Die Schnellpyrolyse ist ein Verfahren, bei dem Biomasse durch Erhitzen auf hohe Temperaturen (400-700 °C) in Abwesenheit von Sauerstoff bei sehr kurzen Verweilzeiten (weniger als 2 Sekunden) in Bioöl, Biokohle und Gase umgewandelt wird.Die Partikelgröße des Ausgangsmaterials ist entscheidend, da die meisten Pyrolysetechnologien nur Partikel bis maximal 2 mm verarbeiten können, um eine schnelle Wärmeübertragung zu gewährleisten.Diese geringe Partikelgröße ist für die Erzielung der hohen Erhitzungs- und Wärmeübertragungsraten, die für eine schnelle Pyrolyse erforderlich sind, von entscheidender Bedeutung. Dadurch wird die Ausbeute an Bioöl maximiert (bis zu 65-80 % auf Basis der trockenen Beschickung).Das Verfahren ist hocheffizient, erfordert jedoch eine präzise Steuerung von Temperatur und Verweilzeit, um die Produktausbeute zu optimieren.
Die wichtigsten Punkte erklärt:
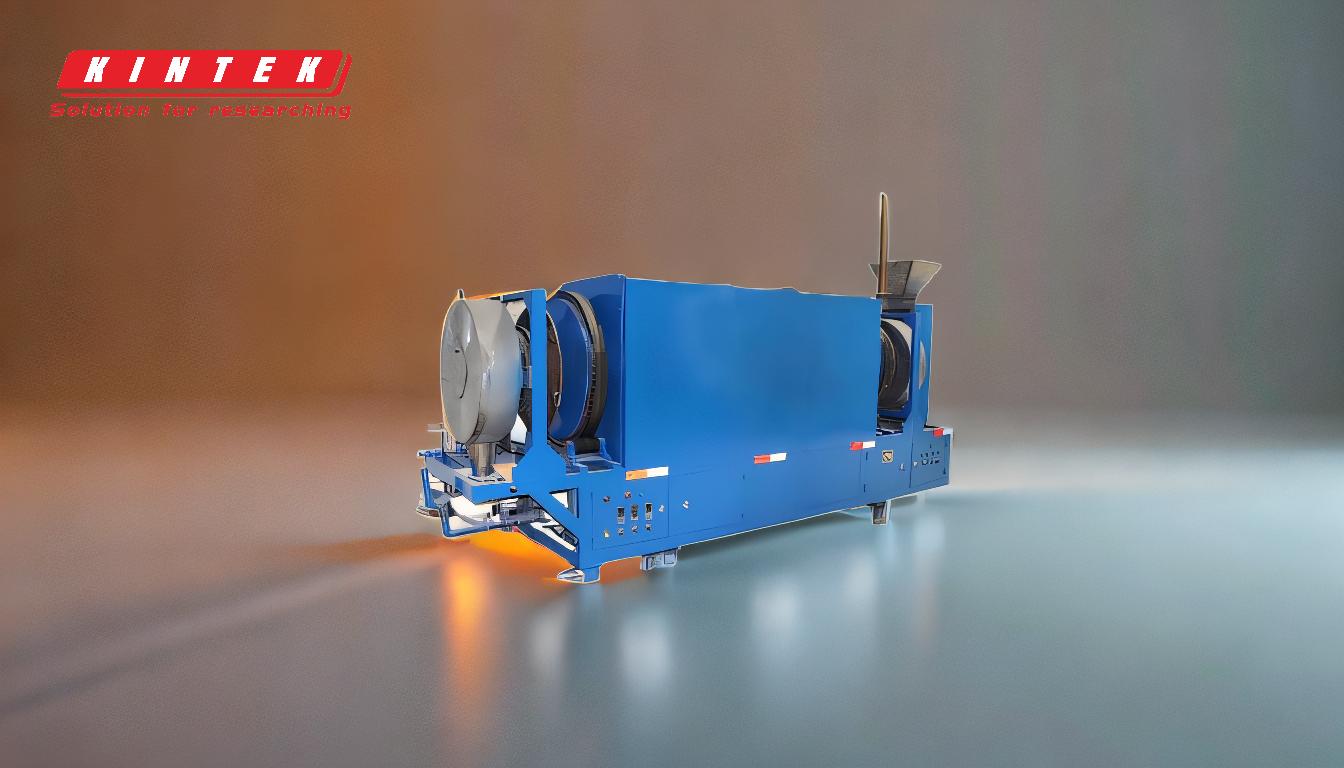
-
Partikelgröße bei der Schnellpyrolyse:
- Die Partikelgröße des Ausgangsmaterials bei der Schnellpyrolyse ist in der Regel begrenzt auf 2 mm oder kleiner .Dies gewährleistet eine schnelle Wärmeübertragung durch die Partikel, was für das Erreichen der für den Prozess erforderlichen hohen Heizraten (10-200 °C/s) und kurzen Verweilzeiten (0,5-10 Sekunden) entscheidend ist.
- Größere Partikel würden die Wärmeübertragung behindern, was zu einer unvollständigen Pyrolyse und einer geringeren Ausbeute an Bioöl und anderen Produkten führen würde.
-
Bedeutung der kleinen Partikelgröße:
- Kleine Partikel ermöglichen eine gleichmäßige Erwärmung Dadurch wird sichergestellt, dass die gesamte Biomasse effizient pyrolysiert wird.
- Sie ermöglichen schnelle Wärmeübertragung was notwendig ist, um die für die Schnellpyrolyse charakteristischen hohen Heizraten zu erreichen.
- Kleine Partikel minimieren auch das Risiko von Nebenreaktionen, die die Qualität des Bioöls beeinträchtigen können.
-
Prozessbedingungen bei der Schnellpyrolyse:
- Temperatur:Die Schnellpyrolyse erfolgt bei moderaten Temperaturen (400-700°C).Niedrigere Temperaturen (bis zu 650°C) maximieren die Ausbeute an kondensierbaren Dämpfen (Bioöl), während höhere Temperaturen (über 700°C) die Gasproduktion begünstigen.
- Verweilzeit:Die Verweilzeit bei der Pyrolysetemperatur ist sehr kurz, in der Regel weniger als 2 Sekunden.Diese schnelle Verarbeitung verhindert den Zerfall des Bioöls in Gase und Holzkohle.
- Heizraten:Hohe Heizraten (10-200°C/s) sind für eine schnelle Pyrolyse unerlässlich, da sie eine schnelle Zersetzung der Biomasse in Dämpfe gewährleisten, die dann zu Bioöl kondensiert werden.
-
Produktausbeute:
- Die Schnellpyrolyse ist optimiert für hohe Ausbeuten an Bio-Öl Die Ausbeute an Bioöl liegt in der Regel zwischen 50 und 80 % auf Basis der trockenen Biomasse.
- Zu den übrigen Produkten gehören Biokohle (fester Rückstand) und nicht kondensierbare Gase (wie Methan, Wasserstoff und Kohlenmonoxid).
-
Vergleich mit anderen Pyrolyseverfahren:
- Langsame Pyrolyse:Arbeitet bei niedrigeren Temperaturen (<500°C) und langsameren Heizraten (0,1-2°C/s), mit längeren Verweilzeiten (Stunden bis Tage).Sie erzeugt in erster Linie Holzkohle und Teer, wobei die Ausbeute an Bioöl geringer ist.
- Ultraschnelle Pyrolyse:Noch höhere Erhitzungsraten und kürzere Verweilzeiten als bei der Schnellpyrolyse, was die Gaserzeugung begünstigt.Sie ähnelt eher der Vergasung.
- Flash-Pyrolyse:Eine Variante der Schnellpyrolyse mit noch höheren Heizraten, bei der Bioölausbeuten von bis zu 75-80 Gew.-% erreicht werden.
-
Anwendungen der Schnellpyrolyse:
- Das erzeugte Bioöl kann als Brennstoff in Kesseln, Motoren und Turbinen.
- Es kann auch als Quelle für Quelle für chemische Grundstoffe Allerdings muss es für die Verwendung als Kraftstoff oft weiter raffiniert und aufbereitet werden.
-
Herausforderungen und Überlegungen:
- Die erforderliche geringe Partikelgröße (≤2 mm) erfordert eine Vorverarbeitung der Biomasse Die Vorverarbeitung von Biomasse, wie z. B. das Mahlen oder Zerkleinern, erhöht die Kosten und den Energieaufwand des Prozesses.
- Das erzeugte Bioöl enthält oft Wasser, Säuren und andere Verunreinigungen, die eine Nachbearbeitung um seine Stabilität und Qualität zu verbessern.
Zusammenfassend lässt sich sagen, dass die Partikelgröße bei der Schnellpyrolyse ein kritischer Faktor ist. Bei den meisten Technologien sind Partikel von ≤2 mm erforderlich, um eine effiziente Wärmeübertragung und hohe Bioölerträge zu gewährleisten.Das Verfahren arbeitet bei moderaten Temperaturen (400-700 °C) mit sehr kurzen Verweilzeiten (<2 Sekunden) und hohen Heizraten (10-200 °C/s), was es für die Bioölproduktion sehr effizient macht.Der Bedarf an kleinen Partikelgrößen und die mit der Bioölqualität verbundenen Herausforderungen machen jedoch deutlich, wie wichtig es ist, sowohl die Vor- als auch die Nachbehandlungsschritte bei der Schnellpyrolyse zu optimieren.
Zusammenfassende Tabelle:
Hauptaspekt | Einzelheiten |
---|---|
Partikelgröße | ≤2 mm für schnelle Wärmeübertragung und gleichmäßige Erwärmung. |
Temperaturbereich | 400-700°C; niedrigere Temperaturen begünstigen Bioöl, höhere Temperaturen begünstigen die Gasproduktion. |
Verweilzeit | <2 Sekunden, um einen Abbau des Bioöls zu verhindern. |
Heizraten | 10-200°C/s für schnellen Biomasseabbau. |
Bio-Öl-Ausbeute | 50-80% auf Basis der trockenen Biomasse. |
Andere Produkte | Biokohle und nicht kondensierbare Gase (z. B. Methan, Wasserstoff, Kohlenmonoxid). |
Anwendungen | Bioöl wird als Brennstoff oder chemischer Rohstoff verwendet; für den Transport ist eine Raffination erforderlich. |
Herausforderungen | Vorverarbeitung (Zerkleinerung) und Nachverarbeitung (Stabilisierung des Bioöls). |
Entdecken Sie, wie die Schnellpyrolyse Ihre Biomasse in wertvolle Produkte umwandeln kann. Kontaktieren Sie uns noch heute für fachkundige Beratung!