Beim Heißsintern handelt es sich um einen Herstellungsprozess, bei dem aus pulverförmigen Materialien durch Anwendung von Wärme feste Objekte hergestellt werden, ohne dass das Material vollständig schmilzt. Dieses Verfahren wird in Branchen wie Metallurgie, Keramik und Zahnmedizin häufig eingesetzt, um Komponenten mit hoher Festigkeit, Haltbarkeit und Wärmebeständigkeit herzustellen. Der Prozess umfasst mehrere Schritte, einschließlich Pulvervorbereitung, Verdichtung und kontrolliertes Erhitzen in einem Sinterofen , und Kühlung. Der Schlüssel zum erfolgreichen Sintern liegt in der präzisen Temperaturkontrolle, die eine Partikelbindung und -verdichtung ohne Verflüssigung gewährleistet. Nachfolgend finden Sie eine detaillierte Erläuterung des Heißsinterprozesses.
Wichtige Punkte erklärt:
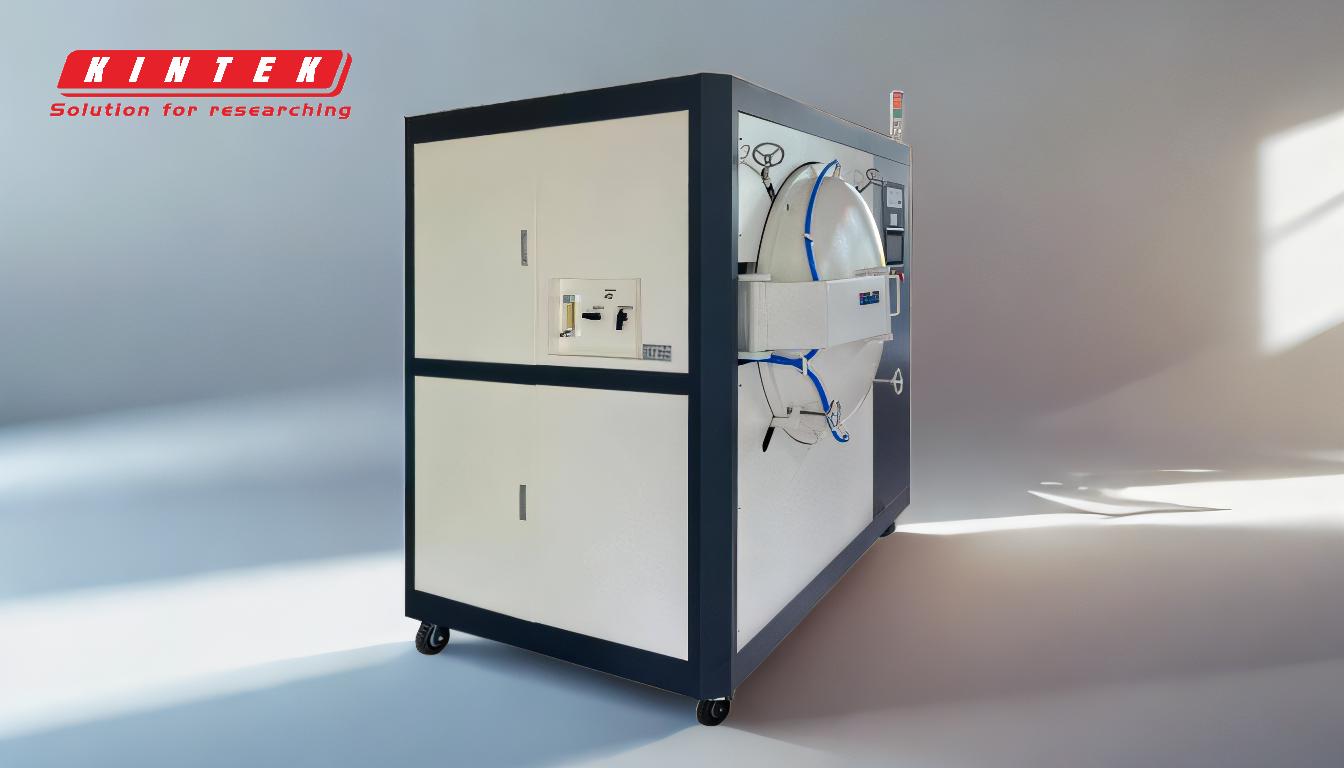
-
Vorbereitung des Pulverkompakts
- Der Prozess beginnt mit der Aufbereitung des Rohmaterials, typischerweise in Pulverform. Dieses Pulver kann durch verschiedene Methoden wie Kaltschweißen, 3D-Druck oder Presswerkzeuge hergestellt werden.
- Anschließend wird das Pulver durch Druck in eine bestimmte Form verdichtet, um Gleichmäßigkeit zu gewährleisten und Hohlräume zu vermeiden. Dieser Schritt ist entscheidend für das Erreichen der gewünschten Dichte und strukturellen Integrität im Endprodukt.
- Die Verdichtung kann je nach Material und Anwendung bei Raumtemperatur oder unter erhitzten Bedingungen erfolgen.
-
Erwärmung und Konsolidierung
- Das verdichtete Pulver wird in einen Sinterofen Dabei wird es auf eine Temperatur knapp unter dem Schmelzpunkt des Materials erhitzt. Diese Temperatur ist entscheidend, da sie die Atomdiffusion über Partikelgrenzen hinweg aktiviert.
- In diesem Stadium beginnen sich die Partikel durch einen Prozess namens Halsbildung zu verbinden, bei dem Material von den Partikeloberflächen zu den Kontaktpunkten zwischen Partikeln diffundiert.
- Bei einigen Materialien kann Flüssigphasensintern (LPS) verwendet werden, um den Verdichtungsprozess zu beschleunigen. Bei LPS bildet sich an den Partikelgrenzen eine kleine Menge flüssiger Phase, wodurch die Partikelverschmelzung verbessert und die Porosität verringert wird.
-
Partikelverschmelzung und -verdichtung
- Mit steigender Temperatur verdichten und verschmelzen die Partikel, wodurch die Gesamtporosität des Materials abnimmt. Dieser Schritt ist für die Erzielung der gewünschten mechanischen Eigenschaften wie Festigkeit und thermische Beständigkeit von entscheidender Bedeutung.
- Der Grad der Verdichtung hängt von Faktoren wie Temperatur, Zeit und den Materialeigenschaften ab. Die genaue Kontrolle dieser Parameter gewährleistet optimale Ergebnisse.
-
Erstarrung und Abkühlung
- Nach der Erhitzungsphase lässt man das Material allmählich abkühlen. Durch diesen Abkühlungsprozess verfestigt sich das gesinterte Produkt zu einer einzigen, einheitlichen Masse.
- Die Kühlung muss kontrolliert werden, um thermische Spannungen zu verhindern, die zu Rissen oder Verformungen führen könnten.
- Das Endprodukt weist eine starre und zusammenhängende Struktur mit hoher Maßgenauigkeit und mechanischer Festigkeit auf.
-
Temperaturkontrolle beim Sintern
- Die Temperatur ist ein entscheidender Faktor im Sinterprozess. Er muss hoch genug sein, um die Atomdiffusion und Partikelbindung zu erleichtern, aber unter dem Schmelzpunkt des Materials bleiben, um eine Verflüssigung zu vermeiden.
- Zu den wichtigsten Temperaturkontrollpunkten gehören die Zündtemperatur, die Endtemperatur und die Abgastemperatur. Diese werden sorgfältig überwacht, um ein ordnungsgemäßes Sintern und eine qualitativ hochwertige Ausgabe zu gewährleisten.
- Fortschrittliche Sinteröfen sind mit präzisen Temperaturkontrollsystemen ausgestattet, um konstante Heiz- und Kühlraten aufrechtzuerhalten.
-
Anwendungen des Sinterns
- Sintern wird in verschiedenen Branchen eingesetzt, darunter in der Metallurgie zur Herstellung von Metallkomponenten, in der Keramik zur Herstellung temperaturbeständiger Materialien und in der Zahnmedizin zur Verarbeitung von Kronen und Brücken aus Zirkonoxid.
- In der Zahnheilkunde werden spezielle Dentalsinteröfen eingesetzt, um die extrem hohen Temperaturen zu erreichen, die zum Sintern von Zirkonoxid auf seine Endhärte erforderlich sind.
-
Vorteile des Sinterns
- Sintern ermöglicht die Herstellung komplexer Formen mit hoher Präzision und minimalem Materialabfall.
- Es verbessert Materialeigenschaften wie Festigkeit, Wärmebeständigkeit und Haltbarkeit.
- Der Prozess ist kostengünstig und für die Massenproduktion skalierbar.
Durch das Verständnis der Phasen und Prinzipien des Heißsinterns können Hersteller den Prozess optimieren, um hochwertige Komponenten herzustellen, die auf bestimmte Anwendungen zugeschnitten sind. Die Verwendung von fortgeschrittenen Sinteröfen und präzise Temperaturkontrollsysteme sorgen für konsistente und zuverlässige Ergebnisse.
Übersichtstabelle:
Bühne | Beschreibung |
---|---|
Pulverzubereitung | Der Rohstoff wird in Pulverform aufbereitet und in eine bestimmte Form verdichtet. |
Heizung und Konsolidierung | Verdichtetes Pulver wird unter den Schmelzpunkt erhitzt, um die Partikelbindung zu aktivieren. |
Partikelverschmelzung | Partikel verdichten und verschmelzen, wodurch die Porosität verringert und die Materialfestigkeit erhöht wird. |
Kühlung | Durch kontrollierte Abkühlung verfestigt sich das Material zu einem zusammenhängenden, hochfesten Produkt. |
Temperaturkontrolle | Präzises Temperaturmanagement sorgt für optimale Verdichtung und vermeidet Verflüssigung. |
Anwendungen | Wird in der Metallurgie, Keramik und Zahnmedizin für Hochleistungskomponenten verwendet. |
Vorteile | Erzeugt komplexe Formen mit minimalem Abfall, erhöht die Festigkeit und ist kostengünstig. |
Entdecken Sie, wie Heißsintern Ihren Herstellungsprozess revolutionieren kann – Kontaktieren Sie noch heute unsere Experten für weitere Informationen!