Bei gesputterten Dünnschichten treten aufgrund der Art des Sputterprozesses und der beteiligten Materialien häufig innere Spannungen auf. Diese Spannungen entstehen durch Faktoren wie die unterschiedlichen Wärmeausdehnungskoeffizienten von Schicht und Substrat, intrinsische Spannungen durch den Abscheidungsprozess und mikrostrukturelle Veränderungen während des Schichtwachstums. Je nach den Abscheidungsbedingungen und den Materialeigenschaften kann die Spannung entweder auf Zug (Auseinanderziehen der Schicht) oder auf Druck (Zusammenschieben der Schicht) beruhen. Die Beherrschung dieser Spannung ist entscheidend für die Haltbarkeit, Haftung und Leistung der Dünnschicht in Anwendungen wie Solarzellen, mikroelektrochemischen Geräten und optischen Beschichtungen. Das Verständnis und die Kontrolle von Spannungen erfordern eine sorgfältige Auswahl von Materialien, Prozessparametern und Nachbehandlungen nach der Abscheidung.
Die wichtigsten Punkte werden erklärt:
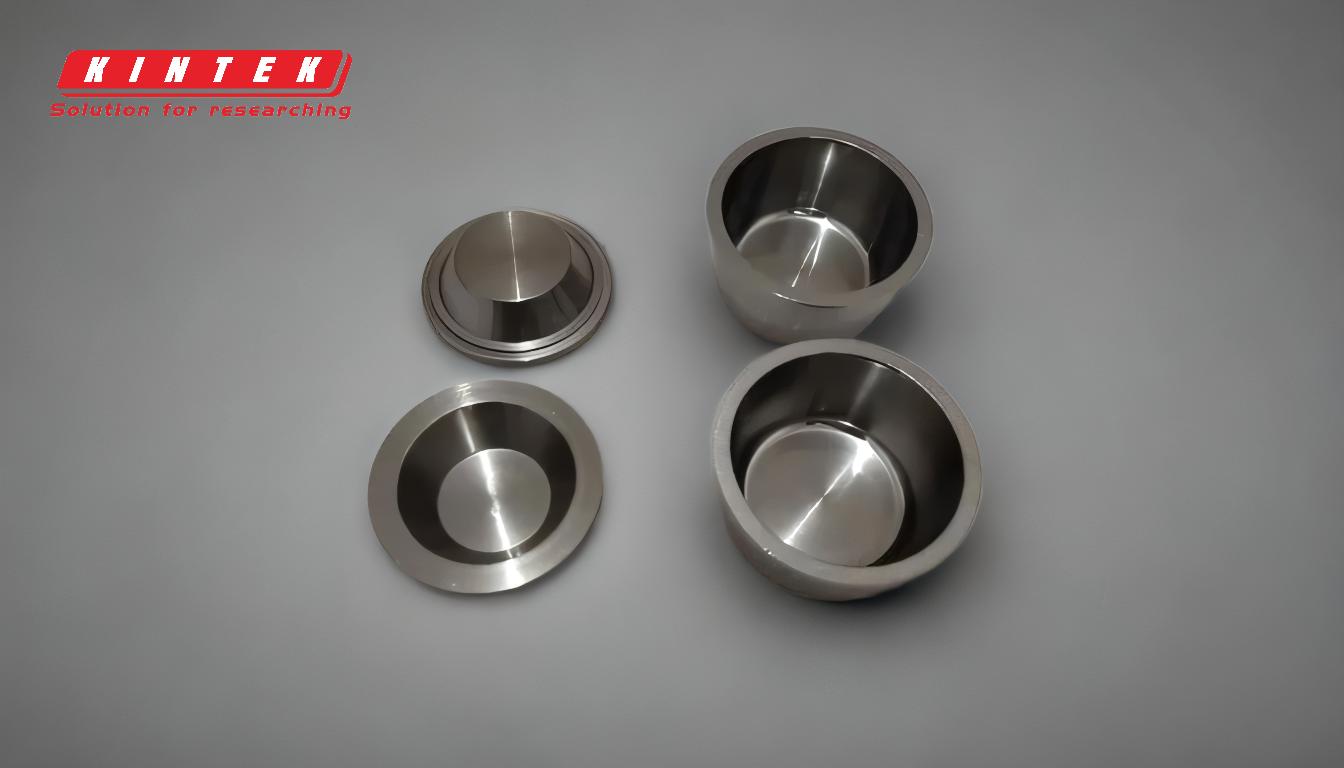
-
Entstehung von Spannungen in gesputterten Dünnschichten:
- Thermische Spannung: Entsteht durch unterschiedliche Wärmeausdehnungskoeffizienten zwischen der dünnen Schicht und dem Substrat. Wenn die Schicht nach der Abscheidung abkühlt, kann eine unangepasste Ausdehnung oder Kontraktion zu Zug- oder Druckspannungen führen.
- Intrinsische Spannung: Entsteht durch den Abscheidungsprozess selbst. Faktoren wie Ionenbeschuss, Adatom-Mobilität und Kornwachstum während des Sputterns können innere Spannungen in der Schicht erzeugen.
- Mikrostrukturelle Spannung: Entsteht durch Defekte, Hohlräume oder kolumnare Wachstumsstrukturen in der Schicht. Diese Unzulänglichkeiten können die mechanischen Eigenschaften der Schicht verändern und zu Spannungen beitragen.
-
Arten von Spannungen:
- Zugspannung: Zieht den Film auseinander, oft verursacht durch Schrumpfung während der Abkühlung oder unzureichende Beweglichkeit der Atome während der Abscheidung.
- Komprimierende Spannung: Drückt den Film zusammen, was typischerweise durch Ionenbeschuss oder den Einbau von überschüssigen Atomen während der Abscheidung verursacht wird.
-
Faktoren, die die Spannung beeinflussen:
- Abscheidungsparameter: Parameter wie Sputterleistung, Gasdruck und Substrattemperatur können das Spannungsniveau erheblich beeinflussen. So kann beispielsweise eine höhere Sputterleistung die Druckspannung aufgrund eines verstärkten Ionenbeschusses erhöhen.
- Materialeigenschaften: Die Wahl des Zielmaterials und seine Eigenschaften, wie Schmelzpunkt und atomare Struktur, beeinflussen die Spannung. So können beispielsweise Metalle mit hohem Schmelzpunkt eine höhere Eigenspannung aufweisen.
- Merkmale des Substrats: Die thermischen und mechanischen Eigenschaften des Substrats, wie Wärmeleitfähigkeit und Steifigkeit, spielen eine Rolle bei der Spannungsentwicklung.
-
Auswirkungen der Spannung auf die Filmeigenschaften:
- Adhäsion: Übermäßige Spannungen können die Verbindung zwischen Folie und Substrat schwächen und zu Delamination oder Ablösung führen.
- Dauerhaftigkeit: Hohe Spannungen machen die Folie anfälliger für Risse, Kratzer oder chemischen Abbau, insbesondere bei gesputterten "Softcoat"-Folien.
- Leistung: Stress kann die optischen, elektrischen und mechanischen Eigenschaften verändern und sich auf Anwendungen wie Solarzellen, optische Beschichtungen und mikroelektrochemische Geräte auswirken.
-
Strategien zur Stresskontrolle:
- Optimierung der Abscheidungsbedingungen: Die Anpassung von Parametern wie Sputterleistung, Gasdruck und Substrattemperatur kann helfen, das Stressniveau zu kontrollieren.
- Behandlungen nach der Abscheidung: Durch Glühen oder Wärmebehandlungen können Spannungen abgebaut werden, da sich die Atome neu anordnen können und Defekte reduziert werden.
- Auswahl des Materials: Die Auswahl von Materialien mit kompatiblen Wärmeausdehnungskoeffizienten und mechanischen Eigenschaften kann Spannungen minimieren.
-
Anwendungen und Spannungsbetrachtungen:
- Solarzellen: Die Beherrschung von Spannungen ist entscheidend für die Gewährleistung der langfristigen Stabilität und Effizienz von Dünnschicht-Solarzellen.
- Optische Beschichtungen: Eine gleichmäßige Spannungsverteilung ist entscheidend für die Aufrechterhaltung der optischen Leistung und Haltbarkeit von gesputterten Schichten, die für reflektierende oder antireflektierende Beschichtungen verwendet werden.
- Mikro-elektrochemische Geräte: Die Kontrolle der Spannungen gewährleistet die richtige Haftung und Funktionalität von Platin- oder anderen Metallbeschichtungen in Geräten wie Brennstoffzellen und Sensoren.
Durch das Verständnis des Ursprungs, der Arten und der Auswirkungen von Spannungen in gesputterten Dünnschichten können Hersteller die Abscheidungsprozesse und die Materialauswahl optimieren, um qualitativ hochwertige, dauerhafte Beschichtungen für fortschrittliche Anwendungen herzustellen.
Zusammenfassende Tabelle:
Aspekt | Einzelheiten |
---|---|
Ursachen von Spannungen | Thermische Spannung, intrinsische Spannung, mikrostrukturelle Spannung |
Arten von Spannung | Zugspannung (Auseinanderziehen), Druckspannung (Zusammenschieben) |
Beeinflussende Faktoren | Abscheidungsparameter, Materialeigenschaften, Substrateigenschaften |
Auswirkungen auf die Eigenschaften | Haftung, Haltbarkeit, Leistung |
Kontrollstrategien | Optimierung der Abscheidung, Nachbehandlung, Materialauswahl |
Anwendungen | Solarzellen, optische Beschichtungen, mikroelektrochemische Geräte |
Optimieren Sie Ihre gesputterten Dünnschichten für eine überragende Leistung - Kontaktieren Sie unsere Experten noch heute !