Die Dichte von gesintertem Material wird durch verschiedene Faktoren beeinflusst, darunter die anfängliche Porosität des Grünlings, die Sintertemperatur, die Sinterzeit, die Partikelgröße und die Anwendung von Druck.Die Dichte wird häufig als relative Dichte gemessen, d. h. als Verhältnis zwischen der Dichte des porösen Körpers und der Dichte des nicht porösen Materials.Faktoren wie Temperatur und Druck verbessern die Verdichtung, indem sie die Umlagerung von Teilchen fördern und die Porosität verringern.Kleinere Partikelgrößen und homogene Zusammensetzungen tragen ebenfalls zu einer besseren Verdichtung bei.Die endgültige Porosität und Dichte von gesinterten Werkstoffen sind entscheidend für Eigenschaften wie Festigkeit, Leitfähigkeit und Haltbarkeit.
Die wichtigsten Punkte erklärt:
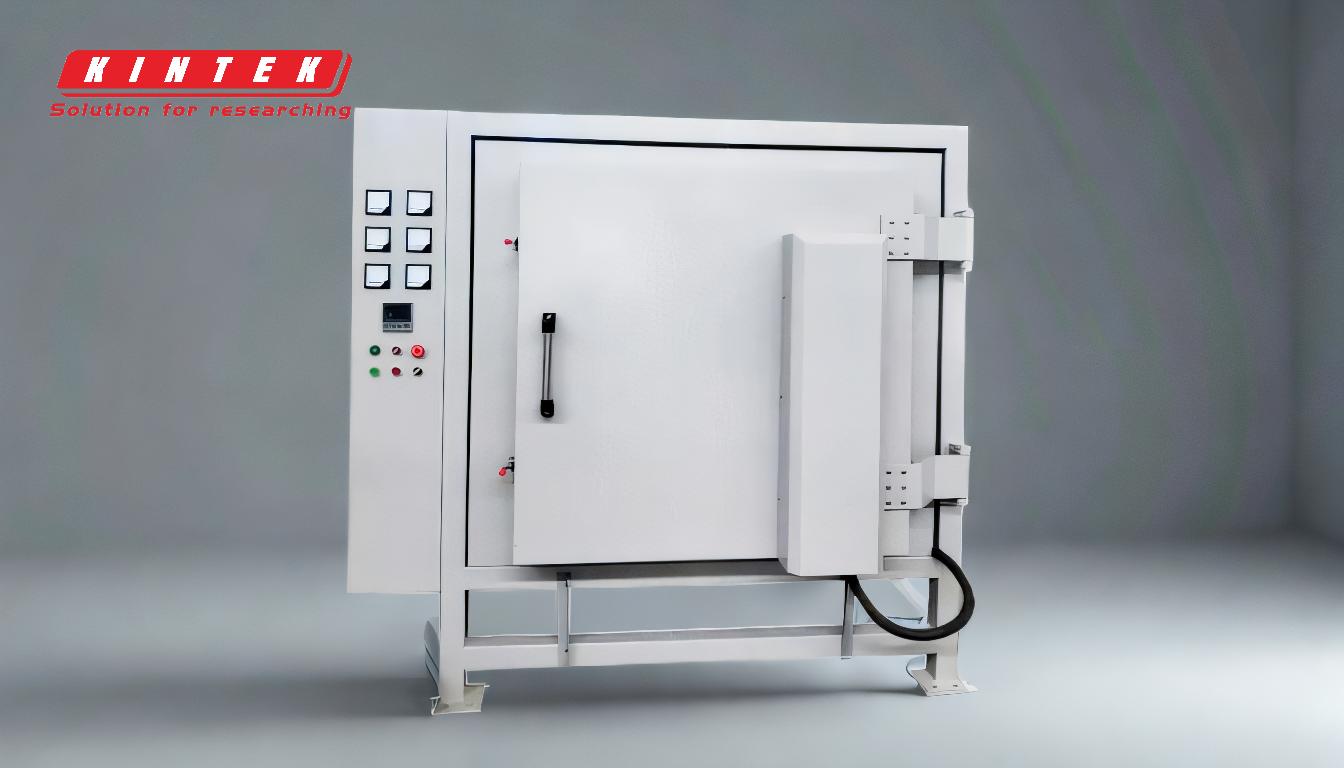
-
Definition der Dichte von gesintertem Material:
- Die Dichte von gesintertem Material bezieht sich auf die Masse pro Volumeneinheit des Materials nach dem Sinterprozess.Sie wird häufig als relative Dichte ausgedrückt, bei der die Dichte des porösen Sinterkörpers mit der theoretischen Dichte des nicht porösen Materials verglichen wird.
-
Faktoren, die die gesinterte Dichte beeinflussen:
- Ausgangsporosität von Green Compact:Die Anfangsporosität des Materials vor dem Sintern hat einen erheblichen Einfluss auf die Enddichte.Eine höhere Anfangsporosität erfordert eine stärkere Verdichtung während des Sinterns.
- Sintertemperatur:Höhere Temperaturen erhöhen im Allgemeinen die Diffusionsgeschwindigkeit der Partikel, was zu einer besseren Verdichtung und geringeren Porosität führt.
- Sinterzeit:Längere Sinterzeiten lassen mehr Zeit für die Umstrukturierung der Partikel und die Beseitigung von Poren, was zu einer höheren Dichte beiträgt.
- Partikelgröße:Kleinere Partikel haben eine größere Oberfläche im Verhältnis zum Volumen, was die Sinterkinetik verbessert und die Verdichtung fördert.
- Druck:Die Anwendung von Druck während des Sinterns kann den Verdichtungsprozess beschleunigen, indem die Partikel in engeren Kontakt gezwungen werden und die Porosität verringert wird.
-
Messung der Dichte:
- Relative Dichte:Dies ist eine gängige Kennzahl zur Beurteilung der Dichte von gesinterten Materialien.Sie wird als Verhältnis zwischen der Dichte des porösen Körpers und der theoretischen Dichte des nicht porösen Materials berechnet.
- Porosität:Die Porosität ist das Verhältnis zwischen dem Porenvolumen und dem Gesamtvolumen des Materials.Eine geringere Porosität bedeutet eine höhere Dichte.
- Porengrößenverteilung:Die Größe und Verteilung der Poren im Material kann die Gesamtdichte und die mechanischen Eigenschaften des Materials beeinflussen.
-
Einfluss der Materialzusammensetzung und der Sinteratmosphäre:
- Materialzusammensetzung:Homogene Zusammensetzungen mit einheitlichen Partikelgrößen neigen dazu, gleichmäßiger zu sintern, was zu einer besseren Verdichtung führt.
- Sinteratmosphäre:Die Umgebung, in der die Sinterung stattfindet (z. B. Luft, Vakuum oder Inertgase wie Argon oder Stickstoff), kann die endgültige Dichte beeinflussen, indem sie Oxidations- oder Reduktionsreaktionen beeinflusst.
-
Praktische Auswirkungen für Einkäufer von Geräten und Verbrauchsmaterialien:
- Langlebigkeit und Leistung:Sinterwerkstoffe mit höherer Dichte weisen in der Regel bessere mechanische Eigenschaften auf, wie z. B. Festigkeit, Härte und Beständigkeit gegen Verschleiß und Umwelteinflüsse.
- Anwendungsspezifische Anforderungen:Käufer sollten bei der Auswahl von Sinterwerkstoffen die spezifischen Anforderungen ihrer Anwendung berücksichtigen, wie z. B. die Notwendigkeit hoher Festigkeit, Wärmebeständigkeit oder Leitfähigkeit.
- Kostenüberlegungen:Die Parameter des Sinterprozesses, wie Temperatur, Zeit und Druck, können die Produktionskosten beeinflussen.Das Verständnis dieser Faktoren kann helfen, kosteneffiziente Kaufentscheidungen zu treffen.
-
Erweiterte Überlegungen:
- Hochtemperatursintern:Für Werkstoffe, die eine hohe Zugfestigkeit, Biegewechselfestigkeit und Kerbschlagarbeit erfordern, kann eine Hochtemperatursinterung erforderlich sein.
- Druckunterstütztes Sintern:Verfahren wie das Heißpressen oder das Funkenplasmasintern können die Sinterzeit und die Porosität erheblich reduzieren, was zu Materialien mit höherer Dichte führt.
Zusammenfassend lässt sich sagen, dass die Dichte von gesinterten Materialien eine komplexe Eigenschaft ist, die von mehreren Faktoren beeinflusst wird, darunter die anfängliche Porosität, die Sintertemperatur, die Zeit, die Partikelgröße und der Druck.Das Verständnis dieser Faktoren ist von entscheidender Bedeutung für die Optimierung des Sinterprozesses und die Auswahl von Materialien, die den spezifischen Anwendungsanforderungen entsprechen.
Zusammenfassende Tabelle:
Faktor | Einfluss auf die gesinterte Dichte |
---|---|
Anfangsporosität | Eine höhere Anfangsporosität erfordert eine stärkere Verdichtung während des Sinterns. |
Sintertemperatur | Höhere Temperaturen erhöhen die Partikeldiffusion, verbessern die Verdichtung und verringern die Porosität. |
Sinterzeit | Längere Sinterzeiten ermöglichen eine bessere Umlagerung der Partikel und die Beseitigung von Poren. |
Partikelgröße | Kleinere Partikel verbessern die Sinterkinetik und fördern die Verdichtung. |
Druck | Angewandter Druck beschleunigt die Verdichtung durch Verringerung der Porosität und Erzwingen des Partikelkontakts. |
Materialzusammensetzung | Homogene Zusammensetzungen mit einheitlichen Partikelgrößen verbessern die Verdichtung. |
Sinteratmosphäre | Die Umgebung (z. B. Luft, Vakuum, Inertgase) wirkt sich auf die Oxidation/Reduktion aus und beeinflusst die Dichte. |
Benötigen Sie Hilfe bei der Optimierung Ihres Sinterprozesses? Kontaktieren Sie noch heute unsere Experten für maßgeschneiderte Lösungen!