Diamantähnliche Kohlenstoffschichten (DLC) werden im Vergleich zu anderen Beschichtungsverfahren in der Regel bei relativ niedrigen Temperaturen aufgebracht und eignen sich daher für eine Vielzahl von Substraten, einschließlich temperaturempfindlicher Materialien.Die Abscheidungstemperatur für DLC-Beschichtungen liegt im Allgemeinen zwischen 100°C bis 300°C abhängig von der jeweiligen Abscheidungsmethode und den gewünschten Eigenschaften der Beschichtung.Diese Niedrigtemperaturanwendung ist einer der Hauptvorteile von DLC, da sie die thermische Belastung und Verformung des Substrats minimiert.Bei diesem Verfahren kommen häufig Techniken wie die plasmaunterstützte chemische Gasphasenabscheidung (PECVD) oder die physikalische Gasphasenabscheidung (PVD) zum Einsatz, mit denen sich die Eigenschaften der Beschichtung, einschließlich Härte, Reibungskoeffizient und Haftung, genau steuern lassen.
Die wichtigsten Punkte werden erklärt:
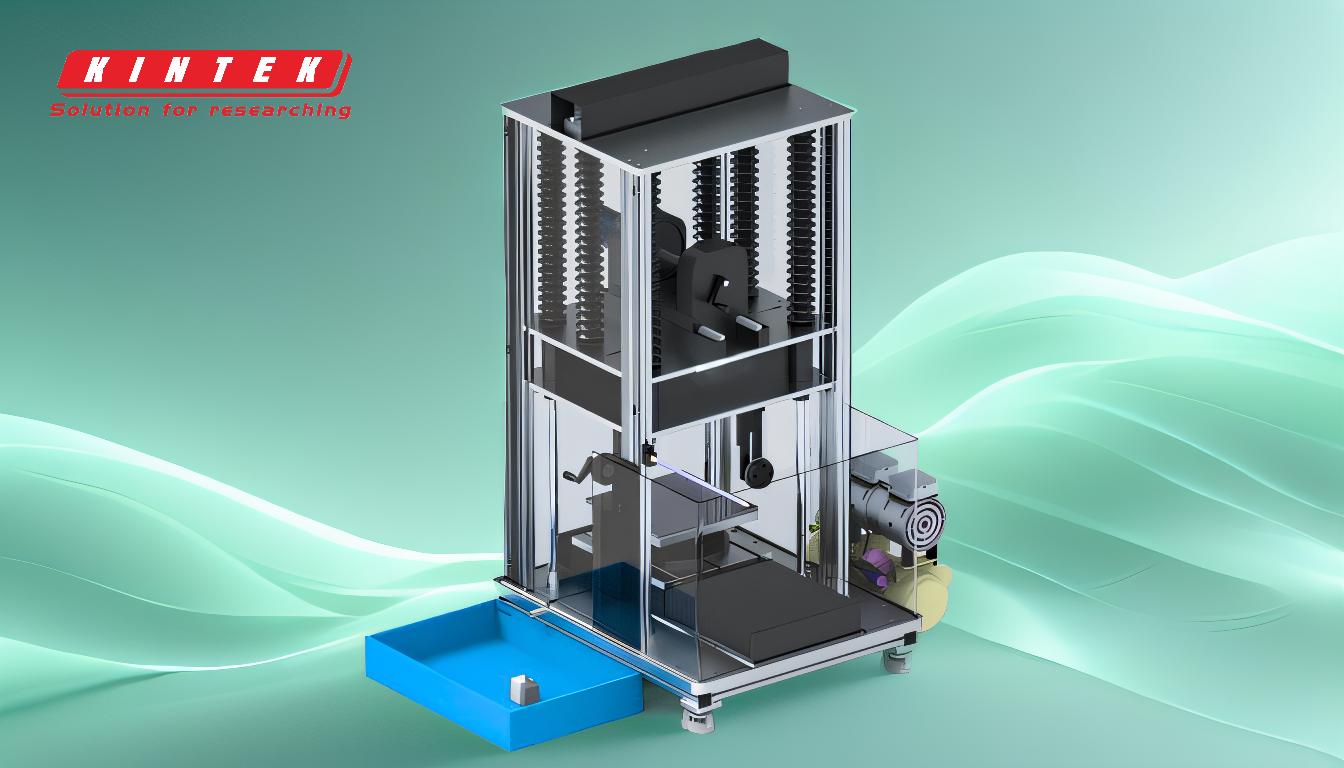
-
Temperaturbereich für die DLC-Beschichtung
- DLC-Beschichtungen werden in der Regel bei Temperaturen zwischen 100°C bis 300°C .
- Dieser Bereich ist deutlich niedriger als bei vielen anderen Beschichtungsverfahren, wie z. B. dem thermischen Spritzen oder dem Hochtemperatur-CVD-Verfahren, das 800 °C überschreiten kann.
- Die Abscheidung bei niedrigen Temperaturen ist entscheidend für Substrate wie Kunststoffe, Polymere oder wärmebehandelte Metalle, die sich bei höheren Temperaturen zersetzen oder verformen können.
-
Abscheidungsmethoden und ihr Einfluss auf die Temperatur
-
Plasmaunterstützte chemische Gasphasenabscheidung (PECVD):
- PECVD ist die gängigste Methode zum Aufbringen von DLC-Schichten.Es arbeitet mit relativ niedrigen Temperaturen (100°C-300°C) und nutzt Plasma zur Aktivierung des Abscheidungsprozesses.
- Mit dieser Methode lassen sich die Eigenschaften der Beschichtung, wie Härte und Haftung, hervorragend steuern, während die Substrattemperatur niedrig gehalten wird.
-
Physikalische Gasphasenabscheidung (PVD):
- PVD-Verfahren wie Sputtern oder Bogenverdampfung können ebenfalls zur Abscheidung von DLC-Beschichtungen verwendet werden.Diese Verfahren arbeiten in der Regel mit etwas höheren Temperaturen (200°C-300°C), die jedoch für die meisten Substrate noch im sicheren Bereich liegen.
-
Plasmaunterstützte chemische Gasphasenabscheidung (PECVD):
-
Vorteile der Niedertemperaturabscheidung
-
Kompatibilität der Substrate:
- Durch den Niedrigtemperaturprozess eignet sich DLC für eine Vielzahl von Substraten, darunter Metalle, Keramiken und Polymere.
-
Minimierte thermische Belastung:
- Durch die Vermeidung hoher Temperaturen verringern DLC-Beschichtungen das Risiko von thermischer Verformung, Verziehen oder Abbau des Substratmaterials.
-
Verbesserte Adhäsion:
- Niedrigere Temperaturen tragen dazu bei, die Integrität der Substrat-Beschichtungs-Grenzfläche zu erhalten, was die Haftung und die Gesamtleistung verbessert.
-
Kompatibilität der Substrate:
-
Faktoren, die die Abscheidetemperatur beeinflussen
-
Material des Substrats:
- Die thermische Stabilität des Substratmaterials spielt eine wichtige Rolle bei der Bestimmung der maximal zulässigen Abscheidungstemperatur.Für Polymere können beispielsweise Temperaturen unter 150 °C erforderlich sein, während Metalle höhere Temperaturen vertragen können.
-
Eigenschaften der Beschichtung:
- Die gewünschten Eigenschaften der DLC-Beschichtung, wie Härte, Reibungskoeffizient oder Verschleißfestigkeit, können die Beschichtungstemperatur beeinflussen.Höhere Temperaturen können manchmal die Schichtdichte und die Haftung verbessern, müssen aber gegen die Einschränkungen des Substrats abgewogen werden.
-
Beschichtungstechnik:
- Verschiedene Techniken (z. B. PECVD vs. PVD) haben unterschiedliche Temperaturanforderungen und Möglichkeiten, die bei der Auswahl der geeigneten Methode berücksichtigt werden müssen.
-
Material des Substrats:
-
Anwendungen von DLC-Beschichtungen
- DLC-Beschichtungen werden in Branchen wie der Automobilindustrie, der Luft- und Raumfahrt, der Medizintechnik und der Unterhaltungselektronik aufgrund ihrer hervorragenden Verschleißfestigkeit, geringen Reibung und Biokompatibilität häufig eingesetzt.
- Die Möglichkeit, diese Beschichtungen bei niedrigen Temperaturen aufzubringen, ist besonders vorteilhaft für Komponenten wie Kunststoffzahnräder, medizinische Implantate und präzisionsgefertigte Teile, bei denen Hochtemperaturprozesse Schäden verursachen könnten.
-
Herausforderungen und Überlegungen
-
Probleme mit der Adhäsion:
- Niedrige Temperaturen sind zwar vorteilhaft, können aber manchmal zu einer schwächeren Haftung zwischen der Beschichtung und dem Substrat führen.Eine ordnungsgemäße Oberflächenvorbereitung, wie z. B. Reinigen und Ätzen, ist entscheidend für eine starke Haftung.
-
Gleichmäßigkeit und Kontrolle der Schichtdicke:
- Das Erreichen einer gleichmäßigen Schichtdicke und gleichmäßiger Eigenschaften kann bei niedrigeren Temperaturen eine Herausforderung sein und erfordert eine präzise Steuerung der Abscheidungsparameter.
-
Kosten und Komplexität:
- Die Anlagen und Verfahren für die DLC-Beschichtung bei niedrigen Temperaturen können im Vergleich zu den Methoden bei höheren Temperaturen komplexer und kostspieliger sein, aber die Vorteile rechtfertigen oft die Investition.
-
Probleme mit der Adhäsion:
Wenn die Hersteller die Temperaturanforderungen und Abscheidungsmethoden für DLC-Beschichtungen kennen, können sie das optimale Verfahren für ihre spezifische Anwendung auswählen, das hohe Leistung und Haltbarkeit gewährleistet und gleichzeitig die Integrität des Substrats schützt.
Zusammenfassende Tabelle:
Aspekt | Einzelheiten |
---|---|
Temperaturbereich | 100°C bis 300°C |
Abscheidungsmethoden | PECVD (100°C-300°C), PVD (200°C-300°C) |
Vorteile | Substratkompatibilität, minimierte thermische Belastung, verbesserte Adhäsion |
Wichtigste Anwendungen | Automobilindustrie, Luft- und Raumfahrt, medizinische Geräte, Unterhaltungselektronik |
Herausforderungen | Haftungsprobleme, Kontrolle der Gleichmäßigkeit, Kosten und Komplexität der Anlagen |
Optimieren Sie Ihren Beschichtungsprozess mit DLC- Kontaktieren Sie noch heute unsere Experten für maßgeschneiderte Lösungen!