PVD (Physical Vapor Deposition) arbeitet unter Vakuumbedingungen, um eine hochwertige Dünnschichtabscheidung zu gewährleisten.Der Vakuumdruck in PVD-Systemen liegt in der Regel unter 10^-5 Torr, was für die Minimierung von Verunreinigungen und die Optimierung des Abscheidungsprozesses unerlässlich ist.Diese Niederdruckumgebung erhöht die mittlere freie Weglänge von Atomen und Ionen, verringert die gasförmige Verunreinigung und beeinflusst die Energieverteilung des Plasmas.Der Vakuumdruck ist entscheidend für die Steuerung der Verdampfung, des Transports und der Kondensation des Zielmaterials und gewährleistet eine effiziente und defektfreie Dünnschichtbildung.Faktoren wie die Sauberkeit des Systems, Ausgasungen und Leckageraten spielen ebenfalls eine wichtige Rolle bei der Aufrechterhaltung des erforderlichen Vakuumniveaus.
Die wichtigsten Punkte erklärt:
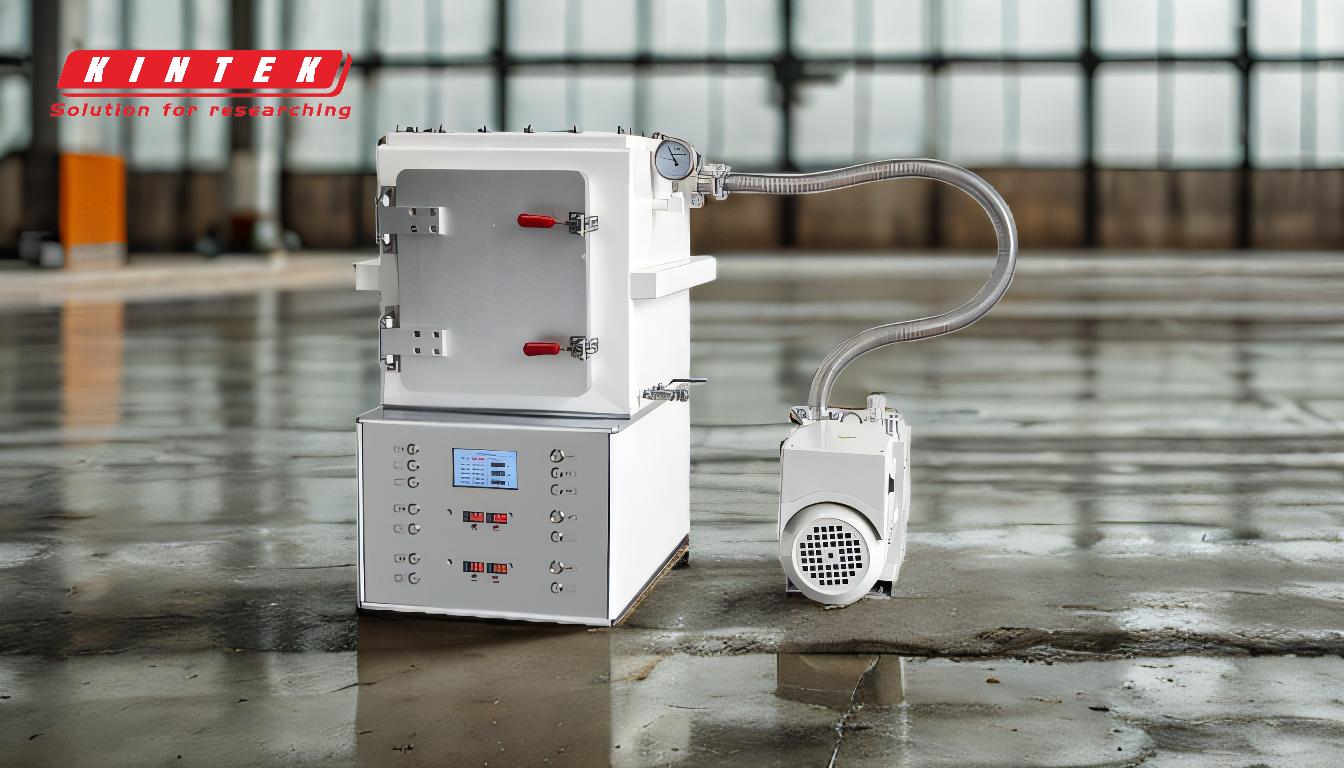
-
Vakuumdruckbereich bei PVD:
- PVD-Verfahren erfordern eine Vakuumumgebung mit einem Druck von in der Regel weniger als 10^-5 Torr.
- Dieser niedrige Druck ist notwendig, um Verunreinigungen zu minimieren und eine hochwertige Dünnschichtabscheidung zu gewährleisten.
- Die Vakuumumgebung vergrößert die mittlere freie Weglänge von Atomen und Ionen, wodurch Kollisionen und gasförmige Verunreinigungen verringert werden.
-
Die Rolle des Vakuums bei PVD-Prozessen:
- Die Vakuumumgebung ist entscheidend für die ordnungsgemäße Verdampfung, den Transport und die Kondensation des Zielmaterials.
- Es beeinflusst die Enthalpie, die Dichte der geladenen und ungeladenen Teilchen und die Energieverteilung im Plasma.
- Ein gut aufrechterhaltenes Vakuum gewährleistet eine effiziente und fehlerfreie Dünnschichtbildung.
-
Faktoren, die das Vakuumniveau beeinflussen:
- Ausgasen:In die Vakuumkammer eingeführte Materialien können Gase freisetzen, die das Vakuumniveau beeinträchtigen.
- Leckagerate:Die Unversehrtheit der Dichtungen des Vakuumsystems hat Auswirkungen auf die Fähigkeit, einen niedrigen Druck aufrechtzuerhalten.
- Sauberkeit:Verunreinigungen in der Kammer können die Vakuumqualität beeinträchtigen.
- Umgebungsbedingungen:Luftfeuchtigkeit und Temperatur können die Leistung des Vakuumsystems beeinflussen.
-
Einfluss des Drucks auf die Abscheidung:
- Hoher Druck:Erhöht die Reaktionsgeschwindigkeit, verringert aber die mittlere freie Weglänge, was die Filmbildung auf den Stufen behindert.
- Niedriger Druck:Verringert die Filmdichte und kann zu Defekten wie nadelartigen Strukturen führen.
- Optimaler Druck:Sorgt für ein Gleichgewicht zwischen Abscheiderate und Schichtqualität und gewährleistet gleichmäßige und dichte dünne Schichten.
-
Wechselwirkung von Plasma und Druck:
- Höherer Gasdruck erhöht die Konzentration der Reaktionsgase und steigert die Abscheidungsrate.
- Ein zu hoher Druck kann jedoch die Plasmapolymerisation verstärken, wodurch die Gleichmäßigkeit des Wachstumsnetzwerks verringert und Defekte verstärkt werden.
- Die Aufrechterhaltung des richtigen Drucks ist für die Kontrolle des Plasmaverhaltens und die Gewährleistung eines qualitativ hochwertigen Schichtwachstums von entscheidender Bedeutung.
-
Moderne Vakuumsystemregelung:
- Moderne PVD-Systeme regulieren die Vakuumtiefe als Schlüsselvariable, um die gewünschten Ergebnisse zu erzielen.
- Der erforderliche Druck kann je nach Anwendung und verwendetem Material erheblich variieren.
- Moderne Systeme sind so konzipiert, dass sie ein präzises Vakuumniveau aufrechterhalten und somit gleichbleibende und hochwertige Beschichtungsprozesse gewährleisten.
-
Vorteile der PVD-Vakuum-Beschichtung:
- PVD-Vakuumbeschichtungsanlagen sind für ihre hohe Beschichtungsgeschwindigkeit und niedrige Beschichtungstemperatur bekannt.
- Sie verwenden umweltfreundliche physikalische Mittel und eignen sich daher für die Beschichtung von Präzisions- und komplexen Werkzeugen.
- Die Vakuumumgebung gewährleistet eine minimale Verunreinigung und eine qualitativ hochwertige Abscheidung von Dünnschichten.
Wenn die Hersteller den Vakuumdruck in PVD-Systemen kennen und kontrollieren, können sie den Abscheidungsprozess optimieren und hochwertige, fehlerfreie Dünnschichten für verschiedene Anwendungen sicherstellen.
Zusammenfassende Tabelle:
Hauptaspekt | Einzelheiten |
---|---|
Vakuum-Druckbereich | Unter 10^-5 Torr für minimale Verunreinigung und optimale Ablagerung. |
Die Rolle des Vakuums | Steuert die Verdampfung, den Transport und die Kondensation des Zielmaterials. |
Faktoren, die das Vakuum beeinflussen | Ausgasung, Leckagerate, Sauberkeit und Umgebungsbedingungen. |
Auswirkung von Druck | Hoher Druck verringert die mittlere freie Weglänge; niedriger Druck verursacht Defekte. |
Plasma-Interaktion | Höherer Druck erhöht die Abscheiderate, kann aber zu mehr Defekten führen. |
Moderne Regulierung | Hochentwickelte Systeme sorgen für ein präzises Vakuumniveau und damit für gleichbleibende Ergebnisse. |
Vorteile der PVD-Beschichtung | Schnelle Abscheidung, niedrige Temperaturen und umweltfreundliche Prozesse. |
Sind Sie bereit, Ihren PVD-Prozess zu optimieren? Kontaktieren Sie uns noch heute für fachkundige Beratung!