Überblick über kaltisostatisches Pressen
Inhaltsverzeichnis
- Überblick über kaltisostatisches Pressen
- Kaltisostatisches Pressen im Werkzeugbau
- Anwendung von CIP zur Herstellung von Verschleiß- und Umformwerkzeugen
- Einsatz von Dry-Bag- und Wet-Bag-CIP-Pressen
- CIP-Prozess mit wasserbasiertem flüssigem Medium bei Umgebungstemperatur
- Verwendung von Formbeuteln mit Kernen und Pulvern ohne oder mit geringem Wachsgehalt
- Maßtoleranzen der von CIP hergestellten Teile
- Kaltisostatisches Pressen bei der Herstellung seltener Metallpulver
- Kaltisostatisches Pressen und Extrudieren
- Kommerzielle Nutzung von CIP und Extrusion zur Herstellung extrudierter AlBeMet-Stäbe und -Stäbe
- Prozess des Einkapselns, Entgasens und Vorwärmens des Barrens
- Extrusionsverfahren mit einer konischen Düse
- Postextrusionsprozesse einschließlich chemischem Ätzen und Entfernen der Kupferhaut
- Glühprozess von extrudierten Aluminium-Beryllium-Legierungen
Kaltisostatisches Pressen (CIP) ist eine leistungsstarke Technik, die bei der Materialverarbeitung zur Verbesserung der Materialeigenschaften eingesetzt wird. Dabei wird ein Material von allen Seiten einem gleichmäßigen Druck ausgesetzt, indem es in ein unter hohem Druck stehendes flüssiges Medium eingetaucht und hydraulischer Druck ausgeübt wird. CIP ist besonders effektiv zum Formen und Konsolidieren von pulverförmigen Materialien, zum Erstellen komplizierter Formen und zum Erreichen einer hohen Gründichte.
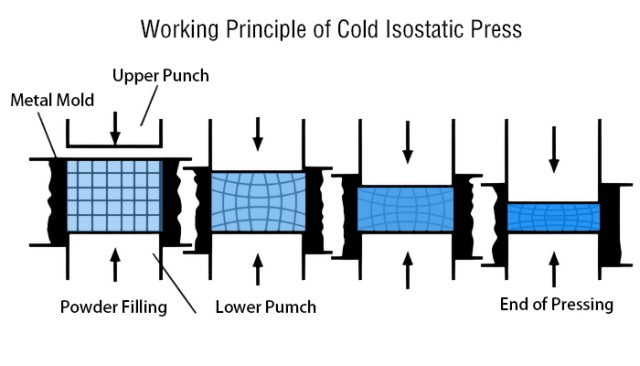
Definition und Gemeinsamkeit des kaltisostatischen Pressens (CIP)
Kaltisostatisches Pressen, auch kaltisostatische Verdichtung genannt, ist ein Verdichtungsverfahren für Pulver, die in einer Elastomerform eingeschlossen sind. Die Form wird in eine Druckkammer gestellt und ein flüssiges Medium eingepumpt, wodurch die Form von allen Seiten einem hohen Druck ausgesetzt wird. CIP wird bei verschiedenen Materialien wie Pulvermetallurgie, Hartmetallen, feuerfesten Materialien, Graphit, Keramik, Kunststoffen und mehr eingesetzt.
Einsatz von Wetbag- und Drybag-Techniken für CIP
Bei der CIP kommen zwei gängige Techniken zum Einsatz: Wetbag und Drybag. Beim Wetbag-Verfahren wird das Pulvermaterial in einem flexiblen Formbeutel eingeschlossen, der in einem Druckbehälter in eine unter hohem Druck stehende Flüssigkeit getaucht wird. Anschließend wird isostatischer Druck ausgeübt, um das Pulver in die gewünschte Form zu verdichten. Dieses Verfahren ist ideal für die Produktion mehrerer Formen, die Produktion kleiner bis großer Mengen und das Pressen großer Produkte.
Für einfache Formen wird dagegen das Trockenbeutelpressen eingesetzt. Die mit Pulver gefüllte Form wird versiegelt und die Kompression erfolgt zwischen der Form und dem Druckbehälter. Diese Technik eignet sich zur Herstellung von Bauteilen mit geringerer Komplexität.
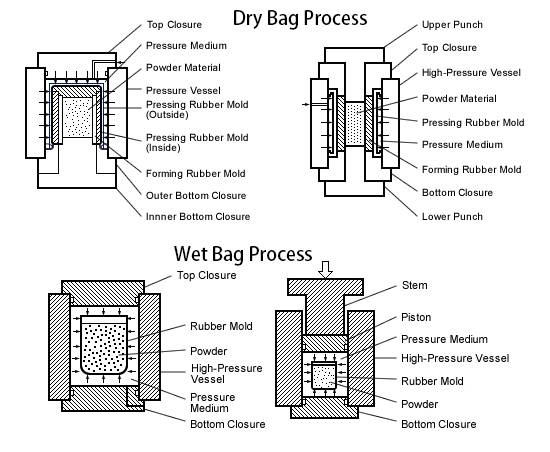
Herstellung komplexer Bauteile und Wolframbarren mittels CIP
CIP wird häufig bei der Herstellung komplexer Bauteile und Wolframbarren eingesetzt. Mit der Wetbag-Technik ist es möglich, Wolframbarren mit einem Gewicht von bis zu 1 Tonne zu pressen. Darüber hinaus ermöglicht CIP die Verdichtung komplexerer Komponenten, da es in der Lage ist, komplizierte Formen zu erzeugen und eine hohe Gründichte zu erreichen.
Zusammenfassend ist Kaltisostatisches Pressen (CIP) eine vielseitige Technik zum Formen und Verfestigen von pulverförmigen Materialien. Es bietet Vorteile wie die Möglichkeit, komplexe Komponenten herzustellen, komplizierte Formen zu erstellen und eine hohe Gründichte zu erreichen. Die Wahl zwischen Wetbag- und Drybag-Technik hängt von den spezifischen Anforderungen des Projekts ab.
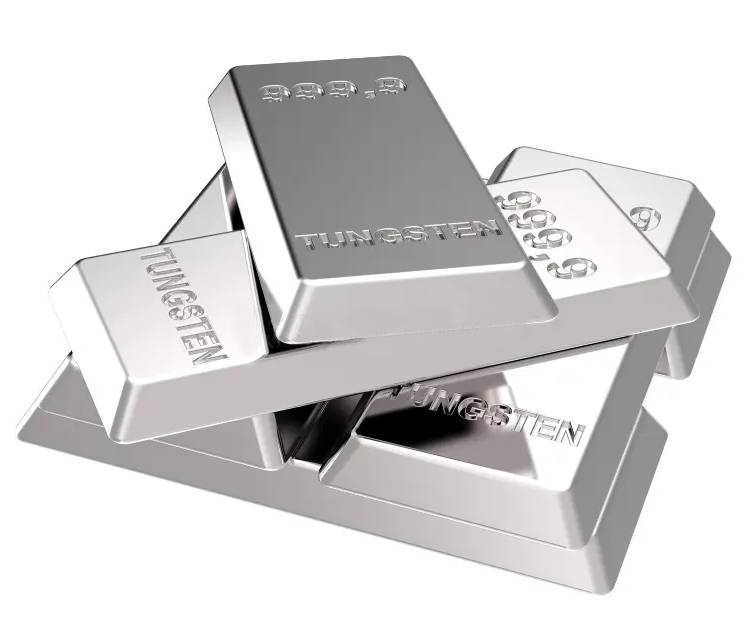
Kaltisostatisches Pressen im Werkzeugbau
Kaltisostatisches Pressen (CIP) ist eine Methode im Werkzeugbau, bei der pulverförmige Materialien vor der Bearbeitung oder dem Sintern zu einer festen, homogenen Masse verdichtet werden. Es wird häufig zur Herstellung von Verschleiß- und Metallumformwerkzeugen verwendet. Beim CIP wird das Pulver aus allen Richtungen dem gleichen Druck ausgesetzt, was zu hochintegrierten Knüppeln oder Vorformen mit geringer Verformung oder Rissbildung beim Brennen führt.
Anwendung von CIP zur Herstellung von Verschleiß- und Umformwerkzeugen
CIP wird häufig bei der Herstellung von Verschleiß- und Metallumformwerkzeugen eingesetzt. Es eignet sich besonders für Teile, die zu groß sind, um in einachsigen Pressen gepresst zu werden, und im gesinterten Zustand keine hohe Präzision erfordern. CIP kann hochintegrierte Knüppel oder Vorformen mit minimaler Verformung oder Rissbildung herstellen.
Einsatz von Dry-Bag- und Wet-Bag-CIP-Pressen
Es gibt zwei Arten von CIP-Prozessen: Dry-Bag und Wet-Bag. Beim Dry-Bag-Verfahren wird das Pulver in einen undurchlässigen, formbaren Beutel in einer Druckkammer gegeben. Anschließend wird der Beutel mit einem flüssigen Medium auf Wasserbasis bei Umgebungstemperatur einem isostatischen Druck ausgesetzt. Dieser Prozess ist automatisiert und ermöglicht die Massenproduktion relativ einfacher Formen.
Beim Wet-Bag-Verfahren hingegen wird das Pulvermaterial in einem Flex-Mold-Beutel in eine Hochdruckflüssigkeit in einem Druckbehälter getaucht. Anschließend wird isostatischer Druck ausgeübt, um das Pulver in die gewünschte Form zu verdichten. Dieses Verfahren ist ideal für die Produktion mehrerer Formen und kleiner bis großer Mengen, einschließlich des Pressens großer Produkte.
CIP-Prozess mit wasserbasiertem flüssigem Medium bei Umgebungstemperatur
Beim CIP wird das Pulvermaterial in einen undurchlässigen, formbaren Beutel in einer Druckkammer gegeben. Der Beutel wird mit einem flüssigen Medium auf Wasserbasis gefüllt und die gesamte Form wird von allen Seiten gleichmäßig mit hohem Druck beaufschlagt. Der Druck wird mit einem flüssigen Medium auf Wasserbasis bei Umgebungstemperatur ausgeübt. Dieser Prozess ermöglicht die Verdichtung des Pulvermaterials zu einer festen, homogenen Masse.
Verwendung von Formbeuteln mit Kernen und Pulvern ohne oder mit geringem Wachsgehalt
Um endkonturnahe Formen zu erhalten, werden im CIP-Prozess geformte Beutel mit Kernen eingesetzt. Diese geformten Beutel tragen dazu bei, die gewünschte Form und Maßtoleranzen des Endprodukts zu erreichen. Darüber hinaus werden beim kaltisostatischen Pressen Pulver ohne oder mit geringem Wachsanteil verwendet. Dadurch wird sichergestellt, dass das Pulvermaterial problemlos zu einer festen Masse verdichtet werden kann, ohne dass übermäßige Hitze oder Druck erforderlich ist.
Maßtoleranzen der von CIP hergestellten Teile
Die Maßtoleranzen der durch CIP hergestellten Teile sind im Vergleich zum einachsigen Pressen relativ groß. Dies bedeutet, dass die Größen- und Formkontrolle im CIP-Prozess nicht so wichtig ist. Allerdings müssen durch CIP hergestellte Teile noch im grünen oder vorgesinterten Zustand bearbeitet und anschließend gesintert werden, um die endgültigen Abmessungen und Eigenschaften zu erreichen.
Insgesamt ist das kaltisostatische Pressen ein vielseitig einsetzbares Verfahren im Werkzeugbau zur Herstellung von Verschleiß- und Umformwerkzeugen. Es bietet Vorteile wie hochintegrierte Knüppel oder Vorformen, minimale Verformung oder Rissbildung und die Möglichkeit, endkonturnahe Formen herzustellen. CIP ist ein kostengünstiges und effizientes Verfahren, das für die Massenproduktion komplexer Formen in verschiedenen Branchen eingesetzt werden kann.
Kaltisostatisches Pressen bei der Herstellung seltener Metallpulver
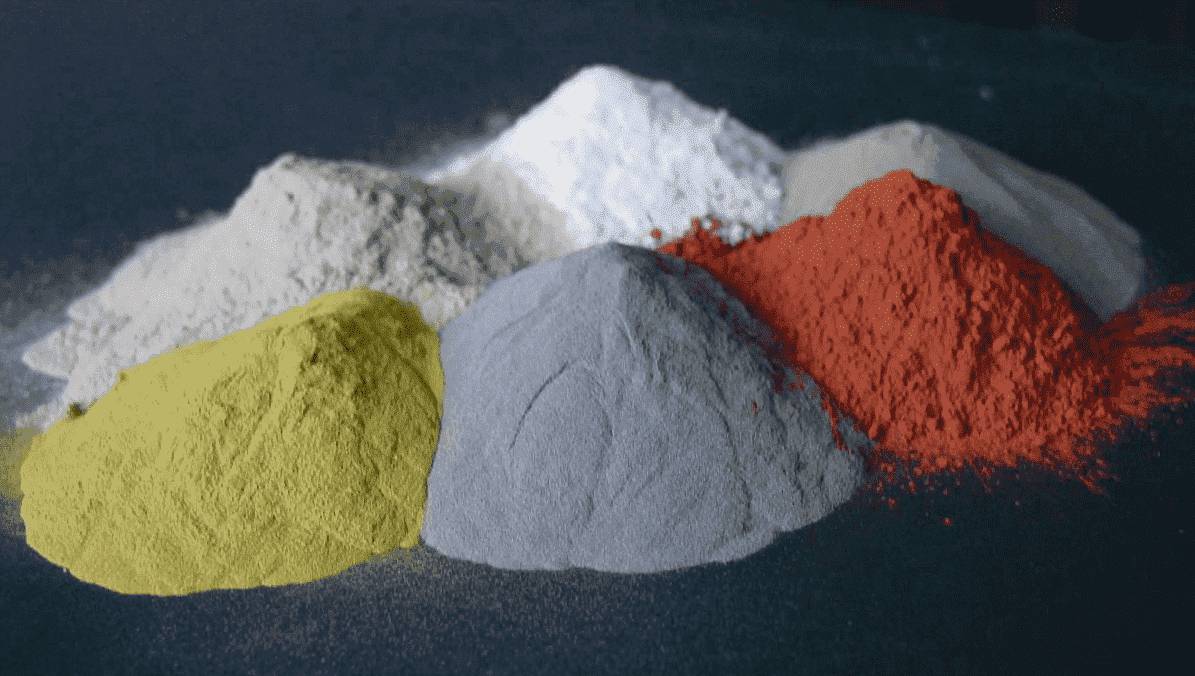
Kaltisostatisches Pressen ist eine Technik zur Herstellung seltener Metallpulver. Dabei wird Druck auf das Pulver bei Raumtemperatur oder etwas höher, typischerweise unter 93 °C, ausgeübt. Der angewandte Druck liegt zwischen 100 und 600 MPa.
Der Zweck des kaltisostatischen Pressens besteht darin, ein „Rohteil“ mit ausreichender Festigkeit für die Handhabung, Verarbeitung und schließlich das Sintern zu erhalten, um die endgültige Festigkeit zu erreichen. Bei dieser Technik wird ein flüssiges Medium wie Wasser, Öl oder eine Glykolmischung verwendet.
Bei Metallen kann durch kaltisostatisches Pressen eine theoretische Dichte von etwa 100 % erreicht werden. Bei Keramikpulvern wird eine Dichte von ca. 95 % erreicht. Kaltisostatisches Pressen eignet sich besonders zum Formen pulverförmiger Materialien bei Raumtemperatur unter Verwendung von Gummi oder Kunststoff als umhüllendes Formmaterial und einer Flüssigkeit als Druckmedium.
Einer der Vorteile des kaltisostatischen Pressens besteht darin, dass keine teuren Presswerkzeuge erforderlich sind, was es zu einer kostengünstigen Option macht. Dies ist besonders vorteilhaft bei der Herstellung großer oder komplexer Presslinge, bei denen sich die hohen Anschaffungskosten für Pressformen nicht rechtfertigen lassen.
Diese Technik kann im kommerziellen Maßstab für verschiedene Arten von Pulvern eingesetzt werden, darunter Metalle, Keramik, Kunststoffe und Verbundwerkstoffe. Die zum Verdichten erforderlichen Drücke reichen von weniger als 5.000 psi bis über 100.000 psi (34,5 bis 690 MPa).
Pulver werden in Elastomerformen entweder im Nass- oder Trockenbeutelverfahren verdichtet. Kaltisostatisches Pressen bietet eine Möglichkeit zur Herstellung hochwertiger Teile, die weiteren Sinter- oder Heißisostatpressprozessen unterzogen werden können.
Kaltisostatisches Pressen und Extrudieren
Kommerzielle Nutzung von CIP und Extrusion zur Herstellung extrudierter AlBeMet-Stäbe und -Stäbe
Kaltisostatisches Pressen (CIP) wird in kommerziellen Anwendungen häufig zur Herstellung extrudierter AlBeMet-Stäbe und -Stangen eingesetzt. Bei diesem Verfahren werden ungesinterte oder grün verdichtete Metallpulverkomponenten vor der Weiterverarbeitung wie Walzen, Bearbeiten oder Sintern vorverdichtet. CIP-Systeme werden in verschiedenen Branchen, darunter Luft- und Raumfahrt, Militär, Industrie und Medizin, eingesetzt, um einwandfreie Komponenten mit ausreichender Grünfestigkeit für die Handhabung und das Sintern herzustellen.
Prozess des Einkapselns, Entgasens und Vorwärmens des Barrens
Der Prozess des kaltisostatischen Pressens beginnt mit der Einkapselung des Metallpulvers in eine Elastomerform aus Materialien wie Urethan, Gummi oder Polyvinylchlorid. Das eingekapselte Pulver wird dann einem Flüssigkeitsdruck ausgesetzt, typischerweise unter Verwendung von Öl oder Wasser, im Bereich von 60.000 lbs/in2 bis 150.000 lbs/in2. Dieser Druck trägt dazu bei, das Pulver gleichmäßig zu verdichten, was zu einem Grünling mit geringer geometrischer Genauigkeit, aber hoher Dichte führt. Anschließend wird der Grünling vorgewärmt, um ihn für die weitere Verarbeitung vorzubereiten.
Extrusionsverfahren mit einer konischen Düse
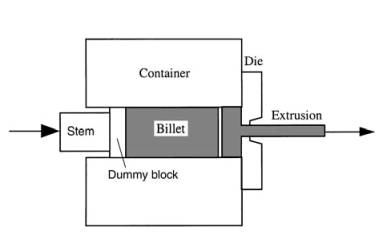
Nachdem der Barren vorgewärmt ist, wird er mithilfe einer konischen Düse extrudiert. Die konische Düse hilft dabei, den extrudierten AlBeMet-Stab oder -Stab entsprechend den gewünschten Abmessungen zu formen. Beim Extrusionsprozess wird hoher Druck ausgeübt, um den Barren durch die konische Düse zu drücken, wodurch ein kontinuierlich extrudiertes Produkt entsteht. Dieser Prozess gewährleistet die Gleichmäßigkeit und Konsistenz des extrudierten AlBeMet-Stabs oder -Stabs.
Postextrusionsprozesse einschließlich chemischem Ätzen und Entfernen der Kupferhaut
Sobald der Extrusionsprozess abgeschlossen ist, werden Nachextrusionsprozesse durchgeführt, um das extrudierte Produkt zu verfeinern. Zu diesen Prozessen gehören chemisches Ätzen und das Entfernen der Kupferhaut. Chemisches Ätzen hilft bei der Entfernung von Oberflächenverunreinigungen oder -defekten und stellt so die Qualität des extrudierten AlBeMet-Stabs oder -Stabs sicher. Das Entfernen der Kupferhaut ist notwendig, da diese aufgrund der Verwendung von Kupferlegierungen im Extrusionsprozess typischerweise auf der Oberfläche des extrudierten Produkts vorhanden ist.
Glühprozess von extrudierten Aluminium-Beryllium-Legierungen
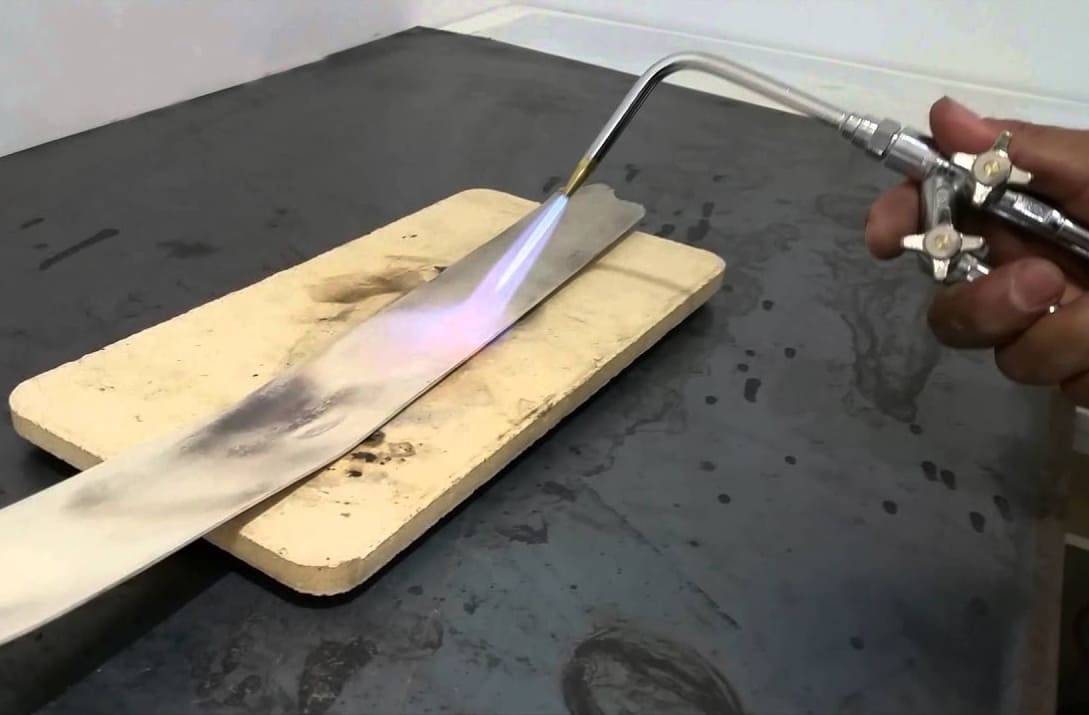
Nach den Nachextrusionsprozessen werden die extrudierten Aluminium-Beryllium-Legierungen (AlBeMet) einem Glühprozess unterzogen. Beim Glühen wird das extrudierte Produkt auf eine bestimmte Temperatur erhitzt und anschließend langsam abgekühlt, um innere Spannungen abzubauen und seine mechanischen Eigenschaften zu verbessern. Dieser Prozess trägt zur Verbesserung der Festigkeit, Duktilität und Stabilität des extrudierten AlBeMet-Stabs oder -Stabs bei.
Insgesamt spielen kaltisostatisches Pressen und Extrudieren eine entscheidende Rolle bei der kommerziellen Produktion von extrudierten AlBeMet-Stäben und -Stäben. Die Kombination dieser Verfahren gewährleistet die Herstellung hochwertiger Bauteile mit präzisen Abmessungen und hervorragenden mechanischen Eigenschaften.
Kontaktieren Sie uns für eine kostenlose Beratung
Die Produkte und Dienstleistungen von KINTEK LAB SOLUTION werden von Kunden auf der ganzen Welt anerkannt. Unsere Mitarbeiter helfen Ihnen gerne bei allen Fragen weiter. Kontaktieren Sie uns für eine kostenlose Beratung und sprechen Sie mit einem Produktspezialisten, um die am besten geeignete Lösung für Ihre Anwendungsanforderungen zu finden!