Das SPS-Verfahren (Spark Plasma Sintering) ist eine fortschrittliche Materialherstellungstechnik, die die Prinzipien des Heißpressens und des gepulsten elektrischen Stroms kombiniert, um ein schnelles und effizientes Sintern von Materialien zu erreichen.Dieses Verfahren zeichnet sich durch seine Fähigkeit aus, Werkstoffe mit einzigartigen Mikrostrukturen und Eigenschaften durch präzise Steuerung von Temperatur, Druck und Heizraten herzustellen.SPS arbeitet im Vakuum oder in einer kontrollierten Atmosphäre, um Oxidation zu verhindern und die Reinheit des Materials zu gewährleisten.Das Verfahren umfasst vier Hauptstufen: Gasentfernung und Vakuumerzeugung, Druckanwendung, Widerstandserhitzung und Kühlung.Der durch gepulste Ströme erzeugte Funkenplasmaeffekt hemmt das Partikelwachstum und ermöglicht die Herstellung von Materialien mit maßgeschneiderten Zusammensetzungen und Eigenschaften.SPS ist in der Forschung und in industriellen Anwendungen weit verbreitet, insbesondere für die Synthese von Hochleistungswerkstoffen wie Ultrahochtemperaturkeramik.
Die wichtigsten Punkte werden erklärt:
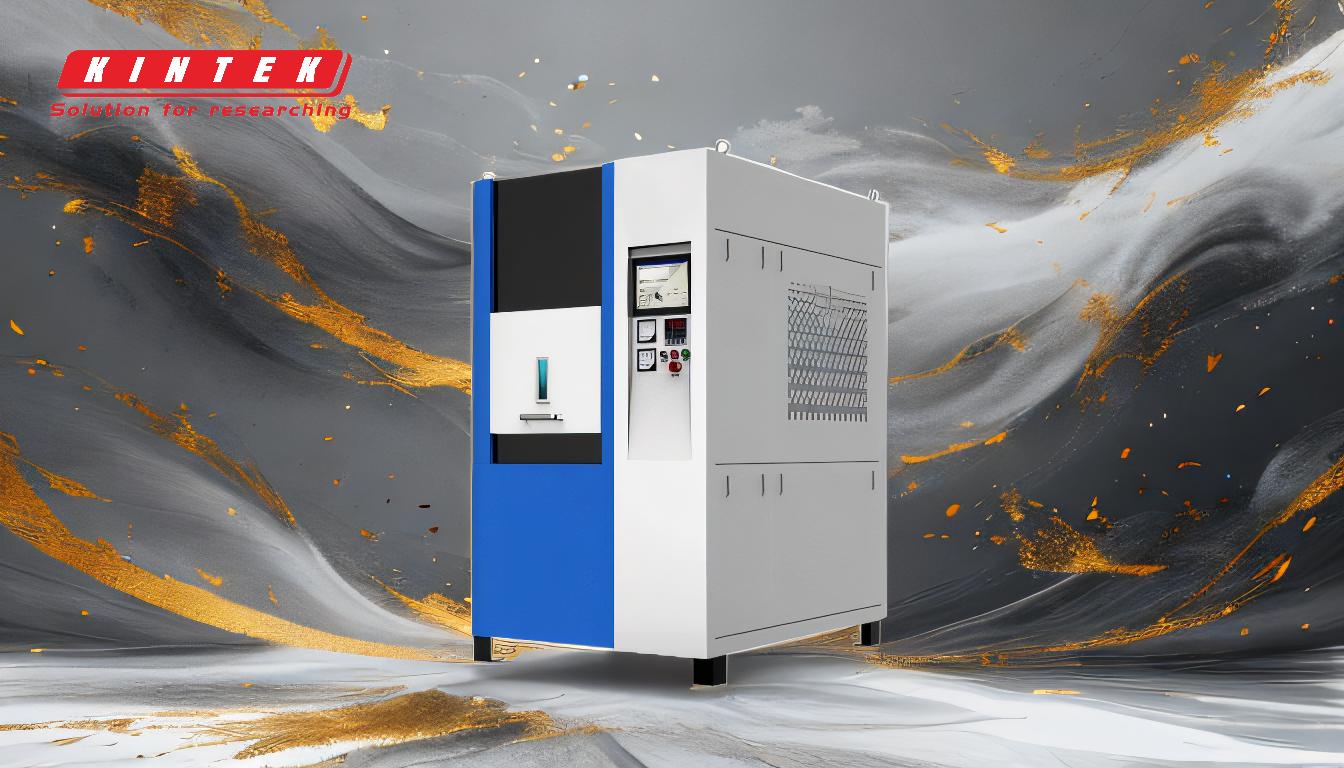
-
Definition und Zweck der SPS-Verarbeitung:
- SPS (Spark Plasma Sintering) ist ein Werkstoffherstellungsverfahren, bei dem Heißpressen mit gepulsten elektrischen Strömen kombiniert wird, um Werkstoffe effizient zu sintern.
- Es dient der Herstellung von Werkstoffen mit einzigartigen Mikrostrukturen und Eigenschaften, wie z. B. Keramik mit hoher Dichte, Nanomaterialien und Verbundwerkstoffe, die mit herkömmlichen Methoden nur schwer zu erreichen sind.
-
Zentraler Mechanismus:Funkenplasma-Effekt:
- Das Verfahren beruht auf dem "Funkenplasmaeffekt", bei dem gepulste elektrische Ströme lokal hohe Temperaturen an der Partikeloberfläche erzeugen.
- Dieser Effekt führt zur Verdampfung, zum Schmelzen und zur Bildung von Nasen zwischen den Partikeln, was zu einer schnellen Verdichtung und Sinterung führt.
- Der Funkenplasmaeffekt hemmt auch das Partikelwachstum und ermöglicht die Herstellung feinkörniger Materialien mit verbesserten mechanischen und thermischen Eigenschaften.
-
Schlüsselphasen des SPS-Prozesses:
-
Stufe 1: Gasentfernung und Vakuumerzeugung:
- Die Kammer wird evakuiert, um Gase zu entfernen und ein Vakuum zu erzeugen, das Oxidation verhindert und die Reinheit des Materials gewährleistet.
-
Stufe 2: Druckanwendung:
- Einachsiger Druck wird auf den Pulverpressling ausgeübt, um die Umlagerung und Verdichtung der Partikel zu erleichtern.
-
Stufe 3: Widerstandsheizung:
- Gepulste elektrische Ströme fließen durch die Graphitmatrize und die Probe und erzeugen Wärme durch Widerstandsheizung.
-
Stufe 4: Kühlung:
- Nach dem Sintern wird die Probe unter kontrollierten Bedingungen abgekühlt, um das gewünschte Gefüge und die gewünschten Eigenschaften zu erhalten.
-
Stufe 1: Gasentfernung und Vakuumerzeugung:
-
Vorteile der SPS-Verarbeitung:
-
Hohe Heizraten und kurze Verarbeitungszeiten:
- SPS erreicht Aufheizraten von bis zu Hunderten von Grad pro Minute, wodurch sich die Verarbeitungszeiten im Vergleich zu herkömmlichen Sinterverfahren erheblich verkürzen.
-
Niedrige Sintertemperaturen:
- Das Verfahren arbeitet mit niedrigeren Temperaturen als das herkömmliche Sintern, wodurch das Kornwachstum minimiert und feine Mikrostrukturen erhalten werden.
-
Präzise Kontrolle:
- Temperatur, Druck und Heizraten können präzise gesteuert werden, was die Herstellung von Materialien mit maßgeschneiderten Eigenschaften ermöglicht.
-
Vielseitigkeit:
- SPS eignet sich für eine breite Palette von Materialien, darunter Keramik, Metalle, Verbundwerkstoffe und Nanomaterialien.
-
Hohe Heizraten und kurze Verarbeitungszeiten:
-
Anwendungen der SPS-Technologie:
-
Synthese fortgeschrittener Materialien:
- SPS wird zur Herstellung von Ultrahochtemperaturkeramik (z. B. ZrC), Nanomaterialien und funktional abgestuften Werkstoffen eingesetzt.
-
Forschung und Entwicklung:
- Diese Technik wird in der materialwissenschaftlichen Forschung häufig eingesetzt, um neue Zusammensetzungen und Eigenschaften zu erforschen.
-
Industrielle Fertigung:
- SPS wird in Branchen eingesetzt, die Hochleistungsmaterialien benötigen, wie z. B. in der Luft- und Raumfahrt, der Automobilindustrie und der Elektronik.
-
Synthese fortgeschrittener Materialien:
-
Ausrüstung und Prozesskontrolle:
-
Graphitstempel:
- Graphit wird aufgrund seiner hohen thermischen und elektrischen Leitfähigkeit üblicherweise für die Pressmatrize verwendet.
-
Touchscreen-Schnittstelle:
- Der Prozess wird über einen Touchscreen gesteuert und programmiert, was eine präzise Einstellung der Parameter und eine Echtzeitüberwachung ermöglicht.
-
Vakuum oder kontrollierte Atmosphäre:
- Das Verfahren wird in einer Vakuum- oder Inertgasumgebung durchgeführt, um Verunreinigungen zu vermeiden und die Materialreinheit zu gewährleisten.
-
Graphitstempel:
-
Vergleich mit konventionellen Methoden:
- SPS bietet erhebliche Vorteile gegenüber herkömmlichen Sinterverfahren, wie z. B. schnellere Verarbeitungszeiten, geringerer Energieverbrauch und die Möglichkeit, Materialien mit einzigartigen Eigenschaften herzustellen.
- Herkömmliche Verfahren erfordern oft höhere Temperaturen und längere Verarbeitungszeiten, was zu Kornwachstum und einer geringeren Materialleistung führt.
Zusammenfassend lässt sich sagen, dass die SPS-Bearbeitung eine Spitzentechnologie ist, die die schnelle und präzise Herstellung fortschrittlicher Werkstoffe ermöglicht.Ihre einzigartige Kombination aus gepulsten elektrischen Strömen, kontrolliertem Druck und hohen Heizraten macht sie zu einem leistungsstarken Werkzeug für Materialwissenschaftler und Ingenieure.Ob in der Forschung oder bei industriellen Anwendungen, SPS bietet eine unvergleichliche Kontrolle und Vielseitigkeit und ist damit eine Schlüsseltechnologie für die Entwicklung von Materialien der nächsten Generation.
Zusammenfassende Tabelle:
Aspekt | Einzelheiten |
---|---|
Definition | Kombiniert Heißpressen und gepulste elektrische Ströme für eine effiziente Sinterung. |
Kern-Mechanismus | Der Funkenplasmaeffekt ermöglicht eine schnelle Verdichtung und feinkörnige Materialien. |
Wichtige Schritte | Gasentnahme, Druckaufbringung, Widerstandserwärmung und kontrollierte Abkühlung. |
Vorteile | Hohe Heizraten, niedrige Sintertemperaturen, präzise Steuerung, Vielseitigkeit. |
Anwendungen | Synthese von Keramiken, Nanomaterialien und industriellen Hochleistungswerkstoffen. |
Ausrüstung | Graphitformen, Touchscreen-Schnittstelle, Vakuum/kontrollierte Atmosphäre. |
Vergleich | Schneller, geringerer Energieverbrauch und bessere Materialeigenschaften als bei herkömmlichen Verfahren. |
Erschließen Sie das Potenzial moderner Werkstoffe mit der SPS-Technologie. Kontaktieren Sie noch heute unsere Experten um mehr zu erfahren!