Die physikalische Gasphasenabscheidung (PVD) ist eine Sammlung von vakuumbasierten Verfahren zur Abscheidung dünner Schichten auf Substraten.Bei diesen Verfahren wird ein festes oder flüssiges Material in eine Dampfphase umgewandelt, die dann auf einer Zieloberfläche kondensiert und eine dünne Schicht bildet.PVD-Verfahren sind in der Industrie weit verbreitet und erfordern präzise, hochwertige Beschichtungen für mechanische, optische, chemische oder elektronische Anwendungen.Zu den gebräuchlichsten PVD-Verfahren gehören Sputtern, thermisches Verdampfen, E-Beam-Verdampfung, gepulste Laserdeposition (PLD) und kathodische Lichtbogenabscheidung.Jede Technik hat ihre eigenen Mechanismen und Anwendungen, was PVD zu einem vielseitigen und wichtigen Verfahren in der modernen Fertigung und Materialwissenschaft macht.
Die wichtigsten Punkte erklärt:
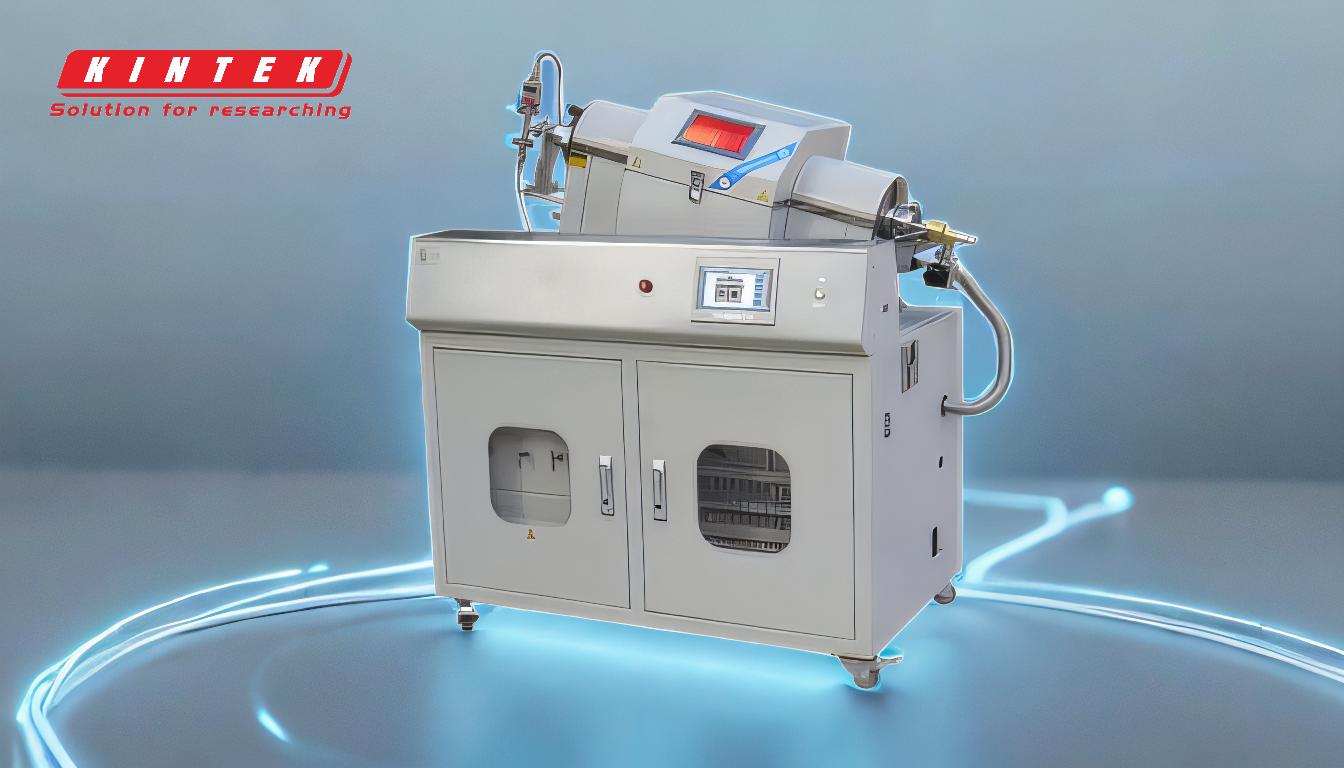
-
Überblick über PVD-Techniken:
- PVD ist eine Gruppe von Vakuumabscheidungsverfahren, bei denen ein Material von einer kondensierten Phase (fest oder flüssig) in eine Dampfphase und dann wieder in eine dünne Schicht auf einem Substrat übergeht.
- Mit diesen Verfahren werden dünne Schichten mit bestimmten mechanischen, optischen, chemischen oder elektronischen Eigenschaften hergestellt.
- PVD-Verfahren werden in einer Vakuumumgebung durchgeführt, um Verunreinigungen zu minimieren und eine genaue Kontrolle der Schichteigenschaften zu gewährleisten.
-
Gängige PVD-Techniken:
-
Sputtern:
- Beim Sputtern wird ein Zielmaterial mit hochenergetischen Ionen (in der Regel aus einem Plasma) beschossen, um Atome von der Oberfläche des Zielmaterials abzulösen.
- Die herausgeschleuderten Atome lagern sich dann auf einem Substrat ab und bilden einen dünnen Film.
- Diese Methode ist weit verbreitet, da sie eine Vielzahl von Materialien, darunter Metalle, Legierungen und Keramiken, mit hervorragender Haftung und Gleichmäßigkeit abscheiden kann.
-
Thermische Verdampfung:
- Bei der thermischen Verdampfung wird das Zielmaterial mit Hilfe von Widerstandsheizungen oder Elektronenstrahlen bis zu seinem Verdampfungspunkt erhitzt.
- Das verdampfte Material kondensiert dann auf dem Substrat und bildet einen dünnen Film.
- Diese Technik ist einfach und kostengünstig, aber in der Regel auf Materialien mit relativ niedrigem Schmelzpunkt beschränkt.
-
Elektronenstrahl (e-Beam) Verdampfung:
- Bei der e-Beam-Verdampfung wird ein fokussierter Elektronenstrahl verwendet, um das Zielmaterial zu erhitzen und zu verdampfen.
- Diese Methode eignet sich für Materialien mit hohem Schmelzpunkt und ermöglicht eine präzise Steuerung der Abscheidungsrate und der Schichtdicke.
-
Gepulste Laserabscheidung (PLD):
- Beim PLD wird ein Hochleistungslaserpuls verwendet, um Material von einem Ziel abzutragen, wodurch eine Dampffahne entsteht, die sich auf dem Substrat ablagert.
- Diese Technik eignet sich besonders für die Abscheidung komplexer Materialien, wie Oxide und Supraleiter, mit hoher stöchiometrischer Genauigkeit.
-
Kathodische Lichtbogenabscheidung:
- Bei diesem Verfahren wird ein elektrischer Lichtbogen verwendet, um Material von einem Kathoden-Target zu verdampfen.
- Das verdampfte Material bildet ein Plasma, das sich dann auf dem Substrat ablagert.
- Die kathodische Lichtbogenabscheidung ist für die Herstellung dichter, hochwertiger Beschichtungen bekannt, kann jedoch Makropartikel erzeugen, die die Filmqualität beeinträchtigen.
-
Sputtern:
-
Schlüsselkomponenten und Prozesse bei der PVD:
-
Vakuum Umwelt:
- PVD-Verfahren werden in Vakuumkammern durchgeführt, um Hintergrundgase zu reduzieren, die den Abscheidungsprozess stören könnten.
- Durch die Senkung des Drucks werden chemische Reaktionen zwischen dem verdampften Material und den Restgasen auf ein Minimum reduziert, was hochreine Schichten gewährleistet.
-
Materialverdampfung:
- Das Zielmaterial wird mit Methoden wie Erhitzen, Sputtern oder Laserablation verdampft.
- Die Wahl der Verdampfungsmethode hängt von den Materialeigenschaften und den gewünschten Schichtmerkmalen ab.
-
Filmabscheidung:
- Das verdampfte Material wird durch die Vakuum- oder Plasmaumgebung transportiert und kondensiert auf dem Substrat.
- Die Abscheiderate und die Schichtdicke werden mit Hilfe von Geräten wie Quarzkristall-Ratenmessern kontrolliert.
-
Vorbereitung des Substrats:
- Die Substrate werden häufig gereinigt und behandelt, um die Haftung und die Filmqualität zu verbessern.
- Zu den Oberflächenbehandlungen gehören die Plasmareinigung oder das Aufbringen von haftungsfördernden Schichten.
-
Vakuum Umwelt:
-
Anwendungen von PVD-Techniken:
-
Mechanische Beschichtungen:
- PVD wird verwendet, um verschleißfeste, harte Beschichtungen (z. B. Titannitrid) auf Werkzeuge, Formen und Maschinenteile aufzubringen.
-
Optische Beschichtungen:
- Dünne Schichten mit spezifischen optischen Eigenschaften, wie Antireflexions- oder Reflexionsschichten, werden auf Linsen, Spiegel und Displays aufgebracht.
-
Elektronische und Halbleiterbeschichtungen:
- PVD wird für die Abscheidung von leitenden, isolierenden oder halbleitenden Schichten in der Mikroelektronik und in Halbleitergeräten verwendet.
-
Dekorative Beschichtungen:
- PVD-Beschichtungen werden auf Konsumgüter (z. B. Uhren, Schmuck und Automobilverkleidungen) aufgebracht, um deren Aussehen und Haltbarkeit zu verbessern.
-
Mechanische Beschichtungen:
-
Vorteile von PVD:
- Hochwertige, dichte und haftende Filme.
- Genaue Kontrolle über die Zusammensetzung, Dicke und Eigenschaften der Schichten.
- Umweltfreundlich im Vergleich zu einigen chemischen Abscheidungsmethoden.
- Kompatibilität mit einer breiten Palette von Materialien und Substraten.
-
Herausforderungen und Überlegungen:
- Hohe Ausrüstungs- und Betriebskosten aufgrund der Vakuumanforderungen.
- Begrenzte Abscheidungsraten im Vergleich zu einigen Verfahren der chemischen Gasphasenabscheidung (CVD).
- Mögliche Defekte, wie Makropartikel bei der kathodischen Lichtbogenabscheidung oder ungleichmäßige Beschichtungen bei der thermischen Verdampfung.
Durch die Kenntnis dieser wichtigen Punkte können die Käufer von Anlagen und Verbrauchsmaterialien fundierte Entscheidungen über die Auswahl des geeigneten PVD-Verfahrens für ihre spezifische Anwendung treffen und so optimale Leistung und Kosteneffizienz gewährleisten.
Zusammenfassende Tabelle:
Aspekt | Einzelheiten |
---|---|
Gängige PVD-Techniken | Sputtern, thermische Verdampfung, e-Beam-Verdampfung, PLD, kathodischer Lichtbogen |
Wichtige Komponenten | Vakuumumgebung, Materialverdampfung, Schichtabscheidung, Substratvorbereitung |
Anwendungen | Mechanische, optische, elektronische und dekorative Beschichtungen |
Vorteile | Hochwertige Folien, präzise Kontrolle, umweltfreundlich, Materialverträglichkeit |
Herausforderungen | Hohe Kosten, begrenzte Abscheidungsraten, mögliche Defekte |
Entdecken Sie die richtige PVD-Lösung für Ihre Anforderungen. Kontaktieren Sie unsere Experten noch heute !