Spark Plasma Sintering (SPS), auch bekannt als Field-Assisted Sintering Technique (FAST), ist ein fortschrittliches pulvermetallurgisches Verfahren, bei dem Druck, elektrischer Strom und schnelle Erwärmung kombiniert werden, um Materialien mit hoher Dichte bei niedrigeren Temperaturen und in kürzerer Zeit als beim herkömmlichen Sintern herzustellen.Bei diesem Verfahren wird Pulver in eine Graphitform gegeben, einachsiger Druck ausgeübt und hochintensive elektrische Impulse durch die Form und das Pulver geleitet.Dadurch werden lokal hohe Temperaturen, ein Plasma und eine Oberflächenaktivierung erzeugt, die die Partikelbindung und Verdichtung erleichtern.Das Ergebnis ist ein Material mit einer Dichte von über 99 %, die durch Mechanismen wie Joule-Erwärmung, Plasmaentladung und plastische Verformung erreicht wird.
Die wichtigsten Punkte werden erklärt:
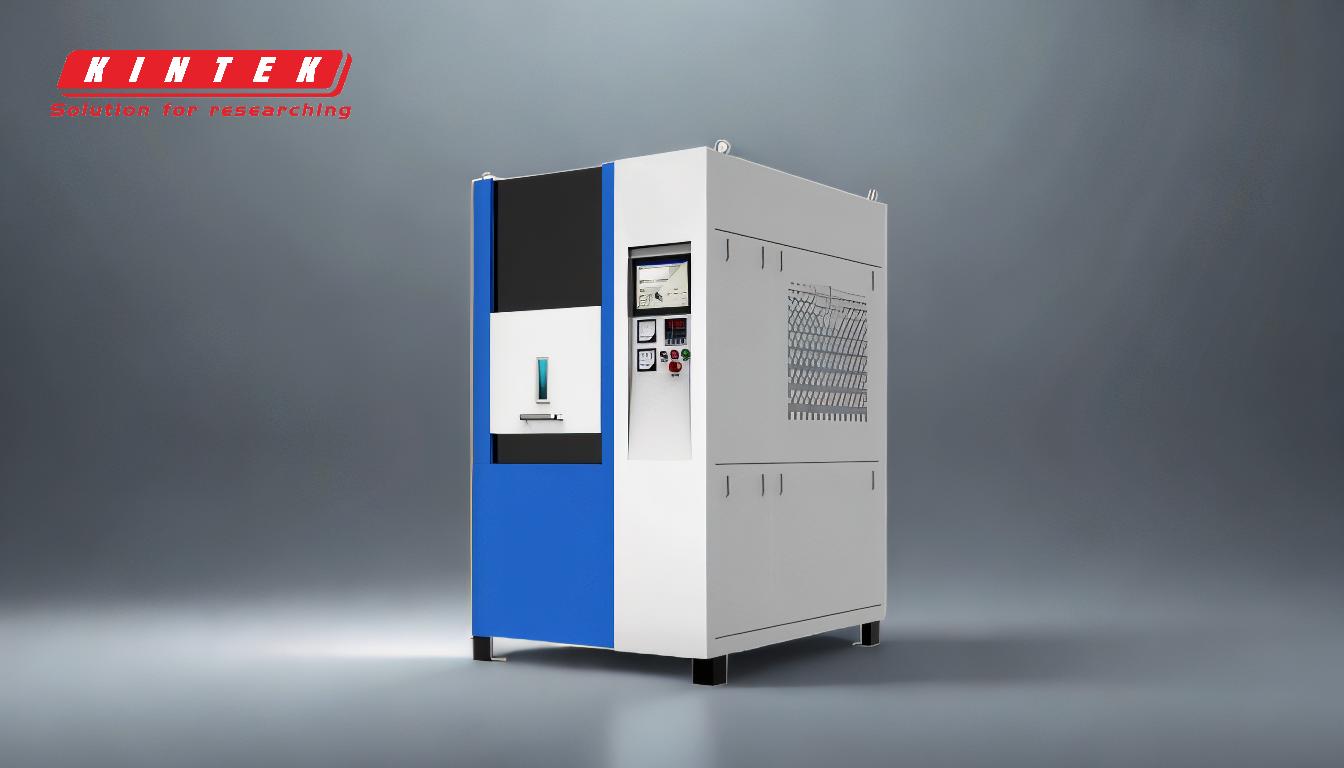
-
Aufbau und Anfangsbedingungen:
- Graphit Schimmel:Das Pulver wird in eine Graphitform gegeben, die sowohl als Matrize als auch als Wärmequelle dient.
- Uniaxialer Druck:Auf den Pulverpressling wird ein Druck von etwa 200 MPa ausgeübt, der einen engen Kontakt zwischen den Partikeln gewährleistet.
- Elektrischer Strom:Ein gepulster Gleichstrom wird durch die Form und, falls leitfähig, durch das Pulver selbst geleitet.
-
Mechanismus der Erwärmung:
- Gepulster Gleichstrom:Der gepulste Hochenergiestrom erzeugt lokal hohe Temperaturen (bis zu 10.000 °C) zwischen den Partikeln, was zu Funkenentladungen und Plasmabildung führt.
- Joulesche Heizung:Der Widerstand des Pulvers und der Form gegenüber dem elektrischen Strom erzeugt Joule-Wärme, die zu einer schnellen Erwärmung beiträgt.
- Schnelle Aufheizraten:Die Erhitzungsraten können bis zu 1.000°C pro Minute erreichen und sind damit deutlich schneller als bei herkömmlichen Sinterverfahren.
-
Partikelbindung und Verdichtung:
- Oberflächenaktivierung:Die elektrische Entladung aktiviert die Partikeloberflächen und reduziert Oberflächenoxide und Verunreinigungen.
- Bildung des Halses:Hohe Temperaturen führen dazu, dass die Oberflächen der Partikel schmelzen und verschmelzen, so dass sich zwischen den Partikeln Verengungen bilden.
- Plastische Verformung:Der ausgeübte Druck und die örtliche Erwärmung führen zu einer plastischen Verformung, wodurch sich die Lücken zwischen den Partikeln weiter schließen.
-
Temperatur- und Zeitsteuerung:
- Hohe Temperaturen:Die Form und die Probe können Temperaturen von bis zu 2.400 °C erreichen, obwohl die Sinterung oft bei niedrigeren Temperaturen als bei herkömmlichen Verfahren erfolgt.
- Kurze Haltezeiten:Das Verfahren erfordert in der Regel sehr kurze Haltezeiten bei Spitzentemperatur, was den Energieverbrauch und die Verarbeitungszeit reduziert.
-
Verdichtung und endgültige Eigenschaften:
- Hohe Dichte:Die kombinierte Wirkung von Druck, elektrischem Strom und schneller Erhitzung führt zu Materialien mit einer Dichte von über 99 %.
- Mikrostrukturelle Kontrolle:Die schnellen Erwärmungs- und Abkühlungsgeschwindigkeiten ermöglichen eine genaue Kontrolle der Mikrostruktur, was häufig zu feineren Körnern und besseren mechanischen Eigenschaften führt.
-
System-Komponenten:
- Axiales Druckgerät:Wendet den einachsigen Druck während des Sinterns an und hält ihn aufrecht.
- Wassergekühlte Stanzelektrode:Gewährleistet einen stabilen elektrischen Kontakt und Kühlung während des Prozesses.
- Vakuumkammer:Bietet eine kontrollierte Atmosphäre, oft unter Vakuum oder Inertgas, um Oxidation zu verhindern.
- Atmosphären-Kontrollsystem:Steuert die Umgebung innerhalb der Kammer, um optimale Sinterbedingungen zu gewährleisten.
- Gleichstromimpuls und Kühlwasser:Liefert den gepulsten Strom und steuert die Wärmeableitung.
- Messung von Verschiebung und Temperatur:Überwacht den Fortschritt der Verdichtung und die Temperaturkontrolle.
- Sicherheitskontrollgeräte:Gewährleistet den sicheren Betrieb der Anlage, insbesondere angesichts der hohen Temperaturen und Drücke.
-
Vorteile gegenüber der konventionellen Sinterung:
- Niedrigere Sintertemperaturen:SPS erfordert in der Regel Temperaturen, die mehrere hundert Grad niedriger sind als beim herkömmlichen Sintern.
- Reduzierte Verarbeitungszeit:Durch die schnelle Erwärmung und die kurzen Haltezeiten wird die Gesamtbearbeitungszeit erheblich reduziert.
- Verbesserte Materialeigenschaften:Die feinen Mikrostrukturen und die hohen Dichten, die erreicht werden, führen oft zu hervorragenden mechanischen, thermischen und elektrischen Eigenschaften.
-
Anwendungen:
- Keramiken und Metalle:SPS ist weit verbreitet für das Sintern von keramischen und metallischen Pulvern, einschließlich moderner Materialien wie Karbide, Nitride und Verbundwerkstoffe.
- Nanomaterialien:Das Verfahren eignet sich besonders für das Sintern von Nanomaterialien, bei denen herkömmliche Methoden zu übermäßigem Kornwachstum führen können.
- Komplexe Formen:Die Möglichkeit, während des Sinterns Druck auszuüben, ermöglicht die Herstellung komplexer Formen mit hoher Maßgenauigkeit.
Zusammenfassend lässt sich sagen, dass das Spark-Plasma-Sintern ein hocheffizientes und vielseitiges Sinterverfahren ist, das elektrischen Strom, Druck und schnelle Erwärmung nutzt, um dichte, hochwertige Materialien mit feinen Mikrostrukturen herzustellen.Aufgrund seiner Vorteile gegenüber herkömmlichen Sinterverfahren eignet es sich besonders für fortschrittliche Werkstoffe und Anwendungen, die eine genaue Kontrolle der Materialeigenschaften erfordern.
Zusammenfassende Tabelle:
Hauptaspekt | Einzelheiten |
---|---|
Aufbau | Graphitform, uniaxialer Druck (200 MPa), gepulster Gleichstrom |
Heiz-Mechanismus | Gepulster Gleichstrom, Joule-Erwärmung, schnelle Heizraten (bis zu 1.000°C/min) |
Partikel-Bonden | Oberflächenaktivierung, Halsbildung, plastische Verformung |
Temperaturkontrolle | Hohe Temperaturen (bis zu 2.400°C), kurze Haltezeiten |
Endgültige Eigenschaften | >99% Dichte, feines Gefüge, verbesserte mechanische Eigenschaften |
Vorteile | Niedrigere Sintertemperaturen, kürzere Verarbeitungszeit, bessere Eigenschaften |
Anwendungen | Keramiken, Metalle, Nanomaterialien, komplexe Formen |
Transformieren Sie Ihre Materialverarbeitung mit Spark Plasma Sintering. Kontaktieren Sie unsere Experten noch heute um mehr zu erfahren!