicke treffen, um das gewünschte Gleichgewicht zwischen Leistung, Haltbarkeit und Kosteneffizienz zu erreichen.
Zusammenfassende Tabelle:
Beschichtungsart | Schichtdicke | Wesentliche Vorteile |
---|---|---|
Pulverbeschichtung | 2 bis 8 Millimeter (50-200 µm) | Langlebigkeit, Korrosionsbeständigkeit, glatte Oberfläche und ästhetische Wirkung. |
Dünnfilmbeschichtung | 0,25 bis 5 Mikrometer | Elektrische Isolierung, optische Klarheit, Verschleißfestigkeit und geringere Reibung. |
Zu berücksichtigende Faktoren | Substratmaterial, Umgebungsbedingungen, funktionale Anforderungen, Anbringungsmethode. |
Benötigen Sie Hilfe bei der Bestimmung der richtigen Schichtdicke für Ihr Projekt? Kontaktieren Sie noch heute unsere Experten !