Spark-Plasma-Sintern (SPS) ist eine fortschrittliche Sintertechnik, die für ihre schnellen Aufheizraten, hohen Sintertemperaturen und gleichmäßigen Erwärmung bekannt ist und die Herstellung dichter Sinterkörper in kurzer Zeit ermöglicht. Der beim SPS ausgeübte Druck ist ein kritischer Parameter, der die Verdichtung und die mechanischen Eigenschaften des Endprodukts beeinflusst. Typischerweise liegt der Druck zwischen 20 MPa und 100 MPa, abhängig vom zu sinternden Material und den gewünschten Eigenschaften. Höhere Drücke werden häufig für Materialien verwendet, die schwerer zu verdichten sind, während niedrigere Drücke für leichter zu sinternde Materialien ausreichen können. Die Kombination von Druck und gepulstem elektrischem Strom bei SPS erleichtert die Partikelumlagerung, plastische Verformung und Diffusion, was zu einer verbesserten Verdichtung und verbesserten Materialeigenschaften führt.
Wichtige Punkte erklärt:
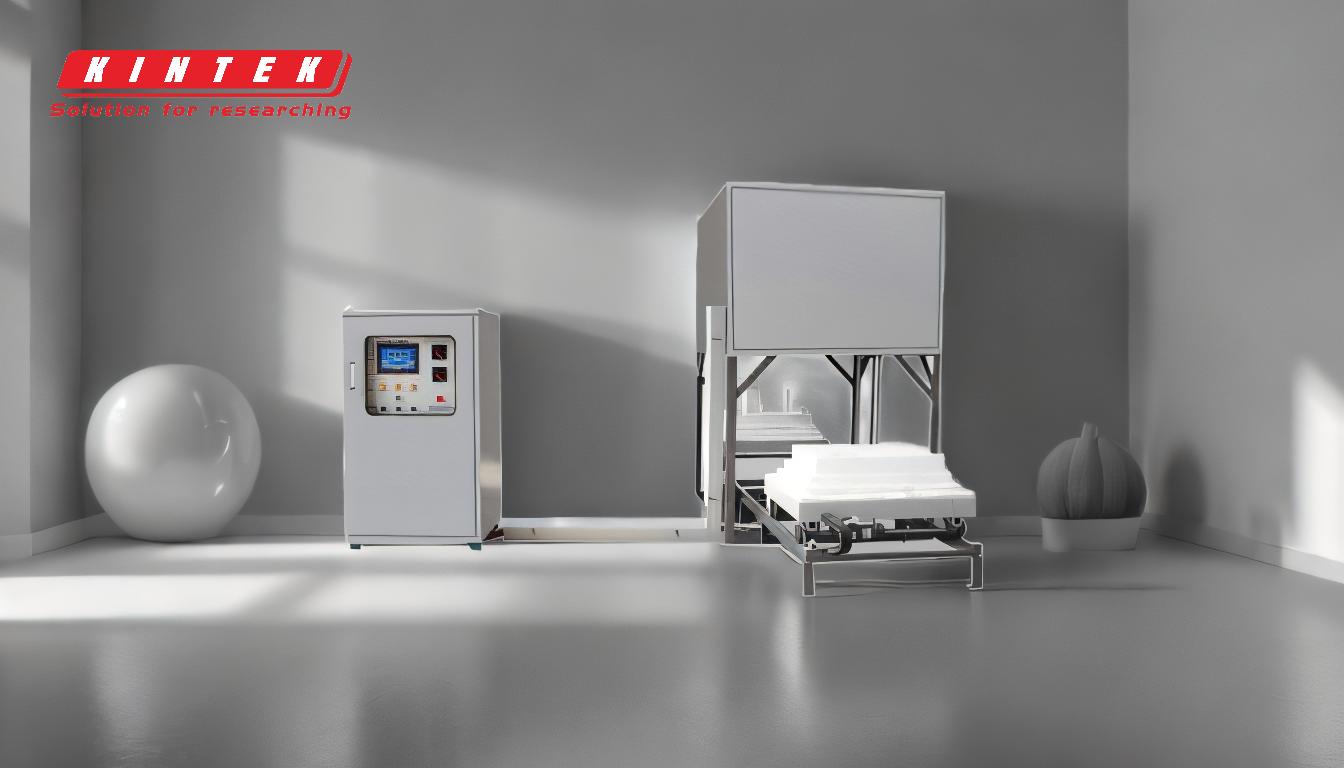
-
Druckbereich in SPS:
- Der beim Spark-Plasma-Sintern angewendete Druck liegt typischerweise im Bereich von 20 MPa bis 100 MPa .
- Dieser Bereich wird auf der Grundlage der Materialeigenschaften wie Härte und Schmelzpunkt sowie der gewünschten Dichte und mechanischen Eigenschaften des Endprodukts ausgewählt.
- Für Materialien, die sich leicht verdichten, reichen oft niedrigere Drücke (20–50 MPa) aus, während für härtere oder feuerfestere Materialien höhere Drücke (50–100 MPa) erforderlich sind.
-
Rolle des Drucks bei SPS:
- Partikelumlagerung: Druck hilft in der Anfangsphase des Sinterns, indem er die Neuordnung der Partikel fördert, was für die Erzielung einer gleichmäßigen und dichten Mikrostruktur entscheidend ist.
- Plastische Verformung: Höhere Drücke induzieren eine plastische Verformung der Partikel, insbesondere bei erhöhten Temperaturen, was dazu beiträgt, Poren zu schließen und die Verdichtung zu verbessern.
- Diffusionsverbesserung: Druck beschleunigt in Kombination mit dem gepulsten elektrischen Strom Diffusionsprozesse, was zu einer schnelleren Korngrenzenmigration und einer verbesserten Sinterkinetik führt.
-
Faktoren, die die Druckauswahl beeinflussen:
- Materialtyp: Unterschiedliche Materialien erfordern je nach Härte, Schmelzpunkt und Sinterverhalten unterschiedliche Drücke. Beispielsweise können bei Keramik im Vergleich zu Metallen höhere Drücke erforderlich sein.
- Gewünschte Dichte: Die Zieldichte des Sinterkörpers beeinflusst die Druckwahl. Höhere Dichten erfordern oft höhere Drücke.
- Temperatur: Die Sintertemperatur und der angewandte Druck hängen zusammen. Höhere Temperaturen können manchmal niedrigere Drücke ausgleichen, die optimale Kombination muss jedoch experimentell ermittelt werden.
-
Einfluss von Druck auf die Endeigenschaften:
- Mechanische Eigenschaften: Der beim SPS ausgeübte Druck beeinflusst die mechanischen Eigenschaften des Sintermaterials wie Härte, Festigkeit und Zähigkeit erheblich.
- Mikrostruktur: Der Druck beeinflusst die Korngröße und Porosität des Sinterkörpers, was wiederum Auswirkungen auf seine mechanischen und thermischen Eigenschaften hat.
- Dichte: Höhere Drücke führen im Allgemeinen zu höheren Dichten, die für Anwendungen, die eine hohe Festigkeit und Haltbarkeit erfordern, von entscheidender Bedeutung sind.
-
Praktische Überlegungen:
- Ausrüstungsfähigkeit: Der maximale Druck, der angewendet werden kann, wird durch die Fähigkeiten der SPS-Ausrüstung begrenzt. Benutzer müssen sicherstellen, dass ihre Ausrüstung den erforderlichen Drücken standhält.
- Sicherheit: Hohe Drücke und Temperaturen erfordern eine sorgfältige Handhabung, um die Sicherheit während des Sinterprozesses zu gewährleisten.
- Kosten: Höhere Drücke können die Kosten des Sinterprozesses erhöhen, da robustere Geräte und längere Verarbeitungszeiten erforderlich sind.
Zusammenfassend lässt sich sagen, dass der beim Spark-Plasma-Sintern angewendete Druck ein kritischer Parameter ist, der sorgfältig auf der Grundlage der Materialeigenschaften, der gewünschten Endeigenschaften und praktischer Überlegungen ausgewählt werden muss. Der typische Druckbereich von 20–100 MPa ermöglicht die Herstellung dichter, hochwertiger Sinterkörper mit verbesserten mechanischen Eigenschaften.
Übersichtstabelle:
Aspekt | Einzelheiten |
---|---|
Druckbereich | 20 MPa bis 100 MPa, je nach Material und gewünschten Eigenschaften. |
Rolle des Drucks | Erleichtert die Neuanordnung, plastische Verformung und Diffusion von Partikeln. |
Einflussfaktoren | Materialtyp, gewünschte Dichte und Sintertemperatur. |
Auswirkungen auf Eigenschaften | Beeinflusst mechanische Eigenschaften, Mikrostruktur und Dichte. |
Praktische Überlegungen | Ausrüstungsfähigkeit, Sicherheit und Kosten. |
Sind Sie bereit, Ihren Spark-Plasma-Sinterprozess zu optimieren? Kontaktieren Sie noch heute unsere Experten für maßgeschneiderte Lösungen!