Das Lasersintern, auch bekannt als selektives Lasersintern (SLS), ist ein fortschrittliches additives Fertigungsverfahren, bei dem ein Hochleistungslaser verwendet wird, um pulverförmiges Material zu einer festen dreidimensionalen Struktur zu verschmelzen.Dieser Prozess wird durch eine computergestützte Konstruktionsdatei (CAD) gesteuert, die den Laser anweist, das Material selektiv an bestimmten Punkten Schicht für Schicht zu binden, um das endgültige Teil herzustellen.Im Gegensatz zu herkömmlichen Sinterverfahren sind beim Lasersintern keine Formen oder Gesenke erforderlich, und es können hochkomplexe Geometrien mit minimalem Materialabfall hergestellt werden.Das Verfahren umfasst die Aufbereitung des Pulvers, das selektive Verschmelzen mit einem Laser und die Nachbearbeitung des fertigen Teils, um die gewünschten Eigenschaften zu erzielen.
Die wichtigsten Punkte werden erklärt:
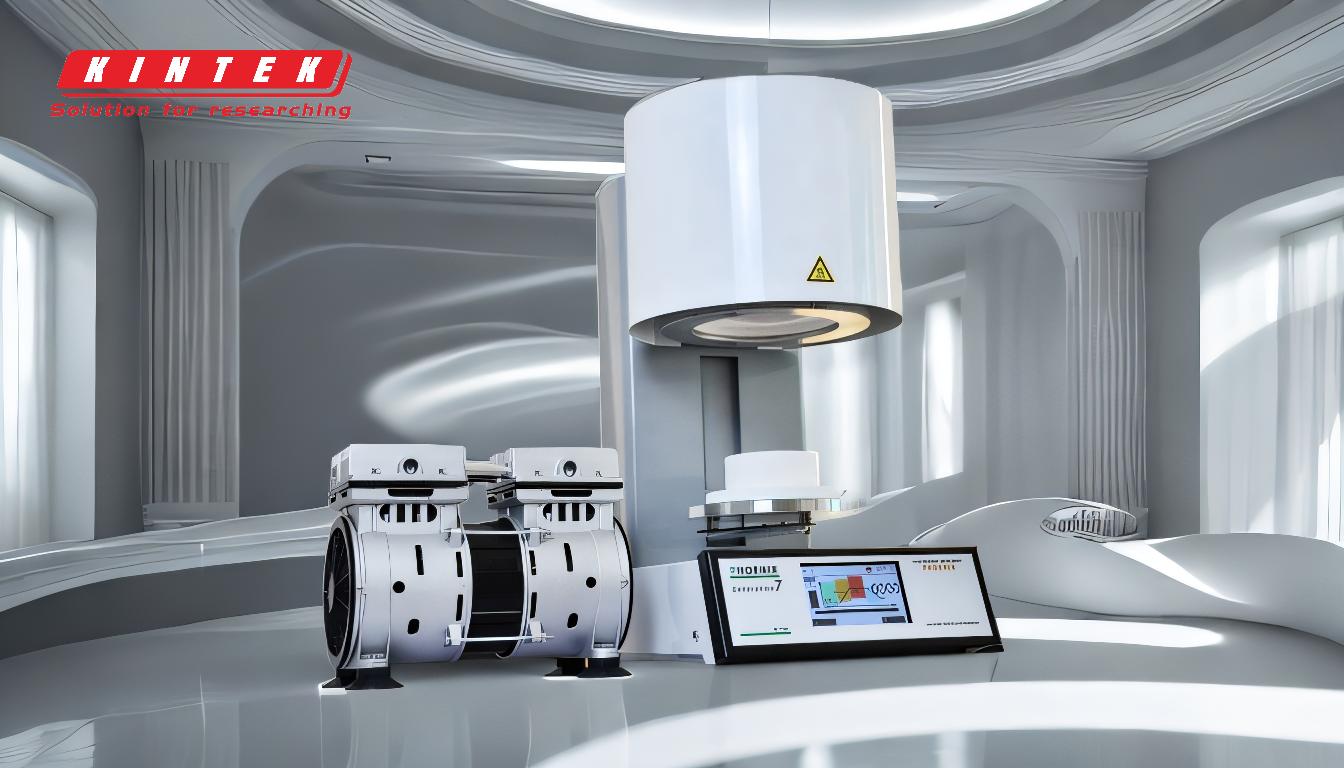
-
Vorbereitung des Pulvermaterials:
- Der Prozess beginnt mit der Vorbereitung des pulverförmigen Materials, das aus Metall, Polymer, Keramik oder Verbundwerkstoff bestehen kann.Das Pulver muss bestimmte Eigenschaften aufweisen, z. B. Partikelgröße und Fließfähigkeit, um eine gleichmäßige Ausbreitung und ein effektives Sintern zu gewährleisten.
- Das Pulver wird in einer dünnen Schicht über eine Bauplattform in der Sintermaschine verteilt.Ein Rückstreichmesser oder eine Walze sorgen für eine gleichmäßige Verteilung des Pulvers.
-
Prozess des Lasersinterns:
- Ein Hochleistungslaser, in der Regel ein CO2- oder Faserlaser, wird zum selektiven Verschmelzen der Pulverpartikel eingesetzt.Der Laser wird anhand einer CAD-Datei gesteuert, in der die genauen Punkte angegeben sind, an denen das Material verbunden werden soll.
- Der Laser erhitzt das Pulver bis knapp unter seinen Schmelzpunkt, wodurch die Partikel zusammenwachsen und eine feste Schicht bilden.Der Vorgang wird Schicht für Schicht wiederholt, bis das gesamte Teil fertig ist.
-
Schicht für Schicht bauen:
- Nachdem jede Schicht gesintert ist, wird die Bauplattform um einen kleinen Schritt abgesenkt und eine neue Pulverschicht über die vorherige Schicht gelegt.Der Laser sintert dann die neue Schicht und verbindet sie mit der darunter liegenden Schicht.
- Dieser iterative Prozess wird fortgesetzt, bis das gesamte Teil fertiggestellt ist.Das ungesinterte Pulver dient während des Aufbaus als Stützstruktur, so dass keine zusätzlichen Stützmaterialien benötigt werden.
-
Abkühlung und Erstarrung:
- Sobald das Teil vollständig hergestellt ist, wird es in der Baukammer abgekühlt.Die Abkühlung ist ein kritischer Schritt, da sie sicherstellt, dass das Teil gleichmäßig erstarrt und die Restspannungen minimiert werden.
- Die Abkühlgeschwindigkeit kann sich auf die Mikrostruktur und die mechanischen Eigenschaften des fertigen Teils auswirken und wird daher sorgfältig kontrolliert.
-
Nachbearbeitung:
- Nach dem Abkühlen wird das Teil aus der Baukammer entnommen, und überschüssiges Pulver wird abgebürstet oder weggeblasen.Je nach Material und Anwendung können weitere Nachbearbeitungsschritte erforderlich sein, z. B. Wärmebehandlung, Oberflächenbehandlung oder maschinelle Bearbeitung.
- Durch die Nachbearbeitung werden die mechanischen Eigenschaften, die Maßhaltigkeit und die Oberflächenqualität des Teils verbessert.
-
Vorteile des Laser-Sinterns:
- Design Freiheit:Das Lasersintern ermöglicht die Herstellung komplexer Geometrien, die mit herkömmlichen Fertigungsmethoden nur schwer oder gar nicht zu erreichen sind.
- Effizienz des Materials:Da es sich um ein additives Verfahren handelt, fällt im Vergleich zu subtraktiven Verfahren wie der maschinellen Bearbeitung nur wenig Abfall an.
- Rapid Prototyping:Das Lasersintern wird häufig für das Rapid Prototyping eingesetzt, da es in der Lage ist, funktionale Teile direkt aus CAD-Dateien herzustellen.
- Anpassungen:Das Verfahren ist ideal für die Herstellung von kundenspezifischen Teilen oder Kleinserien, ohne dass teure Werkzeuge benötigt werden.
-
Anwendungen des Laser-Sinterns:
- Luft- und Raumfahrt:Zur Herstellung leichter, hochfester Bauteile mit komplexen Geometrien.
- Medizinische:Ideal für die Herstellung individueller Implantate, Prothesen und chirurgischer Werkzeuge.
- Automobilindustrie:Für das Prototyping und die Herstellung funktioneller Teile mit geringerem Gewicht und verbesserter Leistung.
- Konsumgüter:Ermöglicht die Herstellung individueller Produkte und komplizierter Designs.
Zusammenfassend lässt sich sagen, dass das Lasersintern ein vielseitiges und effizientes additives Fertigungsverfahren ist, das erhebliche Vorteile in Bezug auf Designflexibilität, Materialeffizienz und schnelle Produktion bietet.Wenn die Hersteller die wichtigsten Schritte und Überlegungen kennen, können sie diese Technologie nutzen, um hochwertige, komplexe Teile für eine Vielzahl von Anwendungen herzustellen.
Zusammenfassende Tabelle:
Wichtige Schritte | Einzelheiten |
---|---|
Vorbereitung des Pulvers | Pulvermaterialien (Metall, Polymer, Keramik) werden für eine gleichmäßige Verteilung vorbereitet. |
Laser-Sintern | Ein Hochleistungslaser verschmilzt Pulverpartikel Schicht für Schicht nach CAD-Vorgaben. |
Schicht-für-Schicht-Aufbau | Jede Schicht wird gesintert und mit der vorherigen verbunden, wodurch das 3D-Teil entsteht. |
Abkühlung und Erstarrung | Das Teil wird gleichmäßig abgekühlt, um Spannungen zu minimieren und eine ordnungsgemäße Erstarrung zu gewährleisten. |
Nachbearbeitung | Überschüssiges Pulver wird entfernt, und die Teile werden einer Wärmebehandlung oder Oberflächenbehandlung unterzogen. |
Vorteile | Designfreiheit, Materialeffizienz, schnelles Prototyping und kundenspezifische Anpassung. |
Anwendungen | Luft- und Raumfahrt, Medizin, Automobil- und Konsumgüterindustrie. |
Sind Sie bereit, das Lasersintern für Ihre Fertigungsanforderungen zu erkunden? Kontaktieren Sie noch heute unsere Experten !