Das Sintern ist ein kritischer Prozess in der Materialwissenschaft, bei dem die Temperatur eine entscheidende Rolle bei der Bestimmung der endgültigen Eigenschaften des Materials spielt. Die Auswirkungen der Temperatur auf das Sintern sind vielfältig und beeinflussen das Kornwachstum, die Verdichtung, die Porosität und die mechanischen Eigenschaften wie Festigkeit und Härte. Optimale Sintertemperaturen und kontrollierte Aufheiz- und Abkühlgeschwindigkeiten sind für das Erreichen der gewünschten Materialeigenschaften unerlässlich. Hohe Temperaturen fördern die Partikelbindung und -diffusion, aber zu hohe Temperaturen oder ungeeignete Heizraten können zu Defekten oder verschlechterten Eigenschaften führen. Das Verständnis des Zusammenspiels zwischen Temperatur, Heizrate und anderen Variablen wie Atmosphäre und Partikelgröße ist für die Optimierung des Sinterprozesses entscheidend.
Die wichtigsten Punkte werden erklärt:
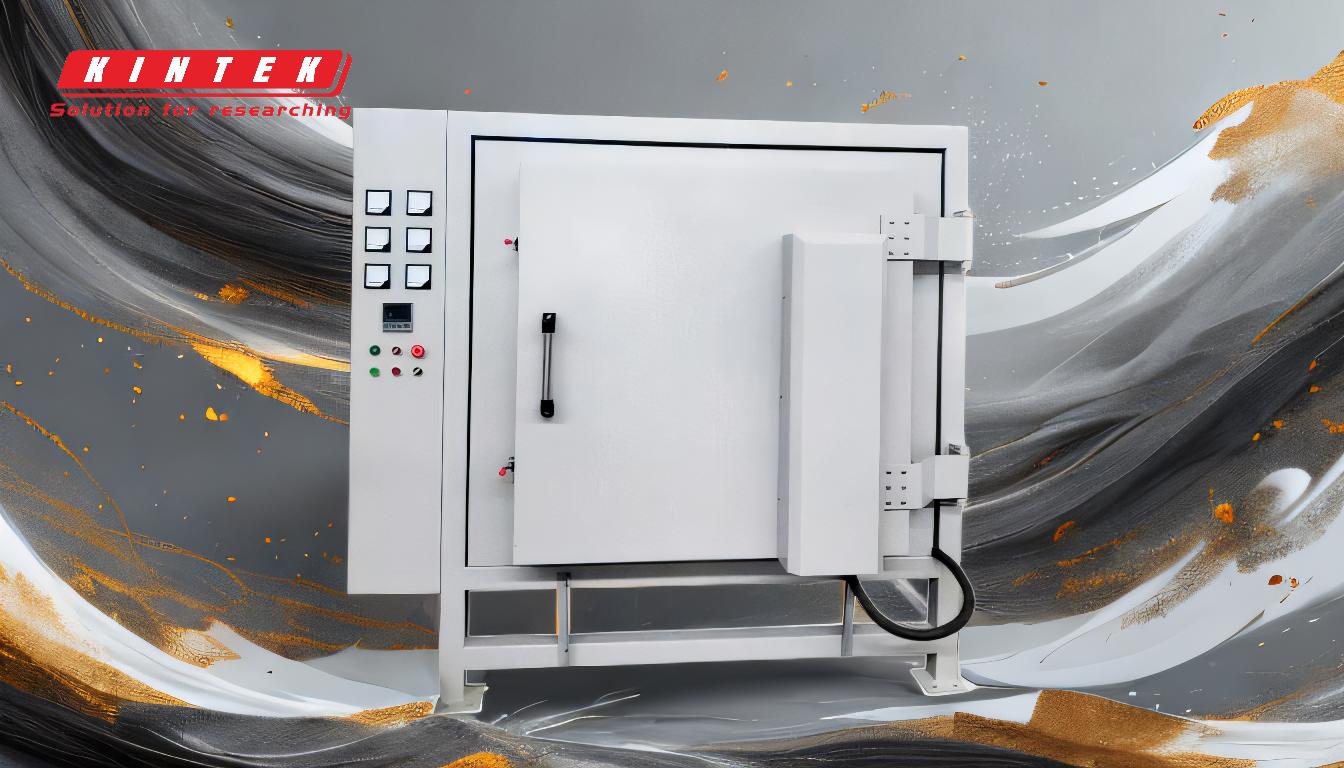
-
Die Rolle der Temperatur bei Partikelbindung und Diffusion:
- Hohe Temperaturen, die oft mehrere tausend Grad Celsius erreichen, sind für die Förderung der Bindung und Diffusion zwischen den Pulverteilchen unerlässlich.
- Diese Bindung führt zu Kornwachstum und Verdichtung, die für das Erreichen der gewünschten Mikrostruktur und der mechanischen Eigenschaften des gesinterten Materials entscheidend sind.
-
Sintern vs. Schmelzen:
- Das Sintern erfolgt bei Temperaturen unterhalb des Schmelzpunkts des Materials und beruht auf einer Kombination aus Temperatur und Druck, um die Partikel zu verschmelzen.
- Beim Schmelzen hingegen muss das Material seinen Schmelzpunkt erreichen, wodurch es flüssig wird. Das Sintern kann daher bei niedrigeren Temperaturen durchgeführt werden und eignet sich für Materialien, die bei höheren Temperaturen zersetzt oder oxidiert werden könnten.
-
Kritische Temperaturbereiche:
- Von Raumtemperatur bis 900 °C sind die Auswirkungen auf das Material minimal. Entscheidend sind jedoch die Temperaturanstiegsgeschwindigkeit von 900 °C auf die obere Sintertemperatur, die Temperaturkonstanz während der Haltezeit und die Abkühlgeschwindigkeit zurück auf etwa 900 °C.
- Die präzise Steuerung dieser Temperaturbereiche gewährleistet eine gleichmäßige Verdichtung und minimiert Fehler.
-
Auswirkungen auf die Mikrostruktur:
- Die Sintertemperatur hat einen direkten Einfluss auf die Korngröße, die Porengröße und die Form und Verteilung der Korngrenzen im Mikrogefüge des Materials.
- Diese mikrostrukturellen Veränderungen wirken sich wiederum auf die Eigenschaften des Materials aus, z. B. auf die Festigkeit, Haltbarkeit und Härte.
-
Porosität, Dichte und mechanische Eigenschaften:
- Die Sintertemperatur und die Sinterzeit haben einen erheblichen Einfluss auf die Porosität, Dichte, Festigkeit und Härte des Sinterkörpers.
- Hohe Sintertemperaturen und lange Erhitzungszeiten können die Porosität verringern und die Dichte erhöhen, aber zu hohe Temperaturen können zu Defekten oder verschlechterten Eigenschaften führen.
- Umgekehrt können unzureichende Temperaturen oder Heizzeiten zu einer unvollständigen Sinterung und damit zu schlechten Materialeigenschaften führen.
-
Variablen, die die Sinterung beeinflussen:
- Neben der Temperatur spielen auch andere Variablen wie die Sinteratmosphäre (Luft, Vakuum oder Inertgase wie Argon/Stickstoff), die Heizrate, der Druck, die Partikelgröße und die Zusammensetzung eine entscheidende Rolle.
- Hochtemperatursintern kann die Zugfestigkeit, die Biegewechselfestigkeit und die Kerbschlagarbeit verbessern, aber diese Vorteile müssen gegen das Risiko von Defekten abgewogen werden.
-
Überlegungen zur Heizrate:
- Die Aufheizrate ist ein kritischer Faktor; ist sie zu hoch, kann sie zu einer unzureichenden Sinterung im Material führen, was zu erheblichen Unterschieden im Sinterungsgrad in verschiedenen Bereichen führt.
- Dies kann zu einem Hochtemperatur-Schmelzpeak und einer hohen Kristallinität führen, was für bestimmte Anwendungen nicht wünschenswert sein kann.
-
Optimierung der Sinterparameter:
- Um die besten Ergebnisse zu erzielen, müssen die Sinterparameter, einschließlich Temperatur, Heizrate, Druck und Atmosphäre, unbedingt optimiert werden.
- Kleinere Partikelgrößen und homogene Zusammensetzungen begünstigen im Allgemeinen eine bessere Verdichtung und gleichmäßigere Eigenschaften des gesinterten Materials.
Zusammenfassend lässt sich sagen, dass die Temperatur ein grundlegender Faktor im Sinterprozess ist, der alles von der Partikelbindung und -diffusion bis hin zu den endgültigen Materialeigenschaften beeinflusst. Die sorgfältige Steuerung der Temperatur ist zusammen mit anderen Sinterparametern eine wesentliche Voraussetzung für die Herstellung hochwertiger Sinterwerkstoffe mit den gewünschten Eigenschaften.
Zusammenfassende Tabelle:
Aspekt | Auswirkungen der Temperatur |
---|---|
Partikelbindung | Hohe Temperaturen fördern die Bindung und Diffusion, die für das Kornwachstum und die Verdichtung unerlässlich sind. |
Sintern vs. Schmelzen | Die Sinterung erfolgt unterhalb des Schmelzpunktes und ist daher ideal für Materialien, die zur Zersetzung neigen. |
Kritische Temperaturbereiche | Die präzise Steuerung zwischen 900°C und der oberen Sintertemperatur gewährleistet eine gleichmäßige Verdichtung. |
Mikrostruktur | Beeinflusst die Korngröße, die Porengröße und die Verteilung der Korngrenzen, was sich auf die Materialeigenschaften auswirkt. |
Porosität und Dichte | Hohe Temperaturen verringern die Porosität und erhöhen die Dichte, aber übermäßige Hitze kann zu Defekten führen. |
Variablen | Atmosphäre, Erhitzungsgeschwindigkeit, Druck, Partikelgröße und Zusammensetzung spielen ebenfalls eine entscheidende Rolle. |
Heizrate | Eine zu hohe Rate kann eine ungleichmäßige Sinterung verursachen, die zu unerwünschten Materialeigenschaften führt. |
Optimierung | Die Abstimmung von Temperatur, Heizrate und anderen Parametern ist der Schlüssel zum gewünschten Ergebnis. |
Benötigen Sie Hilfe bei der Optimierung Ihres Sinterprozesses? Kontaktieren Sie unsere Experten noch heute für maßgeschneiderte Lösungen!