Thermisches Sintern ist ein wichtiges Herstellungsverfahren, mit dem pulverförmige Werkstoffe in dichte, feste Körper umgewandelt werden, ohne sie vollständig zu schmelzen. Dabei wird das Material unter seinen Schmelzpunkt erhitzt, so dass die Atome über die Partikelgrenzen diffundieren und sich miteinander verbinden können. Dieses Verfahren ist in Branchen wie der Pulvermetallurgie, der Keramik und der Elektronik weit verbreitet, um Bauteile mit verbesserten mechanischen Eigenschaften, geringerer Porosität und maßgeschneiderten Mikrostrukturen herzustellen. Thermisches Sintern ist kostengünstig, vielseitig und unerlässlich für die Herstellung komplexer Formen und die Arbeit mit hochschmelzenden Materialien wie Wolfram und Molybdän.
Die wichtigsten Punkte werden erklärt:
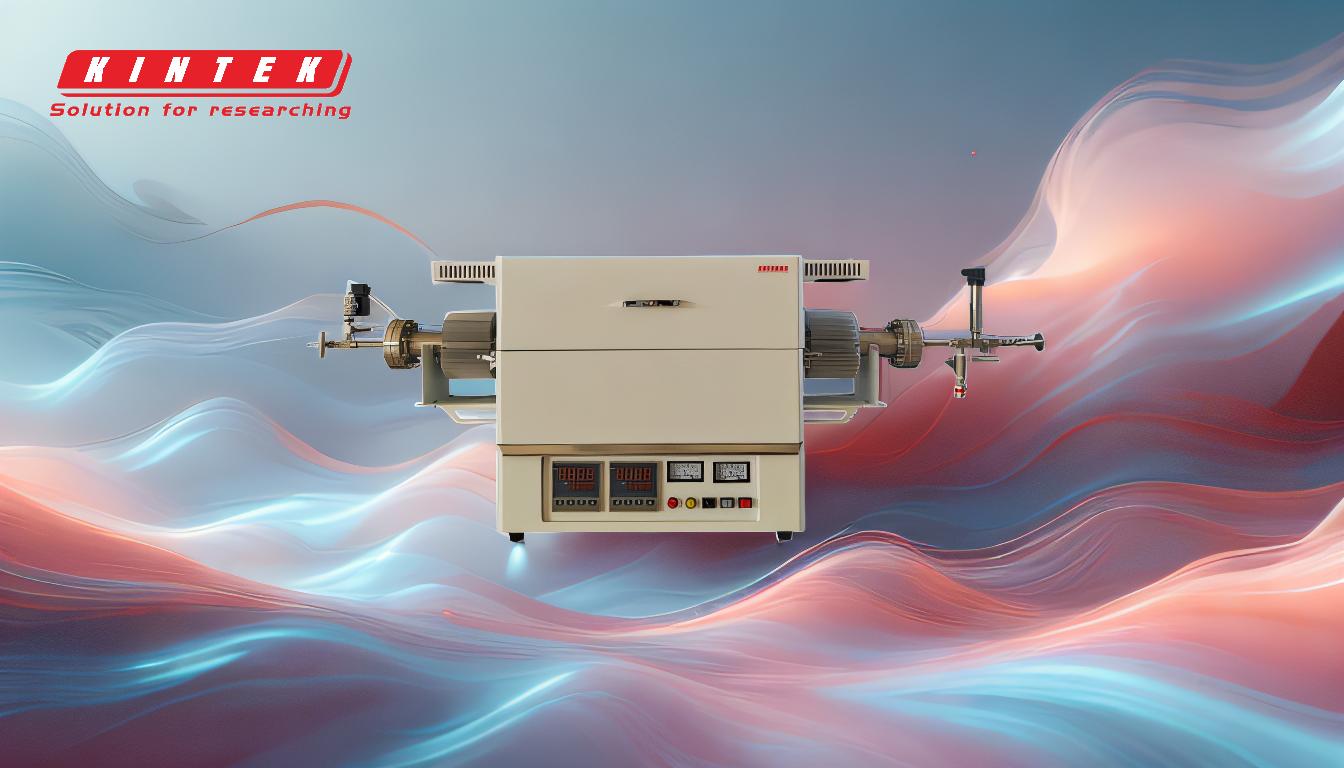
-
Definition des thermischen Sinterns:
- Thermisches Sintern ist ein Wärmebehandlungsverfahren, das pulverförmige Materialien zu einer dichten, festen Masse verbindet, ohne sie zu verflüssigen. Es beruht auf der Festkörperdiffusion, bei der Atome über die Partikelgrenzen hinweg wandern und sie zu einer kohäsiven Struktur verschmelzen.
-
Zweck und Nutzen:
- Verdichtung: Beseitigt die Porosität und erhöht die Dichte und Festigkeit des Materials.
- Mechanische Eigenschaften: Verbessert die Härte, Verschleißfestigkeit und strukturelle Integrität.
- Komplexe Formen: Ermöglicht die Herstellung komplizierter Komponenten, die mit anderen Methoden nur schwer zu erreichen sind.
- Kosten-Wirksamkeit: Verringert den Materialabfall und den Energieverbrauch im Vergleich zu Schmelzverfahren.
-
Prozess-Schritte:
- Verdichtung: Das pulverförmige Material wird zu einem "Grünkörper" mit der gewünschten Form gepresst.
- Heizung: Der Grünling wird in einem Ofen mit kontrollierter Atmosphäre bei Temperaturen unterhalb des Schmelzpunktes des Materials erhitzt.
- Bindung: Die Atome diffundieren über die Partikelgrenzen und verbinden die Partikel miteinander.
- Kühlung: Das gesinterte Teil wird mit einer kontrollierten Geschwindigkeit abgekühlt, um die gewünschten Eigenschaften zu erreichen.
-
Anwendungen:
- Pulvermetallurgie: Wird zur Herstellung von Zahnrädern, Lagern und elektrischen Kontakten verwendet.
- Keramik: Herstellung von Töpferwaren, Fliesen und fortschrittlichen Keramikkomponenten.
- Hochschmelzende Materialien: Ideal für Wolfram, Molybdän und andere Refraktärmetalle.
- Elektronik: Stellt Komponenten wie Armaturen und Rotoren her.
-
Wichtige Mechanismen:
- Festkörperdiffusion: Der wichtigste Mechanismus für die Bindung und Verdichtung von Partikeln.
- Wachstum des Getreides: Die Partikel verschmelzen, was zu größeren Körnern und reduzierten Korngrenzen führt.
- Volumenschrumpfung: Die Porosität nimmt ab, was zu einem dichteren Endprodukt führt.
-
Faktoren, die die Sinterung beeinflussen:
- Temperatur: Muss hoch genug sein, um die Diffusion zu fördern, aber unterhalb des Schmelzpunktes liegen.
- Zeit: Längere Sinterzeiten verbessern die Bindung und Verdichtung.
- Atmosphäre: Kontrollierte Umgebungen (z. B. Inertgase) verhindern Oxidation und Kontamination.
- Eigenschaften des Pulvers: Größe, Form und Verteilung der Partikel beeinflussen das Sinterergebnis.
-
Vorteile gegenüber dem Schmelzen:
- Energie-Effizienz: Benötigt weniger Energie, da das Material nicht vollständig geschmolzen wird.
- Material Vielseitigkeit: Geeignet für Materialien mit extrem hohem Schmelzpunkt.
- Abmessungskontrolle: Ermöglicht eine präzise Formgebung und minimale Schrumpfung.
-
Herausforderungen und Überlegungen:
- Kontrolle der Porosität: Erzielung einer gleichmäßigen Verdichtung ohne Restporosität.
- Thermisches Management: Verhinderung von Verformungen oder Rissen durch ungleichmäßige Erwärmung oder Abkühlung.
- Auswahl des Materials: Gewährleistung der Kompatibilität zwischen dem Pulver und den Sinterbedingungen.
Wenn die Käufer von Geräten und Verbrauchsmaterialien diese wichtigen Punkte kennen, können sie fundierte Entscheidungen über die für ihre spezifischen Anwendungen erforderlichen Materialien und Verfahren treffen und so optimale Leistung und Kosteneffizienz gewährleisten.
Zusammenfassende Tabelle:
Aspekt | Einzelheiten |
---|---|
Definition | Wärmebehandlungsverfahren, das pulverförmige Materialien ohne Schmelzen verbindet. |
Vorteile | Verdichtung, verbesserte mechanische Eigenschaften, Kosteneffizienz. |
Prozess-Schritte | Verdichtung, Erwärmung, Verklebung, Abkühlung. |
Anwendungen | Pulvermetallurgie, Keramik, Elektronik, hochschmelzende Materialien. |
Wichtige Mechanismen | Festkörperdiffusion, Kornwachstum, Volumenschrumpfung. |
Beeinflussende Faktoren | Temperatur, Zeit, Atmosphäre, Pulvereigenschaften. |
Vorteile gegenüber dem Schmelzen | Energieeffizienz, Materialvielfalt, Maßhaltigkeit. |
Herausforderungen | Porositätskontrolle, Wärmemanagement, Materialauswahl. |
Sind Sie bereit, Ihren Herstellungsprozess durch thermisches Sintern zu optimieren? Kontaktieren Sie unsere Experten noch heute um loszulegen!