Anlassen und Sintern sind zwei verschiedene Wärmebehandlungsverfahren, die in der Werkstoffkunde eingesetzt werden und jeweils unterschiedlichen Zwecken dienen und einzigartige Mechanismen beinhalten.Das Anlassen dient in erster Linie dazu, die Sprödigkeit von gehärtetem Stahl zu verringern, indem er auf eine Temperatur unterhalb seines kritischen Punktes erwärmt und anschließend kontrolliert abgekühlt wird.Durch dieses Verfahren wird die Zähigkeit erhöht, während die Härte erhalten bleibt.Sintern hingegen ist ein Verfahren, bei dem eine feste Materialmasse durch Hitze oder Druck verdichtet und geformt wird, ohne sie bis zum Punkt der Verflüssigung zu schmelzen.Es wird häufig in der Pulvermetallurgie eingesetzt, um aus pulverförmigen Materialien feste Objekte zu schaffen und deren Festigkeit und Dichte zu verbessern.Bei beiden Verfahren wird zwar erhitzt, aber ihre Ziele, Mechanismen und Anwendungen unterscheiden sich erheblich.
Die wichtigsten Punkte werden erklärt:
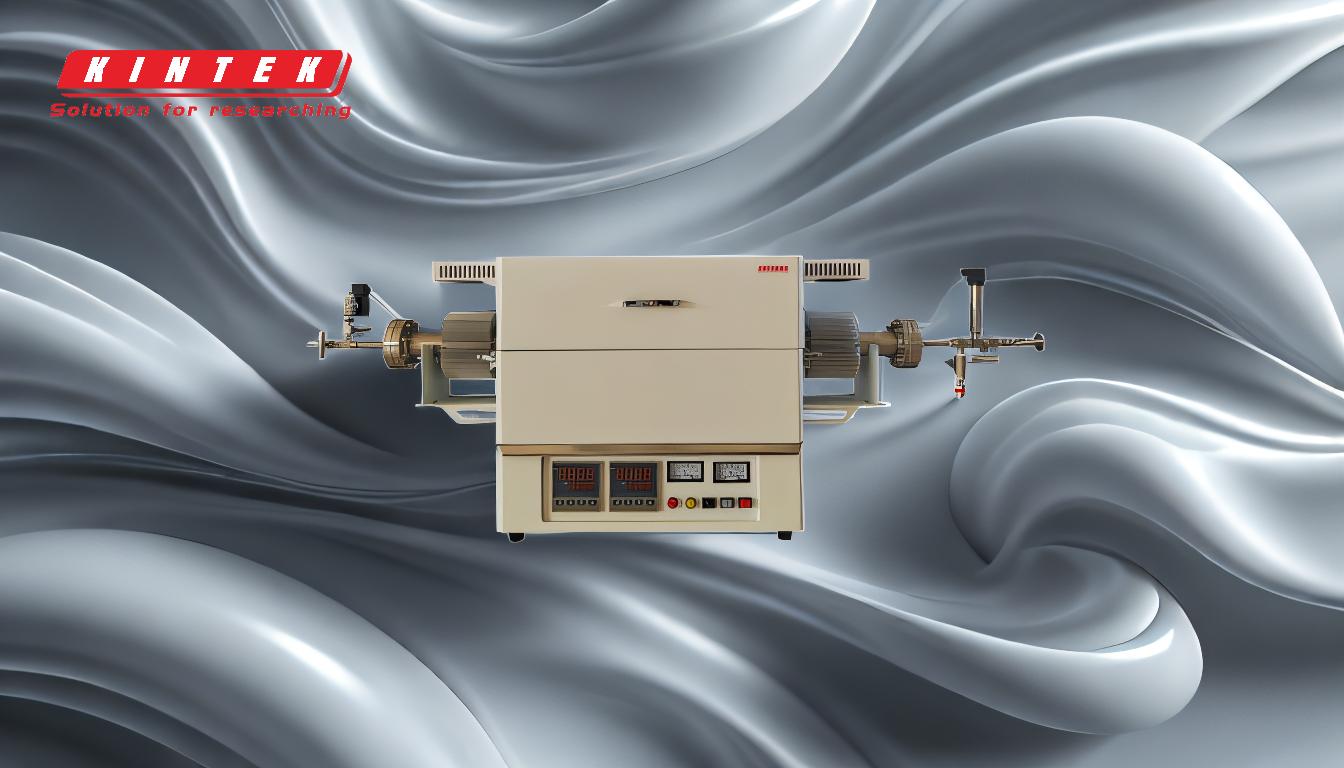
-
Definition und Zweck:
- Anlassen:Ein Wärmebehandlungsverfahren, das bei gehärteten Stählen angewendet wird, um die Sprödigkeit zu verringern und die Zähigkeit zu verbessern.Dabei wird das Material auf eine Temperatur unterhalb des kritischen Punktes erwärmt und anschließend kontrolliert abgekühlt.
- Sintern:Ein Verfahren zur Herstellung fester Gegenstände aus pulverförmigen Materialien durch Anwendung von Wärme und/oder Druck.Es wird üblicherweise in der Pulvermetallurgie eingesetzt, um die Festigkeit, Dichte und strukturelle Integrität des Materials zu verbessern.
-
Temperatur und Mechanismus:
- Anlassen:Das Verfahren findet in der Regel bei Temperaturen zwischen 150°C und 650°C (302°F bis 1202°F) statt, je nach den gewünschten Eigenschaften.Der Prozess beinhaltet die Umwandlung von Martensit (einer harten, spröden Phase) in angelassenen Martensit, der zäher und weniger spröde ist.
- Sintern:Dabei wird das Material auf eine Temperatur unterhalb seines Schmelzpunktes erhitzt, in der Regel auf 70 bis 90 % der Schmelztemperatur.Die Partikel verbinden sich durch Diffusion miteinander, wodurch die Porosität verringert und die Dichte erhöht wird, ohne dass sich das Material verflüssigt.
-
Zustand des Materials:
- Anlassen:Angewandt auf bereits gehärtete Werkstoffe, in der Regel Stähle, die abgeschreckt worden sind.Ziel ist es, das Mikrogefüge zu verändern, um ein Gleichgewicht zwischen Härte und Zähigkeit zu erreichen.
- Sintern:Angewandt auf pulverförmige Materialien, häufig Metalle, Keramiken oder Verbundwerkstoffe.Ziel ist es, das Pulver zu einer festen Masse mit verbesserten mechanischen Eigenschaften zu verfestigen.
-
Mikrostrukturelle Veränderungen:
- Anlassen:Führt zur Zersetzung von Martensit in Ferrit und Zementit, was die inneren Spannungen reduziert und die Duktilität und Zähigkeit verbessert.
- Sintern:Führt zur Bindung der Partikel an ihren Kontaktpunkten, verringert die Porosität und erhöht die Dichte und Festigkeit des Materials.Das Mikrogefüge wird homogener und kohäsiver.
-
Anwendungen:
- Anlassen:Wird häufig bei der Herstellung von Werkzeugen, Zahnrädern, Federn und anderen Bauteilen verwendet, die ein ausgewogenes Verhältnis von Härte und Zähigkeit erfordern.Es ist unerlässlich für Anwendungen, bei denen das Material Stößen und Verschleiß standhalten muss.
- Sintern:Weit verbreitet bei der Herstellung von Metallteilen, Keramik und Verbundwerkstoffen.Besonders wichtig ist sie in Branchen wie der Automobilindustrie, der Luft- und Raumfahrt und der Elektronik, wo komplexe Formen und Hochleistungsmaterialien erforderlich sind.
-
Vorteile und Beschränkungen:
-
Anlassen:
- Vorteile:Verbessert die Zähigkeit und verringert die Sprödigkeit, ohne die Härte wesentlich zu beeinträchtigen.Verbessert die allgemeine Haltbarkeit des Materials.
- Beschränkungen:Kann die Härte des Materials verringern, wenn es nicht sorgfältig kontrolliert wird.Das Verfahren ist auf Materialien beschränkt, die zuvor gehärtet wurden.
-
Sintern:
- Vorteile:Ermöglicht die Herstellung komplexer Formen und endkonturnaher Bauteile mit minimalem Materialabfall.Kann für eine Vielzahl von Materialien verwendet werden, darunter Metalle, Keramiken und Verbundwerkstoffe.
- Beschränkungen:Das Verfahren kann zeitaufwendig sein und zusätzliche Bearbeitungsschritte erfordern, um die gewünschte Oberflächenqualität zu erreichen.Die Anfangskosten für Pulvermaterialien können hoch sein.
-
Anlassen:
-
Prozesskontrolle:
- Anlassen:Um die gewünschten mechanischen Eigenschaften zu erreichen, müssen Temperatur und Abkühlgeschwindigkeit genau gesteuert werden.Übermäßiges Tempern kann zu übermäßiger Erweichung führen, während zu geringes Tempern die Sprödigkeit möglicherweise nicht ausreichend reduziert.
- Sintern:Eine sorgfältige Kontrolle von Temperatur, Druck und Atmosphäre ist erforderlich, um eine ordnungsgemäße Bindung der Partikel zu gewährleisten.Die Sinteratmosphäre (z. B. Vakuum, Inertgas) ist entscheidend, um Oxidation und Verunreinigung zu verhindern.
Zusammenfassend lässt sich sagen, dass Anlassen und Sintern beides wichtige Wärmebehandlungsverfahren in der Werkstoffkunde sind, die jedoch unterschiedlichen Zwecken dienen und verschiedene Mechanismen beinhalten.Beim Anlassen geht es darum, die Zähigkeit gehärteter Werkstoffe zu verbessern, während beim Sintern pulverförmige Werkstoffe zu festen Gegenständen mit verbesserten Eigenschaften verfestigt werden sollen.Das Verständnis der Unterschiede zwischen diesen Verfahren ist entscheidend für die Auswahl der geeigneten Behandlung für bestimmte Anwendungen und Materialien.
Zusammenfassende Tabelle:
Aspekt | Anlassen | Sintern |
---|---|---|
Zweck | Reduziert die Sprödigkeit von gehärtetem Stahl, verbessert die Zähigkeit. | Verfestigt pulverförmige Materialien zu festen Gegenständen, verbessert Festigkeit und Dichte. |
Temperaturbereich | 150°C bis 650°C (302°F bis 1202°F). | 70% bis 90% des Schmelzpunktes des Materials. |
Zustand des Materials | Angewandt auf gehärtete Materialien (z. B. Stahl). | Angewandt auf pulverförmige Werkstoffe (z. B. Metalle, Keramik). |
Mikrostrukturelle Veränderung | Zersetzt Martensit in Ferrit und Zementit. | Bindet Partikel, verringert die Porosität und erhöht die Dichte. |
Anwendungen | Werkzeuge, Zahnräder, Federn und Komponenten, die Härte und Zähigkeit erfordern. | Automobil-, Luft- und Raumfahrt- sowie Elektronikindustrie für komplexe Formen. |
Vorteile | Verbessert die Zähigkeit ohne Einbußen bei der Härte. | Produziert komplexe Formen mit minimalem Materialabfall. |
Beschränkungen | Kann die Härte verringern, wenn sie nicht kontrolliert wird; beschränkt auf gehärtete Materialien. | Zeitaufwendig; kann zusätzliche Nachbearbeitungsschritte erfordern. |
Benötigen Sie Hilfe bei der Auswahl des richtigen Wärmebehandlungsverfahrens für Ihre Materialien? Kontaktieren Sie unsere Experten noch heute!