Selektives Lasersintern (SLS) ist eine 3D-Drucktechnologie, die einzigartige Vorteile bietet, wie z. B. die Möglichkeit, hochkomplexe und funktionale Teile mit minimaler Nachbearbeitung herzustellen.Sie bringt jedoch auch erhebliche Nachteile mit sich, darunter hohe Kosten für Ausrüstung und Materialien sowie den Bedarf an qualifiziertem Personal.Diese Technologie eignet sich besonders für Anwendungen, die komplizierte Formen erfordern, ist aber für die Massenproduktion möglicherweise nicht kosteneffizient.Die Pulvermetallurgie ist dagegen wirtschaftlicher für mittelkomplexe Formen und Großserienfertigung, obwohl sie aufgrund der Reibung während der Verarbeitung zu weniger gleichmäßigen Komponenten führen kann.
Die wichtigsten Punkte erklärt:
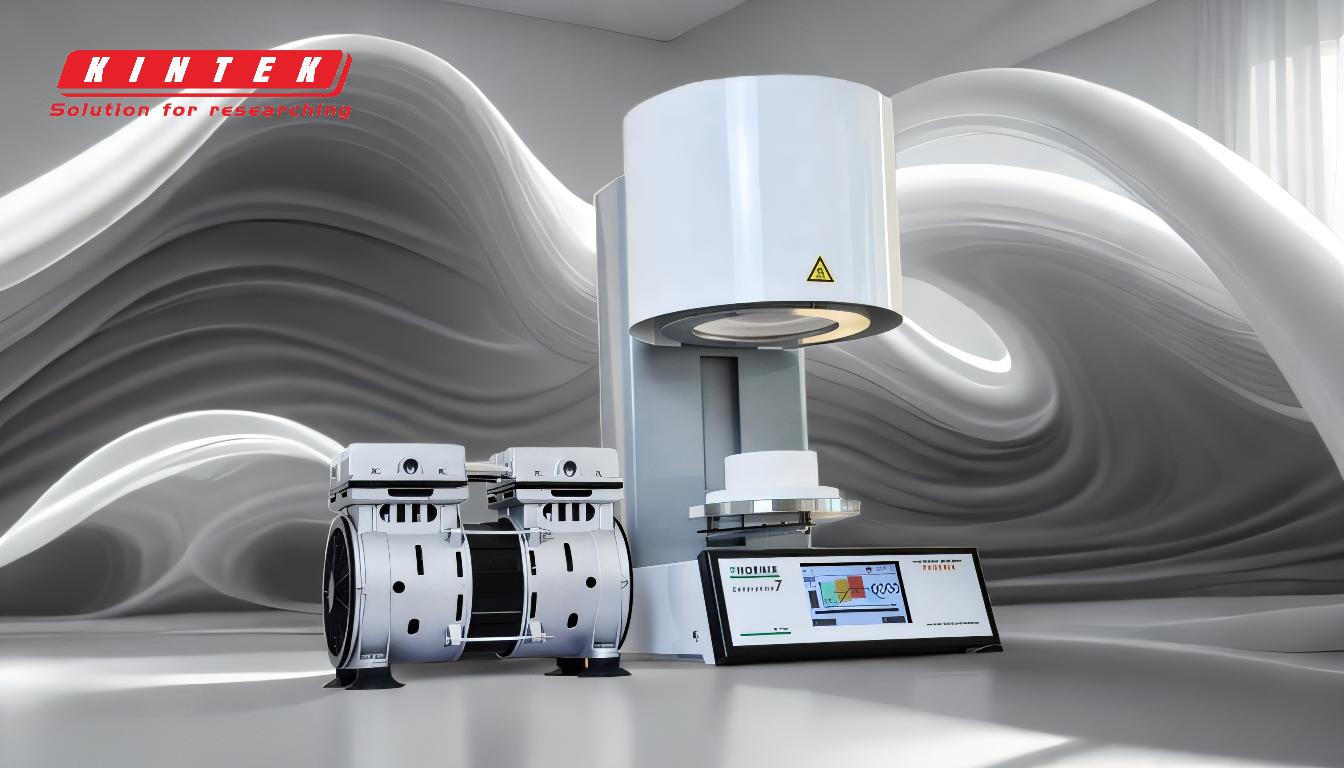
-
Vorteile von SLS:
- Komplexe und funktionelle Formen:SLS eignet sich hervorragend für die Herstellung komplizierter Geometrien, die mit herkömmlicher Sintertechnik oder Pulvermetallurgie nur schwer oder gar nicht zu erreichen sind.Dies macht es ideal für das Prototyping und die Herstellung von Teilen mit komplexen inneren Strukturen oder feinen Details.
- Minimale Nachbearbeitung:Im SLS-Verfahren hergestellte Teile benötigen oft nur wenig oder gar keine zusätzliche Nachbearbeitung, da das Verfahren von Natur aus glatte Oberflächen und funktionale Komponenten erzeugt.
- Material Vielseitigkeit:SLS kann mit einer Vielzahl von Materialien arbeiten, darunter Polymere, Metalle und Keramiken, und bietet somit Flexibilität bei der Materialauswahl für bestimmte Anwendungen.
-
Nachteile von SLS:
- Hohe Kosten:Die Erstinvestition für SLS-Maschinen ist beträchtlich und liegt oft bei über 250.000 Dollar.Außerdem sind die beim SLS-Verfahren verwendeten Materialien teuer, was die Gesamtproduktionskosten weiter erhöht.
- Bedarf an qualifizierten Arbeitskräften:Die Bedienung von SLS-Maschinen erfordert spezielle Kenntnisse und Schulungen, was die Arbeitskosten in die Höhe treibt und die Zugänglichkeit für kleinere Unternehmen einschränkt.
- Begrenzte Skalierbarkeit:SLS eignet sich zwar hervorragend für die Kleinserienfertigung und das Prototyping, ist aber aufgrund der langsameren Produktionsgeschwindigkeit und der höheren Stückkosten für die Großserienfertigung nicht kosteneffizient.
-
Vergleich mit der Pulvermetallurgie:
- Kosten-Wirksamkeit:Die Pulvermetallurgie ist in der Regel kostengünstiger als das SLS-Verfahren und daher die bessere Wahl für die Großserienfertigung von Teilen mittlerer Komplexität.
- Einfachheit der Bedienung:Im Gegensatz zum SLS erfordert die Pulvermetallurgie keine hochqualifizierten Mitarbeiter, was die Arbeitskosten senkt und den Produktionsprozess vereinfacht.
- Fragen der Gleichmäßigkeit:Die Pulvermetallurgie kann jedoch aufgrund der Reibung zwischen dem Pulver und den Werkzeugen während der Pressphase zu ungleichmäßigen Bauteilen führen, was die mechanischen Eigenschaften des Endprodukts beeinträchtigen kann.
-
Anwendungen und Eignung:
- SLS:Am besten geeignet für Anwendungen, die eine hohe Komplexität erfordern, wie z. B. Luft- und Raumfahrtkomponenten, medizinische Geräte und kundenspezifische Werkzeuge.Seine Fähigkeit, schnell funktionale Prototypen herzustellen, macht es in Branchen wertvoll, in denen Design-Iterationen entscheidend sind.
- Pulvermetallurgie:Eher geeignet für die Großserienproduktion von Teilen mit mittlerer Komplexität, wie z. B. Automobilkomponenten, Zahnräder und Lager.Seine Kosteneffizienz und Skalierbarkeit machen es zu einer beliebten Wahl für die Massenproduktion.
-
Zukünftige Überlegungen:
- Technologischer Fortschritt:Mit der Weiterentwicklung der SLS-Technologie könnten die Kosten sinken, und das Verfahren könnte für ein breiteres Spektrum von Branchen zugänglicher werden.Verbesserungen in der Materialwissenschaft könnten auch das Anwendungsspektrum von SLS erweitern.
- Hybride Ansätze:Die Kombination von SLS mit anderen Fertigungsverfahren, wie z. B. der Pulvermetallurgie, könnte ein Gleichgewicht zwischen Komplexität, Kosten und Skalierbarkeit bieten, das neue Möglichkeiten in der fortgeschrittenen Fertigung eröffnen könnte.
Zusammenfassend lässt sich sagen, dass SLS unvergleichliche Möglichkeiten zur Herstellung komplexer und funktionaler Teile bietet, jedoch mit erheblichen Kosten und betrieblichen Herausforderungen verbunden ist.Die Pulvermetallurgie ist zwar in Bezug auf die Designkomplexität weniger vielseitig, bietet aber eine wirtschaftlichere Lösung für die Großserienproduktion.Die Wahl zwischen diesen Technologien hängt von den spezifischen Anforderungen der Anwendung ab, einschließlich Komplexität, Volumen und Budgetbeschränkungen.
Zusammenfassende Tabelle:
Aspekt | Selektives Laser-Sintern (SLS) | Pulvermetallurgie |
---|---|---|
Komplexität | Hervorragend geeignet für komplizierte Geometrien und komplexe Formen. | Begrenzt auf mittelkomplexe Formen. |
Kosten | Hohe Ausrüstungs- und Materialkosten; nicht kosteneffizient für die Massenproduktion. | Wirtschaftlicher für die Großserienfertigung. |
Nachbearbeitung | Minimale Nachbearbeitung erforderlich. | Kann aufgrund von Gleichmäßigkeitsproblemen zusätzliche Nachbearbeitung erfordern. |
Geschicklichkeit des Bedieners | Erfordert qualifizierte Bediener. | Leichtere Bedienung, geringere Arbeitskosten. |
Skalierbarkeit | Am besten geeignet für Kleinserienproduktion und Prototypenbau. | Ideal für die Großserienproduktion. |
Anwendungen | Luft- und Raumfahrt, medizinische Geräte und kundenspezifischer Werkzeugbau. | Automobilkomponenten, Zahnräder und Lager. |
Entdecken Sie, wie SLS oder Pulvermetallurgie Ihren Fertigungsprozess verändern kann. Kontaktieren Sie uns noch heute für fachkundige Beratung!