Das Sputtering-Verfahren ist eine weit verbreitete Technik der physikalischen Gasphasenabscheidung (PVD) zur Abscheidung dünner Schichten von Materialien auf Substraten.Dabei wird ein Vakuum erzeugt, ein Inertgas eingeleitet, das Gas zur Bildung eines Plasmas ionisiert und das Plasma zum Ausstoßen von Atomen aus einem Zielmaterial verwendet, die sich dann auf einem Substrat abscheiden.Das Verfahren ist hochgradig kontrolliert und gewährleistet die Abscheidung hochreiner, gleichmäßiger Schichten.Nachfolgend werden die einzelnen Schritte des Sputtering-Prozesses im Detail erläutert.
Die wichtigsten Punkte werden erklärt:
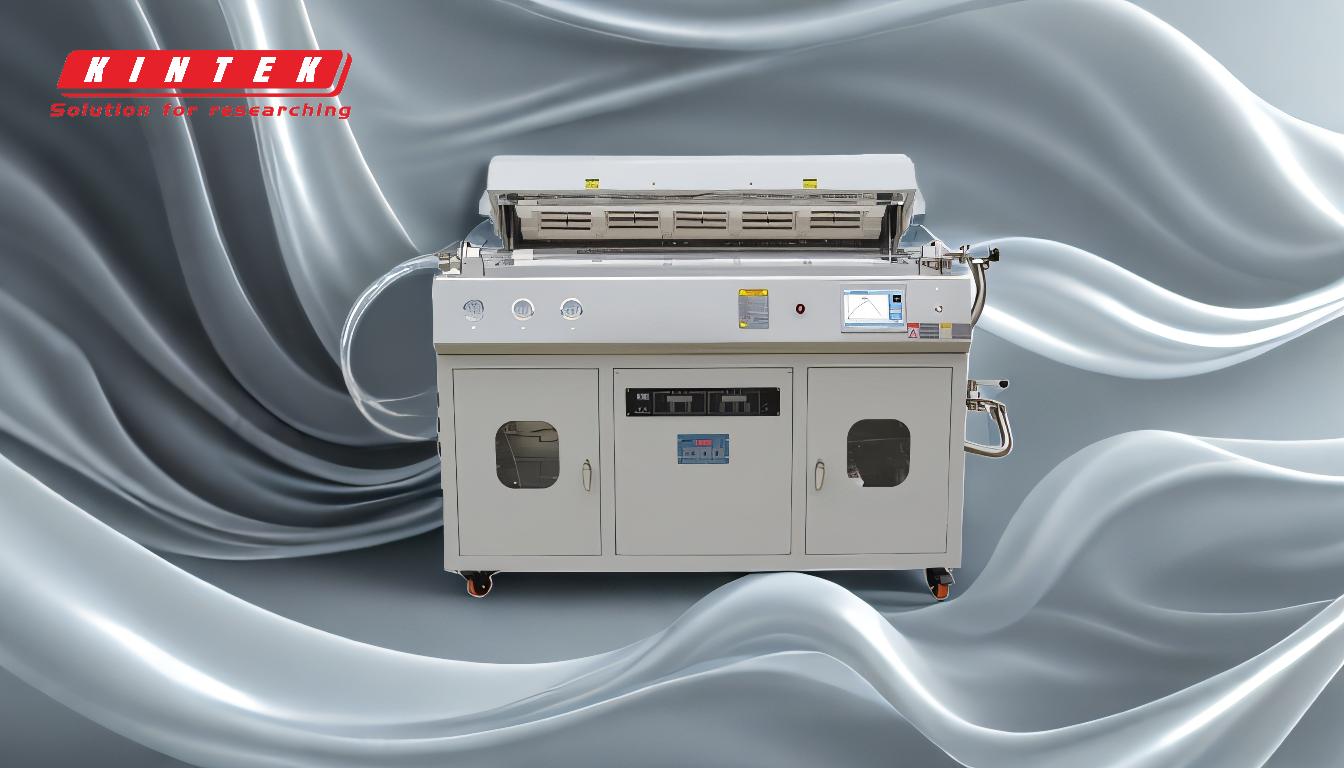
-
Erzeugen eines Vakuums in der Reaktionskammer
- Der erste Schritt besteht darin, die Reaktionskammer zu evakuieren, um Feuchtigkeit, Verunreinigungen und Restgase zu entfernen.
- Der Druck wird in der Regel auf etwa 1 Pa (0,0000145 psi) reduziert, um eine saubere Umgebung für den Prozess zu schaffen.
- Ein Vakuum stellt sicher, dass Verunreinigungen die Abscheidung nicht beeinträchtigen, was für die Erzielung hochwertiger Beschichtungen entscheidend ist.
-
Einleiten eines Inertgases
- Sobald ein Vakuum hergestellt ist, wird ein Inertgas (normalerweise Argon) in die Kammer eingeleitet.
- Das Gas wird gewählt, weil es chemisch inert ist und unerwünschte Reaktionen während des Prozesses minimiert.
- Der Druck des Gases wird so eingestellt, dass eine Niederdruckatmosphäre entsteht, in der Regel im Bereich von 10-¹ bis 10-³ mbar, was für die Plasmabildung ideal ist.
-
Aufheizen der Kammer
- Die Kammer wird auf Temperaturen von 150°C bis 750°C (302°F bis 1382°F) aufgeheizt, je nach dem zu beschichtenden Material.
- Die Erwärmung sorgt für eine gute Haftung der Beschichtung auf dem Substrat und kann auch die Mikrostruktur und die Eigenschaften der abgeschiedenen Schicht beeinflussen.
-
Erzeugung eines Plasmas
- Eine Hochspannung (3-5 kV) wird angelegt, um das Argongas zu ionisieren und ein Plasma zu erzeugen.
- Das Plasma besteht aus positiv geladenen Argon-Ionen (Ar⁺) und freien Elektronen.
- Häufig wird ein Magnetfeld verwendet, um das Plasma zu begrenzen und zu kontrollieren und so die Effizienz des Ionisierungsprozesses zu erhöhen.
-
Beschleunigung der Ionen in Richtung des Targets
- Die positiv geladenen Ar⁺-Ionen werden auf das Zielmaterial (die Quelle des Beschichtungsmaterials) beschleunigt.
- Das Target ist negativ geladen und erzeugt ein elektrisches Feld, das die Ionen anzieht.
- Wenn die Ionen mit dem Target zusammenstoßen, übertragen sie ihre Energie, so dass die Atome von der Oberfläche des Targets ausgestoßen werden.
-
Transport der gesputterten Atome zum Substrat
- Die ausgestoßenen Atome werden durch die Niederdruckumgebung zum Substrat transportiert.
- Der verringerte Druck minimiert die Kollisionen zwischen den Atomen und gewährleistet einen gerichteten Materialfluss.
- Dieser Schritt ist entscheidend, um eine gleichmäßige Abscheidung auf dem Substrat zu erreichen.
-
Abscheidung des Dünnfilms
- Die gesputterten Atome kondensieren auf der Oberfläche des Substrats und bilden einen dünnen Film.
- Die Energie der abgeschiedenen Atome kann die Oberflächenmobilität erhöhen, was zu einer besseren Haftung und Schichtqualität führt.
- Der Prozess wird so lange fortgesetzt, bis die gewünschte Dicke der Beschichtung erreicht ist.
-
Kontrolle der Prozessparameter
- Während des gesamten Prozesses werden Parameter wie Druck, Temperatur, Spannung und Magnetfeldstärke sorgfältig kontrolliert.
- Diese Parameter beeinflussen die Abscheiderate, die Qualität des Films und die Eigenschaften der fertigen Beschichtung.
- Es können Anpassungen vorgenommen werden, um das Verfahren für bestimmte Materialien und Anwendungen zu optimieren.
Das Sputtern ist ein präzises und vielseitiges Verfahren zum Aufbringen dünner Schichten auf Substrate.Durch die sorgfältige Kontrolle jedes einzelnen Schritts, von der Erzeugung eines Vakuums bis zur Abscheidung der Beschichtung, können Hersteller hochwertige, gleichmäßige Schichten mit hervorragender Haftung und Reinheit erzielen.Dies macht das Sputtern zu einer bevorzugten Technik in Branchen wie Elektronik, Optik und Luft- und Raumfahrt, wo Präzision und Leistung entscheidend sind.
Zusammenfassende Tabelle:
Schritt | Wichtige Details |
---|---|
1.Erzeugen eines Vakuums | Evakuieren Sie die Kammer auf ~1 Pa, um Verunreinigungen zu entfernen. |
2.Einleiten von Inertgas | Argongas bei 10-¹ bis 10-³ mbar zur Plasmabildung zugeben. |
3.Erhitzen der Kammer | Erhitzen auf 150°C-750°C, um die Haftung und die Filmeigenschaften zu verbessern. |
4.Erzeugung eines Plasmas | 3-5 kV anlegen, um Argon zu ionisieren und ein Plasma zu erzeugen. |
5.Beschleunigung von Ionen | Positiv geladene Ar⁺-Ionen stoßen mit dem negativ geladenen Ziel zusammen. |
6.Transport von Atomen | Die gesputterten Atome fließen in einer Niederdruckumgebung zum Substrat. |
7.Abscheidung von Dünnschichten | Die Atome kondensieren auf dem Substrat und bilden eine gleichmäßige, hochwertige Schicht. |
8.Steuerung der Parameter | Passen Sie Druck, Temperatur, Spannung und Magnetfeld für optimale Ergebnisse an. |
Benötigen Sie hochwertige Lösungen für die Dünnschichtabscheidung? Kontaktieren Sie noch heute unsere Experten um mehr zu erfahren!