Die physikalische Gasphasenabscheidung (PVD) ist ein vielseitiges und präzises Beschichtungsverfahren, mit dem dünne Materialschichten auf Substrate aufgebracht werden können.Die Dicke von PVD-Beschichtungen reicht in der Regel von 0,00004 bis 0,0002 Zoll (oder ungefähr 1 bis 5 Mikrometer ).Dieser Bereich ist ideal für Anwendungen, die enge Toleranzen erfordern, wie z. B. in der Luft- und Raumfahrt, der Medizin und der Elektronikindustrie.Die Dicke von PVD-Beschichtungen wird durch Faktoren wie Abscheidungsparameter, Materialeigenschaften und Prozessbedingungen beeinflusst.Im Folgenden werden die wichtigsten Aspekte der PVD-Dicke und die Faktoren, die sie beeinflussen, erläutert.
Die wichtigsten Punkte erklärt:
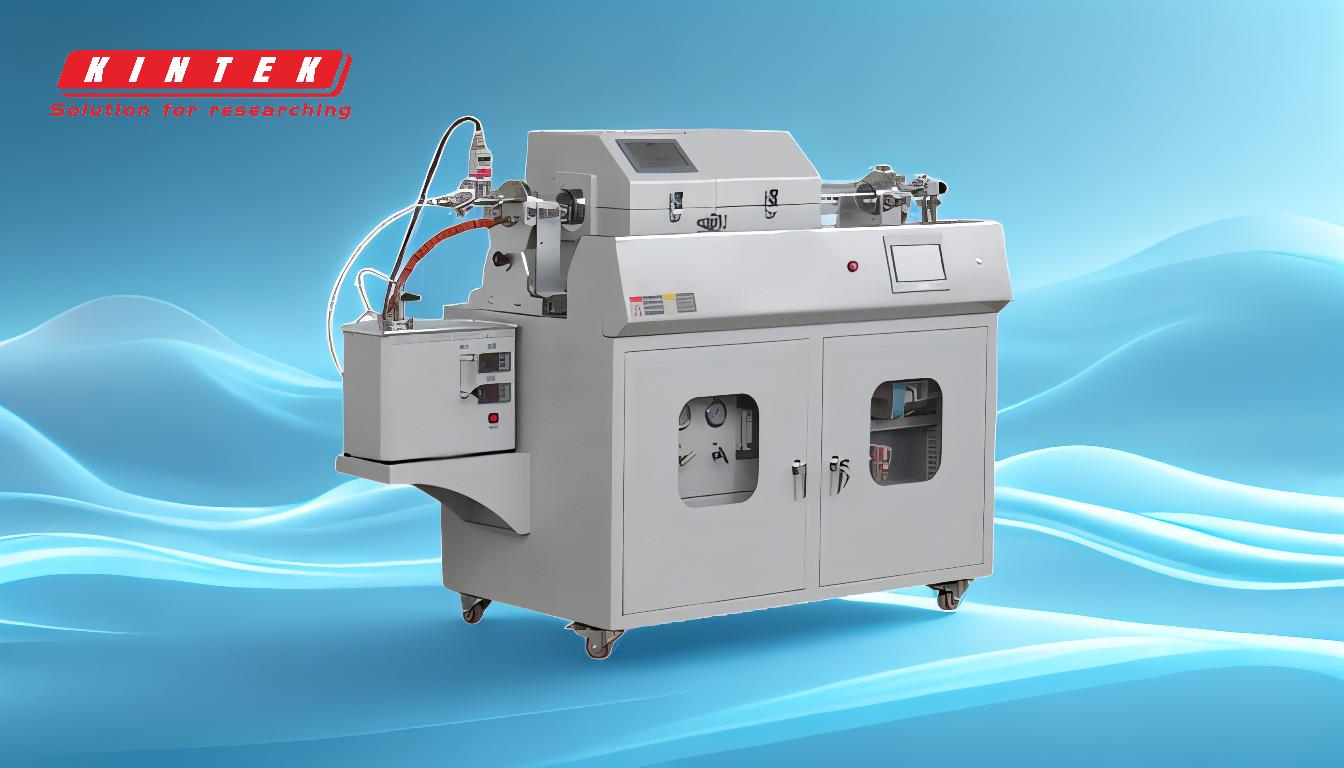
-
Typischer Dickenbereich von PVD-Beschichtungen
- Die durchschnittliche Dicke von PVD-Beschichtungen beträgt 0,00004 bis 0,0002 Zoll (1 bis 5 Mikrometer).
- Dieser Bereich eignet sich für Anwendungen, die hohe Präzision erfordern, z. B. Schneidwerkzeuge, medizinische Geräte und optische Komponenten.
- Die Dünnheit von PVD-Beschichtungen sorgt für minimale Maßänderungen des Substrats und ist damit ideal für Anwendungen mit engen Toleranzen.
-
Faktoren, die die PVD-Beschichtungsdicke beeinflussen
-
Beschichtungszeit und Leistung:
- Längere Abscheidungszeiten und höhere Leistungen führen zu dickeren Schichten.
- So werden beispielsweise Sputterprozesse durch die Zykluszeit und die auf das Zielmaterial angewandte Leistung beeinflusst.
-
Materialeigenschaften:
- Die Masse und die Verdampfungsrate des Ausgangsmaterials wirken sich auf die Abscheidungsrate und die Enddicke aus.
- Materialien mit höherem Molekulargewicht können längere Abscheidungszeiten erfordern, um die gewünschte Dicke zu erreichen.
-
Vorbereitung des Substrats:
- Eine glatte und saubere Substratoberfläche gewährleistet eine gleichmäßige Abscheidung, während raue Oberflächen zu einer ungleichmäßigen Schichtdicke führen können.
-
Vakuum-Bedingungen:
- Ein höherer Vakuumgrad verbessert den freien Weg der Ausgangsmaterialmoleküle, reduziert Verunreinigungen und gewährleistet eine gleichmäßige Dicke.
-
Energie der Beschichtungspartikel:
- Das Energieniveau der Partikel während der Abscheidung (von einigen zehn bis zu Tausenden von Elektronenvolt) beeinflusst die Dichte und Dicke der Beschichtung.
-
Beschichtungszeit und Leistung:
-
Vorteile der PVD-Beschichtungsdicke
-
Präzision und Gleichmäßigkeit:
- PVD-Beschichtungen bilden die Oberflächenbeschaffenheit des Substrats nach und gewährleisten selbst bei komplexen Geometrien eine gleichmäßige Dicke.
-
Kein übermäßiger Aufbau:
- Die dünne Beschaffenheit von PVD-Beschichtungen verhindert eine übermäßige Materialanhäufung, so dass die Abmessungen des Substrats erhalten bleiben.
-
Umweltfreundlichkeit:
- PVD ist ein sauberes Verfahren, das reine, hochwertige Beschichtungen ohne schädliche Nebenprodukte erzeugt.
-
Präzision und Gleichmäßigkeit:
-
Anwendungen von PVD-Beschichtungsdicken
-
Schneidewerkzeuge:
- Dünne PVD-Beschichtungen erhöhen die Verschleißfestigkeit und verlängern die Lebensdauer des Werkzeugs, ohne die Abmessungen des Werkzeugs zu verändern.
-
Medizinische Geräte:
- PVD-Beschichtungen bieten Biokompatibilität und Korrosionsbeständigkeit in dünnen, präzisen Schichten.
-
Optik und Elektronik:
- Die Fähigkeit, ultradünne, gleichmäßige Schichten abzuscheiden, macht PVD ideal für optische Linsen, Halbleiter und Displays.
-
Schneidewerkzeuge:
-
Vergleich mit anderen Beschichtungsmethoden
- PVD-Beschichtungen sind im Allgemeinen dünner als Beschichtungen, die durch chemische Gasphasenabscheidung (CVD) oder Galvanik hergestellt werden.
- Im Gegensatz zu CVD erfordert PVD keine hohen Temperaturen oder Wärmebehandlung, so dass es sich für temperaturempfindliche Substrate eignet.
Zusammenfassend lässt sich sagen, dass die Dicke von PVD-Beschichtungen ein kritischer Parameter ist, der von verschiedenen Prozess- und Materialfaktoren abhängt.Die Fähigkeit, die Schichtdicke präzise zu steuern, macht PVD zu einer bevorzugten Wahl für Branchen, die leistungsstarke, langlebige und maßgenaue Beschichtungen benötigen.
Zusammenfassende Tabelle:
Aspekt | Details |
---|---|
Typischer Dickenbereich | 0,00004 bis 0,0002 Zoll (1 bis 5 Mikrometer) |
Wichtige Einflussfaktoren | Beschichtungszeit, Leistung, Materialeigenschaften, Substratvorbereitung, Vakuum |
Vorteile | Präzision, Gleichmäßigkeit, minimale Anhaftung, Umweltfreundlichkeit |
Anwendungen | Schneidwerkzeuge, medizinische Geräte, Optik, Elektronik |
Vergleich mit anderen Verfahren | Dünner als CVD und galvanische Beschichtung, keine hohen Temperaturen erforderlich |
Entdecken Sie, wie PVD-Beschichtungen Ihre Anwendungen verbessern können. Kontaktieren Sie unsere Experten noch heute !