Ein Induktionsofen vom Direktkerntyp ist zwar hocheffizient und für Betriebe mit hohem Durchsatz geeignet, weist jedoch mehrere erhebliche Nachteile auf. Dazu gehören die Notwendigkeit einer kontinuierlichen Aufrechterhaltung des Metallkreislaufs, die Unfähigkeit, Beschickungsmaterialien zu raffinieren, und die Anforderung, dass Beschickungsmaterialien frei von Oxiden und von bekannter Zusammensetzung sein müssen. Darüber hinaus darf der Ofen selten abkühlen, was den Betrieb und die Wartung erschweren kann. Diese Faktoren machen es weniger flexibel für Operationen, die häufige Legierungswechsel erfordern oder Materialien mit unterschiedlichen Zusammensetzungen verwenden.
Wichtige Punkte erklärt:
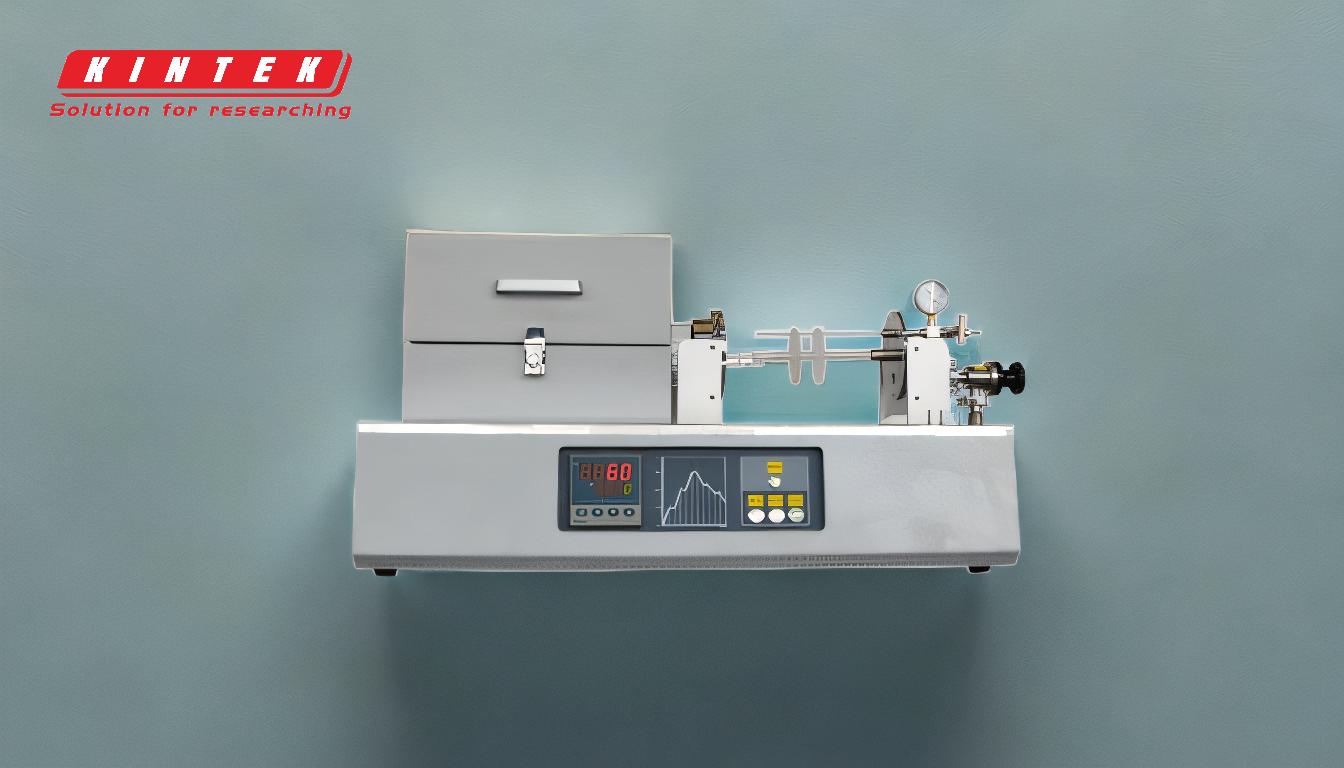
-
Kontinuierliche Wartung des Metallkreislaufs:
- Der Direktkern-Induktionsofen erfordert eine laufende Wartung, um sicherzustellen, dass der Metallkreislauf intakt und funktionsfähig bleibt. Diese kontinuierliche Wartung kann arbeitsintensiv sein und im Laufe der Zeit zu erhöhten Betriebskosten führen.
-
Mangel an Raffinationskapazität:
- Im Gegensatz zu einigen anderen Ofentypen verfügt der Direktkern-Induktionsofen nicht über die Fähigkeit, Beschickungsmaterialien zu raffinieren. Dies bedeutet, dass die verwendeten Materialien bereits frei von Oxiden sein müssen und eine bekannte Zusammensetzung aufweisen, wodurch die Art der Materialien, die verarbeitet werden können, begrenzt ist.
-
Oxidation und Verlust von Legierungselementen:
- Während des Schmelzprozesses können einige Legierungselemente durch Oxidation verloren gehen. Dies erfordert die erneute Zugabe dieser Elemente zur Schmelze, was den Prozess verkomplizieren und die Materialkosten erhöhen kann.
-
Unfähigkeit, sich abzukühlen:
- Der Ofen darf selten abkühlen, was den Betrieb und die Wartung erschweren kann. Dieser kontinuierliche Betrieb kann zu Verschleiß an den Ofenkomponenten führen und möglicherweise die Gesamtlebensdauer der Ausrüstung verkürzen.
-
Begrenzte Flexibilität bei Legierungsänderungen:
- Der Direktkern-Induktionsofen eignet sich nicht gut für Betriebe, die häufige Legierungswechsel erfordern. Dieser Mangel an Flexibilität kann ein erheblicher Nachteil für Anlagen sein, die eine Vielzahl von Materialien mit unterschiedlichen Zusammensetzungen verarbeiten müssen.
-
Hohe Anschaffungs- und Betriebskosten:
- Obwohl der Ofen effizient ist, können die anfänglichen Einrichtungs- und laufenden Wartungskosten hoch sein. Dazu gehören die Kosten für die Aufrechterhaltung des Metallkreislaufs und der Bedarf an hochwertigen, oxidfreien Einsatzmaterialien.
-
Komplexität im Betrieb:
- Die Anforderungen an einen kontinuierlichen Betrieb und die Notwendigkeit einer präzisen Kontrolle der Beschickungsmaterialien können den Betrieb eines Direktkern-Induktionsofens im Vergleich zu anderen Ofentypen komplexer machen.
Zusammenfassend lässt sich sagen, dass der Direktkern-Induktionsofen zwar einen hohen Wirkungsgrad bietet und für Betriebe mit hohem Durchsatz geeignet ist, seine Nachteile, einschließlich der Notwendigkeit einer kontinuierlichen Wartung, mangelnder Raffinierungskapazität und begrenzter Flexibilität für Legierungswechsel, ihn jedoch weniger ideal für machen bestimmte Anwendungen. Diese Faktoren sollten bei der Auswahl eines Ofens für spezifische industrielle Anforderungen sorgfältig berücksichtigt werden.
Übersichtstabelle:
Nachteil | Erläuterung |
---|---|
Kontinuierliche Wartung der Metallschleife | Erfordert ständige Wartung, wodurch die Arbeits- und Betriebskosten steigen. |
Mangel an Raffinationskapazität | Ladungsmaterialien können nicht verfeinert werden; Materialien müssen oxidfrei sein und eine bekannte Zusammensetzung haben. |
Oxidation und Verlust von Legierungselementen | Legierungselemente können oxidieren, was eine erneute Zugabe erforderlich macht und die Materialkosten erhöht. |
Unfähigkeit, sich abzukühlen | Lässt es selten abkühlen, was den Betrieb und die Wartung erschwert. |
Begrenzte Flexibilität bei Legierungsänderungen | Nicht ideal für häufige Legierungswechsel oder Materialien mit unterschiedlicher Zusammensetzung. |
Hohe Anschaffungs- und Betriebskosten | Hohe Einrichtungs- und Wartungskosten, einschließlich Wartung der Metallschleife und Materialqualität. |
Komplexität im Betrieb | Kontinuierlicher Betrieb und präzise Materialkontrolle machen den Betrieb komplexer. |
Erwägen Sie einen Ofen für Ihren Betrieb? Kontaktieren Sie noch heute unsere Experten um die beste Lösung für Ihre Bedürfnisse zu finden!