Einführung in die CVD-Technologie
Definition und Bedeutung
Die chemische Gasphasenabscheidung (Chemical Vapor Deposition, CVD) ist eine zentrale Technologie für die Abscheidung dünner Schichten, die bei der Halbleiterherstellung und in einer Vielzahl anderer Industriezweige eine entscheidende Rolle spielt. Diese Technologie ermöglicht die präzise und kontrollierte Abscheidung dünner Schichten auf verschiedenen Substraten, was für die Herstellung von elektronischen Bauteilen, optischen Beschichtungen und Schutzschichten unerlässlich ist.
In der Halbleiterfertigung ist CVD unverzichtbar für die Herstellung hochwertiger, gleichmäßiger Schichten, die die Leistung und Zuverlässigkeit integrierter Schaltungen verbessern. Die Fähigkeit, Materialien mit spezifischen Eigenschaften wie Leitfähigkeit, Isolierung und optischer Transparenz abzuscheiden, macht CVD zu einem unverzichtbaren Werkzeug bei der Herstellung moderner mikroelektronischer Geräte.
Neben Halbleitern findet die CVD auch in der Displaytechnologie breite Anwendung, wo sie zur Abscheidung von Indium-Zinn-Oxid- (ITO) und Kupferschichten eingesetzt wird, um die Funktionalität und Haltbarkeit von Displaygeräten zu verbessern. Darüber hinaus wird CVD bei der Herstellung von optischen Beschichtungen für Linsen und Spiegel sowie von Korrosionsschutzschichten für Metalloberflächen eingesetzt, was die Vielseitigkeit des Verfahrens in verschiedenen Bereichen belegt.
Die Bedeutung der CVD liegt nicht nur in ihren vielfältigen Anwendungsmöglichkeiten, sondern auch in ihrer Fähigkeit, Schichten mit außergewöhnlicher Gleichmäßigkeit, Haftung und Kontrollierbarkeit herzustellen. Diese Eigenschaften machen CVD zu einer unverzichtbaren Technologie für die Weiterentwicklung verschiedener Branchen und die Förderung von Innovationen in der Materialwissenschaft.
Arbeitsprinzip der CVD
Chemischer Reaktionsprozess
Bei der chemischen Gasphasenabscheidung (CVD) beruht die Bildung dünner Schichten auf einer kontrollierten chemischen Reaktion. Zunächst werden in die Reaktionskammer Gasvorläufer, die Ausgangsstoffe für die gewünschte Schicht, eingeleitet. Bei diesen Vorläufern handelt es sich in der Regel um flüchtige Verbindungen, die leicht verdampft werden können. In der Kammer werden diese Gase dann erhitzt, wobei die Temperatur je nach Ausgangsstoff und gewünschten Folieneigenschaften oft zwischen mehreren hundert und tausend Grad Celsius liegt.
Der Erhitzungsprozess ist von entscheidender Bedeutung, da er den Gasmolekülen die nötige Energie liefert, um ihre Aktivierungsenergiebarrieren zu überwinden und damit zu reagieren. Mit steigender Temperatur zersetzen sich die Gasvorläufer und reagieren miteinander oder mit der Oberfläche des Substrats. Diese Reaktion findet in der Regel an der Substratoberfläche statt, wo die Ausgangsstoffe adsorbiert werden und sich dann weiter zersetzen oder verbinden. Zu den aus diesen Reaktionen resultierenden Produkten gehören das gewünschte Filmmaterial, das sich auf dem Substrat abscheidet, und Nebenprodukte, die in der Regel gasförmig sind und aus dem System abgeleitet werden.
Bei der Abscheidung von Siliziumschichten beispielsweise ist ein gängiges Vorprodukt Silan (SiH4). Beim Erhitzen zerfällt das Silan in Silizium und Wasserstoffgas. Die Siliziumatome lagern sich dann auf dem Substrat ab und bilden einen kontinuierlichen Film, während das Wasserstoffgas aus der Reaktionskammer abgesaugt wird. Dieses Beispiel veranschaulicht den dynamischen Charakter des CVD-Verfahrens, bei dem eine präzise Steuerung der Temperatur und der Durchflussmengen der Ausgangsstoffe unerlässlich ist, um die gewünschte Schichtqualität und Gleichmäßigkeit zu erreichen.
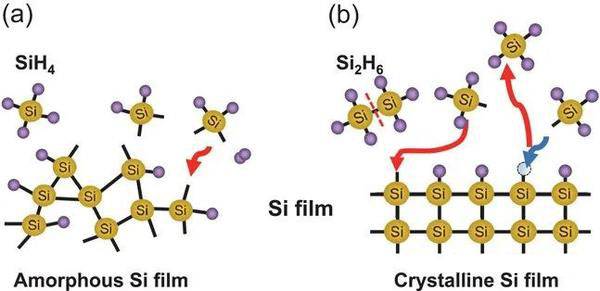
Der chemische Reaktionsprozess bei der CVD ist nicht auf einfache Zersetzungen beschränkt, sondern kann auch komplexe Reaktionen wie Oxidation, Nitrierung oder die Bildung von Verbundstoffen umfassen. Diese Reaktionen werden häufig durch das Vorhandensein zusätzlicher Reaktionsgase wie Sauerstoff oder Stickstoff erleichtert, die in die Kammer eingeleitet werden, um die Schichteigenschaften zu verändern. Bei der Abscheidung von Siliziumdioxid (SiO2)-Filmen wird beispielsweise Silan mit Sauerstoff zur Bildung der Oxidschicht umgesetzt.
Beispiel einer Reaktion
Bei der chemischen Gasphasenabscheidung (CVD) ist eine der wichtigsten Reaktionen die Zersetzung von Trichlorsilan (SiHCl₃). Dieser Prozess ist von grundlegender Bedeutung für die Bildung dünner Schichten, insbesondere bei der Halbleiterherstellung. Wenn SiHCl₃ erhitzt wird, durchläuft es eine komplexe chemische Umwandlung. Das Ausgangsmaterial für Silizium, SiHCl₃, zerfällt in elementares Silizium, das sich dann auf dem Substrat ablagert. Gleichzeitig werden Chlor (Cl₂) und Salzsäure (HCl) als Nebenprodukte freigesetzt. Diese Gase werden in der Regel aus der Reaktionskammer abgesaugt, um sicherzustellen, dass sie den Abscheidungsprozess nicht beeinträchtigen.
Diese Reaktion veranschaulicht das Kernprinzip der CVD, bei der Vorläufergase durch kontrollierte chemische Reaktionen in feste Schichten umgewandelt werden. Die Zersetzung von SiHCl₃ liefert nicht nur das notwendige Silizium für die Filmbildung, sondern verdeutlicht auch die Bedeutung des Gasmanagements für die Aufrechterhaltung einer sauberen und effizienten Abscheidungsumgebung. Die Nebenproduktgase Cl₂ und HCl müssen unbedingt überwacht und gesteuert werden, da ihr Vorhandensein die Qualität und Gleichmäßigkeit der abgeschiedenen Schicht beeinträchtigen kann.
Klassifizierung von CVD
Thermische CVD
Bei der thermischen chemischen Gasphasenabscheidung (CVD) werden die Vorstufengase in einer Reaktionskammer auf eine hohe Temperatur, in der Regel über 700 °C, erhitzt. Diese hohe Temperatur ist entscheidend für die Zersetzung der Vorläufergase, die sich dann auf dem Substrat ablagern und eine dünne Schicht bilden. Das Verfahren beruht auf der thermischen Energie, die die für die Filmbildung erforderlichen chemischen Reaktionen antreibt und dafür sorgt, dass der abgeschiedene Film verbesserte Eigenschaften wie eine höhere Kristallinität, eine größere Dichte und schnellere Abscheidungsraten aufweist.
Bei der thermischen CVD werden die gasförmigen Reaktanten häufig durch ein Inertgas wie Stickstoff in die Reaktorkammer geleitet, was zur Aufrechterhaltung einer kontrollierten Umgebung beiträgt. Die hohen Temperaturen erleichtern nicht nur die Zersetzung der Ausgangsstoffe, sondern ermöglichen auch Reaktionen, die bei niedrigeren Temperaturen nicht möglich wären. Diese hohen Temperaturen können jedoch auch Nachteile mit sich bringen, wie z. B. die Bildung von Spannungen in der Schicht, höhere Diffusionsraten von Elementen aus dem Substrat in die Schicht und eine mögliche Zersetzung des Substrats selbst.
Vorteile | Nachteile |
---|---|
Erhöhte Abscheidungsrate | Bildung von Spannungen |
Verbesserte Kristallinität | Höhere Diffusionsraten |
Größere Schichtdichte | Verschlechterung des Substrats |
Die thermische CVD ist besonders vorteilhaft bei der Halbleiterherstellung, wo sie zur Abscheidung dünner Schichten wie Siliziumdioxid, Siliziumnitrid und Polysilizium auf Siliziumwafern eingesetzt wird. Diese Schichten sind für die Herstellung von integrierten Schaltkreisen und anderen elektronischen Geräten unerlässlich. Trotz ihrer Vorteile erfordert die thermische CVD eine sorgfältige Steuerung der Temperatur und der Zuführungsraten der Ausgangsstoffe, um den Abscheidungsprozess zu optimieren und potenzielle Nachteile abzumildern.
Plasmaunterstützte CVD (PECVD)
Die plasmagestützte chemische Gasphasenabscheidung (Plasma Enhanced Chemical Vapor Deposition, PECVD) ist eine spezielle Variante der chemischen Gasphasenabscheidung (Chemical Vapor Deposition, CVD), bei der ein Plasma zur Erhöhung der Reaktionsgeschwindigkeit und zur genauen Steuerung des Abscheidungsprozesses eingesetzt wird. Im Gegensatz zu den herkömmlichen CVD-Methoden, die sich ausschließlich auf thermische Energie zur Zersetzung der Vorläufergase stützen, wird bei der PECVD ein Plasma zur Aktivierung der reaktiven Gase eingesetzt, was die Abscheidung bei deutlich niedrigeren Temperaturen ermöglicht, die in der Regel zwischen 100 und 600 °C liegen.
Bei der PECVD wirkt das Plasma als Katalysator, der die reaktiven Vorstufen in ihre einzelnen Atome oder Moleküle zerlegt, die dann reagieren und sich auf der Substratoberfläche ablagern. Diese plasmagestützte Aufspaltung ermöglicht die Abscheidung verschiedener Schichten, einschließlich Silizium (Si), Siliziumdioxid (SiO2), Siliziumnitrid, Siliziumoxynitrid und Siliziumkarbid, bei Temperaturen von nur 200-350 °C. Dieser niedrigere Temperaturbereich ist besonders vorteilhaft für Anwendungen mit temperaturempfindlichen Materialien wie Aluminium, bei denen höhere Temperaturen die Integrität des Substrats beeinträchtigen könnten.
Der PECVD-Prozess wird häufig in einer kapazitiv gekoppelten Parallelplatten-Plasmaanlage durchgeführt. Bei diesem Aufbau wird das Substrat auf einer geerdeten Elektrode positioniert, während das Plasma zwischen zwei Elektroden erzeugt wird. Die bei der PECVD verwendeten Gase können je nach den gewünschten Schichteigenschaften variieren. Zu den gängigen Gasen gehören Silan (SiH4), Distickstoffoxid (N2O), Ammoniak (NH3), Helium (He), Argon (Ar), Stickstofftrifluorid (NF3) und Phosphin (PH3). Jedes Gas spielt eine spezifische Rolle im Abscheidungsprozess und trägt zur Bildung der gewünschten Schicht bei.
Eines der wichtigsten technischen Merkmale des PECVD-Verfahrens ist seine Fähigkeit, bei Temperaturen unter 540 °C zu arbeiten, wodurch es für eine breite Palette von Substraten geeignet ist. Die Prozesskammer ist in der Regel mit mehreren Gaskammern ausgestattet, z. B. mit Silan-Kammern (A + C) und einer TEOS-Kammer (Tetraethylorthosilikat) (B), die jeweils für unterschiedliche Gasgemische und Abscheidungsanforderungen ausgelegt sind. Dieser modulare Aufbau ermöglicht eine größere Flexibilität und Kontrolle über den Abscheidungsprozess und gewährleistet die Herstellung hochwertiger Schichten mit präzisen Eigenschaften.
Metallorganische CVD (MOCVD)
Die metallorganische chemische Gasphasenabscheidung (MOCVD) ist eine fortschrittliche Epitaxietechnik, bei der metallorganische Verbindungen als Vorstufengase für die Abscheidung von Metall- und Halbleiterschichten verwendet werden. Diese Methode zeichnet sich besonders durch ihre Fähigkeit aus, eine breite Palette von Verbindungshalbleitern, einschließlich Ⅲ-V- und Ⅱ-VI-Materialien, sowie deren mehrschichtige feste Lösungen zu erzeugen.
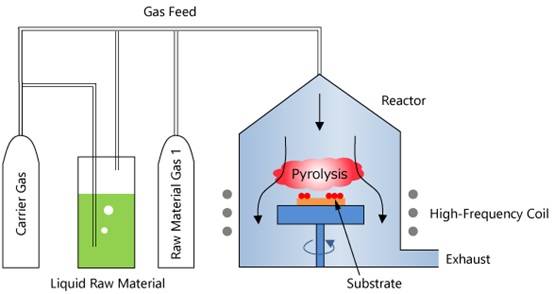
Hauptmerkmale von MOCVD
-
Ausgangsmaterialien: Bei der MOCVD werden organische Verbindungen der Elemente der Gruppen III und II sowie Hydride der Elemente der Gruppen V und VI als primäre Ausgangsmaterialien für das Kristallwachstum verwendet. Diese Materialien werden in gasförmigem Zustand in die Reaktionskammer eingeleitet, wo sie sich thermisch zersetzen und dünne, einkristalline Schichten auf dem Substrat bilden.
-
Präzisionskontrolle: Einer der wesentlichen Vorteile der MOCVD ist die präzise Kontrolle über die Zusammensetzung und die Dotierstoffkonzentration der abgeschiedenen Schichten. Diese Präzision wird durch die Regulierung der Durchflussrate und des Ein- und Ausschaltzeitpunkts der gasförmigen Ausgangsstoffe erreicht, was das Wachstum von dünnen und ultradünnen Schichten mit hoher Genauigkeit ermöglicht.
-
Schnelles Umschalten: Die relativ schnelle Gasdurchflussrate in der Reaktionskammer ermöglicht schnelle Änderungen der Zusammensetzung und der Dotierstoffkonzentration der verschiedenen Verbindungen. Diese schnelle Umschaltmöglichkeit verringert die Wahrscheinlichkeit von Memory-Effekten, erleichtert die Erzeugung steiler Grenzflächen und macht MOCVD ideal für das Wachstum von Heterostrukturen, Supergittern und Quantenwellmaterialien.
Vorteile gegenüber anderen Epitaxietechniken
Im Vergleich zu anderen Epitaxieverfahren bietet die MOCVD mehrere deutliche Vorteile:
Vorteil | Beschreibung |
---|---|
Kontrolle der Komponenten | Der gasförmige Zustand der Ausgangsstoffe ermöglicht eine genaue Kontrolle über die Komponenten, die Dotierstoffkonzentration und die Dicke der Epitaxieschicht. |
Schnelle Anpassungen | Schnelle Änderungen der Gasflussraten ermöglichen eine rasche Anpassung der Verbindungszusammensetzung, wodurch Memory-Effekte reduziert und die Qualität der Grenzflächen verbessert werden. |
Vielseitigkeit | Geeignet für eine breite Palette von Verbindungshalbleitern, einschließlich Ⅲ-V- und Ⅱ-VI-Materialien, was das Verfahren sehr vielseitig für verschiedene Anwendungen macht. |
Anwendungen von CVD
Herstellung von Halbleitern
In der Halbleiterfertigung spielt die chemische Gasphasenabscheidung (CVD) eine entscheidende Rolle bei der Herstellung fortschrittlicher Materialien, die die Leistung und Zuverlässigkeit der Bauelemente verbessern. Das Verfahren umfasst die Abscheidung verschiedener Schichten, darunter Silizide, Nitridschichten und Metallschichten, die jeweils auf bestimmte Anwendungen in der Halbleiterindustrie zugeschnitten sind.
Silizide
Silizide, die durch die Reaktion von Silizium mit Metallen entstehen, sind entscheidend für die Verringerung des Kontaktwiderstands und die Verbesserung der Effizienz von Halbleiterbauelementen. Sie werden häufig in Gate-Elektroden, Zwischenverbindungen und Kontaktpads verwendet. Wolframsilicid (WSi₂) wird beispielsweise wegen seines geringen Widerstandes und seiner thermischen Stabilität häufig in der CMOS-Technologie eingesetzt.
Nitrid-Schichten
Nitridschichten, wie z. B. Siliziumnitrid (Si₃N₄), erfüllen bei der Halbleiterherstellung mehrere Zwecke. Sie dienen als Diffusionsbarrieren, die die Migration von Dotierstoffen und Verunreinigungen verhindern, und als Passivierungsschichten, die das Bauelement vor Umwelteinflüssen schützen. Darüber hinaus sind Nitridschichten ein wesentlicher Bestandteil bei der Herstellung von Kondensatoren in DRAM-Bauelementen, die eine hohe Kapazität und geringe Leckströme gewährleisten.
Metallschichten
Metallschichten, einschließlich Aluminium (Al) und Kupfer (Cu), sind für die Herstellung von Verbindungen, die den Fluss von elektrischen Signalen in integrierten Schaltungen erleichtern, unerlässlich. Insbesondere Kupfer wird wegen seines geringen Widerstandes und seiner Fähigkeit, den Stromverbrauch und die Wärmeentwicklung zu reduzieren, bevorzugt. Der Einsatz von CVD bei der Abscheidung dieser Metallschichten gewährleistet eine gleichmäßige Bedeckung und eine hervorragende Haftung, die für die Integrität und Leistung von Halbleiterbauelementen entscheidend sind.
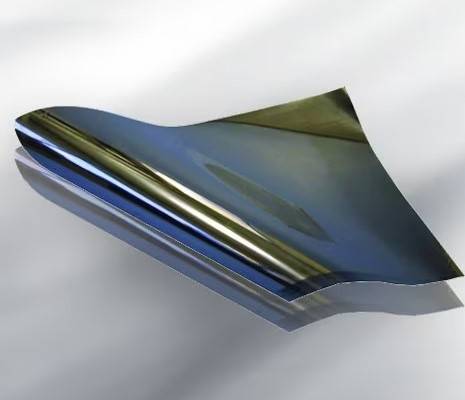
Durch den Einsatz der CVD-Technologie können Halbleiterhersteller den Abscheidungsprozess präzise steuern. Das Ergebnis sind hochwertige Schichten, die den strengen Anforderungen moderner elektronischer Geräte entsprechen.
Display-Technologie
Im Bereich der Display-Technologie,Indium-Zinn-Oxid-Schichten (ITO) undKupferschichten eine zentrale Rolle. Diese Materialien sind ein wesentlicher Bestandteil bei der Herstellung verschiedener Anzeigegeräte und verbessern deren Leistung und Funktionalität.
Indium-Zinn-Oxid (ITO)-Folien
ITO-Schichten sind für ihre außergewöhnliche elektrische Leitfähigkeit und optische Transparenz bekannt. Diese einzigartige Kombination macht sie ideal für Anwendungen wie:
- Touchscreens: Bereitstellung der leitfähigen Schicht, die für berührungsempfindliche Displays erforderlich ist.
- Elektrolumineszenz-Paneele: Erleichtern die Emission von Licht in Displays.
- Solarzellen: Verbessern den Wirkungsgrad von photovoltaischen Geräten, indem sie Licht durchlassen und gleichzeitig Strom leiten.
Kupferfolien
Kupferfolien hingegen sind bekannt für ihre hohe elektrische Leitfähigkeit und mechanische Festigkeit. Diese Eigenschaften werden in:
- Flexible Displays: Sie bieten Haltbarkeit und effiziente Signalübertragung.
- Hochauflösende Displays: Minimaler Signalverlust und Hochgeschwindigkeitsdatenverarbeitung.
- Fortschrittliche Verpackung: Unterstützung der Verbindungsfähigkeit in komplexen elektronischen Systemen.
Sowohl ITO- als auch Kupferschichten werden in der Regel abgeschieden durchChemische Gasphasenabscheidung (CVD) Techniken abgeschieden, die eine präzise Kontrolle der Schichtdicke und -gleichmäßigkeit ermöglichen und so eine optimale Leistung in Anzeigegeräten gewährleisten.
Andere Bereiche
Die Chemical Vapor Deposition (CVD)-Technologie findet nicht nur in der Halbleiterherstellung und der Displaytechnologie Anwendung, sondern auch in anderen Branchen, die präzise und dauerhafte Beschichtungen benötigen. Eine herausragende Anwendung ist dieoptischen Beschichtungenwo CVD eingesetzt wird, um dünne Schichten auf Linsen, Spiegeln und anderen optischen Komponenten abzuscheiden. Diese Beschichtungen erhöhen die Lichtdurchlässigkeit, verringern die Reflexion und verbessern die optische Gesamtleistung, was sie in Bereichen wie Telekommunikation, Luft- und Raumfahrt und medizinische Bildgebung unverzichtbar macht.
Eine weitere wichtige Anwendung sindAnti-Korrosions-Beschichtungen. Mittels CVD-Verfahren werden Schutzschichten auf Metallen und Legierungen aufgebracht, die sie vor rauen Umweltbedingungen schützen und ihre Lebensdauer verlängern. Dies ist besonders wichtig in Branchen wie der Automobilindustrie, der Luft- und Raumfahrt und der Schiffstechnik, wo die Materialien korrosiven Elementen ausgesetzt sind.
Anwendung | Auswirkung auf die Industrie |
---|---|
Optische Beschichtungen | Verbessert optische Geräte, die für die Telekommunikation und die medizinische Bildgebung entscheidend sind. |
Anti-Korrosions-Beschichtungen | Schützt Metalle in der Automobil-, Luft- und Raumfahrt- und Schifffahrtsbranche und verlängert die Lebensdauer. |
Diese Anwendungen unterstreichen die Vielseitigkeit und Robustheit der CVD-Technologie und machen sie zu einem Eckpfeiler moderner Industrieprozesse.
Merkmale des CVD-Verfahrens
Hohe Temperaturanforderung
Die hohen Temperaturanforderungen des CVD-Verfahrens sind aus mehreren Gründen von entscheidender Bedeutung. Erstens sind hohe Temperaturen unerlässlich, umdie Reaktionsgeschwindigkeit der Vorläufergase zu fördern. Wenn diese Gase erhitzt werden, kommt es zur Zersetzung und anschließenden chemischen Reaktionen auf der Substratoberfläche, die zur Bildung der gewünschten dünnen Schicht führen. Die durch die Wärme bereitgestellte kinetische Energie sorgt dafür, dass die Moleküle genügend Energie haben, um zu reagieren und stabile Bindungen zu bilden.
Außerdem tragen hohe Temperaturen dazu beiVerbesserung der Diffusionsgeschwindigkeit der Reaktanten auf dem Substrat. Diese Diffusion ist entscheidend für eine gleichmäßige Schichtabscheidung auf der Oberfläche. Ohne ausreichende Wärme würde der Diffusionsprozess nur langsam ablaufen, was zu ungleichmäßigen und möglicherweise fehlerhaften Schichten führen würde.
Außerdem spielen hohe Temperaturen eine Rolle bei derEntfernung von Verunreinigungen aus der Reaktionsumgebung. Verunreinigungen wie Feuchtigkeit oder Restgase können bei erhöhten Temperaturen ausgetrieben werden, was einen saubereren Abscheidungsprozess gewährleistet. Dieser Reinigungsaspekt ist besonders wichtig bei der Herstellung von hochreinen Materialien, die in Halbleiterbauelementen verwendet werden.
Temperaturbereich | Wirkung |
---|---|
Niedrig (<400°C) | Langsame Reaktionsgeschwindigkeiten, begrenzte Diffusion, Potenzial für ungleichmäßige Schichten. |
Mittel (400-800°C) | Optimiert für viele CVD-Verfahren, ausgewogene Reaktions- und Diffusionsraten. |
Hoch (>800°C) | Schnelle Reaktionen, hohe Diffusionsraten, kann jedoch die thermischen Grenzen des Substrats überschreiten. |
Vakuumumgebung
Das CVD-Verfahren wird in der Regel in einer Vakuumumgebung durchgeführt. Diese kontrollierte Atmosphäre ist aus mehreren Gründen entscheidend. Erstens wird durch das Vakuum das Vorhandensein von Verunreinigungen wie Sauerstoff und Wasserdampf minimiert, die andernfalls die chemischen Reaktionen stören und die Qualität der abgeschiedenen Schicht beeinträchtigen könnten. Zweitens hilft die Aufrechterhaltung des Vakuums bei der Steuerung des Drucks in der Beschichtungskammer, wodurch sichergestellt wird, dass die Gasvorläufer mit optimaler Geschwindigkeit fließen und effizient auf der Substratoberfläche reagieren.
Im Vakuum vergrößert sich die mittlere freie Weglänge der Gasmoleküle, wodurch die Kollisionen zwischen den Molekülen verringert werden. Diese Verringerung der Kollisionen ermöglicht eine gezieltere Bewegung der Gasvorläufer in Richtung des Substrats und verbessert so den Abscheidungsprozess. Darüber hinaus ermöglicht die Vakuumumgebung eine bessere Kontrolle der Temperatur- und Druckbedingungen, die kritische Parameter im CVD-Prozess sind.
Nutzen | Beschreibung |
---|---|
Verringerung von Verunreinigungen | Minimiert die Störung durch Sauerstoff und Wasserdampf. |
Druckmanagement | Sorgt für optimale Strömung und Reaktion von Gasvorläufern. |
Erhöhter mittlerer freier Weg | Verringert molekulare Kollisionen und verbessert die Abscheidung. |
Temperaturkontrolle | Ermöglicht eine bessere Kontrolle über kritische Parameter. |
Die Vakuumumgebung ist nicht nur eine technische Anforderung, sondern ein grundlegender Aspekt, der die Effizienz und Präzision des CVD-Prozesses untermauert. Durch die Aufrechterhaltung des Vakuums können die Hersteller hochwertige, gleichmäßige Schichten mit den gewünschten Eigenschaften erzielen, was es zu einem unverzichtbaren Bestandteil der CVD-Technologie macht.
Vorbereitung der Oberfläche
Vor jedem Beschichtungsverfahren, insbesondere bei der chemischen Gasphasenabscheidung (CVD), muss die Oberfläche des Substrats gründlich vorbereitet werden, um eine optimale Haftung und Schichtqualität zu gewährleisten. Dieser Schritt ist von entscheidender Bedeutung, da er sich direkt auf die Leistung und Langlebigkeit der abgeschiedenen Dünnschichten auswirkt.
Verunreinigungen wie organische Rückstände, Oxide und Feuchtigkeit müssen akribisch entfernt werden. Diese Verunreinigungen können die für die Schichtbildung notwendigen chemischen Reaktionen behindern und zu Defekten wie Nadellöchern oder ungleichmäßigen Schichten führen. Die Techniken für die Oberflächenvorbereitung sind unterschiedlich, aber gängige Methoden sindchemische Reinigung,ÄtzenundPlasmabehandlung.
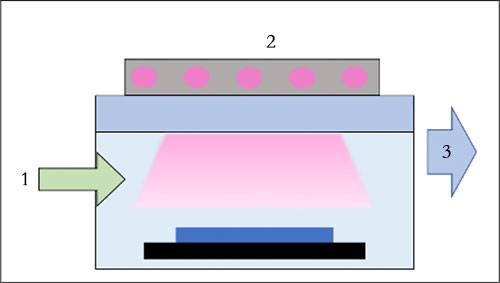
-
Chemische Reinigung: Hierbei werden Lösungsmittel oder Säuren verwendet, um organische und anorganische Verunreinigungen aufzulösen und zu entfernen. Die RCA-Reinigung ist beispielsweise ein Standardverfahren, bei dem eine Mischung aus Wasserstoffperoxid und Schwefelsäure zur Reinigung von Siliziumwafern verwendet wird.
-
Ätzen: Bei dieser Methode werden Oberflächenschichten durch chemische Reaktionen selektiv abgetragen. Zum Beispiel wird Flusssäure häufig verwendet, um natives Siliziumdioxid von Siliziumsubstraten zu entfernen.
-
Plasmabehandlung: Bei dieser Technik wird die Oberfläche durch Plasma aktiviert, um ihre Reaktivität zu erhöhen und sie von Restverunreinigungen zu befreien. Sie ist besonders wirksam bei der Entfernung organischer Rückstände und der Verbesserung der Oberflächenenergie.
Jede dieser Methoden trägt entscheidend dazu bei, dass das Substrat frei von Verunreinigungen ist, und erleichtert so die erfolgreiche Abscheidung hochwertiger dünner Schichten. Eine ordnungsgemäße Oberflächenvorbereitung verbessert nicht nur die Haftung der abgeschiedenen Schicht, sondern stellt auch sicher, dass die Schichteigenschaften, wie Gleichmäßigkeit und Dichte, den erforderlichen Spezifikationen entsprechen.
Beschränkungen des Substrats
Temperatur- und Reaktivitätsbeschränkungen sind kritische Faktoren, die die Auswahl an geeigneten Substraten für die chemische Gasphasenabscheidung (CVD) erheblich einschränken können. Die hohen Temperaturen, die für die chemischen Reaktionen erforderlich sind, können dem Substratmaterial thermische Beschränkungen auferlegen, so dass nur solche Materialien in Frage kommen, die diesen extremen Bedingungen standhalten können, ohne sich zu zersetzen oder zu verformen. Bestimmte organische Materialien oder Metalle mit niedrigem Schmelzpunkt sind beispielsweise nicht geeignet, da sie ihre strukturelle Integrität bei hohen Temperaturen nicht aufrechterhalten können.
Darüber hinaus können die Reaktivität der Vorläufergase und die daraus resultierenden chemischen Wechselwirkungen mit der Substratoberfläche die Auswahl an geeigneten Materialien weiter einschränken. Einige Substrate können ungünstig mit den Abscheidungsgasen reagieren, was zu unerwünschten Nebenreaktionen oder zur Bildung ungleichmäßiger Schichten führt. Diese Einschränkung der Reaktivität erfordert eine sorgfältige Auswahl und Vorbehandlung der Substrate, um die Kompatibilität mit dem CVD-Verfahren sicherzustellen.
Bedeckung und Maskierung
Im Zusammenhang mit der chemischen Gasphasenabscheidung (CVD) spielt der Prozess der Bedeckung und Maskierung eine entscheidende Rolle bei der Bestimmung der endgültigen Qualität und Funktionalität der abgeschiedenen dünnen Schichten. Während bei der CVD-Beschichtung sichergestellt wird, dass alle Bereiche des Substrats gleichmäßig mit dem gewünschten Material bedeckt werden, ist die Fähigkeit, bestimmte Bereiche selektiv zu maskieren, ein entscheidender Faktor für die Erzielung präziser Muster und Strukturen.
Der Aspekt der Bedeckung ist bei der CVD sehr effektiv, da er in der Regel zu einer gleichmäßigen Materialabscheidung auf der gesamten Substratoberfläche führt. Diese Gleichmäßigkeit ist wichtig für Anwendungen, bei denen eine gleichmäßige Schichtdicke erforderlich ist, wie z. B. bei der Halbleiterherstellung und der Displaytechnologie. Eine Herausforderung ergibt sich jedoch, wenn bestimmte Bereiche des Substrats vor dem Abscheideprozess geschützt werden müssen. Hier kommen Maskierungstechniken ins Spiel.
Bei der Maskierung im CVD-Verfahren werden physikalische Barrieren oder Fotolackschichten verwendet, um die Abscheidung von Material in bestimmten Bereichen zu verhindern. Diese Technik ist zwar im Allgemeinen wirksam, hat aber auch ihre Grenzen. So kann die Präzision des Maskierungsprozesses durch Faktoren wie die Art des Substrats, die Komplexität des Musters und die spezifischen CVD-Parameter beeinflusst werden. Außerdem müssen die Maskierungsmaterialien selbst sorgfältig ausgewählt werden, um sicherzustellen, dass sie nicht mit den Abscheidungsgasen reagieren oder sich bei den hohen Temperaturen, die bei CVD-Verfahren typischerweise auftreten, zersetzen.
Begrenzung der Schichtdicke
Die Dicke von Dünnschichten, die durch chemische Gasphasenabscheidung (CVD) abgeschieden werden, wird durch mehrere Faktoren begrenzt, in erster Linie durch die Prozessparameter und den physikalischen Zustand der beteiligten Materialien. Diese Einschränkungen sind entscheidend für das Verständnis der praktischen Anwendungen und Grenzen der CVD-Technologie.
Prozessparameter
Die Schichtdicke wird durch den Beschichtungsprozess selbst in mehrfacher Hinsicht eingeschränkt. Zu den wichtigsten Faktoren gehören:
- Temperatur und Druck: Die für CVD-Reaktionen erforderlichen hohen Temperaturen können die Dicke der abgeschiedenen Schicht begrenzen. Extreme Temperaturen können zu einem thermischen Abbau oder zu Ungleichmäßigkeiten in der Schicht führen. Ebenso kann der Druck, unter dem das Verfahren durchgeführt wird, die Wachstumsrate und Gleichmäßigkeit der Schicht beeinflussen.
- Reaktionskinetik: Die Geschwindigkeit, mit der die Vorläufergase reagieren und den gewünschten Film bilden, ist ein weiterer begrenzender Faktor. Schnellere Reaktionen können zu dünneren Schichten führen, wenn der Prozess nicht sorgfältig kontrolliert wird.
Zustand des Materials
Die physikalischen und chemischen Eigenschaften der Ausgangsmaterialien spielen ebenfalls eine wichtige Rolle:
- Stabilität des Vorläufermaterials: Die Stabilität der Vorläufergase bei hohen Temperaturen kann die Dicke des Films begrenzen. Instabile Vorstufen können sich vorzeitig zersetzen, was zu unvollständigen oder ungleichmäßigen Schichten führt.
- Substrat-Kompatibilität: Die Fähigkeit des Substratmaterials, den Abscheidungsbedingungen standzuhalten, ist von entscheidender Bedeutung. Bestimmte Substrate sind möglicherweise nicht in der Lage, die hohen Temperaturen oder die Reaktivität auszuhalten, die für die Abscheidung dickerer Schichten erforderlich sind.
Diese Einschränkungen sind keine bloßen Begrenzungen, sondern integraler Bestandteil des Verfahrens, um sicherzustellen, dass die abgeschiedenen Schichten von hoher Qualität und für die vorgesehenen Anwendungen geeignet sind.
Haftung
Hervorragende Haftungseigenschaften sind ein Markenzeichen der chemischen Gasphasenabscheidung (CVD), die für die Haltbarkeit und Funktionalität der erzeugten dünnen Schichten entscheidend ist. Die Haftung dieser Schichten wird von mehreren Faktoren beeinflusst, darunter die Oberflächenvorbereitung des Substrats, die chemische Reaktivität der Vorläufergase und die Prozessbedingungen wie Temperatur und Druck.
So sorgt eine ordnungsgemäße Oberflächenvorbereitung dafür, dass Verunreinigungen entfernt werden und eine saubere und reaktive Oberfläche entsteht, die die Haftung zwischen der Schicht und dem Substrat verbessert. Dieser Schritt ist besonders wichtig bei der Halbleiterherstellung, wo schon geringe Verunreinigungen zu erheblichen Leistungsproblemen führen können.
Auch die chemische Beschaffenheit der Vorläufergase spielt eine entscheidende Rolle. Die Reaktion zwischen den Gasvorläufern und der Substratoberfläche bildet eine starke chemische Bindung, die die Grundlage für die ausgezeichnete Haftung der CVD-Schichten bildet. Dieser chemische Bindungsmechanismus sorgt dafür, dass die abgeschiedenen Schichten auch unter rauen Betriebsbedingungen fest mit dem Substrat verbunden bleiben.
Prozessbedingungen wie die hohen Temperaturen, die für die CVD-Beschichtung erforderlich sind, tragen ebenfalls zu dieser starken Haftung bei. Diese hohen Temperaturen fördern nicht nur die für die Filmbildung erforderlichen chemischen Reaktionen, sondern ermöglichen auch eine bessere Diffusion der Filmmaterialien in das Substrat, wodurch eine robustere Grenzfläche entsteht.
Vorteile der CVD-Technologie
Gleichmäßigkeit
Gleichmäßigkeit bei der chemischen Gasphasenabscheidung (CVD) ist ein entscheidendes Merkmal, das eine gleichbleibende Schichtqualität auf großflächigen Substraten gewährleistet. Diese Gleichmäßigkeit wird durch eine sorgfältige Kontrolle der Prozessparameter, einschließlich Temperatur, Druck und Durchflussmenge der Ausgangsstoffe, erreicht. Die Fähigkeit, die Gleichmäßigkeit aufrechtzuerhalten, ist vor allem in der Halbleiterherstellung von entscheidender Bedeutung, wo selbst geringfügige Abweichungen zu erheblichen Leistungsproblemen des Endprodukts führen können.
Zur Veranschaulichung sei ein typischer CVD-Aufbau betrachtet, bei dem das Substrat einem gleichmäßigen Fluss von Precursor-Gasen ausgesetzt ist. Die Gasmoleküle diffundieren und reagieren auf der Substratoberfläche und bilden einen dünnen Film. Durch eine präzise Steuerung der Gasverteilung können die Hersteller sicherstellen, dass die Abscheidung gleichmäßig über das gesamte Substrat erfolgt, unabhängig von dessen Größe. Dies wird häufig durch fortschrittliche Reaktorkonstruktionen erleichtert, die eine gleichmäßige Gasverteilung fördern und örtliche Schwankungen minimieren.
Parameter | Auswirkung auf die Gleichmäßigkeit |
---|---|
Temperatur | Sorgt für eine gleichmäßige Zersetzung und Abscheidung der Ausgangsstoffe. |
Druck | Hilft bei der Aufrechterhaltung eines gleichmäßigen Gasflusses und einer gleichmäßigen Reaktionsgeschwindigkeit. |
Vorläuferfluss | Steuert die Konzentration und Verteilung der reaktiven Stoffe. |
Zusammenfassend lässt sich sagen, dass die Gleichmäßigkeit von CVD-Prozessen nicht nur eine wünschenswerte Eigenschaft, sondern eine grundlegende Voraussetzung für die Herstellung hochwertiger dünner Schichten ist. Sie unterstreicht die Bedeutung einer präzisen Prozesssteuerung und einer fortschrittlichen Reaktortechnologie für die Erzielung gleichmäßiger Ergebnisse auf großen Substraten.
Kontrollierbarkeit
Eines der herausragenden Merkmale der chemischen Gasphasenabscheidung (CVD) ist der hohe Grad an Kontrollierbarkeit des Abscheidungsprozesses. Diese Kontrollierbarkeit ist für die Erzielung präziser Schichteigenschaften und Abscheidungsraten unerlässlich, die für verschiedene Anwendungen in der Halbleiterherstellung, der Displaytechnologie und darüber hinaus von entscheidender Bedeutung sind.
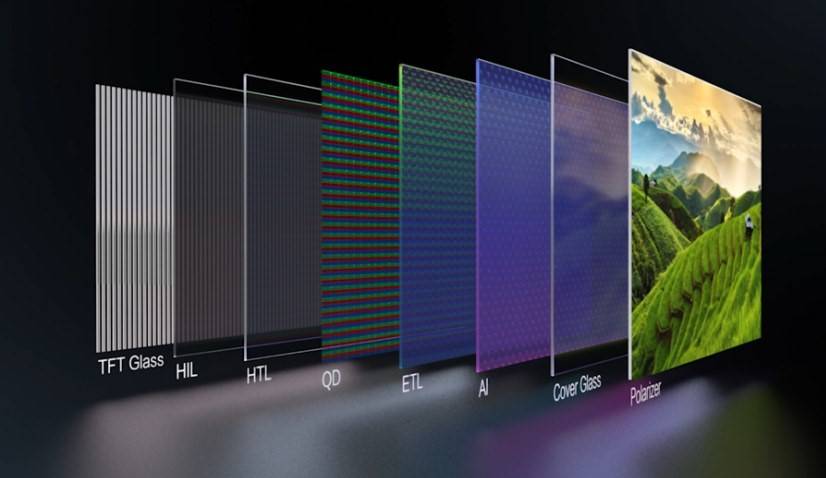
Kontrolle der Abscheidungsrate
Die Abscheiderate bei der CVD kann durch die Einstellung verschiedener Parameter genau kontrolliert werden. Dazu gehören:
- Temperatur: Durch Variation der Temperatur des Substrats und der Vorläufergase kann die Geschwindigkeit der chemischen Reaktionen fein abgestimmt werden. Höhere Temperaturen beschleunigen im Allgemeinen die Reaktionsgeschwindigkeit, was zu einer schnelleren Abscheidung führt.
- Druck: Der Betrieb unter verschiedenen Drücken kann die Strömungsdynamik der Vorläufergase und die Geschwindigkeit, mit der sie die Substratoberfläche erreichen, beeinflussen.
- Gasflussraten: Die Steuerung der Durchflussraten der Vorläufergase ermöglicht eine präzise Anpassung der Konzentration der Reaktanten am Substrat und beeinflusst so die Abscheidungsrate.
Anpassung der Filmeigenschaften
Neben der Abscheiderate bietet das CVD-Verfahren auch eine umfassende Kontrolle über die Eigenschaften der entstehenden Schicht. Zu den wichtigsten Eigenschaften, die angepasst werden können, gehören:
- Schichtdicke: Durch eine sorgfältige Steuerung der Prozessparameter kann die Dicke der abgeschiedenen Schicht innerhalb eines engen Bereichs gesteuert werden, so dass die Gleichmäßigkeit über große Substrate hinweg gewährleistet ist.
- Chemische Zusammensetzung: Die Verwendung verschiedener Vorläufergase oder -gemische ermöglicht die Abscheidung von Schichten mit unterschiedlicher chemischer Zusammensetzung, die auf die jeweiligen Anwendungsanforderungen zugeschnitten sind.
- Kristallstruktur: Die Temperatur- und Druckbedingungen können die Kristallinität der abgeschiedenen Schicht beeinflussen, so dass je nach Bedarf entweder amorphe oder kristalline Strukturen entstehen können.
- Spannung: Die Eigenspannung innerhalb der Schicht kann kontrolliert werden, um Defekte zu vermeiden und die Integrität der Schicht sowie die Haftung auf dem Substrat zu gewährleisten.
Prozess-Flexibilität
Die Kontrollierbarkeit von CVD erstreckt sich auch auf die Flexibilität des Prozesses selbst. Die verschiedenen CVD-Verfahren, wie thermische CVD, plasmaunterstützte CVD (PECVD) und metallorganische CVD (MOCVD), bieten einzigartige Vorteile und Kontrollmechanismen. So wird bei der PECVD ein Plasma eingesetzt, um die Reaktionsgeschwindigkeit zu erhöhen und eine zusätzliche Kontrolle über den Abscheidungsprozess zu ermöglichen, während bei der MOCVD metallorganische Verbindungen zur Abscheidung komplexer Materialien verwendet werden können.
Vielseitigkeit
Die Chemical Vapor Deposition (CVD)-Technologie zeichnet sich durch ihre außergewöhnliche Vielseitigkeit aus, die sie zu einem Eckpfeiler in verschiedenen Branchen macht. Diese Vielseitigkeit ist in erster Linie auf ihre Fähigkeit zurückzuführen, eine breite Palette von Materialien abzuscheiden, die jeweils auf spezifische Anwendungen zugeschnitten sind. Ob es um die Herstellung hochwertiger Halbleiterschichten, die Verbesserung von Display-Technologien oder die Entwicklung von Schutzschichten geht, CVD beweist seine Anpassungsfähigkeit an unterschiedliche Materialtypen und Funktionsanforderungen.
Vielfältige Materialien
Die Fähigkeit von CVD, unterschiedliche Materialien zu verarbeiten, ist ein wesentlicher Vorteil. Von Silizium- und Metallschichten bis hin zu komplexen Verbindungen wie Nitriden und Oxiden ist die Palette der verarbeitbaren Materialien sehr groß. Dieses breite Spektrum gewährleistet, dass CVD die strengen Anforderungen moderner technologischer Anwendungen erfüllen kann, von der Mikroelektronik bis zur modernen Optik.
Anwendungsflexibilität
Über die Materialvielfalt hinaus erstreckt sich die Flexibilität von CVD auch auf seine Anwendung in verschiedenen Bereichen. In der Halbleiterfertigung ist sie unverzichtbar für die Herstellung von Siliziden, Nitridschichten und Metallschichten, die alle eine entscheidende Rolle für die Leistung der Bauelemente spielen. In der Displaytechnologie wird CVD zur Abscheidung von Indium-Zinn-Oxid (ITO) und Kupferschichten eingesetzt, um die Funktionalität und Haltbarkeit von Bildschirmen zu verbessern. Darüber hinaus findet CVD auch in weniger konventionellen Bereichen wie optischen Beschichtungen und Korrosionsschutzbehandlungen Anwendung, was die Vielseitigkeit des Verfahrens weiter verdeutlicht.
Anpassungsfähigkeit des Verfahrens
Die Anpassungsfähigkeit von CVD-Verfahren ist ein weiterer Aspekt ihrer Vielseitigkeit. Techniken wie die thermische CVD, die plasmaunterstützte CVD (PECVD) und die metallorganische CVD (MOCVD) bieten jeweils einzigartige Vorteile und ermöglichen eine präzise Steuerung des Abscheidungsprozesses. Diese Anpassungsfähigkeit gewährleistet, dass CVD für verschiedene Substrate und Umgebungsbedingungen optimiert werden kann, was es zu einem vielseitigen Werkzeug in den Händen von Forschern und Ingenieuren macht.
Kontaktieren Sie uns für eine kostenlose Beratung
Die Produkte und Dienstleistungen von KINTEK LAB SOLUTION werden von Kunden auf der ganzen Welt anerkannt. Unsere Mitarbeiter helfen Ihnen gerne bei allen Fragen weiter. Kontaktieren Sie uns für eine kostenlose Beratung und sprechen Sie mit einem Produktspezialisten, um die am besten geeignete Lösung für Ihre Anwendungsanforderungen zu finden!