Die Anwendung von Dünnschichten umfasst eine Vielzahl von Verfahren, die sich grob in chemische und physikalische Abscheidetechniken einteilen lassen.Mit diesen Verfahren lassen sich Dicke, Zusammensetzung und Eigenschaften der dünnen Schichten genau steuern, so dass sie sich für ein breites Spektrum von Anwendungen eignen, von Halbleitern bis hin zu flexibler Elektronik.Die Wahl des Verfahrens hängt von den gewünschten Schichteigenschaften, dem Substratmaterial und den spezifischen Anwendungsanforderungen ab.
Die wichtigsten Punkte erklärt:
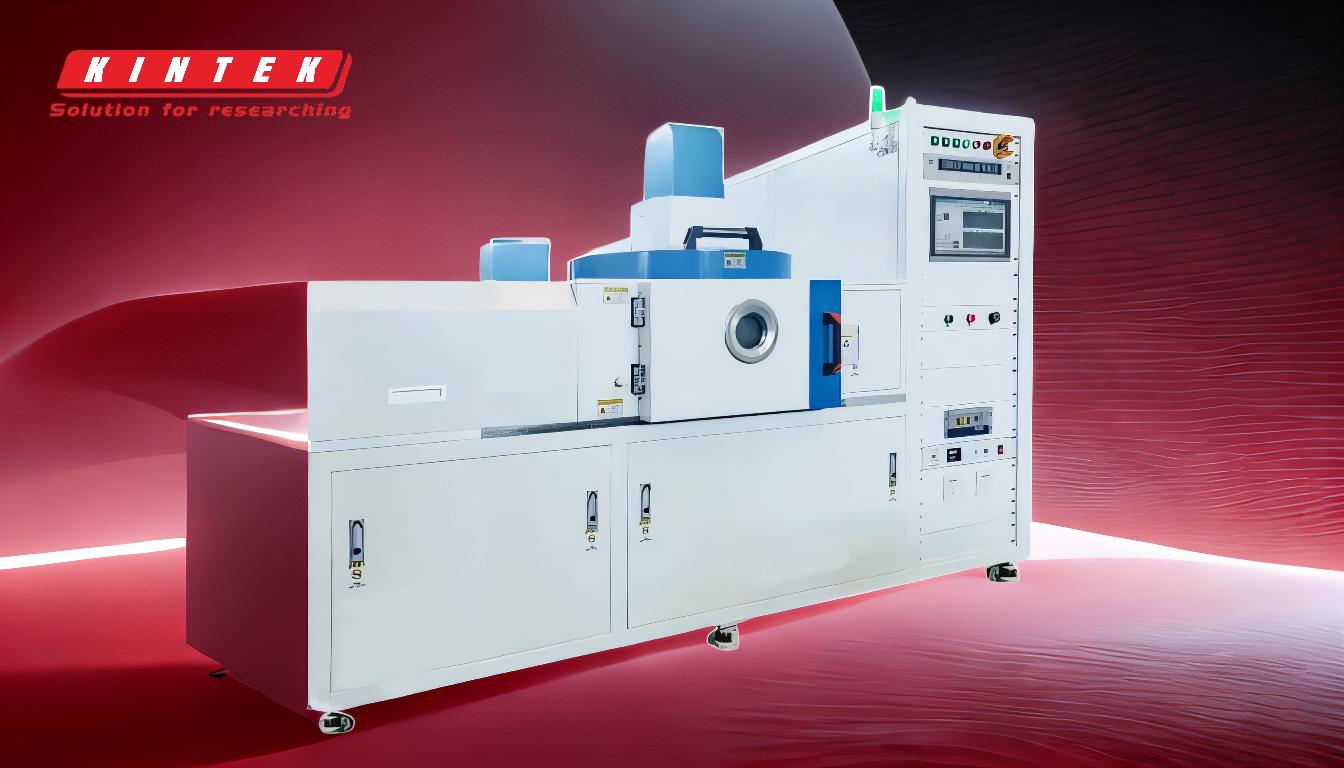
-
Chemische Abscheidungsmethoden:
- Galvanik:Bei diesem Verfahren wird eine dünne Schicht auf ein leitendes Substrat aufgebracht, indem ein elektrischer Strom durch eine Elektrolytlösung geleitet wird, die die gewünschten Metallionen enthält.Es wird üblicherweise für die Beschichtung von Metallen und Legierungen verwendet.
- Sol-Gel:Bei dieser Technik wird eine Lösung (Sol) in einen gelartigen Zustand überführt, der dann getrocknet und gesintert wird, um einen dünnen Film zu bilden.Es wird häufig zur Herstellung von Oxidschichten verwendet und ist bekannt für seine Fähigkeit, Schichten mit hoher Reinheit und Homogenität zu erzeugen.
- Tauchbeschichtung:Bei diesem Verfahren wird das Substrat in eine Lösung getaucht, die das Filmmaterial enthält, und dann mit einer kontrollierten Geschwindigkeit herausgezogen.Die Dicke des Films wird durch die Abzugsgeschwindigkeit und die Viskosität der Lösung bestimmt.Es wird üblicherweise für die gleichmäßige Beschichtung großer Flächen verwendet.
- Spin-Beschichtung:Bei dieser Technik wird ein Flüssigkeitsfilm auf ein Substrat aufgebracht und dann mit hoher Geschwindigkeit geschleudert, um die Flüssigkeit in einer dünnen, gleichmäßigen Schicht zu verteilen.Es wird in der Halbleiterindustrie häufig zum Aufbringen von Fotolackschichten verwendet.
- Chemische Gasphasenabscheidung (CVD):Beim CVD-Verfahren werden gasförmige Ausgangsstoffe auf einem erhitzten Substrat chemisch umgesetzt, um einen festen Dünnfilm zu bilden.Es dient der Abscheidung hochwertiger, gleichmäßiger Schichten und ist bei der Herstellung von Halbleitern und Beschichtungen weit verbreitet.
- Plasma-unterstütztes CVD (PECVD):Hierbei handelt es sich um eine Variante der CVD, bei der ein Plasma zur Verstärkung der chemischen Reaktion bei niedrigeren Temperaturen eingesetzt wird.Es ist besonders nützlich für die Abscheidung von Schichten auf temperaturempfindlichen Substraten.
- Atomlagenabscheidung (ALD):ALD ist ein präzises Verfahren, bei dem dünne Schichten durch abwechselnde Belichtung mit verschiedenen gasförmigen Vorläufersubstanzen Schicht für Schicht abgeschieden werden.Es bietet eine hervorragende Kontrolle über die Schichtdicke und die Gleichmäßigkeit der Schichten und ist daher ideal für Anwendungen, die extrem dünne und gleichmäßige Schichten erfordern.
-
Physikalische Abscheidungsmethoden:
- Sputtern:Bei dieser Technik wird ein Zielmaterial mit hochenergetischen Ionen beschossen, wodurch Atome herausgeschleudert werden und sich auf einem Substrat ablagern.Es wird häufig für die Abscheidung von Metallen, Legierungen und Verbundschichten verwendet.
- Thermische Verdampfung:Bei diesem Verfahren wird das abzuscheidende Material in einem Vakuum bis zu seinem Verdampfungspunkt erhitzt, und der Dampf kondensiert auf dem Substrat und bildet einen dünnen Film.Es wird üblicherweise für die Abscheidung von Metallen und einfachen Verbindungen verwendet.
- Elektronenstrahl-Verdampfung:Hierbei handelt es sich um eine Variante der thermischen Verdampfung, bei der ein Elektronenstrahl verwendet wird, um das Material bis zu seinem Verdampfungspunkt zu erhitzen.Es ermöglicht die Abscheidung hochreiner Schichten und wird für Materialien mit hohem Schmelzpunkt verwendet.
- Molekularstrahlepitaxie (MBE):MBE ist ein hochgradig kontrolliertes Verfahren, bei dem dünne Schichten durch die Ausrichtung molekularer oder atomarer Strahlen auf ein Substrat unter Ultrahochvakuumbedingungen abgeschieden werden.Es wird für die Herstellung hochwertiger kristalliner Schichten verwendet, insbesondere in der Halbleiterforschung.
- Gepulste Laserabscheidung (PLD):Beim PLD wird mit einem Hochleistungslaser Material von einem Ziel abgetragen, das sich dann auf einem Substrat ablagert.Es wird für die Abscheidung komplexer Oxidschichten und anderer Materialien verwendet, die sich mit anderen Methoden nur schwer abscheiden lassen.
-
Kombinierte Methoden:
- Thermisches Verdampfen und Sputtern:Bei einigen Anwendungen kann es erforderlich sein, sowohl das thermische Verdampfen als auch das Sputtern einzusetzen, um bestimmte Schichteigenschaften zu erzielen.Beispielsweise kann eine Kombination dieser Verfahren verwendet werden, um mehrschichtige Filme mit verschiedenen Materialien abzuscheiden.
-
Anwendungen und Überlegungen:
- Halbleiter:Verfahren wie CVD, PECVD und ALD werden in der Halbleiterindustrie häufig für die Abscheidung dünner Schichten aus Silizium, Siliziumdioxid und anderen Materialien verwendet.
- Flexible Elektronik:Techniken wie Spin-Coating und Dip-Coating werden zur Abscheidung von Polymerfilmen für flexible Solarzellen und OLEDs eingesetzt.
- Optische Beschichtungen:Sputtern und thermisches Aufdampfen werden üblicherweise für die Abscheidung dünner Schichten für optische Anwendungen wie Antireflexbeschichtungen und Spiegel verwendet.
- Barriereschichten:ALD und PECVD werden zur Abscheidung ultradünner Sperrschichten verwendet, um empfindliche Materialien vor Feuchtigkeit und Gasen zu schützen.
Zusammenfassend lässt sich sagen, dass die Wahl der Methode zum Aufbringen dünner Schichten von den spezifischen Anforderungen der Anwendung abhängt, einschließlich der gewünschten Schichteigenschaften, des Substratmaterials und des Produktionsmaßstabs.Jede Methode hat ihre Vorteile und Grenzen, und oft wird eine Kombination von Techniken eingesetzt, um die gewünschten Ergebnisse zu erzielen.
Zusammenfassende Tabelle:
Kategorie | Verfahren | Wichtigste Anwendungen |
---|---|---|
Chemische Abscheidung | Galvanische Beschichtung | Beschichtung von Metallen und Legierungen |
Sol-Gel | Oxidschichten, hohe Reinheit und Homogenität | |
Tauchbeschichtung | Gleichmäßige Beschichtung von großen Flächen | |
Spin-Beschichtung | Halbleiter-Fotoresist-Schichten | |
CVD | Hochwertige Halbleiterschichten | |
PECVD | Schichten auf temperaturempfindlichen Substraten | |
ALD | Ultradünne, konforme Beschichtungen | |
Physikalische Abscheidung | Sputtern | Metalle, Legierungen und Verbundschichten |
Thermische Verdampfung | Metalle und einfache Verbindungen | |
Elektronenstrahlverdampfung | Hochreine Filme, Materialien mit hohem Schmelzpunkt | |
MBE | Hochwertige kristalline Schichten für Halbleiter | |
PLD | Komplexe Oxidschichten und schwer abscheidbare Materialien | |
Kombinierte Verfahren | Thermisches Verdampfen + Sputtern | Mehrschichtige Filme mit verschiedenen Materialien |
Benötigen Sie Hilfe bei der Auswahl der richtigen Methode zum Aufbringen dünner Schichten? Kontaktieren Sie noch heute unsere Experten für maßgeschneiderte Lösungen!