Die Vakuum-Dünnschichtabscheidung ist ein spezielles Verfahren, mit dem unter Vakuumbedingungen extrem dünne Materialschichten auf ein Substrat aufgebracht werden.Diese Schichten, die zwischen Angström und Mikron dick sind, können aus einem einzigen Material oder aus mehreren Materialien bestehen, die in Schichtstrukturen angeordnet sind.Das Verfahren ist in Branchen wie Halbleiter, Optik, Luft- und Raumfahrt und Energie weit verbreitet und ermöglicht die Herstellung von Beschichtungen mit spezifischen Eigenschaften wie verbesserter Leitfähigkeit, Korrosionsbeständigkeit, optischer Leistung und mehr.Die Vakuumbeschichtung ist unverzichtbar für Anwendungen wie optische Beschichtungen, Halbleiterbauelemente, Solarzellen und dekorative Oberflächen, was sie zu einem Eckpfeiler der modernen Fertigung und Technologie macht.
Die wichtigsten Punkte erklärt:
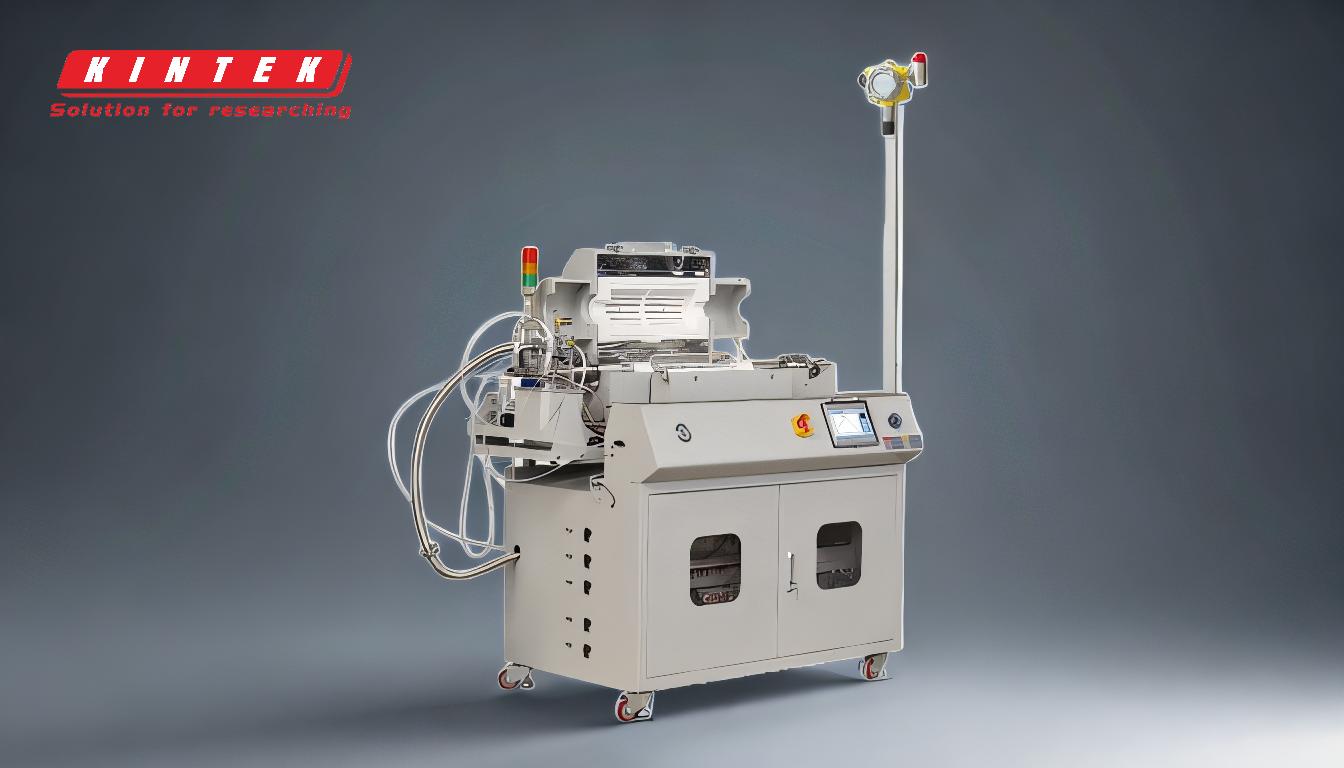
-
Definition und Zweck der Vakuum-Dünnschichtabscheidung
- Die Vakuum-Dünnschichtabscheidung ist ein Verfahren, bei dem dünne Materialschichten in einer Vakuumumgebung auf ein Substrat aufgebracht werden.
- Ziel ist es, Beschichtungen mit bestimmten Eigenschaften zu erzeugen, wie z. B. verbesserte optische Leistung, elektrische Leitfähigkeit, Korrosionsbeständigkeit oder dekorative Oberflächen.
- Die Dicke dieser Schichten reicht in der Regel von Angström (10^-10 Meter) bis zu Mikron (10^-6 Meter).
-
So funktioniert die Vakuum-Dünnschichtabscheidung
- Das Verfahren findet in einer Vakuumkammer statt, um Verunreinigungen zu beseitigen und die Reinheit des abgeschiedenen Materials zu gewährleisten.
- Die Materialien werden im Vakuum verdampft oder gesputtert und kondensieren dann auf dem Substrat und bilden eine dünne Schicht.
- Die Vakuumumgebung ermöglicht eine präzise Steuerung des Abscheidungsprozesses und gewährleistet Gleichmäßigkeit und Haftung auf dem Substrat.
-
Anwendungen der Vakuum-Dünnschichtabscheidung
- Optische Beschichtungen: Zur Verbesserung der Übertragungs-, Reflexions- und Brechungseigenschaften von Linsen, Spiegeln und anderen optischen Geräten.
- Halbleiterindustrie: Unerlässlich für die Herstellung von leitenden oder isolierenden Schichten in integrierten Schaltungen und Halbleitergeräten.
- Energieanwendungen: Verwendung in Solarzellen, Batterien und energieeffizienten Beschichtungen.
- Dekorative und schützende Beschichtungen: Werden aus ästhetischen Gründen auf Oberflächen aufgetragen oder um Verschleißfestigkeit und Korrosionsschutz zu gewährleisten.
- Fortschrittliche Technologien: Ermöglicht die Schaffung ultrakleiner Strukturen wie Quantencomputer und Arzneimittelverabreichungssysteme.
-
Bei der Dünnschichtabscheidung verwendete Materialien
- Je nach Anwendung können sowohl anorganische als auch organische Materialien abgeschieden werden.
- Zu den gängigen Materialien gehören Metalle, Keramiken und Polymere, die aufgrund ihrer spezifischen Eigenschaften wie Leitfähigkeit, Härte oder optische Leistung ausgewählt werden.
-
Vorteile der Vakuum-Dünnschichtabscheidung
- Präzision: Ermöglicht die Abscheidung extrem dünner und gleichmäßiger Schichten.
- Reinheit: Die Vakuumumgebung verhindert Verunreinigungen und gewährleistet hochwertige Beschichtungen.
- Vielseitigkeit: Kann für die Abscheidung einer breiten Palette von Materialien für verschiedene Anwendungen verwendet werden.
- Skalierbarkeit: Sowohl für die Forschung im kleinen Maßstab als auch für die industrielle Großproduktion geeignet.
-
Industrien, die auf die Vakuum-Dünnschichtabscheidung angewiesen sind
- Halbleiter und Elektronik: Für die Züchtung elektronischer Materialien und die Herstellung funktioneller Schichten in Geräten.
- Luft- und Raumfahrt: Zur Herstellung von thermischen und chemischen Barrierebeschichtungen, die vor rauen Umgebungen schützen.
- Optik: Verleiht Linsen und Spiegeln die gewünschten Reflexions- und Durchlässigkeitseigenschaften.
- Energie: Für die Herstellung von Solarzellen, Batterien und energieeffizienten Beschichtungen.
- Automobilindustrie: Für korrosionsbeständige und dekorative Beschichtungen.
-
Zukünftige Trends und Innovationen
- Die Entwicklung neuer Materialien und Abscheidungstechniken erweitert die Möglichkeiten der Dünnschichttechnologie.
- Anwendungen in neuen Bereichen wie Quantencomputing, flexible Elektronik und fortschrittliche medizinische Geräte treiben die Innovation voran.
- Die Bemühungen um Nachhaltigkeit konzentrieren sich auf die Reduzierung von Abfällen und die Verbesserung der Energieeffizienz im Beschichtungsprozess.
Wenn die Käufer von Anlagen und Verbrauchsmaterialien diese Kernpunkte verstehen, können sie fundierte Entscheidungen über die Materialien und Technologien treffen, die sie für ihre spezifischen Anwendungen bei der Vakuum-Dünnschichtabscheidung benötigen.
Zusammenfassende Tabelle:
Aspekt | Einzelheiten |
---|---|
Prozess | Aufbringen dünner Materialschichten in einer Vakuumumgebung. |
Dickenbereich | Angström (10^-10 Meter) bis Mikrometer (10^-6 Meter). |
Wichtigste Anwendungen | Optische Beschichtungen, Halbleiter, Solarzellen, dekorative Veredelungen. |
Verwendete Materialien | Metalle, Keramiken, Polymere, ausgewählt nach Leitfähigkeit, Härte oder Optik. |
Vorteile | Präzision, Reinheit, Vielseitigkeit, Skalierbarkeit. |
Branchen | Halbleiter, Luft- und Raumfahrt, Optik, Energie, Automobil. |
Zukünftige Trends | Quantencomputer, flexible Elektronik, Verbesserung der Nachhaltigkeit. |
Entdecken Sie, wie die Vakuum-Dünnschichtabscheidung Ihre Anwendungen verändern kann. Kontaktieren Sie unsere Experten noch heute !