Das Sputtern, ein modernes Vakuumbeschichtungsverfahren, bietet mehrere Vorteile gegenüber älteren Methoden wie der thermischen Verdampfung oder der E-Beam-Verdampfung.Zu den wichtigsten Vorteilen gehören die Möglichkeit, eine breite Palette von Materialien abzuscheiden (einschließlich solcher mit hohen Schmelzpunkten), die genaue Kontrolle über die Zusammensetzung und die Eigenschaften der Schichten, eine bessere Haftung aufgrund der höheren kinetischen Energie der gesputterten Atome und die Kompatibilität mit reaktiven Gasen für fortschrittliche Verfahren.Außerdem ist das Sputtern reproduzierbarer, leichter zu automatisieren und für Ultrahochvakuumanwendungen geeignet.Außerdem ermöglicht es Präzision auf molekularer Ebene, so dass selbst bei niedrigen Temperaturen makellose Grenzflächen und gleichmäßige Schichten mit hoher Packungsdichte erzeugt werden können.
Die wichtigsten Punkte werden erklärt:
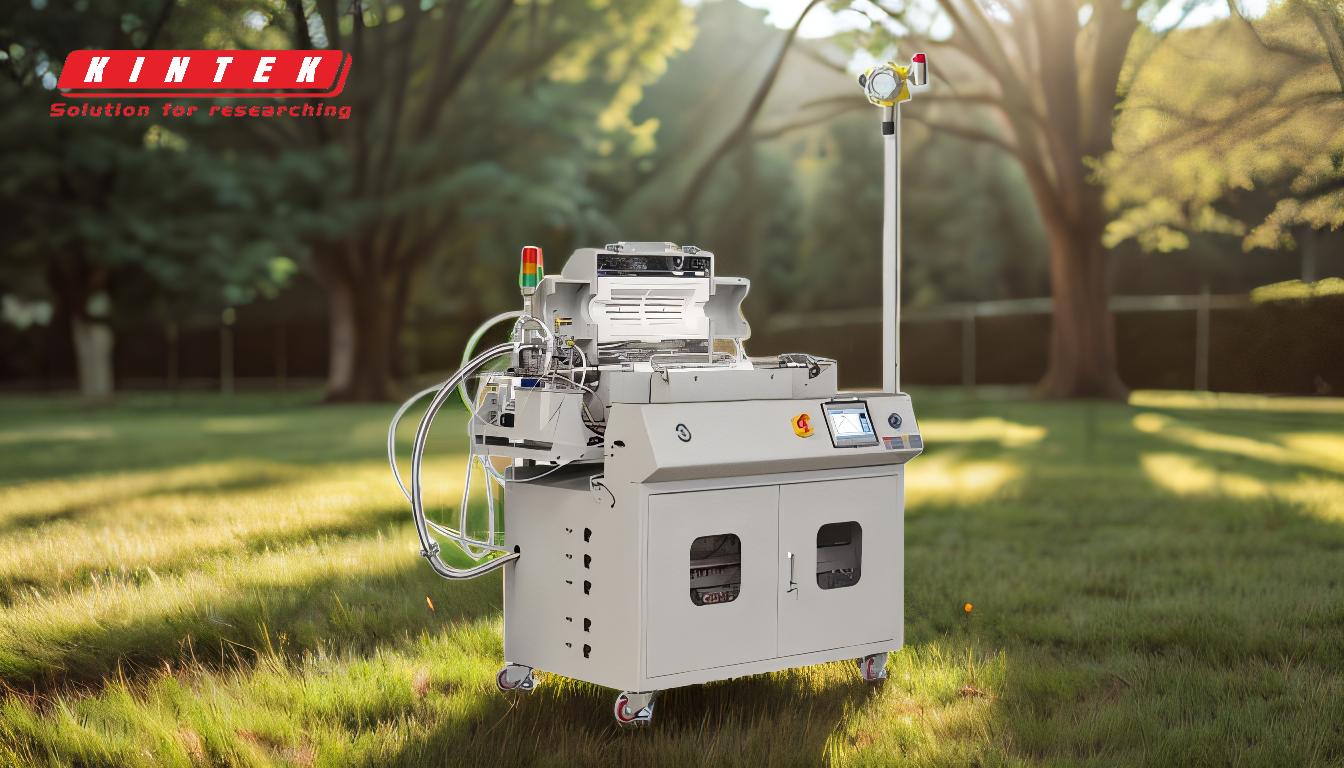
-
Ablagerung einer breiten Palette von Materialien:
- Durch Sputtern können Materialien mit sehr hohen Schmelzpunkten abgeschieden werden, die mit älteren Methoden wie der thermischen Verdampfung nur schwer oder gar nicht verdampft werden können.
- Es eignet sich für eine Vielzahl von Materialien, darunter Metalle, Legierungen, Verbundwerkstoffe, Kunststoffe, organische Stoffe und Glas, und ist damit vielseitiger als herkömmliche Vakuumbeschichtungsverfahren.
-
Bessere Haftung und Filmqualität:
- Durch Sputtern ausgestoßene Atome haben im Vergleich zu aufgedampften Materialien eine wesentlich höhere kinetische Energie, was zu einer besseren Haftung auf Substraten führt.
- Die durch Sputtern hergestellten Schichten sind gleichmäßiger, haben eine höhere Packungsdichte und weisen eine bessere Oberflächenhaftung auf, selbst bei niedrigen Temperaturen.
-
Präzision und Kontrolle:
- Das Sputtern bietet Präzision auf molekularer Ebene und ermöglicht die Schaffung von makellosen Grenzflächen zwischen Materialien.
- Die Filmeigenschaften können durch die Steuerung von Prozessparametern, wie Gaszusammensetzung, Druck und Leistung, genau eingestellt werden.
-
Reproduzierbarkeit und Automatisierung:
- Die Sputterdeposition ist im Vergleich zu älteren Verfahren wie E-Beam oder thermischer Verdampfung äußerst reproduzierbar und leichter zu automatisieren.
- Das Sputtertarget stellt eine stabile, langlebige Verdampfungsquelle dar, die gleichbleibende Ergebnisse über einen längeren Zeitraum gewährleistet.
-
Reaktive Abscheidung und fortgeschrittene Prozesse:
- Die reaktive Abscheidung ist mit Hilfe reaktiver Gase, die in einem Plasma aktiviert werden, leicht zu bewerkstelligen und ermöglicht die Bildung von Oxid- oder Nitridschichten mit der gewünschten Zusammensetzung.
- Das Sputtern ist mit fortschrittlichen Verfahren wie dem Epitaxiewachstum kompatibel und kann unter Ultrahochvakuumbedingungen durchgeführt werden.
-
Kosteneffizienz und Wartung:
- Die Sputterdeposition ist im Vergleich zu anderen Depositionsverfahren relativ kostengünstig.
- Das Verfahren ist wartungsfrei, was die Betriebskosten und Ausfallzeiten reduziert.
-
Kompakter und flexibler Aufbau:
- Die Sputterbeschichtungskammer kann ein kleines Volumen haben, und die Quelle und das Substrat können nahe beieinander liegen, wodurch die Strahlungswärme minimiert und der Aufbau vereinfacht wird.
- Die Form des Sputtertargets (z. B. Linie, Stab oder Zylinder) kann an die jeweilige Anwendung angepasst werden.
-
Breite Materialkompatibilität:
- Im Vergleich zu Verfahren wie der thermischen Verdampfung eignet sich das Sputtern für ein breiteres Spektrum von Materialien, einschließlich Mischungen und Legierungen.
- Es eignet sich für die Abscheidung optischer Schichten durch Oxidation oder Nitrierung der gesputterten Metallionen, um die gewünschte Schichtzusammensetzung zu erreichen.
Durch die Nutzung dieser Vorteile ist das Sputtern zu einer bevorzugten Methode für die moderne Vakuumabscheidung geworden, die im Vergleich zu älteren Verfahren eine höhere Leistung, Flexibilität und Kosteneffizienz bietet.
Zusammenfassende Tabelle:
Vorteil | Beschreibung |
---|---|
Breite Palette von Materialien | Beschichtet Materialien mit hohem Schmelzpunkt, Metalle, Legierungen, Verbindungen und mehr. |
Bessere Haftung und Filmqualität | Höhere kinetische Energie sorgt für gleichmäßige Filme mit hervorragender Haftung. |
Präzision und Kontrolle | Präzision auf molekularer Ebene für makellose Grenzflächen und einstellbare Filmeigenschaften. |
Reproduzierbarkeit und Automatisierung | Hochgradig reproduzierbar, leicht zu automatisieren und zeitlich konstant. |
Reaktive Abscheidung | Kompatibel mit reaktiven Gasen für Oxid-/Nitridschichten und fortschrittliche Verfahren. |
Kosteneffizienz | Relativ kostengünstig und wartungsfrei. |
Kompakte und flexible Einrichtung | Kleine Kammergröße, minimale Strahlungswärme und anpassbare Zielformen. |
Breite Materialkompatibilität | Funktioniert mit Mischungen, Legierungen und optischen Filmen für verschiedene Anwendungen. |
Sind Sie bereit, Ihren Abscheidungsprozess zu verbessern? Kontaktieren Sie uns noch heute um mehr über Sputtering-Lösungen zu erfahren!