Die PVD-Beschichtung (Physical Vapour Deposition) ist eine weit verbreitete Technik zum Aufbringen dünner Filme auf Oberflächen und bietet Vorteile wie hohe Härte, Verschleißfestigkeit und niedrigere Prozesstemperaturen. Allerdings bringt es auch einige Nachteile mit sich, die seine Eignung für bestimmte Anwendungen beeinträchtigen können. Zu diesen Nachteilen gehören hohe Kosten aufgrund spezieller Geräte- und Vakuumanforderungen, Einschränkungen bei der Beschichtung komplexer Geometrien, niedrige Abscheidungsraten und die Tatsache, dass es sich um ein „Sichtlinien“-Verfahren handelt, das seine Verwendung für nicht sichtbare Oberflächen einschränkt. Darüber hinaus kann der Prozess zeitaufwändig sein und erfordert eine sorgfältige Temperaturkontrolle und Kühlsysteme, um Schäden an Komponenten zu verhindern.
Wichtige Punkte erklärt:
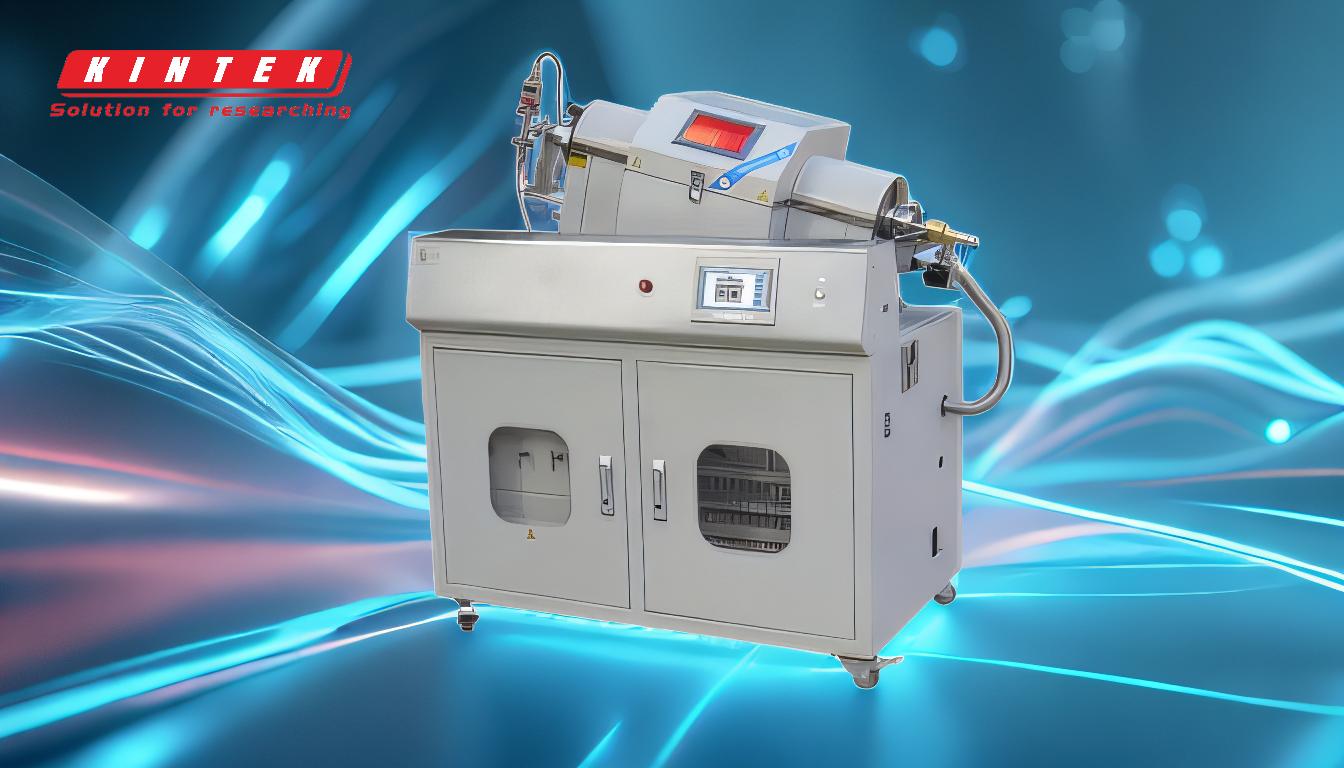
-
Hohe Kosten für Ausrüstung und Betrieb
- Für die PVD-Beschichtung sind spezielle Geräte erforderlich, darunter große Vakuumkammern und Kühlsysteme, deren Anschaffung und Wartung teuer sein können.
- Der Prozess erfordert intensive Heiz- und Kühlzyklen, was die Betriebskosten erhöht.
- Der Bedarf an hoher Fachkenntnis und Präzision im Umgang mit der Ausrüstung trägt zusätzlich zu den Gesamtkosten bei.
-
Einschränkung der Sichtlinie
- PVD ist ein „Sichtlinien“-Verfahren, das heißt, es können nur Oberflächen beschichtet werden, die direkt dem Dampfstrom ausgesetzt sind.
- Diese Einschränkung macht es ungeeignet für die Beschichtung komplexer Geometrien oder nicht sichtbarer Oberflächen wie interne Hohlräume oder komplizierte Designs.
-
Niedrige Abscheidungsrate und geringer Durchsatz
- Die Abscheidungsrate von PVD ist relativ langsam und liegt typischerweise im Bereich von 1–2 Å/s, was zu längeren Verarbeitungszeiten führen kann.
- Der Prozess ist nicht einfach skalierbar, was im Vergleich zu anderen Beschichtungsverfahren zu einem geringeren Durchsatz führt.
- Dies macht PVD für die Massenproduktion weniger effizient.
-
Komplexität und zeitraubende Natur
- PVD ist eine der komplexesten Abscheidungsmethoden und erfordert eine präzise Steuerung der Vakuumbedingungen, der Temperatur und der Kühlsysteme.
- Der Prozess ist im Vergleich zu anderen Techniken langsamer, was die Produktionszeit verzögern kann.
-
Herausforderungen mit komplexen Geometrien
- Obwohl bei der Lösung dieses Problems Fortschritte erzielt wurden, hat PVD immer noch Probleme mit der gleichmäßigen Beschichtung von Teilen mit komplexen Formen.
- Um gleichmäßige Beschichtungen auf komplizierten Designs zu erzielen, sind möglicherweise spezielle Methoden und Geräte erforderlich, was die Komplexität und die Kosten erhöht.
-
Materialverschwendung und Farbverfälschung
- PVD kann Farben aggressiv verändern oder zerstören, was zu Materialverschwendung und potenziellen ästhetischen Problemen führt.
- Dieser Nachteil kann den Einsatz bei Anwendungen einschränken, bei denen die Farbkonservierung von entscheidender Bedeutung ist.
-
Hohes Stress- und Wärmemanagement
- PVD-Beschichtungen können während des Abscheidungsprozesses hohe Spannungen erzeugen, die die Haltbarkeit der Beschichtung beeinträchtigen können.
- Um die Wärme abzuleiten und Schäden sowohl an der Beschichtung als auch am Untergrund zu verhindern, sind geeignete Kühlsysteme unerlässlich.
-
Begrenzte Eignung für bestimmte Anwendungen
- Trotz seiner Vorteile ist PVD möglicherweise nicht für alle Anwendungen die beste Wahl, insbesondere für solche, die eine schnelle Produktion, komplexe Geometrien oder eine Beschichtung ohne Sichtlinie erfordern.
Zusammenfassend lässt sich sagen, dass die PVD-Beschichtung zwar erhebliche Vorteile wie hohe Härte, Verschleißfestigkeit und niedrigere Prozesstemperaturen bietet, ihre Nachteile – darunter hohe Kosten, Einschränkungen der Sichtlinie, niedrige Abscheidungsraten und Herausforderungen bei komplexen Geometrien – jedoch sorgfältig abgewogen werden müssen bei der Auswahl einer Beschichtungsmethode für bestimmte Anwendungen.
Übersichtstabelle:
Nachteile der PVD-Beschichtung | Einzelheiten |
---|---|
Hohe Ausrüstungskosten | Spezialausrüstung, Vakuumkammern und Kühlsysteme erhöhen die Kosten. |
Einschränkung der Sichtlinie | Nicht sichtbare Oberflächen oder komplexe Geometrien können nicht effektiv beschichtet werden. |
Niedrige Ablagerungsrate | Langsame Abscheidungsraten (1–2 Å/s) verringern den Durchsatz und die Effizienz. |
Komplexität und Zeitaufwand | Erfordert eine präzise Steuerung von Vakuum-, Temperatur- und Kühlsystemen. |
Herausforderungen mit komplexen Formen | Eine gleichmäßige Beschichtung komplizierter Designs ist schwierig und kostspielig. |
Materialverschwendung | Kann Farben verändern oder zerstören, was zu ästhetischen und materiellen Problemen führen kann. |
Hohe Belastung und thermische Probleme | Erfordert wirksame Kühlsysteme, um Hitze und Stress zu bewältigen. |
Begrenzte Eignung | Nicht ideal für schnelle Produktion oder Anwendungen ohne Sichtverbindung. |
Benötigen Sie Hilfe bei der Entscheidung, ob eine PVD-Beschichtung für Ihr Projekt geeignet ist? Kontaktieren Sie noch heute unsere Experten für persönliche Beratung!