Das Sintern ist ein kritischer Herstellungsprozess, bei dem aus pulverförmigen Stoffen durch Anwendung von Hitze und Druck feste Materialien entstehen, ohne dass der Schmelzpunkt des Materials erreicht wird.Der Prozess umfasst mehrere Stufen, darunter die Vorbereitung des Pulvers, die Verdichtung, das Erhitzen und das Abkühlen.Während des Sinterns verbinden sich die Partikel durch Diffusion, was zu einer Verdichtung und der Bildung einer kohäsiven Struktur führt.Das Verfahren wird in der Metallurgie, Keramik und anderen Industriezweigen zur Herstellung hochfester Materialien mit geringer Porosität eingesetzt.Im Folgenden werden die wichtigsten Phasen und Mechanismen des Sinterns im Detail erläutert.
Die wichtigsten Punkte werden erklärt:
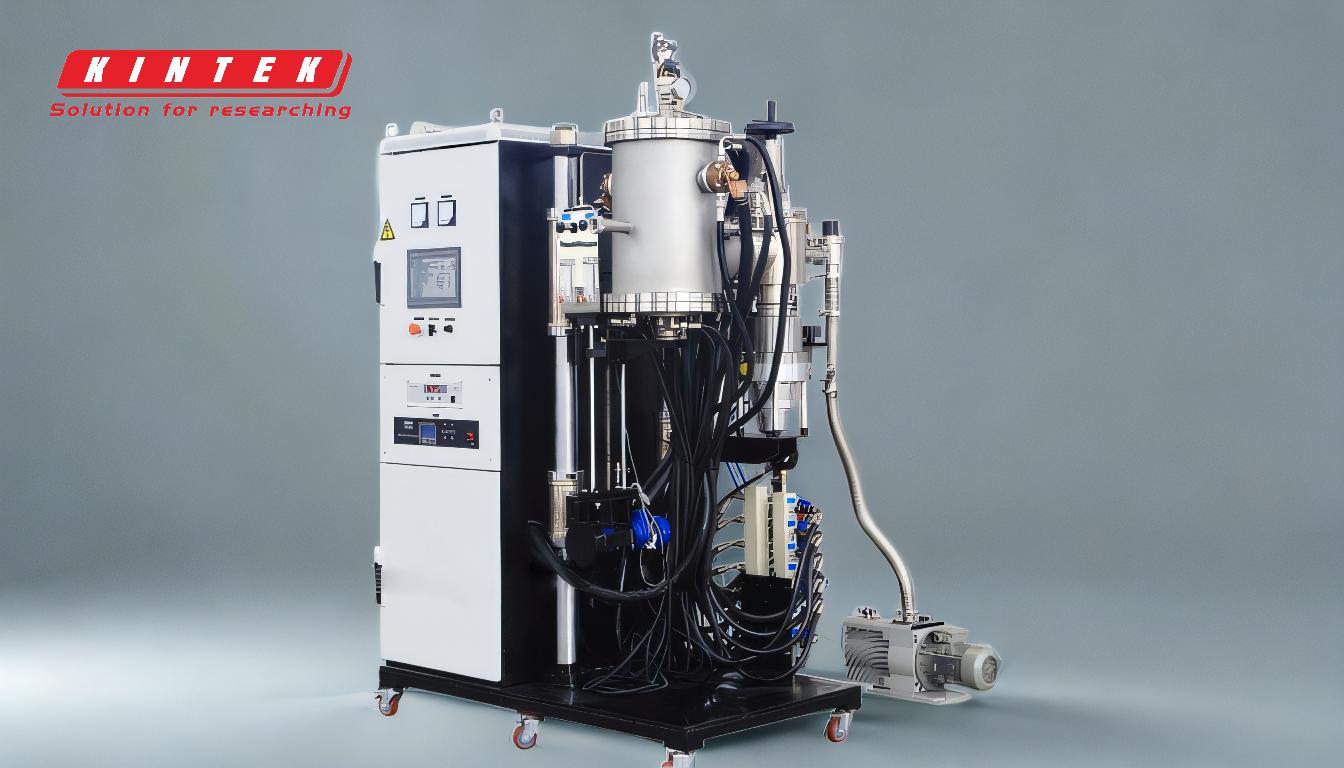
-
Vorbereitung des Pulvers
- Der Sinterprozess beginnt mit der Aufbereitung von Rohstoffen in Pulverform.
- Das Pulver wird häufig mit Zusatzstoffen wie Bindemitteln, Entflockungsmitteln oder Haftvermittlern gemischt, um die Handhabung und die Verdichtungseigenschaften zu verbessern.
- Bei Keramik wird durch Mischen von Wasser, Bindemitteln und Keramikpulver eine Aufschlämmung hergestellt, die dann durch Sprühtrocknung zu einem Granulat verarbeitet wird.
- In der Metallurgie werden Metallpulver auf der Grundlage der gewünschten Endeigenschaften, wie Festigkeit oder Wärmeleitfähigkeit, ausgewählt.
-
Verdichtung
- Das Pulver wird durch mechanischen Druck in eine bestimmte Form gepresst.
- Zu den Methoden gehören das Kalt- oder Heißpressen, bei dem das Pulver in einer Form verdichtet wird, um ein "grünes" Teil zu formen.
- Die Verdichtung sorgt für Gleichmäßigkeit und beseitigt Hohlräume, so dass vor dem Sintern eine dichte und zusammenhängende Struktur entsteht.
- Der grüne Teil ist zerbrechlich und muss sorgfältig behandelt werden, um Beschädigungen vor dem Sinterprozess zu vermeiden.
-
Erhitzung und Sinterung
- Das verdichtete Material wird in einer kontrollierten Umgebung erhitzt, in der Regel in einem Sinterofen oder Brennofen.
- Die Temperatur wird sorgfältig reguliert, um knapp unter dem Schmelzpunkt des Materials zu bleiben, damit sich die Partikel verbinden können, ohne sich zu verflüssigen.
- Während des Erhitzens diffundieren die Atome über die Partikelgrenzen hinweg, bilden "Hälse" und verdichten das Material.
- Das Flüssigphasensintern (LPS) kann zur Beschleunigung der Verdichtung eingesetzt werden, indem eine flüssige Phase eingeführt wird, die in die Poren fließt und das Zusammenwachsen der Partikel fördert.
- Durch den Erhitzungsprozess werden auch Bindemittel, Schmiermittel oder andere Zusatzstoffe entfernt, so dass eine feste Struktur mit geringer Porosität zurückbleibt.
-
Abkühlung und Erstarrung
- Nach dem Sintern wird das Material allmählich abgekühlt, damit es zu einer festen und kohäsiven Struktur erstarrt.
- Die Abkühlungsgeschwindigkeit wird kontrolliert, um innere Spannungen oder Risse zu vermeiden.
- Das Endprodukt weist verbesserte mechanische Eigenschaften wie Festigkeit, Härte und Verschleißfestigkeit auf, die auf die Beseitigung von Hohlräumen und die Bildung starker Verbindungen zwischen den Partikeln zurückzuführen sind.
-
Arten des Sinterns
- Festkörpersintern:Partikelbindung durch Diffusion ohne flüssige Phase.Wird häufig für Metalle und Keramiken verwendet.
- Flüssigphasen-Sintern (LPS):Führt eine flüssige Phase ein, um die Verdichtung und das Zusammenwachsen der Partikel zu verbessern.Geeignet für Materialien mit hohen Schmelzpunkten oder komplexen Zusammensetzungen.
- Transientes Flüssigphasensintern:Beim Erhitzen bildet sich eine vorübergehende flüssige Phase, die sich beim Abkühlen verfestigt und eine dichte Struktur hinterlässt.
-
Anwendungen des Sinterns
-
Das Sintern wird zur Herstellung einer breiten Palette von Werkstoffen verwendet, darunter:
- Metallteile für die Automobil-, Luft- und Raumfahrtindustrie.
- Keramische Komponenten für Elektronik und medizinische Geräte.
- Sinterkarbide für Schneidwerkzeuge und verschleißfeste Teile.
- Das Verfahren ist besonders wertvoll für Werkstoffe mit extrem hohen Schmelzpunkten, wie Wolfram und Molybdän, die mit herkömmlichen Schmelzmethoden nur schwer zu verarbeiten sind.
-
Das Sintern wird zur Herstellung einer breiten Palette von Werkstoffen verwendet, darunter:
-
Faktoren, die die Sinterung beeinflussen
- Temperatur:Muss sorgfältig kontrolliert werden, um eine Partikelbindung ohne Schmelzen zu gewährleisten.
- Druck:Wird während des Verdichtens angewendet, um eine gleichmäßige Dichte zu erreichen.
- Atmosphäre:Kontrollierte Umgebungen (z. B. Inertgase) verhindern Oxidation oder Kontamination.
- Größe und Form der Partikel:Kleinere Partikel und sphärische Formen verbessern die Verdichtung und Bindung.
Das Sintern ist ein vielseitiges und wichtiges Verfahren zur Herstellung von Hochleistungswerkstoffen mit maßgeschneiderten Eigenschaften.Wenn die Hersteller die beteiligten Phasen und Mechanismen verstehen, können sie den Prozess optimieren, um Bauteile mit überlegener Festigkeit, Haltbarkeit und Präzision herzustellen.
Zusammenfassende Tabelle:
Stufe | Beschreibung |
---|---|
Zubereitung von Pulvern | Die Rohstoffe werden in Pulverform aufbereitet und häufig mit Zusatzstoffen vermischt. |
Verdichtung | Das Pulver wird in eine Form gepresst, wodurch ein "grünes" Teil mit gleichmäßiger Dichte entsteht. |
Erhitzen und Sintern | Das Material wird unter den Schmelzpunkt erhitzt, wodurch sich die Partikel verbinden und verdichten. |
Abkühlung | Durch die allmähliche Abkühlung verfestigt sich das Material und erhöht seine Festigkeit und Haltbarkeit. |
Arten des Sinterns | Festkörper-, Flüssigphasen- und transiente Flüssigphasen-Sinterverfahren. |
Anwendungen | Verwendung in der Automobil-, Luft- und Raumfahrt-, Elektronik- und Medizinindustrie. |
Schlüsselfaktoren | Temperatur, Druck, Atmosphäre und Partikelgröße beeinflussen die Sinterung. |
Optimieren Sie Ihren Sinterprozess für hervorragende Ergebnisse - Kontaktieren Sie unsere Experten noch heute !