Der Sinterprozess wird von einer Vielzahl von Variablen beeinflusst, die die Qualität, Dichte und mechanischen Eigenschaften des Endprodukts bestimmen.Zu den Schlüsselvariablen gehören Temperatur, Heizrate, Druck, Partikelgröße, Zusammensetzung, Atmosphäre, Abkühlrate und prozessspezifische Parameter wie Schichtdicke und Maschinengeschwindigkeit.Jede Variable spielt eine entscheidende Rolle für die Sinterkinetik, die Verdichtung und die Beseitigung von Porosität.Das Verständnis und die Optimierung dieser Variablen sind entscheidend für das Erreichen der gewünschten Materialeigenschaften und die Effizienz des Sinterprozesses.
Die wichtigsten Punkte werden erklärt:
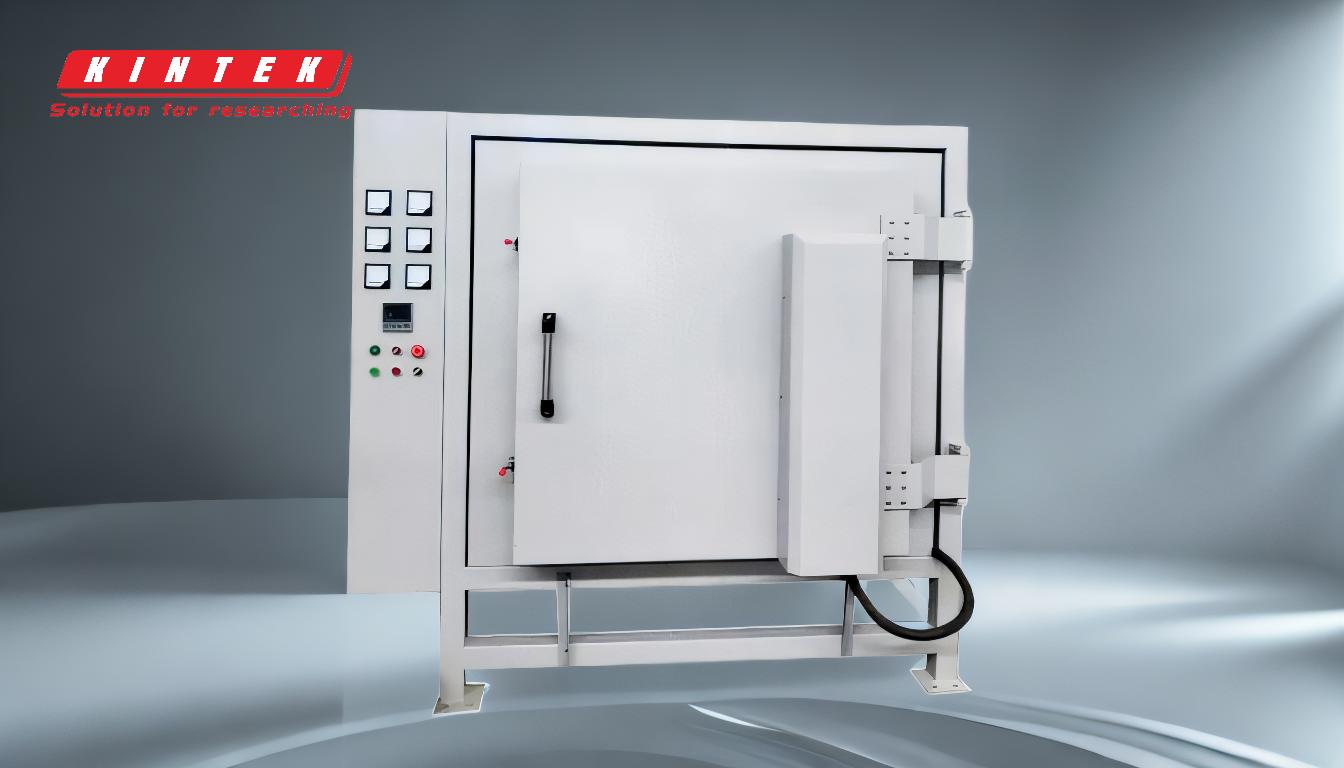
-
Temperatur:
- Rolle:Die Temperatur ist eine entscheidende Variable, die die Sinterkinetik und die endgültigen Materialeigenschaften bestimmt.Sie beeinflusst die Diffusionsgeschwindigkeit und die Bildung von Bindungen zwischen den Partikeln.
- Aufschlag:Höhere Temperaturen erhöhen im Allgemeinen die Verdichtungsrate und verbessern die mechanischen Eigenschaften wie Zugfestigkeit und Kerbschlagarbeit.Übermäßig hohe Temperaturen können jedoch zu unerwünschtem Kornwachstum oder Schmelzen führen.
- Optimierung:Die Sintertemperatur muss in Abhängigkeit von der Materialzusammensetzung und den gewünschten Eigenschaften sorgfältig kontrolliert werden.
-
Aufheizrate:
- Rolle:Die Heizrate beeinflusst den Verdichtungsprozess, indem sie die für die Umlagerung der Partikel und die Bildung von Bindungen verfügbare Zeit steuert.
- Aufprall:Eine langsamere Heizrate ermöglicht eine gleichmäßigere Verdichtung, während eine schnellere Rate zu ungleichmäßiger Sinterung und Restporosität führen kann.
- Optimierung:Die Aufheizrate sollte so eingestellt werden, dass ein Gleichgewicht zwischen Verdichtungseffizienz und Gleichmäßigkeit besteht.
-
Druck:
- Rolle:Angewandter Druck fördert die Umlagerung der Partikel und trägt zur Beseitigung von Porosität bei, indem er die Partikel in engeren Kontakt zwingt.
- Aufprall:Ein höherer Druck kann die Verdichtung deutlich verbessern und die Sinterzeit verkürzen.Ein zu hoher Druck kann jedoch Verformungen oder Risse verursachen.
- Optimierung:Der angewandte Druck muss auf das Material und die Sinterbedingungen abgestimmt sein, um optimale Ergebnisse zu erzielen.
-
Partikelgröße:
- Rolle:Die Partikelgröße beeinflusst das Sinterverhalten, wobei kleinere Partikel aufgrund ihrer größeren Oberfläche und Energie eine schnellere Verdichtung fördern.
- Aufprall:Feinere Pulver führen im Allgemeinen zu einer besseren Verdichtung und besseren mechanischen Eigenschaften.Sehr feine Partikel können jedoch agglomerieren, was zu einer ungleichmäßigen Sinterung führt.
- Optimierung:Die Partikelgrößenverteilung sollte kontrolliert werden, um eine gleichmäßige Sinterung zu gewährleisten und Agglomeration zu vermeiden.
-
Zusammensetzung:
- Rolle:Die chemische Zusammensetzung des Materials beeinflusst das Sinterverhalten, einschließlich der Bildung von flüssigen Phasen und der Stabilität der festen Phase.
- Aufprall:Homogene Zusammensetzungen fördern eine bessere Verdichtung und gleichmäßigere Materialeigenschaften.Verunreinigungen oder Inhomogenitäten können zu Defekten oder ungleichmäßiger Sinterung führen.
- Optimierung:Die Zusammensetzung sollte sorgfältig ausgewählt und kontrolliert werden, um die gewünschten Sinterergebnisse zu erzielen.
-
Atmosphäre:
- Rolle:Die Sinteratmosphäre (z. B. Luft, Vakuum, Argon, Stickstoff) beeinflusst Oxidation, Reduktion und andere chemische Reaktionen während des Sinterns.
- Aufprall:Inerte oder reduzierende Atmosphären können Oxidation verhindern und die Sinterqualität verbessern, während reaktive Atmosphären unerwünschte chemische Veränderungen hervorrufen können.
- Optimierung:Die Wahl der Atmosphäre hängt vom Material und den gewünschten Eigenschaften des Endprodukts ab.
-
Abkühlungsrate:
- Rolle:Die Abkühlungsgeschwindigkeit beeinflusst das Gefüge und die mechanischen Eigenschaften des gesinterten Materials.
- Aufprall:Eine kontrollierte Abkühlung kann thermische Spannungen verhindern und die Materialeigenschaften verbessern, während eine schnelle Abkühlung zu Rissen oder Eigenspannungen führen kann.
- Optimierung:Die Abkühlungsgeschwindigkeit sollte je nach Material und Sinterbedingungen angepasst werden, um das gewünschte Gefüge zu erreichen.
-
Prozessspezifische Parameter:
-
Schichtdicke:
- Rolle:Die Dicke der Sinterschicht beeinflusst die Wärmeverteilung und Verdichtung.
- Aufprall:Dickere Schichten können zu einer ungleichmäßigen Sinterung führen, während dünnere Schichten eine gleichmäßigere Erwärmung ermöglichen.
- Optimierung:Die Schichtdicke sollte kontrolliert werden, um eine gleichmäßige Sinterung zu gewährleisten und Fehler zu vermeiden.
-
Geschwindigkeit der Maschine:
- Rolle:Die Geschwindigkeit der Sintermaschine bestimmt die Verweilzeit des Materials in der Sinterzone.
- Aufprall:Schnellere Geschwindigkeiten verkürzen zwar die Sinterzeit, können aber zu einer unvollständigen Verdichtung führen, während langsamere Geschwindigkeiten eine vollständige Sinterung gewährleisten.
- Optimierung:Die Maschinengeschwindigkeit sollte so angepasst werden, dass Effizienz und Sinterqualität im Gleichgewicht sind.
-
Luftmenge und Vakuum:
- Rolle:Luftmenge und Vakuumpegel beeinflussen den Wärmeübergang und den Gasfluss während des Sinterns.
- Aufschlag:Die richtige Steuerung der Luftmenge und des Vakuums gewährleistet eine effiziente Wärmeverteilung und Gasabfuhr, was zu besseren Sinterergebnissen führt.
- Optimierung:Diese Parameter sollten auf der Grundlage der Sinteranlage und der Materialanforderungen angepasst werden.
-
Schichtdicke:
Durch eine sorgfältige Kontrolle und Optimierung dieser Variablen können die Hersteller hochwertige Sinterprodukte mit den gewünschten mechanischen Eigenschaften und mikrostrukturellen Merkmalen erzielen.
Zusammenfassende Tabelle:
Variable | Rolle | Auswirkungen | Optimierung |
---|---|---|---|
Temperatur | Bestimmt die Sinterkinetik und die Materialeigenschaften. | Höhere Temperaturen verbessern die Verdichtung; übermäßige Hitze verursacht Kornwachstum. | Steuerung je nach Material und gewünschten Eigenschaften. |
Aufheizrate | Beeinflusst die Verdichtung und Gleichmäßigkeit. | Langsame Geschwindigkeiten gewährleisten eine gleichmäßige Sinterung; schnelle Geschwindigkeiten können Porosität verursachen. | Gleichgewicht zwischen Verdichtungseffizienz und Gleichmäßigkeit. |
Druck | Verbessert die Umlagerung der Partikel und beseitigt die Porosität. | Höherer Druck verbessert die Verdichtung; zu hoher Druck verursacht Risse. | Auf das Material und die Sinterbedingungen abstimmen. |
Partikelgröße | Beeinflusst das Sinterverhalten; kleinere Partikel verdichten sich schneller. | Feinere Pulver verbessern die Verdichtung; Agglomeration kann zu Ungleichmäßigkeiten führen. | Kontrollieren Sie die Partikelgrößenverteilung für eine gleichmäßige Sinterung. |
Zusammensetzung | Beeinflusst das Sinterverhalten und die Materialstabilität. | Homogene Zusammensetzungen fördern eine bessere Verdichtung und bessere Eigenschaften. | Wählen und kontrollieren Sie die Zusammensetzung sorgfältig. |
Atmosphäre | Beeinflusst Oxidation, Reduktion und chemische Reaktionen. | Inerte Atmosphären verhindern Oxidation; reaktive Atmosphären können die Eigenschaften verändern. | Wählen Sie die Atmosphäre entsprechend dem Material und den gewünschten Ergebnissen. |
Abkühlungsrate | Beeinflusst das Mikrogefüge und die mechanischen Eigenschaften. | Kontrolliertes Abkühlen verhindert Spannungen; schnelles Abkühlen kann zu Rissen führen. | Stellen Sie die Abkühlungsgeschwindigkeit je nach Material und Sinterbedingungen ein. |
Schichtdicke | Beeinflusst die Wärmeverteilung und Verdichtung. | Dickere Schichten können zu ungleichmäßiger Sinterung führen; dünnere Schichten gewährleisten Gleichmäßigkeit. | Optimieren Sie die Schichtdicke für eine gleichmäßige Sinterung. |
Maschinengeschwindigkeit | Bestimmt die Verweilzeit in der Sinterzone. | Schnellere Geschwindigkeiten verkürzen die Zeit, können aber eine unvollständige Verdichtung verursachen. | Wählen Sie die richtige Geschwindigkeit für Effizienz und Qualität. |
Luftvolumen/Vakuum | Beeinflusst die Wärmeübertragung und den Gasfluss. | Eine korrekte Steuerung gewährleistet eine effiziente Wärmeverteilung und Gasabfuhr. | Passen Sie die Regelung an die Sinterbedingungen und Materialanforderungen an. |
Optimieren Sie Ihren Sinterprozess noch heute - Kontaktieren Sie unsere Experten für maßgeschneiderte Lösungen!