Physikalische Gasphasenabscheidung (PVD) und chemische Gasphasenabscheidung (CVD) sind zwei weit verbreitete Verfahren zur Abscheidung dünner Schichten auf Substraten.PVD beruht auf physikalischen Verfahren wie Verdampfung oder Sputtern, um ein festes Material in einen Dampf zu verwandeln, der dann auf dem Substrat kondensiert.Im Gegensatz dazu nutzt CVD chemische Reaktionen mit gasförmigen Ausgangsstoffen, um einen festen Film auf dem Substrat zu bilden.Während PVD bei niedrigeren Temperaturen arbeitet und korrosive Nebenprodukte vermeidet, ermöglicht CVD eine gleichmäßige Beschichtung komplexer Geometrien und höhere Abscheideraten.Beide Verfahren sind in Branchen wie der Halbleiter-, Optik- und Beschichtungsindustrie unverzichtbar und bieten je nach Anwendung einzigartige Vorteile.
Die wichtigsten Punkte werden erklärt:
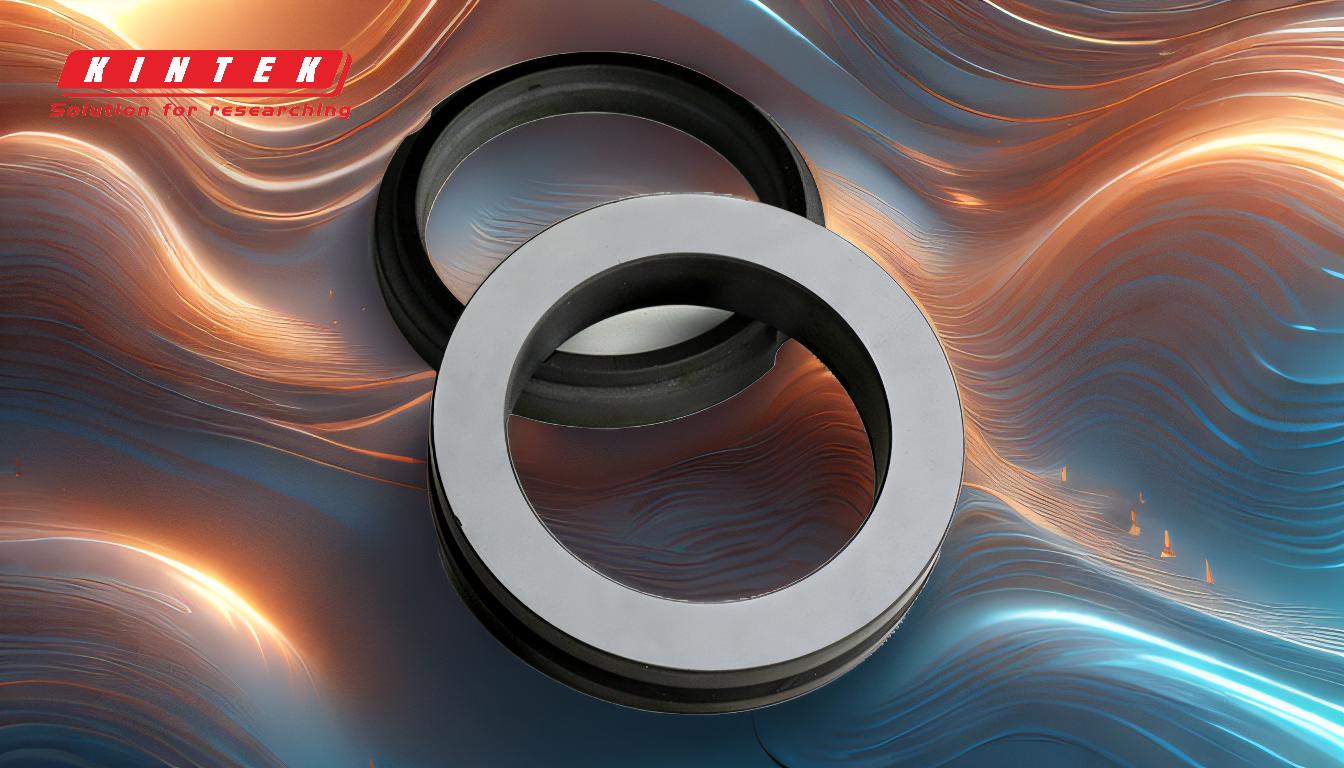
-
Definition und Grundprinzipien:
- PVD:Bei der physikalischen Gasphasenabscheidung wird ein festes Material durch physikalische Mittel (z. B. Erhitzen, Sputtern) in Dampf verwandelt.Der Dampf kondensiert dann auf dem Substrat und bildet eine dünne Schicht.
- CVD:Bei der chemischen Gasphasenabscheidung werden gasförmige Ausgangsstoffe verwendet, die auf der Substratoberfläche chemisch reagieren oder sich zersetzen, um einen festen Film zu bilden.Dieses Verfahren beruht auf chemischen Reaktionen und nicht auf physikalischen Umwandlungen.
-
Prozessmechanismen:
-
PVD:
- Das feste Material wird über seinen Schmelzpunkt erhitzt oder mit Ionen beschossen (Sputtern), um Dampf zu erzeugen.
- Die verdampften Atome oder Moleküle gelangen auf das Substrat und scheiden sich als dünner Film ab.
- Zu den gängigen PVD-Verfahren gehören Verdampfen, Sputtern, Elektronenstrahlen und Drahtexplosion.
-
CVD:
- Gasförmige Ausgangsstoffe werden in eine Reaktionskammer eingeleitet.
- Die Gase reagieren chemisch oder zersetzen sich auf der erhitzten Substratoberfläche und bilden einen festen Film.
- CVD kann thermisch aktiviert oder plasmaunterstützt werden, um die Reaktionseffizienz zu verbessern.
-
PVD:
-
Hauptunterschiede:
-
Material Zustand:
- PVD verwendet feste Materialien, die physikalisch verdampft werden.
- Bei CVD werden gasförmige Ausgangsstoffe verwendet, die sich chemisch in einen festen Film verwandeln.
-
Sichtlinie:
- PVD erfordert eine direkte Sichtlinie zwischen dem Zielmaterial und dem Substrat, was die Fähigkeit, komplexe Geometrien gleichmäßig zu beschichten, einschränkt.
- CVD erfordert keine Sichtlinie und ermöglicht die gleichmäßige Beschichtung komplizierter Formen und mehrerer Teile gleichzeitig.
-
Temperatur und Nebenprodukte:
- PVD arbeitet bei niedrigeren Temperaturen und erzeugt keine korrosiven Nebenprodukte.
- CVD erfordert oft hohe Temperaturen, was zu korrosiven gasförmigen Nebenprodukten und möglichen Verunreinigungen in der Schicht führen kann.
-
Material Zustand:
-
Vorteile und Beschränkungen:
-
PVD:
- Vorteile:Niedrigere Abscheidetemperaturen, keine korrosiven Nebenprodukte, hohe Materialausnutzung (z. B. bietet EBPVD hohe Abscheideraten).
- Beschränkungen:Begrenzt auf Sichtkontakt, geringere Ablagerungsraten im Vergleich zu CVD.
-
CVD:
- Vorteile:Gleichmäßige Beschichtung komplexer Geometrien, höhere Abscheideraten, Möglichkeit, mehrere Teile in einer Reaktion zu beschichten.
- Beschränkungen:Hohe Temperaturen und korrosive Nebenprodukte, mögliche Verunreinigungen im Film.
-
PVD:
-
Anwendungen:
-
PVD:
- Häufig verwendet für dekorative Beschichtungen, verschleißfeste Beschichtungen und Halbleitergeräte.
- Beispiele sind Titannitridbeschichtungen auf Schneidwerkzeugen und Aluminiumbeschichtungen auf Verpackungsmaterialien.
-
CVD:
- Weit verbreitet in der Halbleiterherstellung, bei optischen Beschichtungen und Schutzschichten.
- Beispiele sind Siliziumdioxid- und Siliziumnitridschichten in der Mikroelektronik und diamantähnliche Kohlenstoffschichten.
-
PVD:
-
Materialverwendung und Effizienz:
- PVD:Hohe Materialausnutzung, insbesondere bei Verfahren wie EBPVD, wo die Abscheideraten zwischen 0,1 und 100 μm/min liegen.
- CVD:Effizient für die Beschichtung komplexer Formen und mehrerer Teile gleichzeitig, kann aber aufgrund der Verwendung gasförmiger Vorprodukte höhere Materialkosten verursachen.
-
Umwelt- und Sicherheitsaspekte:
- PVD:Im Allgemeinen sicherer und umweltfreundlicher, da niedrigere Temperaturen und keine korrosiven Nebenprodukte entstehen.
- CVD:Erfordert einen sorgfältigen Umgang mit reaktiven Gasen und korrosiven Nebenprodukten, was eine Herausforderung für die Sicherheit und den Umweltschutz darstellen kann.
Wenn ein Käufer von Anlagen oder Verbrauchsmaterialien diese Kernpunkte kennt, kann er fundierte Entscheidungen darüber treffen, ob PVD oder CVD für seine spezifische Anwendung besser geeignet ist, wobei Faktoren wie Substratgeometrie, Abscheidungsrate, Temperaturempfindlichkeit und Umweltauswirkungen zu berücksichtigen sind.
Zusammenfassende Tabelle:
Blickwinkel | PVD | CVD |
---|---|---|
Zustand des Materials | Physikalisch verdampfte feste Materialien | Gasförmige Ausgangsstoffe chemisch in einen festen Film umgewandelt |
Sichtlinie | Direkte Sichtlinie erforderlich; begrenzt für komplexe Geometrien | Keine Sichtlinie erforderlich; gleichmäßige Beschichtung komplizierter Formen |
Temperatur | Niedrigere Temperaturen; keine korrosiven Nebenprodukte | Hohe Temperaturen; mögliche korrosive Nebenprodukte |
Abscheiderate | Geringer im Vergleich zu CVD | Höhere Abscheideraten |
Anwendungen | Dekorative Beschichtungen, verschleißfeste Beschichtungen, Halbleiter | Halbleiter, optische Beschichtungen, Schutzschichten |
Auswirkungen auf die Umwelt | Sicherer und umweltfreundlicher | Erfordert einen sorgfältigen Umgang mit reaktiven Gasen und Nebenprodukten |
Benötigen Sie Hilfe bei der Entscheidung zwischen PVD und CVD für Ihre Anwendung? Kontaktieren Sie noch heute unsere Experten für eine persönliche Beratung!