Sputtern und physikalische Gasphasenabscheidung (PVD) sind beides Techniken zur Abscheidung dünner Schichten auf Substraten, unterscheiden sich jedoch erheblich in ihren Mechanismen und Anwendungen. Sputtern ist eine Untergruppe von PVD, die verschiedene Verfahren wie thermische Verdampfung und Elektronenstrahlverdampfung umfasst. Der Hauptunterschied liegt darin, wie das Material für die Abscheidung in einen Dampf umgewandelt wird. Beim Sputtern werden energiereiche Ionen verwendet, um Atome aus einem Zielmaterial herauszulösen, während andere PVD-Methoden in der Regel auf der Erhitzung des Materials bis zu seinem Verdampfungspunkt beruhen. Dieser grundlegende Unterschied macht das Sputtern vielseitiger, insbesondere für temperaturempfindliche Materialien wie Kunststoffe und organische Stoffe, da es im Vergleich zu anderen PVD-Verfahren bei niedrigeren Temperaturen arbeitet.
Die wichtigsten Punkte werden erklärt:
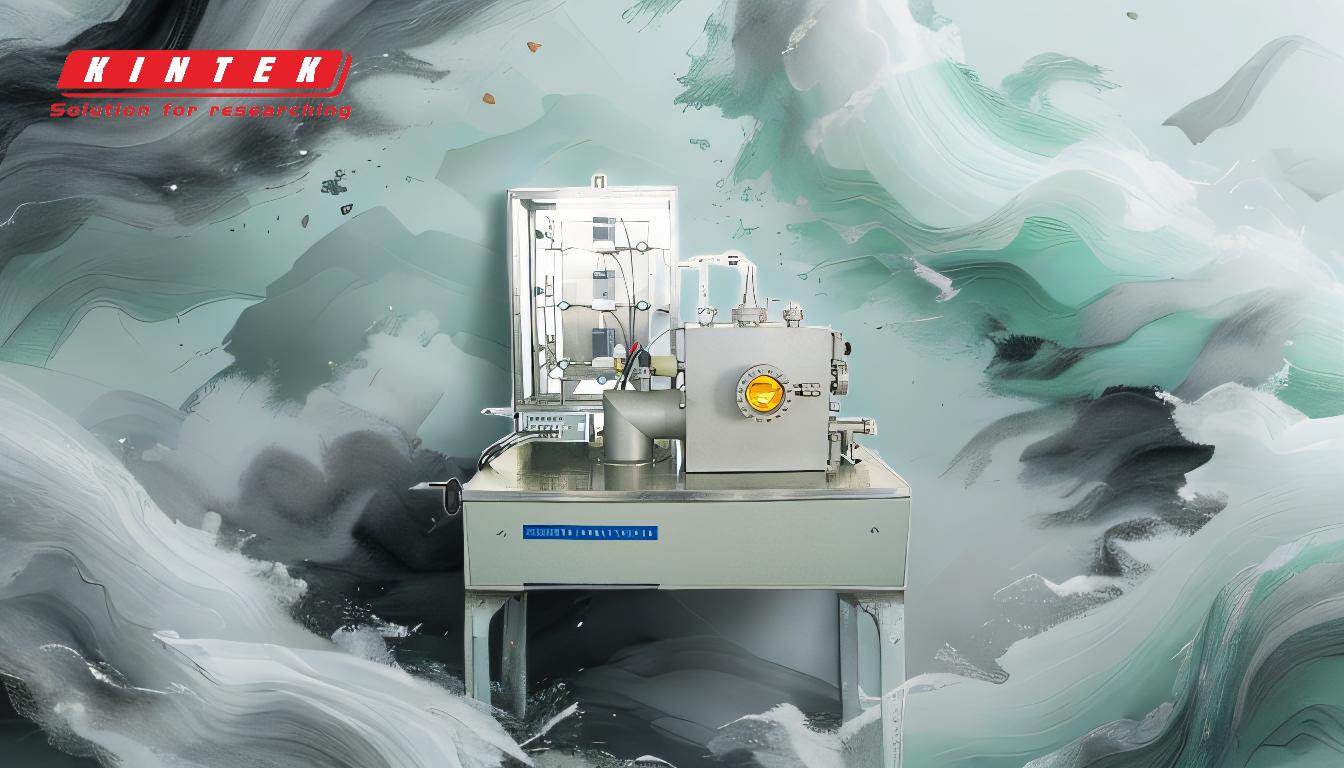
-
Mechanismus der Materialverdampfung:
- Sputtern: Beim Sputtern wird zwischen dem Targetmaterial und dem Substrat ein Plasma erzeugt. Energetische Ionen aus dem Plasma stoßen mit dem Target zusammen und schlagen Atome aus der Oberfläche des Targets heraus (Sputtern). Diese Atome wandern dann auf das Substrat und bilden einen dünnen Film.
- Andere PVD-Verfahren (z. B. thermische oder E-Strahl-Verdampfung): Bei diesen Verfahren wird das Zielmaterial auf seine Verdampfungstemperatur erhitzt, wodurch ein Dampf entsteht, der auf dem Substrat kondensiert. Dazu wird das Material in der Regel geschmolzen oder sublimiert.
-
Energiequelle:
- Sputtern: Nutzt elektrische Energie zur Erzeugung eines Plasmas, das energiereiche Ionen produziert. Diese Ionen übertragen ihren Impuls auf das Zielmaterial und stoßen Atome aus, ohne dass hohe Temperaturen erforderlich sind.
- Andere PVD-Methoden: Verlassen sich auf thermische Energie, um das Zielmaterial zu verdampfen. Dazu sind oft hohe Temperaturen erforderlich, was die Art der zu beschichtenden Substrate einschränken kann.
-
Prozess-Temperatur:
- Sputtern: Im Vergleich zu anderen PVD-Verfahren wird bei niedrigeren Temperaturen gearbeitet. Daher eignet sich dieses Verfahren für die Beschichtung temperaturempfindlicher Materialien wie Kunststoffe, organische Stoffe und bestimmte Glasarten.
- Andere PVD-Verfahren: Erfordern in der Regel höhere Temperaturen, um eine Verdampfung zu erreichen, was für hitzeempfindliche Substrate nachteilig sein kann.
-
Material-Kompatibilität:
- Sputtern: Es kann eine breite Palette von Materialien abgeschieden werden, darunter Metalle, Legierungen und Keramiken, ohne dass das Zielmaterial geschmolzen wird. Dies liegt daran, dass das Verfahren auf Impulsübertragung und nicht auf thermischer Energie beruht.
- Andere PVD-Verfahren: Haben möglicherweise Probleme mit Materialien, die einen hohen Schmelzpunkt haben oder empfindlich auf thermische Zersetzung reagieren, da das Material auf hohe Temperaturen erhitzt werden muss.
-
Filmqualität und Gleichmäßigkeit:
- Sputtern: Erzeugt oft Schichten mit besserer Haftung und Gleichmäßigkeit, insbesondere bei komplexen Geometrien. Das Verfahren ermöglicht eine genaue Kontrolle der Abscheidungsrate und der Schichtdicke.
- Andere PVD-Verfahren: Sie sind zwar immer noch in der Lage, qualitativ hochwertige Schichten zu erzeugen, können aber aufgrund von Problemen mit der Sichtlinie bei der Herstellung gleichmäßiger Beschichtungen auf komplexen Formen Probleme bereiten.
-
Anwendungen:
- Sputtern: Weit verbreitet in Branchen, die eine präzise Abscheidung bei niedrigen Temperaturen erfordern, wie z. B. die Halbleiterherstellung, optische Beschichtungen und flexible Elektronik.
- Andere PVD-Methoden: Werden häufig bei Anwendungen eingesetzt, bei denen eine Hochtemperaturverarbeitung akzeptabel ist, z. B. bei der Abscheidung von Metallen für dekorative Beschichtungen oder bei hochtemperaturbeständigen Schichten.
Zusammenfassend lässt sich sagen, dass sowohl das Sputtern als auch andere PVD-Verfahren für die Abscheidung von Dünnschichten verwendet werden, wobei sich das Sputtern durch seine Fähigkeit auszeichnet, bei niedrigeren Temperaturen zu arbeiten, und dass es auf Impulsübertragung statt auf Wärmeenergie beruht. Dies macht es besonders vorteilhaft für die Beschichtung temperaturempfindlicher Materialien und die Herstellung hochwertiger, gleichmäßiger Schichten für verschiedene Anwendungen.
Zusammenfassende Tabelle:
Blickwinkel | Sputtern | Andere PVD-Verfahren |
---|---|---|
Mechanismus | Verwendet energiereiche Ionen, um Atome aus einem Zielmaterial herauszulösen. | Das Material muss bis zu seinem Verdampfungspunkt erhitzt werden. |
Energiequelle | Elektrische Energie erzeugt ein Plasma für den Ionenbeschuss. | Thermische Energie erwärmt das Material, um es zu verdampfen. |
Prozesstemperatur | Arbeitet bei niedrigeren Temperaturen, ideal für hitzeempfindliche Materialien. | Erfordert höhere Temperaturen, was die Verwendung mit hitzeempfindlichen Substraten einschränkt. |
Material-Kompatibilität | Beschichtet Metalle, Legierungen und Keramiken, ohne das Target zu schmelzen. | Kann bei hochschmelzenden oder thermisch empfindlichen Materialien Probleme bereiten. |
Filmqualität | Erzeugt gleichmäßige Schichten mit besserer Haftung, selbst auf komplexen Geometrien. | Es kann schwierig sein, gleichmäßige Beschichtungen auf komplexen Formen zu erzielen. |
Anwendungen | Einsatz in der Halbleiterherstellung, bei optischen Beschichtungen und in der flexiblen Elektronik. | Geeignet für dekorative Beschichtungen und hochtemperaturbeständige Filme. |
Benötigen Sie Hilfe bei der Auswahl des richtigen Verfahrens zur Dünnschichtabscheidung? Kontaktieren Sie noch heute unsere Experten für eine persönliche Beratung!