Die Bildung dünner Schichten ist ein wichtiger Prozess in der Materialwissenschaft und -technik, bei dem dünne Materialschichten auf ein Substrat aufgebracht werden.Dieser Prozess ist für die Veränderung von Oberflächeneigenschaften und die Erzielung gewünschter Merkmale wie Leitfähigkeit, Verschleißfestigkeit und Korrosionsschutz von wesentlicher Bedeutung.Die Schritte bei der Herstellung von Dünnschichten können je nach der verwendeten Abscheidungstechnik variieren, umfassen aber im Allgemeinen die Materialauswahl, die Vorbereitung des Substrats, die Abscheidung und die Nachbehandlung.Jeder Schritt ist entscheidend für die Qualität und Leistung der Dünnschicht.
Die wichtigsten Punkte erklärt:
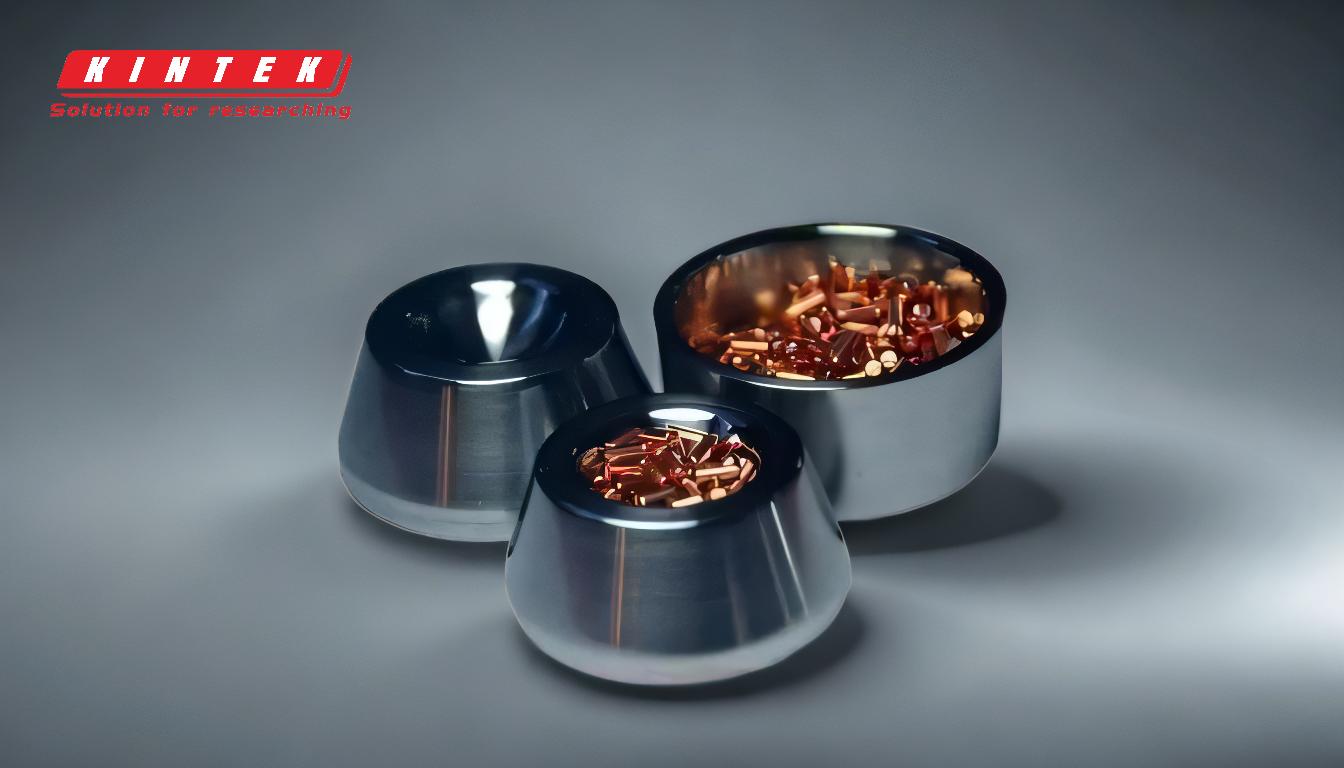
-
Materialauswahl:
- Zweck:Die Wahl des richtigen Materials ist von grundlegender Bedeutung, um die gewünschten Eigenschaften der Dünnschicht zu erreichen.
- Verfahren:Das Material, das oft als Target bezeichnet wird, muss rein und für die vorgesehene Anwendung geeignet sein.Die Auswahl hängt von den erforderlichen Eigenschaften wie Leitfähigkeit, Härte oder optischen Eigenschaften ab.
- Überlegungen:Faktoren wie die Materialverträglichkeit mit dem Substrat, die Abscheidungsmethode und die Anforderungen an die Endanwendung sind entscheidend.
-
Vorbereitung des Substrats:
- Zweck:Die Vorbereitung des Substrats gewährleistet eine gute Haftung und Gleichmäßigkeit des dünnen Films.
- Verfahren:Dabei wird das Substrat gereinigt, um Verunreinigungen zu entfernen, und manchmal wird die Oberfläche verändert, um die Haftung zu verbessern.Zu den Techniken gehören chemische Reinigung, mechanisches Polieren und Oberflächenaktivierung.
- Überlegungen:Die Oberflächenrauheit, die Sauberkeit und die chemische Zusammensetzung des Substrats können die Qualität der Schicht erheblich beeinflussen.
-
Abscheidung:
- Zweck:Der Kernschritt, bei dem die dünne Schicht auf dem Substrat gebildet wird.
-
Prozess:Es werden verschiedene Abscheidungstechniken verwendet, darunter:
- Thermische Verdampfung:Erhitzen des Targetmaterials, bis es verdampft und dann auf dem Substrat kondensiert.
- Sputtern:Beschuss des Targets mit Ionen, um Atome auszustoßen, die sich dann auf dem Substrat ablagern.
- Chemische Gasphasenabscheidung (CVD):Durch chemische Reaktionen wird eine Schicht auf dem Substrat erzeugt.
- Ionenstrahl-Beschichtung:Richten eines Ionenstrahls zur Abscheidung von Material auf dem Substrat.
- Überlegungen:Parameter wie Temperatur, Druck und Abscheidungsrate müssen sorgfältig kontrolliert werden, um die gewünschten Schichteigenschaften zu erreichen.
-
Behandlungen nach der Abscheidung:
- Zweck:Verbesserung der Eigenschaften und der Stabilität der Folie.
-
Prozess:Übliche Behandlungen sind:
- Glühen:Erhitzen der Folie zum Abbau von Spannungen und zur Verbesserung der Kristallinität.
- Wärmebehandlung:Veränderung der Mikrostruktur der Folie, um Eigenschaften wie Härte oder elektrische Leitfähigkeit zu verbessern.
- Überlegungen:Die Behandlungsbedingungen müssen optimiert werden, um eine Beschädigung der Folie oder des Substrats zu vermeiden.
-
Analyse und Qualitätskontrolle:
- Zweck:Sicherstellen, dass der Film die erforderlichen Spezifikationen erfüllt.
-
Prozess:Zur Bewertung der Folieneigenschaften, wie Dicke, Gleichmäßigkeit, Haftung und chemische Zusammensetzung, werden verschiedene Analyseverfahren eingesetzt.Zu den Techniken gehören:
- Ellipsometrie:Messung der Schichtdicke und der optischen Eigenschaften.
- Röntgenbeugung (XRD):Analyse der kristallographischen Struktur.
- Rasterelektronenmikroskopie (SEM):Untersuchung der Oberflächenmorphologie.
- Überlegungen:Kontinuierliche Überwachung und Feedback sind für die Prozessoptimierung und -konsistenz unerlässlich.
-
Prozess-Optimierung:
- Zweck:Verfeinerung des Abscheidungsprozesses zur Verbesserung der Filmqualität und -leistung.
- Verfahren:Auf der Grundlage der Analyseergebnisse werden Anpassungen an den Abscheidungsparametern, der Substratvorbereitung oder den Nachbehandlungen vorgenommen.
- Überlegungen:Iterative Tests und Verfeinerungen sind notwendig, um ein optimales Gleichgewicht zwischen Filmeigenschaften und Prozesseffizienz zu erreichen.
Wenn diese Schritte sorgfältig befolgt werden, können die Hersteller dünne Schichten mit präzisen Eigenschaften herstellen, die auf bestimmte Anwendungen zugeschnitten sind und eine hohe Leistung und Zuverlässigkeit in verschiedenen technischen und technologischen Bereichen gewährleisten.
Zusammenfassende Tabelle:
Schritt | Zweck | Wichtige Überlegungen |
---|---|---|
Auswahl des Materials | Wählen Sie das richtige Material für die gewünschten Eigenschaften (z. B. Leitfähigkeit, Härte). | Materialverträglichkeit, Abscheidungsmethode und Anwendungsanforderungen. |
Vorbereitung des Substrats | Sicherstellen, dass der dünne Film gut haftet und gleichmäßig ist. | Oberflächenrauhigkeit, Sauberkeit und chemische Zusammensetzung des Substrats. |
Abscheidung | Bilden Sie die dünne Schicht auf dem Substrat mit Techniken wie Sputtern oder CVD. | Steuerung von Temperatur, Druck und Abscheidungsrate für optimale Schichteigenschaften. |
Behandlungen nach der Abscheidung | Verbessern Sie die Filmeigenschaften und die Stabilität durch Glühen oder Wärmebehandlung. | Optimieren Sie die Behandlungsbedingungen, um eine Beschädigung der Folie oder des Substrats zu vermeiden. |
Analyse und Qualitätskontrolle | Stellen Sie sicher, dass die Folie den erforderlichen Spezifikationen entspricht. | Verwenden Sie Techniken wie Ellipsometrie, XRD und SEM für Dicke, Gleichmäßigkeit und Haftung. |
Prozess-Optimierung | Verfeinerung des Prozesses zur Verbesserung der Folienqualität und -leistung. | Iterative Tests und Anpassungen auf der Grundlage der Analyseergebnisse. |
Sind Sie bereit, Ihren Dünnschichtbildungsprozess zu optimieren? Kontaktieren Sie noch heute unsere Experten für maßgeschneiderte Lösungen!