Die endgültige Sintertemperatur ist entscheidend, da sie direkten Einfluss auf die Mikrostruktur, die mechanischen Eigenschaften und die Gesamtqualität des gesinterten Materials hat. Es bestimmt das Ausmaß der Verdichtung, des Kornwachstums und der Phasenumwandlungen, die für das Erreichen der gewünschten Materialeigenschaften wie Festigkeit, Haltbarkeit und Leistung unerlässlich sind. Die präzise Steuerung der endgültigen Sintertemperatur gewährleistet eine optimale Sinterkinetik, minimiert Defekte und stimmt das Endprodukt auf die beabsichtigten Anwendungsanforderungen ab.
Wichtige Punkte erklärt:
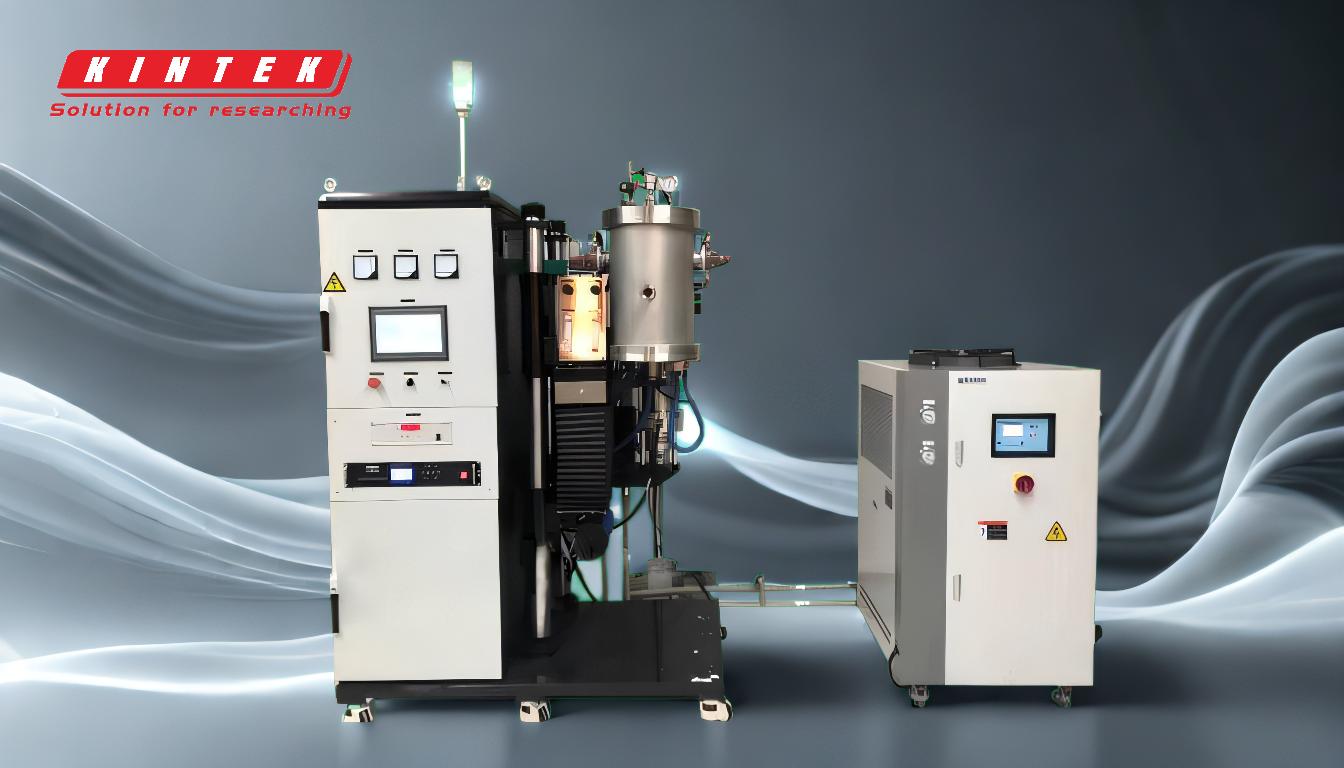
-
Einfluss auf Verdichtung und Mikrostruktur:
- Die endgültige Sintertemperatur bestimmt den Grad der Verdichtung, bei dem es sich um den Prozess der Verringerung der Porosität und der Erhöhung der Materialdichte handelt. Höhere Temperaturen verbessern die Bindungs- und Diffusionsmechanismen der Partikel und führen zu einer kompakteren und homogeneren Mikrostruktur.
- Das Kornwachstum wird auch von der Temperatur beeinflusst. Zu hohe Temperaturen können zu unkontrolliertem Kornwachstum führen, was zu einer Verschlechterung der mechanischen Eigenschaften führen kann, während zu niedrige Temperaturen zu unvollständiger Sinterung und Restporosität führen können.
-
Mechanische Eigenschaften:
- Hochtemperatursintern verbessert wichtige mechanische Eigenschaften wie Zugfestigkeit, Biegewechselfestigkeit und Schlagenergie. Diese Eigenschaften sind entscheidend für Materialien, die in anspruchsvollen Anwendungen wie der Luft- und Raumfahrt, der Automobilindustrie und medizinischen Geräten verwendet werden.
- Die Endtemperatur stellt sicher, dass das Material die gewünschte Härte, Zähigkeit und Verschleißfestigkeit erreicht, die für eine langfristige Leistungsfähigkeit unerlässlich sind.
-
Phasenumwandlungen und Materialzusammensetzung:
- Die endgültige Sintertemperatur kann Phasenumwandlungen auslösen, beispielsweise die Bildung neuer kristalliner Phasen oder die Stabilisierung bestimmter Mikrostrukturen. Diese Umwandlungen beeinflussen maßgeblich die thermischen, elektrischen und mechanischen Eigenschaften des Materials.
- Bei Materialien mit komplexer Zusammensetzung muss die Endtemperatur sorgfältig ausgewählt werden, um eine gleichmäßige Phasenverteilung sicherzustellen und unerwünschte Reaktionen oder Entmischungen zu verhindern.
-
Sinterkinetik und Diffusionsmechanismen:
- Die Temperatur ist ein Haupttreiber der Sinterkinetik und beeinflusst Prozesse wie die Korngrenzendiffusion und die Massendiffusion. Diese Mechanismen sind für die Partikelbindung und -verdichtung verantwortlich.
- Höhere Temperaturen beschleunigen die Diffusion und ermöglichen so ein schnelleres Sintern und eine bessere Partikelumlagerung. Allerdings müssen auch die Aufheiz- und Abkühlgeschwindigkeit kontrolliert werden, um thermische Spannungen oder ungleichmäßiges Sintern zu vermeiden.
-
Kontrolle von Porosität und Defekten:
- Die endgültige Sintertemperatur spielt eine entscheidende Rolle bei der Minimierung der Porosität und der Beseitigung von Defekten. Eine ordnungsgemäße Temperaturkontrolle stellt sicher, dass das Material seine theoretische Dichte erreicht, ohne dass Risse oder Hohlräume entstehen.
- Unvollständiges Sintern aufgrund unzureichender Temperatur kann Restporosität hinterlassen, die das Material schwächt und seine Leistung in kritischen Anwendungen verringert.
-
Einfluss der Sinterumgebung:
- Die Sinteratmosphäre (z. B. Luft, Vakuum oder Inertgase) interagiert mit der Endtemperatur und beeinflusst die Eigenschaften des Materials. Beispielsweise kann eine Vakuumumgebung Oxidation verhindern und die Verdichtung bei hohen Temperaturen verbessern.
- Auch die Wahl des Sinterofens und dessen Temperaturgleichmäßigkeit sind entscheidend, um über das gesamte Material hinweg konsistente Ergebnisse zu erzielen.
-
Anwendungsspezifische Anforderungen:
- Die endgültige Sintertemperatur muss auf den vorgesehenen Einsatzzweck des Materials abgestimmt sein. Beispielsweise müssen Materialien, die in Umgebungen mit hohen Temperaturen verwendet werden, möglicherweise bei erhöhten Temperaturen gesintert werden, um Stabilität und Leistung unter Betriebsbedingungen sicherzustellen.
- Die Temperatur wird oft angepasst, um je nach Anwendung bestimmte Eigenschaften wie Wärmeleitfähigkeit, elektrischen Widerstand oder Korrosionsbeständigkeit zu erreichen.
-
Prozessoptimierung und -konsistenz:
- Die präzise Steuerung der endgültigen Sintertemperatur gewährleistet die Wiederholbarkeit und Konsistenz des Prozesses, die für die industrielle Produktion unerlässlich sind. Temperaturschwankungen können zu Chargeninkonsistenzen führen und die Produktqualität und -zuverlässigkeit beeinträchtigen.
- Fortschrittliche Sintertechniken wie Funkenplasmasintern oder heißisostatisches Pressen basieren auf einer genauen Temperaturkontrolle, um hervorragende Materialeigenschaften zu erzielen.
Zusammenfassend ist die endgültige Sintertemperatur ein kritischer Parameter, der sich direkt auf die Mikrostruktur, die mechanischen Eigenschaften und die Gesamtleistung des Materials auswirkt. Es muss sorgfältig ausgewählt und kontrolliert werden, um den spezifischen Anforderungen des Materials und seiner beabsichtigten Anwendung gerecht zu werden und optimale Ergebnisse und gleichbleibende Qualität zu gewährleisten.
Übersichtstabelle:
Aspekt | Einfluss der endgültigen Sintertemperatur |
---|---|
Verdichtung und Mikrostruktur | Steuert die Reduzierung der Porosität, die Partikelbindung und das Kornwachstum. Höhere Temperaturen verbessern die Homogenität. |
Mechanische Eigenschaften | Verbessert Zugfestigkeit, Härte, Zähigkeit und Verschleißfestigkeit für anspruchsvolle Anwendungen. |
Phasentransformationen | Löst die Bildung neuer Phasen aus und beeinflusst die thermischen, elektrischen und mechanischen Eigenschaften. |
Sinterkinetik | Beschleunigt Diffusionsmechanismen für schnelleres Sintern und bessere Partikelumlagerung. |
Porosität und Defekte | Minimiert Porosität und Defekte und stellt sicher, dass das Material die theoretische Dichte erreicht. |
Sinterumgebung | Interagiert mit der Atmosphäre (z. B. Vakuum), um die Verdichtung zu verbessern und Oxidation zu verhindern. |
Bewerbungsvoraussetzungen | Passt die Temperatur an den Verwendungszweck des Materials an und sorgt so für Stabilität und Leistung. |
Prozesskonsistenz | Gewährleistet Wiederholbarkeit und Konsistenz in der industriellen Produktion und vermeidet Abweichungen von Charge zu Charge. |
Benötigen Sie Hilfe bei der Optimierung Ihres Sinterprozesses? Kontaktieren Sie noch heute unsere Experten für maßgeschneiderte Lösungen!