Das Pulversintern ist ein wichtiger Prozess in der Pulvermetallurgie und der Keramikherstellung, bei dem pulverförmige Materialien auf hohe Temperaturen unterhalb ihres Schmelzpunkts erhitzt werden, um die Partikel zu verbinden und dichte, hochfeste Komponenten zu schaffen.Dieses Verfahren umfasst mehrere Methoden, die jeweils einzigartige Merkmale und Anwendungen aufweisen.Zu den gängigen Sinterverfahren gehören das konventionelle Sintern, das Spark-Plasma-Sintern (SPS), das Mikrowellensintern, das heißisostatische Pressen (HIP) und das Heißpresssintern.Diese Verfahren unterscheiden sich in ihren Heizmechanismen, der Druckanwendung und den Umgebungsbedingungen, wie z. B. Vakuum oder Wasserstoffschutz.Die Wahl des Sinterverfahrens hängt von den Materialeigenschaften, der gewünschten Dichte und der mechanischen Leistung des Endprodukts ab.
Die wichtigsten Punkte werden erklärt:
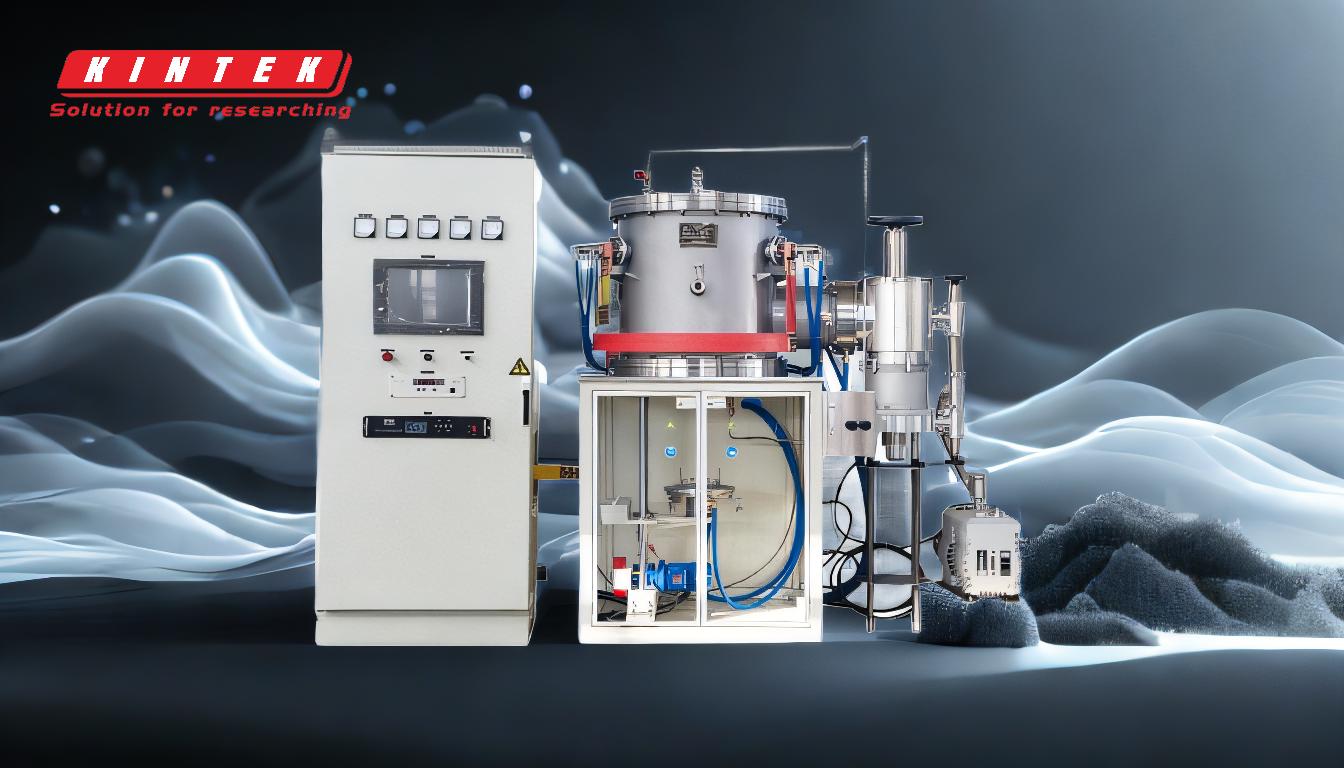
-
Konventionelles Sintern
- Dies ist das am weitesten verbreitete Sinterverfahren, bei dem pulverförmige Materialien in einem Ofen auf Temperaturen unterhalb ihres Schmelzpunktes erhitzt werden.
- Das Verfahren beruht auf thermischer Energie zur Förderung der Partikelbindung durch Diffusion, Verringerung der Oberflächenenergie und Schließen der Poren.
- Es eignet sich für eine breite Palette von Werkstoffen, darunter Metalle und Keramiken, und ist in der Großproduktion kostengünstig.
- Es kann jedoch längere Verarbeitungszeiten erfordern und im Vergleich zu fortschrittlichen Sinterverfahren zu einer geringeren Dichte führen.
-
Spark-Plasma-Sintern (SPS)
- SPS ist eine fortschrittliche Sintertechnik, bei der gepulste elektrische Ströme zur schnellen Erhitzung und Sinterung von Pulvern eingesetzt werden.
- Bei diesem Verfahren werden gleichzeitig Wärme und Druck angewendet, was eine schnellere Verdichtung und niedrigere Sintertemperaturen ermöglicht.
- SPS ist ideal für die Herstellung von Materialien mit hoher Dichte, feinen Mikrostrukturen und verbesserten mechanischen Eigenschaften.
- Es ist besonders nützlich für fortschrittliche Materialien wie Keramik, Verbundwerkstoffe und Nanomaterialien.
-
Sintern mit Mikrowellen
- Beim Mikrowellensintern werden elektromagnetische Wellen eingesetzt, um das pulverförmige Material direkt zu erhitzen, was zu einer gleichmäßigen und schnellen Erwärmung führt.
- Diese Methode ist energieeffizient und verkürzt die Verarbeitungszeit im Vergleich zum herkömmlichen Sintern.
- Es eignet sich für Materialien mit hohem dielektrischem Verlust, wie z. B. bestimmte Keramiken und Polymere.
- Durch das Sintern mit Mikrowellen können Produkte mit hoher Dichte und minimalem Kornwachstum hergestellt werden, wobei feine Mikrostrukturen erhalten bleiben.
-
Heiß-Isostatisches Pressen (HIP)
- Beim HIP-Verfahren werden pulverförmige Werkstoffe unter Verwendung von Inertgasen (z. B. Argon) bei hoher Temperatur und gleichmäßigem Druck gesintert.
- Bei diesem Verfahren werden innere Hohlräume und Defekte beseitigt, wodurch völlig dichte Bauteile mit hervorragenden mechanischen Eigenschaften entstehen.
- HIP wird häufig für kritische Anwendungen in der Luft- und Raumfahrt, für medizinische Implantate und Hochleistungslegierungen eingesetzt.
- Es eignet sich besonders gut für Werkstoffe, die mit herkömmlichen Methoden nur schwer zu verdichten sind.
-
Heißpress-Sintern
- Bei diesem Verfahren werden Wärme und einachsiger Druck gleichzeitig auf den Pulverpressling ausgeübt, was die Verdichtung fördert und die Sinterzeit verkürzt.
- Das Heißpresssintern eignet sich für Werkstoffe, die eine hohe Dichte und kontrollierte Mikrostrukturen erfordern, wie Keramiken und Hartmetalle.
- Das Verfahren wird häufig im Vakuum oder in einer Schutzatmosphäre durchgeführt, um Oxidation zu verhindern.
- Es findet breite Anwendung bei der Herstellung von Schneidwerkzeugen, verschleißfesten Komponenten und Hochleistungskeramik.
-
Umweltbedingungen beim Sintern
- Das Sintern kann unter verschiedenen Umgebungsbedingungen durchgeführt werden, z. B. im Vakuum, unter Wasserstoffschutz oder unter Schutzgasatmosphäre.
- Das Vakuumsintern verhindert Oxidation und Verunreinigung und ist daher ideal für reaktive Werkstoffe wie Titan und Refraktärmetalle.
- Wasserstoffschutz wird für oxidationsanfällige Materialien wie rostfreie Stähle und bestimmte Keramiken verwendet.
- Die Wahl der Umgebung hängt von der chemischen Reaktivität des Materials und den gewünschten Eigenschaften des Endprodukts ab.
-
Behandlungen nach dem Sintern
- Nach dem Sintern können zusätzliche Behandlungen durchgeführt werden, um die Eigenschaften des gesinterten Teils zu verbessern.
- Zu den üblichen Nachbehandlungen gehören Wärmebehandlung, Oberflächenbehandlung und maschinelle Bearbeitung.
- Die Wärmebehandlung verbessert die mechanischen Eigenschaften wie Härte und Zähigkeit, während die Oberflächenbehandlung die Verschleißfestigkeit und das Aussehen verbessert.
- Diese Behandlungen stellen sicher, dass das Endprodukt bestimmte Leistungsanforderungen erfüllt.
-
Materialüberlegungen beim Sintern
- Die Wahl des Sinterverfahrens hängt von den Materialeigenschaften ab, wie z. B. Schmelzpunkt, Reaktivität und Partikelgröße.
- Metallpulver, wie z. B. Materialien auf Kupfer- und Eisenbasis, werden in der Regel mit konventionellen oder fortschrittlichen Verfahren gesintert.
- Keramische Pulver erfordern eine präzise Steuerung der Sinterbedingungen, um eine hohe Dichte zu erreichen und Risse zu vermeiden.
- Hochentwickelte Werkstoffe wie Verbundwerkstoffe und Nanomaterialien profitieren häufig von schnellen Sintertechniken wie SPS oder Mikrowellensintern.
-
Anwendungen von Sinterverfahren
- Das konventionelle Sintern ist in der Automobil-, Elektronik- und Konsumgüterindustrie für die Herstellung kostengünstiger Komponenten weit verbreitet.
- SPS und HIP werden für Hochleistungsanwendungen in der Luft- und Raumfahrt, bei medizinischen Geräten und im Energiesektor bevorzugt.
- Das Mikrowellensintern wird aufgrund seiner Energieeffizienz und seiner Fähigkeit, Hochleistungskeramik zu verarbeiten, immer beliebter.
- Das Heißpresssintern wird üblicherweise für die Herstellung von Schneidwerkzeugen, verschleißfesten Teilen und Strukturkeramik verwendet.
Wenn die Hersteller die verschiedenen Sinterverfahren und ihre Anwendungen kennen, können sie die am besten geeignete Technik auswählen, um die gewünschten Materialeigenschaften und Leistungsmerkmale zu erzielen.Jedes Verfahren bietet einzigartige Vorteile und macht das Pulversintern zu einem vielseitigen und unverzichtbaren Prozess in der modernen Fertigung.
Zusammenfassende Tabelle:
Sinterverfahren | Wesentliche Merkmale | Anwendungen |
---|---|---|
Konventionelle Sinterung | Kosteneffektiv, auf thermischer Energie basierend, geeignet für Metalle und Keramiken | Automobil, Elektronik, Konsumgüter |
Funkenplasmasintern (SPS) | Schnelle Erwärmung, hohe Dichte, feine Mikrostrukturen | Hochleistungskeramik, Verbundwerkstoffe, Nanomaterialien |
Mikrowellen-Sintern | Energieeffiziente, gleichmäßige Erwärmung, minimales Kornwachstum | Materialien mit hohem dielektrischen Verlust, Hochleistungskeramik |
Heiß-Isostatisches Pressen (HIP) | Hohe Temperatur, gleichmäßiger Druck, vollständig dichte Komponenten | Luft- und Raumfahrt, medizinische Implantate, Hochleistungslegierungen |
Heißpress-Sintern | Gleichzeitige Hitze und Druck, hohe Dichte, kontrollierte Gefüge | Schneidwerkzeuge, verschleißfeste Komponenten, Hochleistungskeramik |
Benötigen Sie Hilfe bei der Auswahl des richtigen Sinterverfahrens für Ihre Werkstoffe? Kontaktieren Sie noch heute unsere Experten !