Beim Hartlöten handelt es sich um einen Metallverbindungsprozess, bei dem ein Füllmetall in eine Verbindung zwischen zwei oder mehr Grundmetallen geschmolzen wird. Die höchste Temperatur beim Löten hängt typischerweise von den zu verbindenden Materialien und der Art des verwendeten Zusatzmetalls ab. Im Allgemeinen liegen die Löttemperaturen zwischen 450 °C und 1200 °C (840 °F bis 2200 °F). Die spezifische Temperatur muss jedoch sorgfältig ausgewählt werden, um eine Beschädigung der Grundmetalle zu vermeiden und gleichzeitig einen ordnungsgemäßen Fluss und eine ordnungsgemäße Haftung des Zusatzmetalls sicherzustellen. Faktoren wie der Schmelzpunkt des Zusatzmetalls, die thermischen Eigenschaften der Grundmetalle und die gewünschte Verbindungsfestigkeit spielen alle eine Rolle bei der Bestimmung der optimalen Löttemperatur.
Wichtige Punkte erklärt:
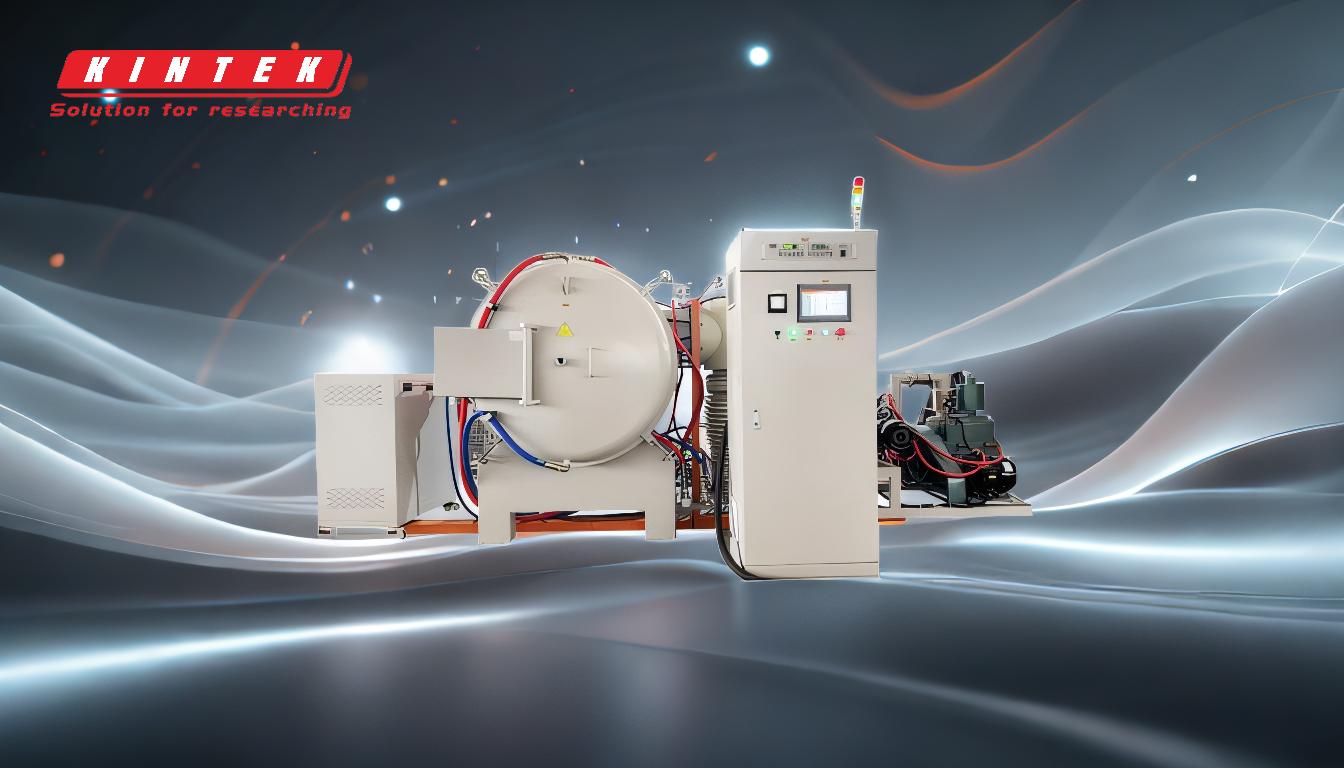
-
Definition und Prozess des Hartlötens:
- Beim Hartlöten handelt es sich um einen Metallverbindungsprozess, bei dem ein Füllmetall geschmolzen und in die Verbindung zwischen zwei oder mehr Grundmetallen eingeflossen wird.
- Das Zusatzmetall hat einen niedrigeren Schmelzpunkt als die Grundmetalle und stellt so sicher, dass die Grundmetalle während des Prozesses nicht schmelzen.
-
Temperaturbereich zum Hartlöten:
- Das Hartlöten erfolgt typischerweise bei Temperaturen zwischen 450 °C und 1200 °C (840 °F bis 2200 °F).
- Die genaue Temperatur hängt von den zu verbindenden Materialien und der Art des verwendeten Zusatzmetalls ab.
-
Faktoren, die die Löttemperatur beeinflussen:
- Schmelzpunkt des Zusatzmetalls: Das Füllmetall muss bei einer Temperatur schmelzen, die niedriger ist als die der Grundmetalle, aber hoch genug, um einen ordnungsgemäßen Fluss und eine ordnungsgemäße Haftung zu gewährleisten.
- Thermische Eigenschaften unedler Metalle: Die Grundmetalle müssen der Löttemperatur standhalten, ohne sich zu zersetzen oder zu schmelzen.
- Gewünschte Gelenkstärke: Höhere Temperaturen können die Verbindungsfestigkeit verbessern, bergen jedoch das Risiko einer Beschädigung der Grundmetalle.
-
Arten von Zusatzwerkstoffen und ihre Temperaturbereiche:
- Silberbasierte Zusatzmetalle: Wird normalerweise bei Temperaturen zwischen 600 °C und 900 °C (1112 °F und 1652 °F) verwendet.
- Kupferbasierte Zusatzmetalle: Wird häufig bei höheren Temperaturen verwendet, etwa 900 °C bis 1100 °C (1652 °F bis 2012 °F).
- Nickelbasierte Zusatzmetalle: Wird für Hochtemperaturanwendungen mit Löttemperaturen von bis zu 1200 °C (2200 °F) verwendet.
-
Anwendungen des Hochtemperaturlötens:
- Hochtemperaturlöten wird in Branchen wie der Luft- und Raumfahrt, der Automobilindustrie und der Energieerzeugung eingesetzt, wo Verbindungen extremen Bedingungen standhalten müssen.
- Beispiele hierfür sind Turbinenschaufeln, Wärmetauscher und Abgassysteme.
-
Überlegungen zur Auswahl der Löttemperatur:
- Materialkompatibilität: Stellen Sie sicher, dass die Grundmetalle und das Zusatzmetall bei der gewählten Temperatur kompatibel sind.
- Gelenkdesign: Die Gestaltung der Verbindung kann die optimale Löttemperatur beeinflussen.
- Atmosphärenkontrolle: In manchen Fällen ist eine kontrollierte Atmosphäre (z. B. Vakuum oder Inertgas) erforderlich, um Oxidation zu verhindern und eine starke Verbindung sicherzustellen.
-
Sicherheits- und Ausrüstungsanforderungen:
- Das Hochtemperaturlöten erfordert spezielle Geräte wie Öfen oder Brenner, die in der Lage sind, die erforderlichen Temperaturen zu erreichen und aufrechtzuerhalten.
- Sicherheitsvorkehrungen, einschließlich angemessener Belüftung und Schutzausrüstung, sind unerlässlich, um Bediener vor hohen Temperaturen und Dämpfen zu schützen.
Wenn Sie diese Schlüsselpunkte verstehen, können Sie die geeignete Löttemperatur für Ihre spezifische Anwendung bestimmen und so eine starke und dauerhafte Verbindung gewährleisten und gleichzeitig das Risiko einer Beschädigung der Grundmetalle minimieren.
Übersichtstabelle:
Aspekt | Einzelheiten |
---|---|
Temperaturbereich | 450 °C bis 1200 °C (840 °F bis 2200 °F) |
Arten von Zusatzwerkstoffen | Silberbasis (600 °C–900 °C), Kupferbasis (900 °C–1100 °C), Nickelbasis (bis 1200 °C) |
Schlüsselfaktoren | Schmelzpunkt des Zusatzmetalls, thermische Eigenschaften der Grundmetalle, Verbindungsfestigkeit |
Anwendungen | Luft- und Raumfahrt, Automobil, Energieerzeugung (z. B. Turbinenschaufeln, Wärmetauscher) |
Sicherheit und Ausrüstung | Spezialöfen oder Fackeln, ausreichende Belüftung und Schutzausrüstung |
Benötigen Sie Hilfe bei der Bestimmung der richtigen Löttemperatur für Ihr Projekt? Kontaktieren Sie noch heute unsere Experten!