Das Flüssigphasensintern ist zwar vorteilhaft für die Verbesserung der Verdichtung und die Senkung der Sintertemperaturen, bringt aber auch einige Nachteile mit sich. Dazu gehören Herausforderungen bei der Kontrolle der Mikrostruktur, das Potenzial für ungleichmäßige Verdichtung und Einschränkungen bei der Materialauswahl aufgrund der Notwendigkeit einer kompatiblen Flüssigphase. Außerdem kann das Verfahren zu Problemen wie Kornwachstum, Eigenspannungen und Anisotropie der Eigenschaften führen. Die hohen Temperaturen und der hohe Energieverbrauch, die mit dem Flüssigphasensintern verbunden sind, tragen ebenfalls zu erhöhten Betriebskosten und Umweltproblemen bei. Das Verständnis dieser Nachteile ist entscheidend für die Optimierung des Prozesses und die Auswahl der richtigen Materialien und Parameter für bestimmte Anwendungen.
Die wichtigsten Punkte werden erklärt:
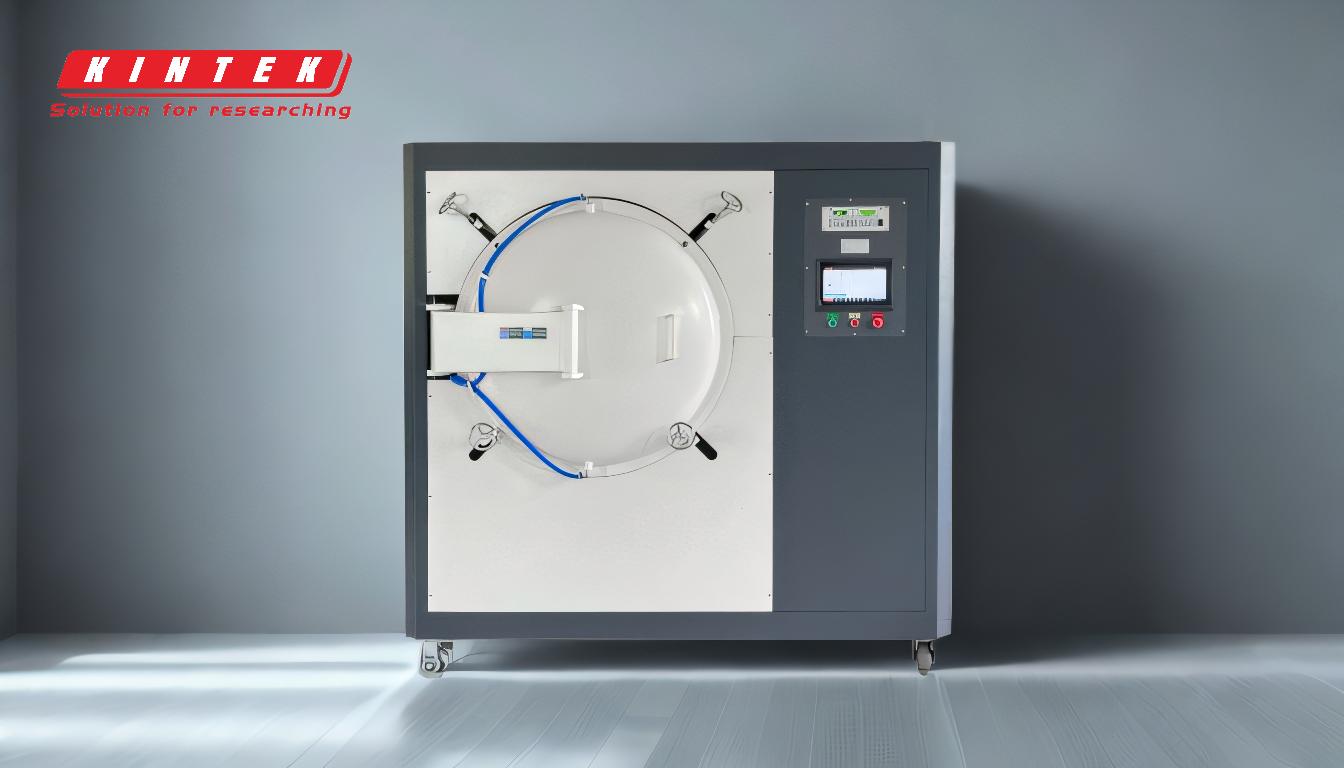
-
Herausforderungen bei der Mikrostrukturkontrolle:
- Das Flüssigphasensintern kann zu ungleichmäßigem Kornwachstum und Vergröberung führen, was ein weniger einheitliches Gefüge zur Folge hat.
- Das Vorhandensein einer flüssigen Phase kann eine örtlich begrenzte Verdichtung verursachen, was zu Schwankungen der Dichte und der mechanischen Eigenschaften des Sinterteils führt.
-
Anisotropie der Eigenschaften:
- Der Fluss der flüssigen Phase während des Sinterns kann eine gerichtete Ausrichtung der Körner verursachen, was zu einer Anisotropie der mechanischen, thermischen und elektrischen Eigenschaften führt.
- Diese Anisotropie kann für Anwendungen, die isotropes Verhalten erfordern, problematisch sein.
-
Einschränkungen bei der Materialauswahl:
- Das Flüssigphasensintern erfordert die Bildung einer kompatiblen flüssigen Phase, was die Bandbreite der Materialien, die mit dieser Methode effektiv gesintert werden können, einschränkt.
- Der Bedarf an spezifischen Additiven zur Bildung der flüssigen Phase kann die Materialformulierung erschweren und die Kosten erhöhen.
-
Eigenspannungen und Defekte:
- Der Abkühlungsprozess nach dem Sintern in der Flüssigphase kann aufgrund der unterschiedlichen Schrumpfung zwischen der festen und der flüssigen Phase zu Eigenspannungen führen.
- Diese Spannungen können zu Rissen, Verwerfungen oder anderen Mängeln im Endprodukt führen.
-
Hoher Energieverbrauch:
- Beim Flüssigphasensintern sind oft hohe Temperaturen erforderlich, um die notwendige Flüssigphasenbildung zu erreichen, was zu einem erhöhten Energieverbrauch führt.
- Dies trägt zu höheren Betriebskosten und Umweltbelastungen bei.
-
Wachstum und Vergröberung der Körner:
- Die flüssige Phase kann das Kornwachstum beschleunigen, was die mechanischen Eigenschaften des gesinterten Materials beeinträchtigen kann.
- Die Kontrolle der Korngröße wird immer schwieriger und erfordert eine präzise Steuerung der Sinterparameter.
-
Kosten und Komplexität:
- Die für das Flüssigphasensintern erforderlichen Anlagen und die Prozesssteuerung sind im Vergleich zum Festphasensintern komplexer und teurer.
- Der Bedarf an speziellen Gussformen, Zusatzstoffen und Hochtemperaturöfen erhöht die Gesamtkosten.
-
Schrumpfung und Abmessungskontrolle:
- Bei Teilen, die mit einer flüssigen Phase gesintert werden, kommt es häufig zu einer stärkeren Schrumpfung, die bei der Konstruktion und Herstellung berücksichtigt werden muss.
- Dies kann die Herstellung von Teilen mit engen Maßtoleranzen erschweren.
-
Umwelt- und Sicherheitsaspekte:
- Die hohen Temperaturen und die mögliche Verwendung gefährlicher Stoffe beim Flüssigphasensintern können Sicherheitsrisiken und Umweltprobleme mit sich bringen.
- Eine ordnungsgemäße Handhabung und Entsorgung von Materialien und Nebenprodukten ist notwendig, um diese Bedenken zu zerstreuen.
Wenn die Hersteller diese Nachteile kennen, können sie die Eignung des Flüssigphasensinterns für ihre spezifischen Anwendungen besser beurteilen und Maßnahmen ergreifen, um potenzielle Probleme durch eine sorgfältige Prozessgestaltung und Materialauswahl zu verringern.
Zusammenfassende Tabelle:
Nachteil | Wichtige Details |
---|---|
Kontrolle der Mikrostruktur | Ungleichmäßiges Kornwachstum, örtlich begrenzte Verdichtung und ungleichmäßige Eigenschaften. |
Anisotropie der Eigenschaften | Richtungsabhängige Kornausrichtung, die zu uneinheitlichem mechanischen/thermischen Verhalten führt. |
Einschränkungen bei der Materialauswahl | Erfordert eine kompatible Flüssigphase, was die Materialauswahl einschränkt und die Kosten erhöht. |
Eigenspannungen und Defekte | Unterschiedliche Schrumpfung führt zu Rissen, Verwerfungen oder anderen Mängeln. |
Hoher Energieverbrauch | Hohe Temperaturen erhöhen den Energiebedarf und die Betriebskosten. |
Wachstum und Vergröberung der Körner | Ein beschleunigtes Kornwachstum verschlechtert die mechanischen Eigenschaften. |
Kosten und Komplexität | Spezialisierte Anlagen und Zusatzstoffe erhöhen die Kosten und die Komplexität des Prozesses. |
Schrumpfung und Abmessungskontrolle | Größere Schrumpfung erschwert die Fertigung mit engen Toleranzen. |
Umwelt- und Sicherheitsaspekte | Hohe Temperaturen und gefährliche Stoffe bergen Risiken und Umweltprobleme. |
Benötigen Sie Hilfe bei der Optimierung Ihres Sinterprozesses? Kontaktieren Sie unsere Experten noch heute für maßgeschneiderte Lösungen!