Mahlkörper spielen eine entscheidende Rolle für die Mahlleistung von Kugelmühlen und Perlmühlen.Ihre Größe, Zusammensetzung, Dichte und Menge haben einen direkten Einfluss auf die Energieübertragung, die Partikelzerkleinerung und die gesamte Mahlleistung.Größere Mahlkörper können eine höhere Aufprallenergie liefern, während kleinere Medien die Häufigkeit der Zusammenstöße erhöhen, was sich wiederum auf die Bruchrate der Partikel auswirkt.Die Zusammensetzung der Mahlkörper muss mit dem zu mahlenden Material kompatibel sein, um Verunreinigungen oder unerwünschte Reaktionen zu vermeiden.Darüber hinaus bestimmen Faktoren wie der Füllgrad, die Rotationsgeschwindigkeit und die Verweilzeit des Materials in der Mühle die Mahlleistung.Die Optimierung dieser Parameter gewährleistet eine effektive Vermahlung, einen geringeren Stromverbrauch und die gewünschte Korngrößenverteilung.
Die wichtigsten Punkte erklärt:
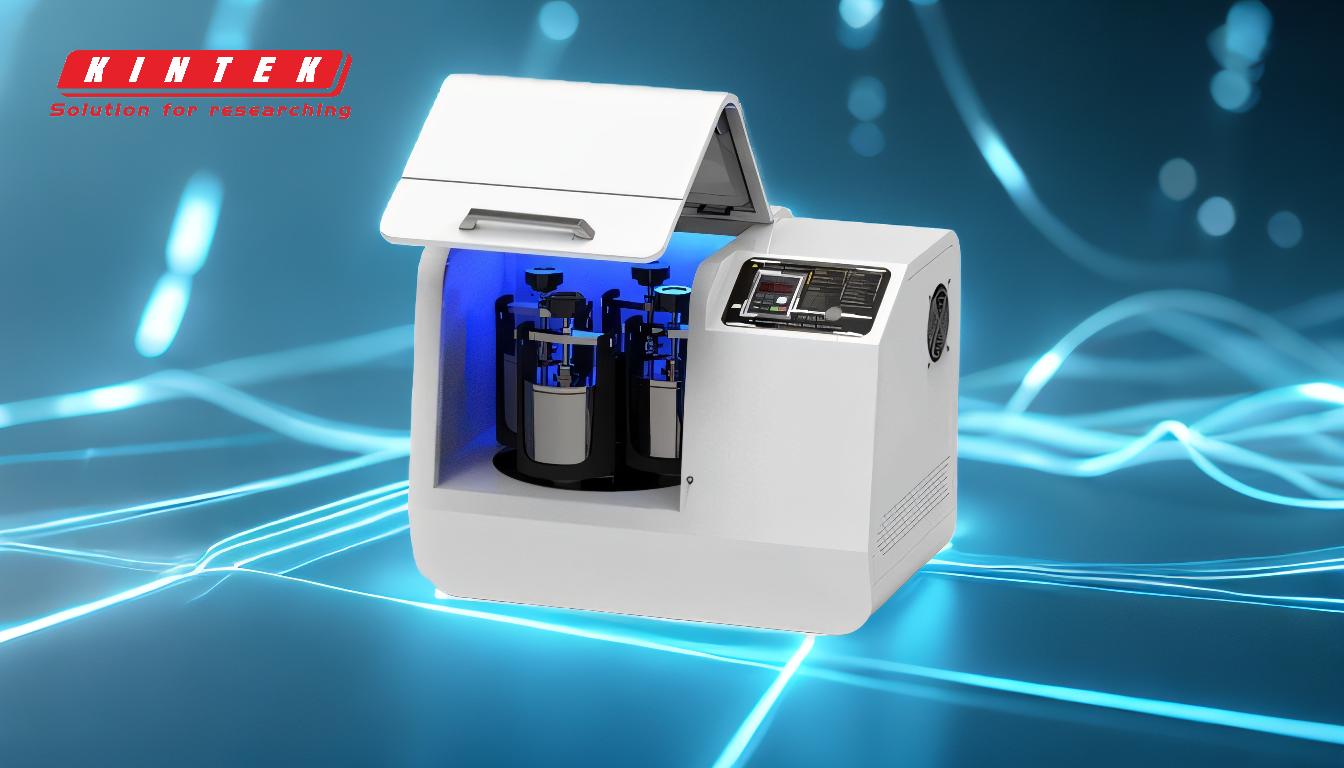
-
Größe der Mahlkörper:
- Die Größe der Mahlkörper ist ein entscheidender Faktor für die Mahlleistung.Größere Mahlkörper liefern eine höhere Aufprallenergie, die für die Zerkleinerung grober Partikel wirksam ist, während kleinere Mahlkörper die Häufigkeit der Zusammenstöße erhöhen und damit die Zerkleinerung feinerer Partikel fördern.
- Die Wahl der Mediengröße hängt von der angestrebten Partikelgröße und dem zu mahlenden Material ab.So werden z. B. kleinere Perlen bevorzugt, um in Perlmühlen ultrafeine Partikelgrößen zu erzielen.
-
Zusammensetzung der Mahlkörper:
- Die Zusammensetzung der Mahlkörper muss auf die spezifischen Anforderungen der Mahlanwendung abgestimmt sein.So werden z. B. in der Lebensmittel- oder Pharmaindustrie häufig keramische oder rostfreie Mahlkörper verwendet, um Verunreinigungen zu vermeiden.
- Reaktive Materialien erfordern unter Umständen inerte Mahlkörper, um chemische Wechselwirkungen zu vermeiden, die die Eigenschaften des Endprodukts verändern könnten.
-
Dichte und Masse von Mahlkörpern:
- Medien mit höherer Dichte (z. B. Stahl oder Zirkoniumdioxid) liefern eine größere Aufprallenergie und verbessern so die Mahlleistung bei harten Materialien.
- Auch die Masse der in die Mühle eingebrachten Perlen beeinflusst den Mahlprozess.Eine optimale Masse gewährleistet einen ausreichenden Energietransfer, ohne die Mühle zu überlasten, was die Effizienz verringern könnte.
-
Füllungsgrad der Mühle:
- Der Füllungsgrad, d. h. der prozentuale Anteil der Mahlkörper am Mühlenvolumen, beeinflusst die Mahlleistung.Ein optimaler Füllungsgrad gewährleistet einen angemessenen Kontakt zwischen Mahlgut und Mahlkörper und vermeidet gleichzeitig übermäßige Reibung oder Energieverluste.
- Eine Überfüllung kann zu einer verminderten Mahlleistung und einem erhöhten Energieverbrauch führen, während eine Unterfüllung zu einem unzureichenden Partikelbruch führen kann.
-
Rotationsgeschwindigkeit und Rotordesign:
- Die Rotationsgeschwindigkeit der Mühle bestimmt die kinetische Energie der Mahlkörper.Höhere Drehzahlen erhöhen die Aufprallenergie und die Häufigkeit der Zusammenstöße, wodurch die Mahlleistung gesteigert wird.
- Auch die Konstruktion des Rotors (bei Perlmühlen) spielt eine Rolle.Spezialisierte Rotoren können die Verteilung der Perlen verbessern und den Mahlprozess optimieren.
-
Verweilzeit und Vorschubgeschwindigkeit:
- Die Verweilzeit des Materials in der Mühlenkammer beeinflusst den Mahlgrad.Längere Verweilzeiten ermöglichen eine gründlichere Vermahlung, können aber den Durchsatz verringern.
- Die Zuführungsrate und der Füllstand im Behälter müssen ausgewogen sein, um eine gleichmäßige Vermahlung ohne Überlastung der Mühle zu gewährleisten.
-
Aufprallenergie und Häufigkeit der Kollisionen:
- Die Zerkleinerungseffizienz wird durch das Gleichgewicht zwischen Aufprallenergie und Häufigkeit der Kollisionen bestimmt.Größere Medien liefern mehr Energie, aber weniger Kollisionen, während kleinere Medien die Kollisionshäufigkeit erhöhen, aber weniger Energie liefern.
- Die Optimierung dieser Faktoren gewährleistet eine effiziente Partikelzerkleinerung und minimiert den Energieverbrauch.
-
Anwendungsspezifische Überlegungen:
- Die Wahl der Mahlkörper und der Mahlparameter hängt von der jeweiligen Anwendung ab.So können für die Feinvermahlung von Pigmenten kleinere Perlen und höhere Rotordrehzahlen erforderlich sein, während für die Grobvermahlung von Mineralien größere Medien und niedrigere Drehzahlen von Vorteil sind.
- Die Kompatibilität mit dem zu mahlenden Material ist entscheidend, um Verunreinigungen oder unerwünschte Reaktionen zu vermeiden.
Durch eine sorgfältige Auswahl und Optimierung dieser Faktoren kann die Effizienz des Mahlens erheblich verbessert werden, was zu einer besseren Produktqualität, einem geringeren Energieverbrauch und niedrigeren Betriebskosten führt.
Zusammenfassende Tabelle:
Faktor | Einfluss auf die Mahleffizienz |
---|---|
Größe der Mahlkörper | Größere Mahlkörper = höhere Aufprallenergie; kleinere Mahlkörper = höhere Aufprallhäufigkeit. |
Zusammensetzung | Muss dem zu mahlenden Material entsprechen, um Verunreinigungen oder Reaktionen zu vermeiden. |
Dichte und Masse | Höhere Dichte = größere Aufprallenergie; optimale Masse = effiziente Energieübertragung. |
Füllungsgrad | Optimales Verhältnis = ausreichender Kontakt zwischen Medium und Material; vermeidet Reibung und Energieverlust. |
Rotationsgeschwindigkeit | Höhere Geschwindigkeiten = höhere Aufprallenergie und Aufprallhäufigkeit. |
Verweilzeit | Längere Zeiten = gründliches Mahlen; kürzere Zeiten = höherer Durchsatz. |
Anwendungsspezifisch | Medien und Parameter variieren je nach Material und gewünschter Partikelgröße. |
Sind Sie bereit, Ihren Mahlprozess zu optimieren? Kontaktieren Sie noch heute unsere Experten für maßgeschneiderte Lösungen!