Die PVD-Metallisierung (Physical Vapor Deposition) ist ein hochentwickeltes Verfahren, mit dem dünne Materialschichten auf ein Substrat aufgebracht werden.Dieses Verfahren wird in vielen Branchen eingesetzt, z. B. in der Elektronik, der Optik und der Werkzeugherstellung, um die Eigenschaften von Oberflächen zu verbessern, z. B. Härte, Verschleißfestigkeit und elektrische Leitfähigkeit.Das PVD-Verfahren umfasst in der Regel mehrere wichtige Schritte: Reinigung des Substrats, Erzeugung eines Dampfes aus dem Zielmaterial, Reaktion des Dampfes mit Gasen zur Bildung einer Verbindung und Abscheidung der Verbindung auf dem Substrat.Jeder einzelne Schritt ist entscheidend für die Qualität und Leistungsfähigkeit der endgültigen Beschichtung.
Die wichtigsten Punkte erklärt:
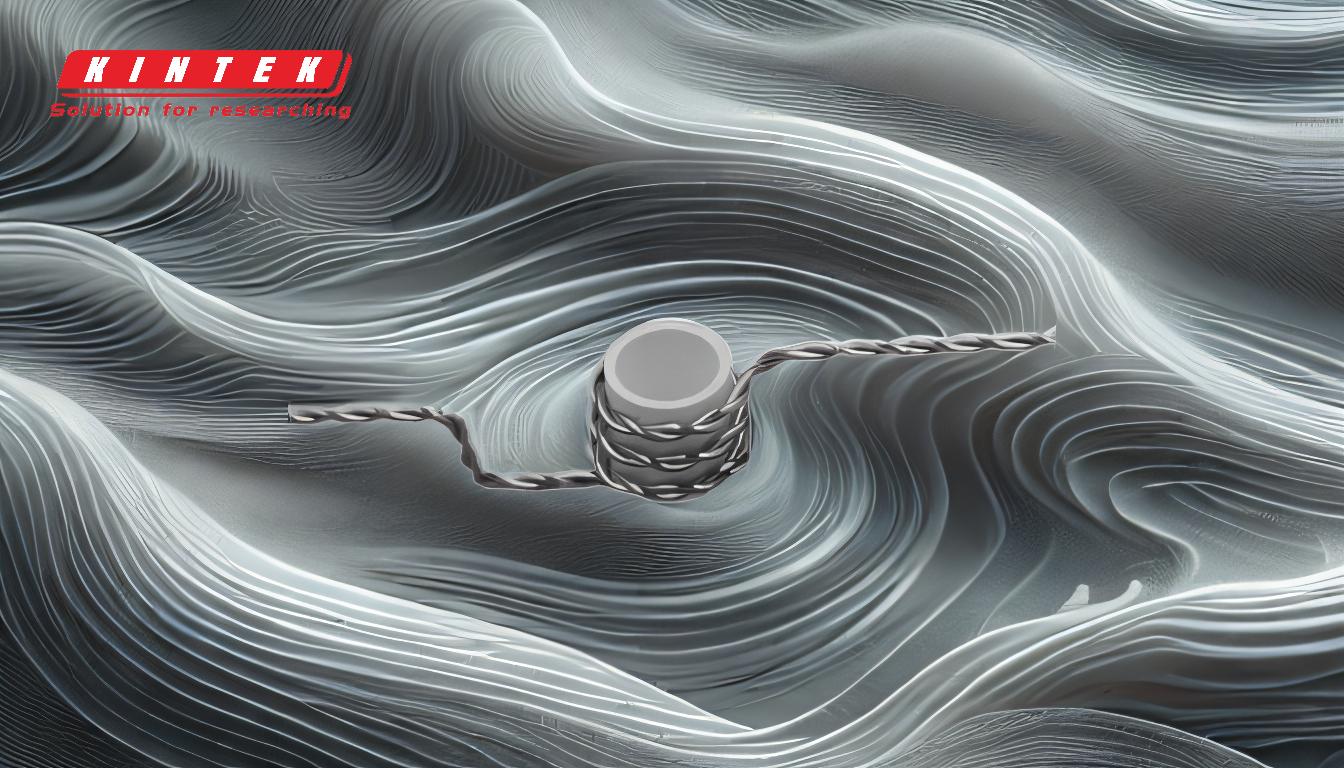
-
Reinigung des Substrats:
- Zweck:Der erste Schritt im PVD-Verfahren ist die gründliche Reinigung des Substrats.Dies ist wichtig, um alle Verunreinigungen wie Öle, Staub oder Oxide zu entfernen, die die Haftung und Qualität der Beschichtung beeinträchtigen könnten.
- Methoden:Die Reinigung kann mit verschiedenen Techniken erfolgen, darunter Ultraschallreinigung, chemische Reinigung oder Plasmareinigung.Die Wahl der Methode hängt von der Art des Substrats und dem erforderlichen Reinheitsgrad ab.
-
Verdampfung des Zielmaterials:
- Prozess:Das Zielmaterial, d. h. die aufzubringende Substanz, wird verdampft.Dies wird in der Regel durch die Erzeugung eines Plasmas in einer Vakuumkammer erreicht.Das Plasma wird mit Hilfe von Hochleistungsstrom oder einem Laser erzeugt, der das Gas ionisiert und hochenergetische Elektronen erzeugt.
- Mechanismus:Diese hochenergetischen Elektronen stoßen mit den Gasmolekülen zusammen, wodurch diese in Atome dissoziieren.Das Zielmaterial wird dann verdampft, entweder durch Sputtern (wobei Ionen das Ziel beschießen und Atome herausschlagen) oder durch Verdampfen (wobei das Ziel erhitzt wird, bis es verdampft).
-
Reaktion mit gasförmigen Spezies:
- Einführung von Reaktivgas:Nachdem das Zielmaterial verdampft ist, wird ein reaktives Gas (z. B. Stickstoff oder Sauerstoff) in die Kammer eingeleitet.Dieses Gas reagiert mit den verdampften Atomen und bildet eine Verbindung.
- Bildung der Verbindung:Die Reaktion zwischen den verdampften Atomen und dem reaktiven Gas bestimmt die Eigenschaften der endgültigen Beschichtung, wie ihre Härte, Farbe und chemische Zusammensetzung.Wenn zum Beispiel Titan das Zielmaterial und Stickstoff das reaktive Gas ist, würde die resultierende Verbindung Titannitrid (TiN) sein, das für seine Härte und sein goldähnliches Aussehen bekannt ist.
-
Abscheidung auf dem Substrat:
- Mechanismus:Die im vorherigen Schritt gebildete Verbindung wird dann auf das Substrat aufgebracht.Dies geschieht Atom für Atom, so dass eine gleichmäßige und dünne Schicht entsteht.Der Abscheidungsprozess wird kontrolliert, um die gewünschte Dicke und die gewünschten Eigenschaften der Beschichtung zu erreichen.
- Umwelt:Der gesamte Prozess findet in einer Vakuumkammer statt, um Verunreinigungen zu vermeiden und die Reaktionsumgebung genau zu kontrollieren.
-
Prüfung und Qualitätskontrolle:
- Batch-Prüfung:Nach dem Auftragen der Beschichtung wird jede Charge von Komponenten auf ihre Konsistenz geprüft.Auf diese Weise wird sichergestellt, dass die Beschichtung die erforderlichen Spezifikationen in Bezug auf Zusammensetzung, Dicke und Farbe erfüllt.
- Analytische Werkzeuge:Zur Analyse der Beschichtung werden Geräte wie Röntgenfluoreszenzgeräte (XRF) und Spektralphotometer eingesetzt.Mit einem RFA-Gerät können die Elementzusammensetzung und die Dicke der Beschichtung bestimmt werden, während ein Spektralphotometer die Farbe und das Reflexionsvermögen messen kann.
-
Hochtemperatur-Vakuum-Bedingungen:
- Wichtigkeit:Das PVD-Verfahren wird unter Hochtemperatur-Vakuumbedingungen durchgeführt, um die Stabilität und Qualität der Beschichtung zu gewährleisten.Die Vakuumumgebung verhindert Oxidation und Verunreinigung, während die hohe Temperatur die Verdampfungs- und Reaktionsprozesse unterstützt.
- Ausrüstung:Die Vakuumkammer ist mit Heizelementen und präzisen Kontrollsystemen ausgestattet, um die erforderlichen Bedingungen während des gesamten Prozesses aufrechtzuerhalten.
Zusammenfassend lässt sich sagen, dass das PVD-Metallisierungsverfahren ein mehrstufiges Verfahren ist, das die Reinigung des Substrats, die Verdampfung des Zielmaterials, dessen Reaktion mit einem Gas zur Bildung einer Verbindung und die Abscheidung dieser Verbindung auf dem Substrat umfasst.Jeder einzelne Schritt ist entscheidend, um eine hochwertige, dauerhafte Beschichtung mit den gewünschten Eigenschaften zu erhalten.Der Prozess wird unter kontrollierten Vakuum- und Hochtemperaturbedingungen durchgeführt, um die besten Ergebnisse zu erzielen.
Zusammenfassende Tabelle:
Schritt | Beschreibung |
---|---|
Reinigung von Substraten | Entfernen Sie Verunreinigungen mit Hilfe von Ultraschall-, Chemie- oder Plasmareinigungsverfahren. |
Verdampfung | Verdampfen des Zielmaterials durch Sputtern oder Verdampfen in einer Vakuumkammer. |
Reaktion mit Gas | Einleiten von reaktivem Gas (z. B. Stickstoff) zur Bildung einer Verbindung (z. B. TiN). |
Abscheidung | Die Verbindung wird für eine gleichmäßige Beschichtung Atom für Atom auf das Substrat aufgebracht. |
Prüfung und Qualität | Analysieren Sie Dicke, Zusammensetzung und Farbe von Beschichtungen mit XRF und Spektralphotometrie. |
Hochtemperatur-Vakuum | Halten Sie die Vakuum- und Hochtemperaturbedingungen für eine optimale Beschichtungsstabilität ein. |
Entdecken Sie, wie die PVD-Metallisierung die Leistung Ihres Produkts verbessern kann. Kontaktieren Sie unsere Experten noch heute !