Die Abscheidung dünner Schichten ist ein wichtiger Prozess bei der Herstellung integrierter Schaltungen (IC), bei dem eine dünne Materialschicht auf ein Substrat aufgebracht wird, um dessen Eigenschaften zu verändern oder funktionelle Schichten zu erzeugen.Dieses Verfahren ist für die Herstellung von Halbleitern, optischen Geräten und anderen Mikro-/Nanobauteilen unerlässlich.Dünne Schichten, die in der Regel weniger als 1000 Nanometer dick sind, werden erzeugt, indem Partikel aus einer Quelle emittiert, zu einem Substrat transportiert und auf dessen Oberfläche kondensiert werden.Bei diesem Prozess können verschiedene Techniken zum Einsatz kommen, z. B. thermisches Verdampfen, Sputtern, Ionenstrahlabscheidung oder chemische Gasphasenabscheidung, die jeweils einzigartige Merkmale in Bezug auf Abscheidungsgeschwindigkeit, Materialkompatibilität und resultierende Schichteigenschaften aufweisen.Die Dünnschichtabscheidung wird eingesetzt, um die elektrischen, optischen, mechanischen und chemischen Eigenschaften von Materialien zu verändern, was sie in der modernen Elektronik und Materialwissenschaft unverzichtbar macht.
Die wichtigsten Punkte werden erklärt:
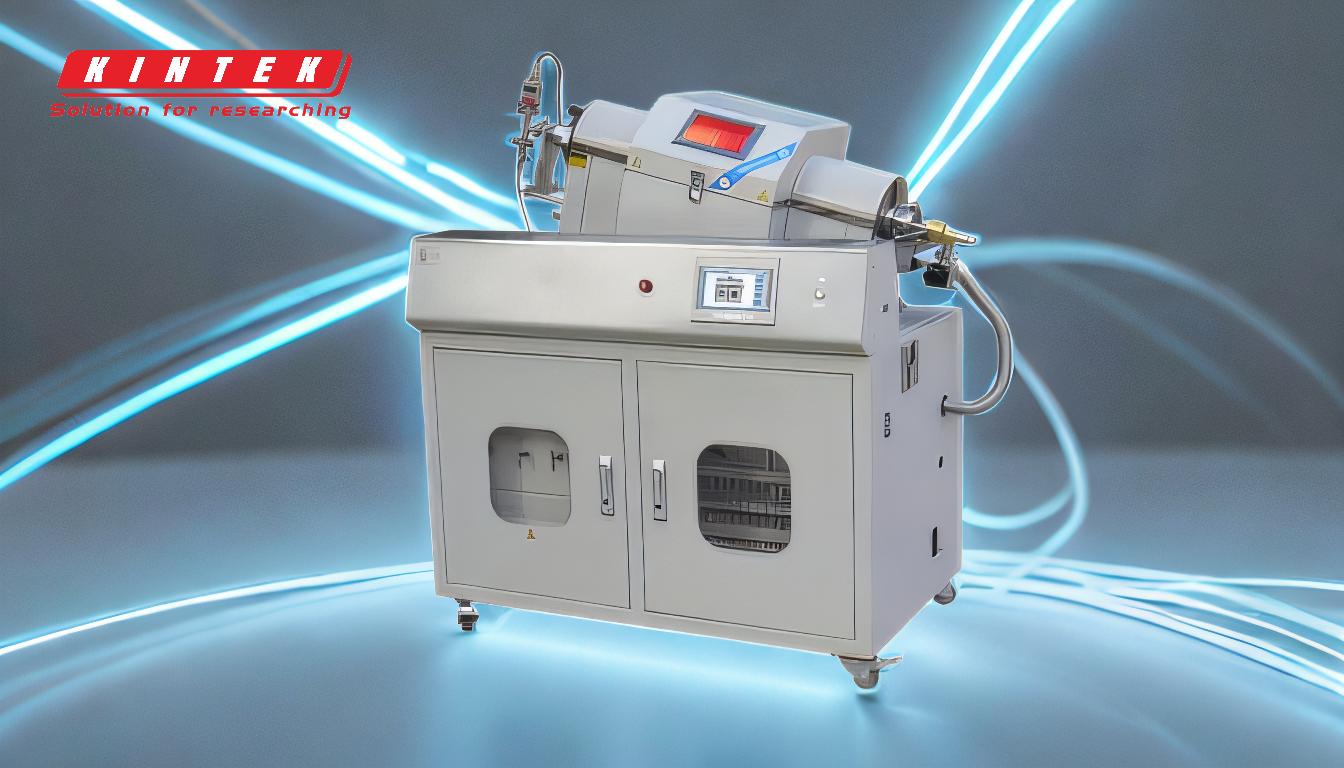
-
Definition und Zweck der Dünnschichtabscheidung:
- Bei der Dünnschichtabscheidung wird eine dünne Materialschicht (im Bereich von Nanometern bis Mikrometern) auf ein Substrat aufgebracht, um dessen Oberflächeneigenschaften zu verändern oder funktionelle Schichten zu erzeugen.
- Es ist ein grundlegender Schritt in der IC-Fertigung und ermöglicht die Herstellung von leitenden, isolierenden oder halbleitenden Schichten, die für elektronische Geräte benötigt werden.
- Das Verfahren wird auch in anderen Branchen wie der Optik, der Solartechnik und der Datenspeicherung eingesetzt, um Materialeigenschaften wie Leitfähigkeit, Verschleißfestigkeit und Korrosionsbeständigkeit zu verbessern.
-
Prozess-Übersicht:
- Emission:Partikel werden von einem Ausgangsmaterial (z. B. einem festen Ziel oder Gas) emittiert.
- Transport:Diese Partikel werden durch ein Medium (oft ein Vakuum) zum Substrat transportiert.
- Kondensation:Die Partikel kondensieren auf der Substratoberfläche und bilden einen dünnen Film.
- Das Verfahren wird in der Regel in einer Vakuumkammer durchgeführt, um die Verunreinigung zu minimieren und eine genaue Kontrolle über die Abscheidung zu gewährleisten.
-
Bei der Dünnschichtabscheidung verwendete Techniken:
-
Physikalische Gasphasenabscheidung (PVD):
- Dazu gehören Verfahren wie thermisches Verdampfen, Sputtern und Ionenstrahlbeschichtung.
- Beim thermischen Verdampfen wird ein Material erhitzt, bis es verdampft, und dann auf dem Substrat kondensiert.
- Beim Sputtern werden mit hochenergetischen Ionen Atome aus einem Zielmaterial herausgelöst, die sich dann auf dem Substrat ablagern.
-
Chemische Gasphasenabscheidung (CVD):
- Es handelt sich um chemische Reaktionen zwischen gasförmigen Vorläufern, die einen festen Film auf dem Substrat bilden.
- Bietet eine hervorragende Konformität und ist für komplexe Geometrien geeignet.
-
Atomlagenabscheidung (ALD):
- Eine Untergruppe des CVD-Verfahrens, bei dem eine Schicht nach der anderen abgeschieden wird, was eine außergewöhnliche Kontrolle und Gleichmäßigkeit der Schichtdicke ermöglicht.
-
Physikalische Gasphasenabscheidung (PVD):
-
Anwendungen in der IC-Fertigung:
-
Die Dünnschichtabscheidung wird zur Herstellung von:
- Leitende Schichten (z. B. Kupfer- oder Aluminium-Verbindungen).
- Isolierende Schichten (z. B. Siliziumdioxid oder Siliziumnitrid).
- Halbleitende Schichten (z. B. Silizium oder Galliumarsenid).
- Sie ermöglichen die Miniaturisierung elektronischer Komponenten und die Integration mehrerer Funktionen auf einem einzigen Chip.
-
Die Dünnschichtabscheidung wird zur Herstellung von:
-
Auswirkungen auf die Materialeigenschaften:
- Dünne Schichten können die elektrischen, optischen, mechanischen und chemischen Eigenschaften des Substrats verändern.
-
Zum Beispiel:
- Leitende Schichten verbessern die elektrische Leitfähigkeit in Verbindungen.
- Optische Folien verbessern die Lichtdurchlässigkeit oder -reflexion in Linsen und Spiegeln.
- Schutzfolien erhöhen die Verschleißfestigkeit und Korrosionsbeständigkeit mechanischer Komponenten.
-
Herausforderungen und Überlegungen:
- Einheitlichkeit:Die Erzielung einer gleichmäßigen Schichtdicke über das gesamte Substrat ist entscheidend für die Leistung des Geräts.
- Haftung:Für die Haltbarkeit ist es wichtig, dass die Folie gut auf dem Substrat haftet.
- Reinheit:Die Minimierung von Verunreinigungen in der Folie ist entscheidend für die Erhaltung der gewünschten Eigenschaften.
- Skalierbarkeit:Das Verfahren muss für die Massenproduktion in der Industrie skalierbar sein.
-
Zukünftige Trends:
- Die Fortschritte bei der Dünnschichtabscheidung werden durch die Nachfrage nach kleineren, schnelleren und effizienteren elektronischen Geräten vorangetrieben.
- Neue Techniken wie ALD und plasmaunterstützte CVD ermöglichen die Abscheidung ultradünner Schichten mit präziser Kontrolle.
- Die Integration der Dünnschichtabscheidung mit anderen Nanofabrikationstechniken eröffnet neue Möglichkeiten für fortschrittliche Materialien und Geräte.
Wenn die Hersteller die Prinzipien und Anwendungen der Dünnschichtabscheidung verstehen, können sie ihre Prozesse optimieren, um die sich ständig weiterentwickelnden Anforderungen der IC-Fertigung und anderer Hightech-Industrien zu erfüllen.
Zusammenfassende Tabelle:
Hauptaspekt | Einzelheiten |
---|---|
Definition | Aufbringen einer dünnen Schicht (Nanometer bis Mikrometer) zur Veränderung der Substrateigenschaften. |
Techniken | Physikalische Gasphasenabscheidung (PVD), chemische Gasphasenabscheidung (CVD), ALD. |
Anwendungen | IC-Fertigung, Optik, Solarzellen, Datenspeicherung. |
Aufprall | Veränderung der elektrischen, optischen, mechanischen und chemischen Eigenschaften. |
Herausforderungen | Gleichmäßigkeit, Haftung, Reinheit, Skalierbarkeit. |
Zukünftige Trends | Ultradünne Schichten, plasmagestützte CVD, Integration mit Nanofabrikation. |
Optimieren Sie Ihren Dünnschichtabscheidungsprozess - Kontaktieren Sie unsere Experten noch heute !